



hen a pickup project’s cab and chassis remain separated long enough, we might (OK, I might) lose sight of a detail or two. Our ’55 Chevy second-series project has been seen this way in tech before. If by chance you missed it, we started with a wreck.
Because this old truck first belonged to its current owner’s father, it’s a sentimental build. In this instance we wouldn’t want to completely erase the truck’s personality. Granted, it’s receiving the mandatory stance-enhancement but apart from that, it’ll be a dolled-up stocker, pretty much.
When the project’s twisted Unisteel cab was first lifted, its twisted-to-match foundation went straight to the frame shop. Still bearing some scars, it did at least roll out true. As an extra-added plus, the frame retains its digits, just as an Oakland assembly plant worker stamped ’em in late 1955.
So, what detail or two have we (OK, I) lost sight of? Well, during the standard-procedure mock-up, the panel gapectomy, and the general fight for fitment, I neglected to notice that brake master cylinder access would end up somewhat hindered.
Early in the build we’d upgraded to front disc brakes. At the same time we stepped up for a dual master cylinder conversion—all from Classic Performance Products. Our new, now-functioning dual master cylinder of course has a larger-than-stock lid, but it also misaligns awkwardly with the floor’s existing access hole.
Impending modification for the dilemma du jour would’ve been easier earlier, before rubberized undercoating, color, and final cab installation. Still, if we’re careful, we can pull this off without much marring of resplendent surfaces.
Years—and I mean years—ago, when this project first came to us, I didn’t expect I’d be typing up this particular tech story. Quite fortunately, however, there are some old photos that I do believe could fill the gaps.
For the actual job at hand, the needed modification will be “seat-of-the-pants,” or “on-the-fly” if you prefer. So far, I have no idea what I’ll end up doing here.
At times like these an inspirational trudge (weather permitting) through an old-enough wreckin’ yard can render solutions. If there’s an old car or truck with a flat-enough dash, a glovebox door with a bit of surrounding ’jamb metal could function nicely as a master cylinder access door. With our cab in color top-and-bottom, however, it’s a little late for that much cutting, welding, or even chemical panel bonding.
Since our build isn’t too far from stock, should we hold back a bit this time? Our custom work here would be concealed beneath a reproduction floor mat, anyway. With the mat flipped up, it might be nice if our modification could have a factory-fool-you appearance.
As it all works out, it’s time to place a rather extensive order with Steele Rubber Products. In preparation, while thumbin’ through my personalized catalog, it occurred to me (yes, finally) that we could ease master cylinder access simply by creating an additional hole for an additional master cylinder access cover (PN 66-0016-24 ) from Steele Rubber Products.
Sometimes the easy route is also the appropriate route. The plan as it stands wouldn’t be so tough at all. While this may not have the dramatic effect we’d create by trudgin’ across the tundra (it’s snowing now), through an old-enough wreckin’ yard it’ll certainly help us expedite the larger job at hand.
First things first, there’ll be some heavy lifting. With new mounting pads and related hardware we’ll finally reinstall a painted cab. Then, with some assembly required, let’s place that order with Steele—and let’s get started here.
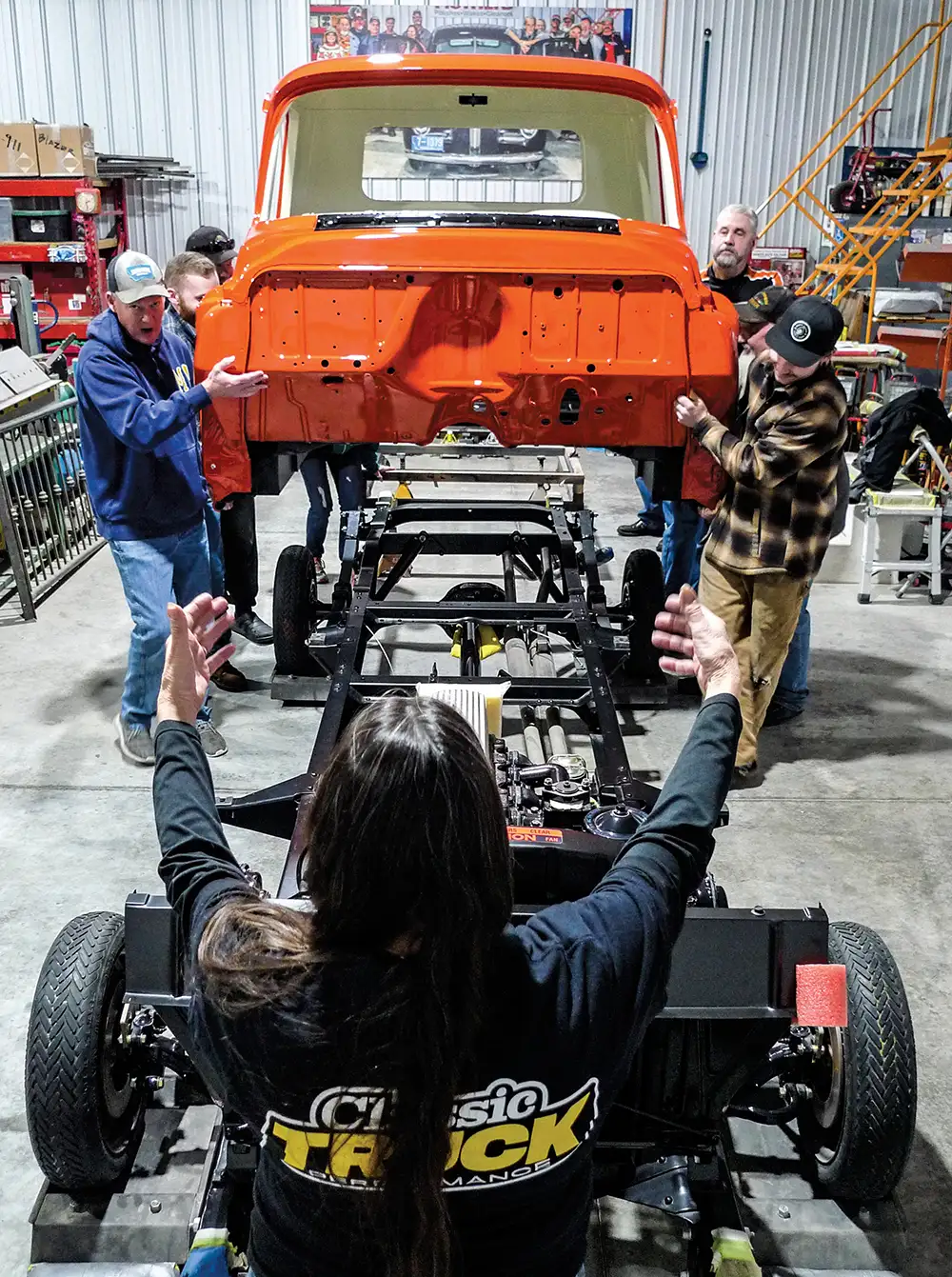
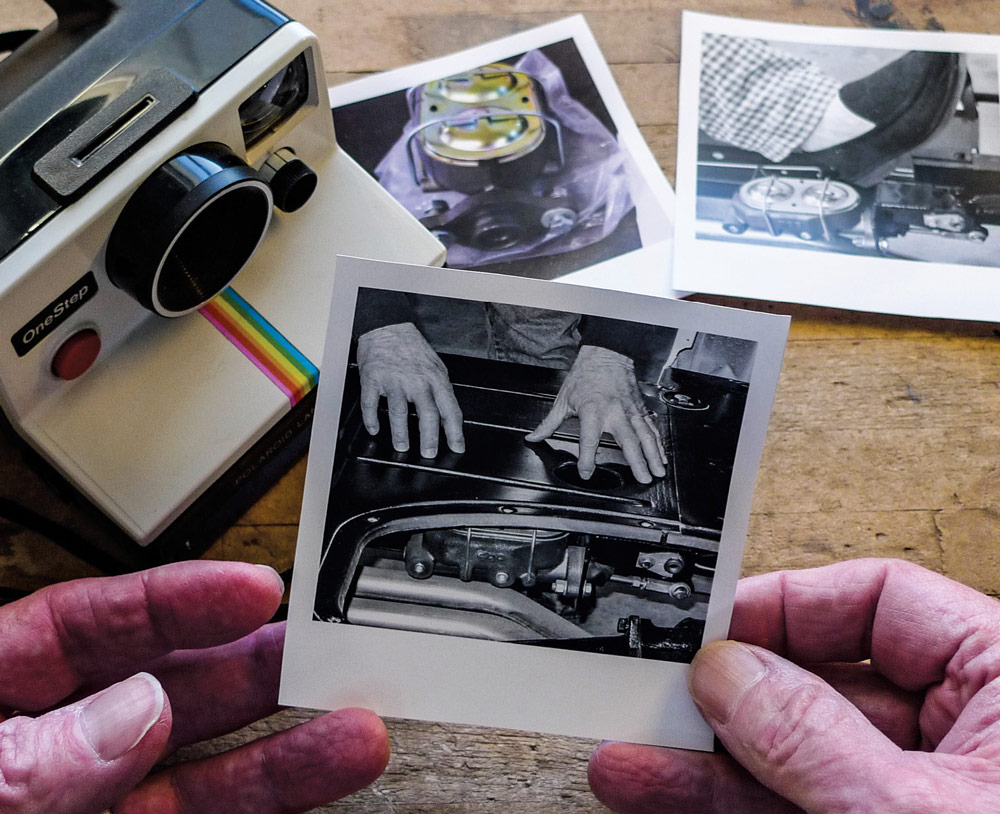
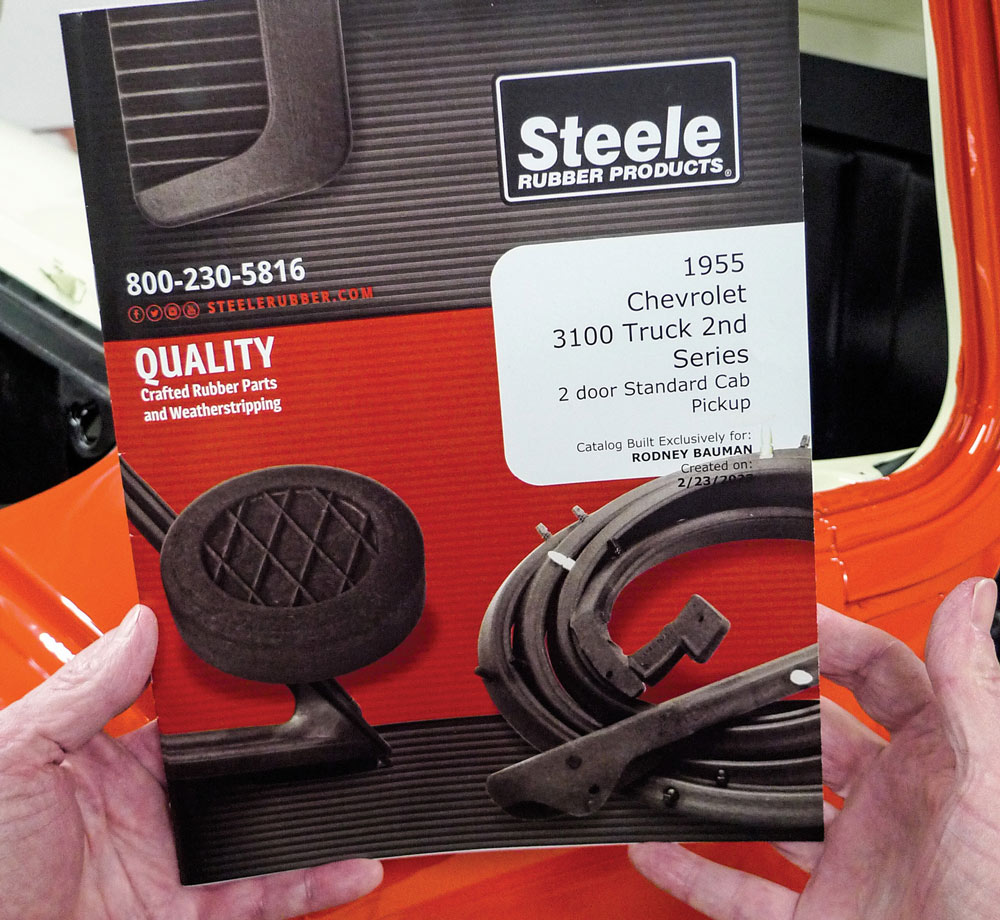
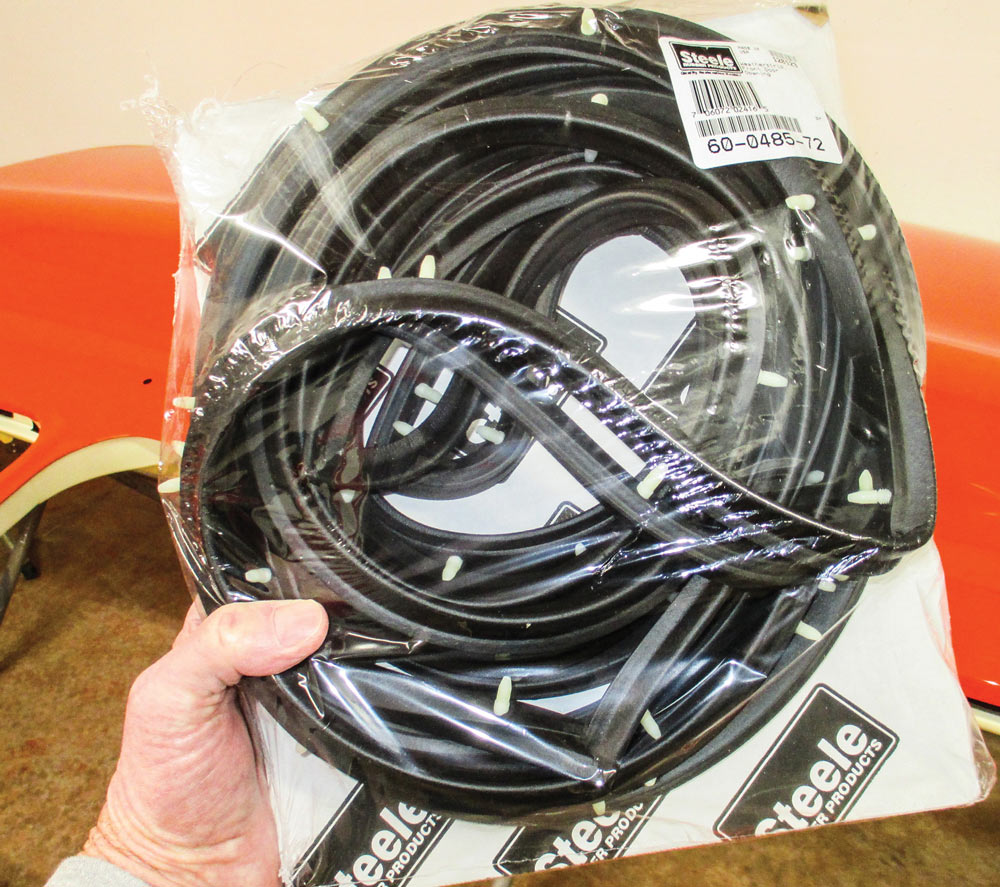
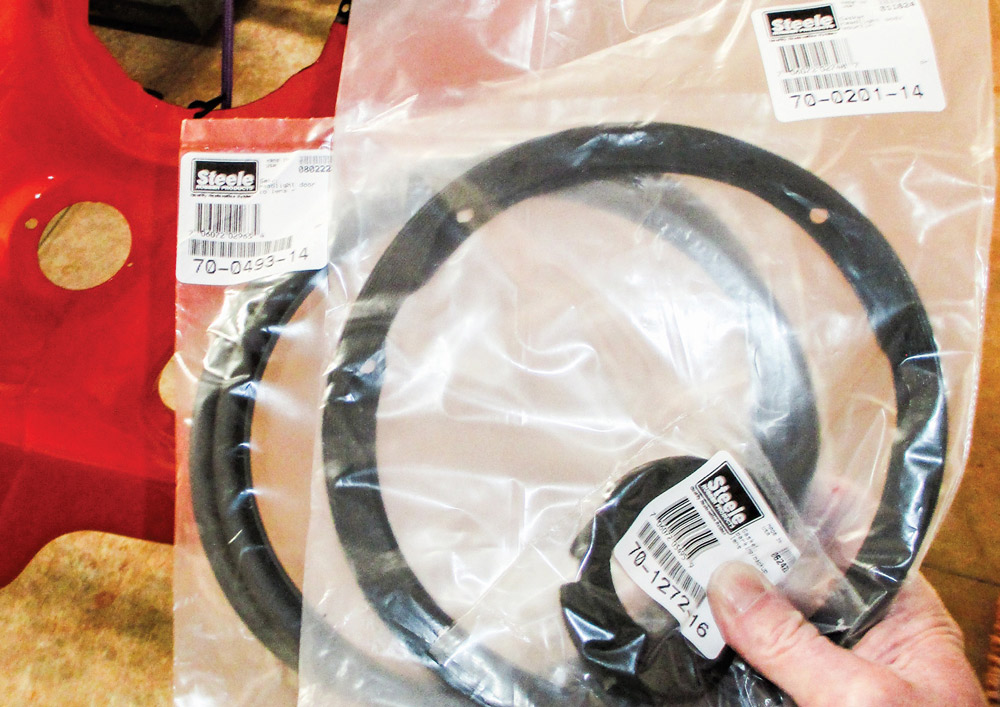





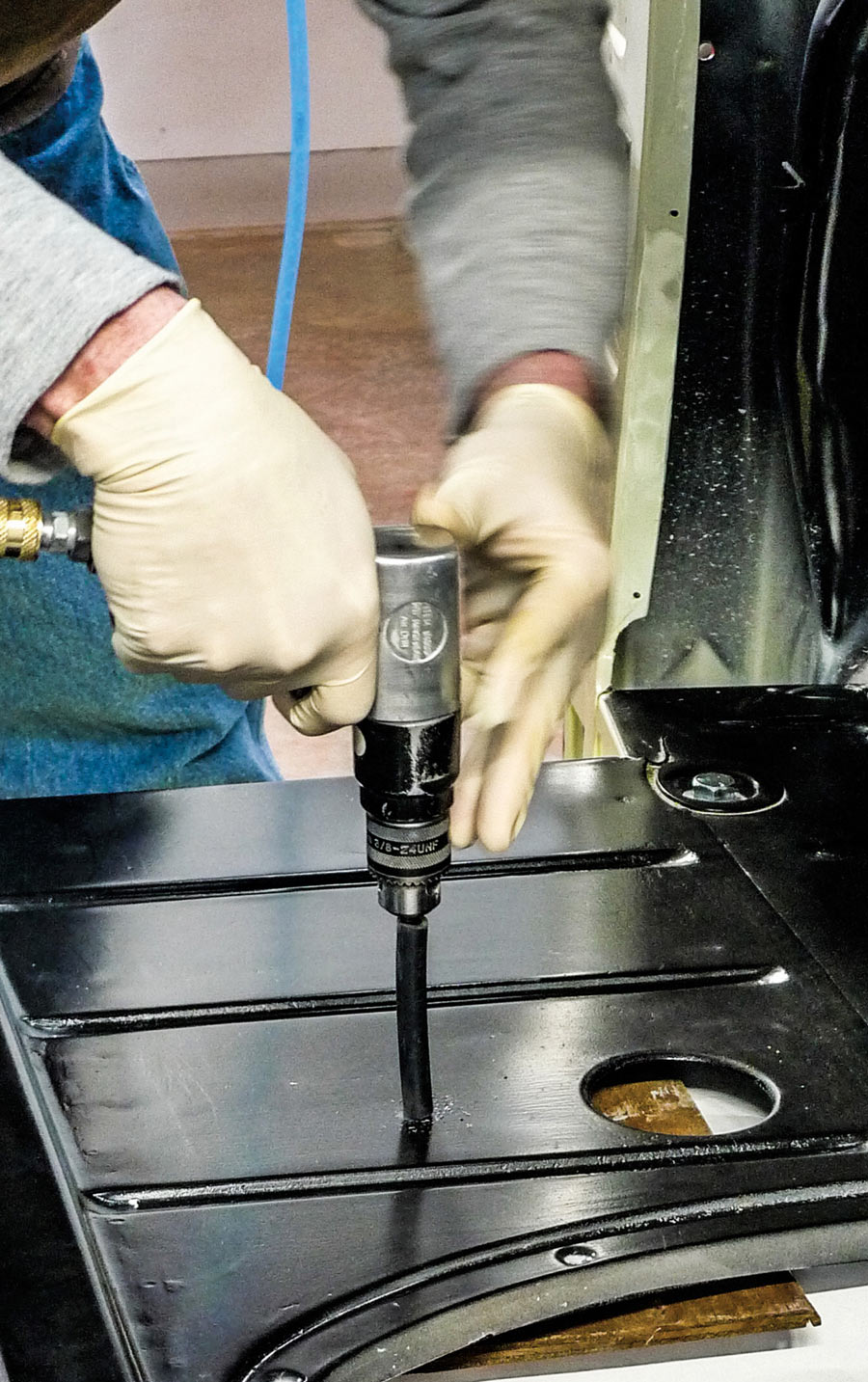
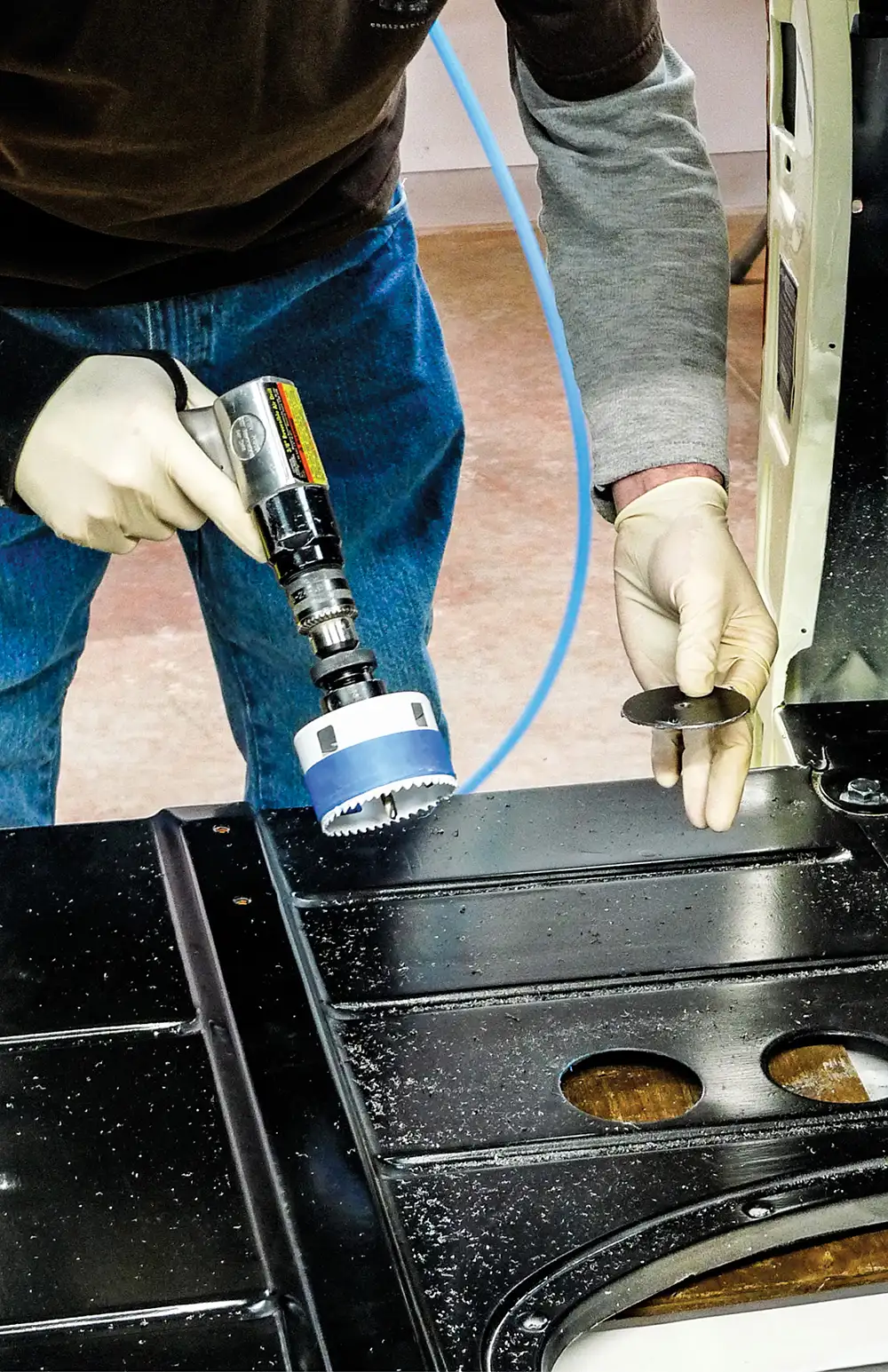
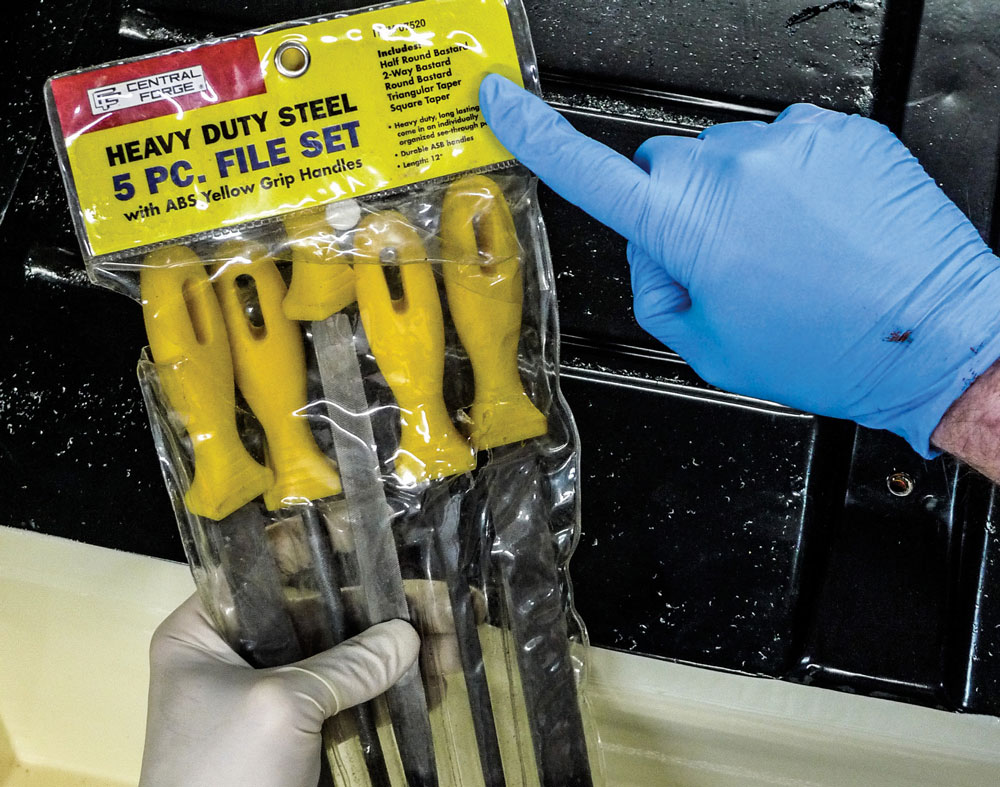
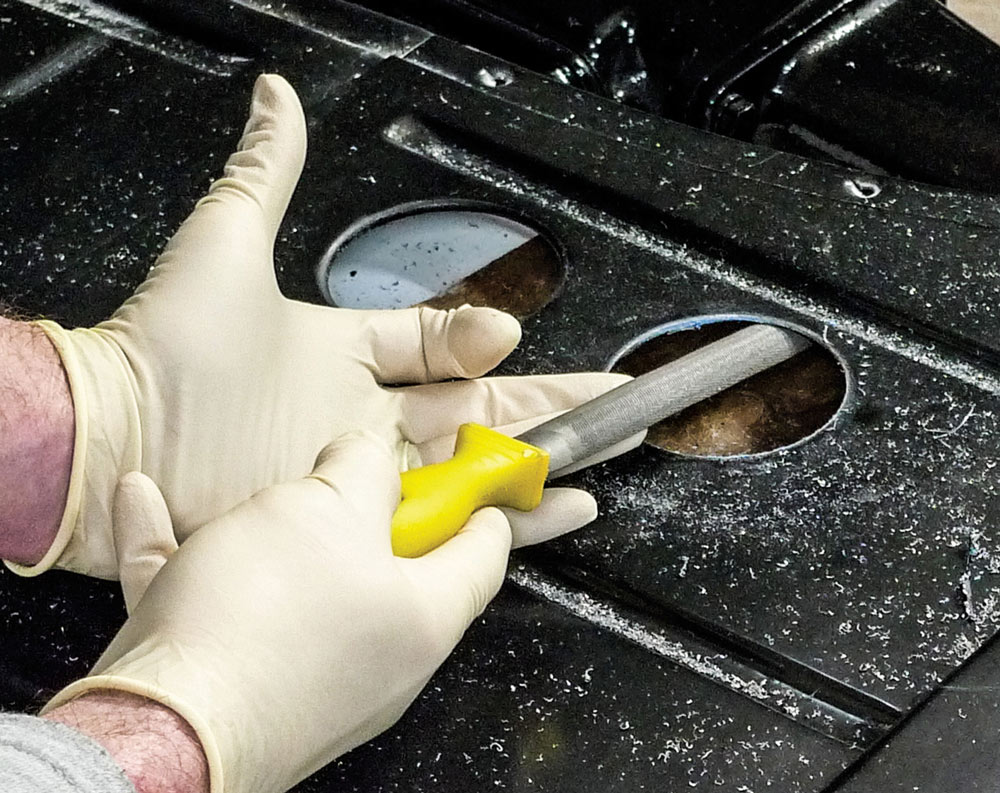

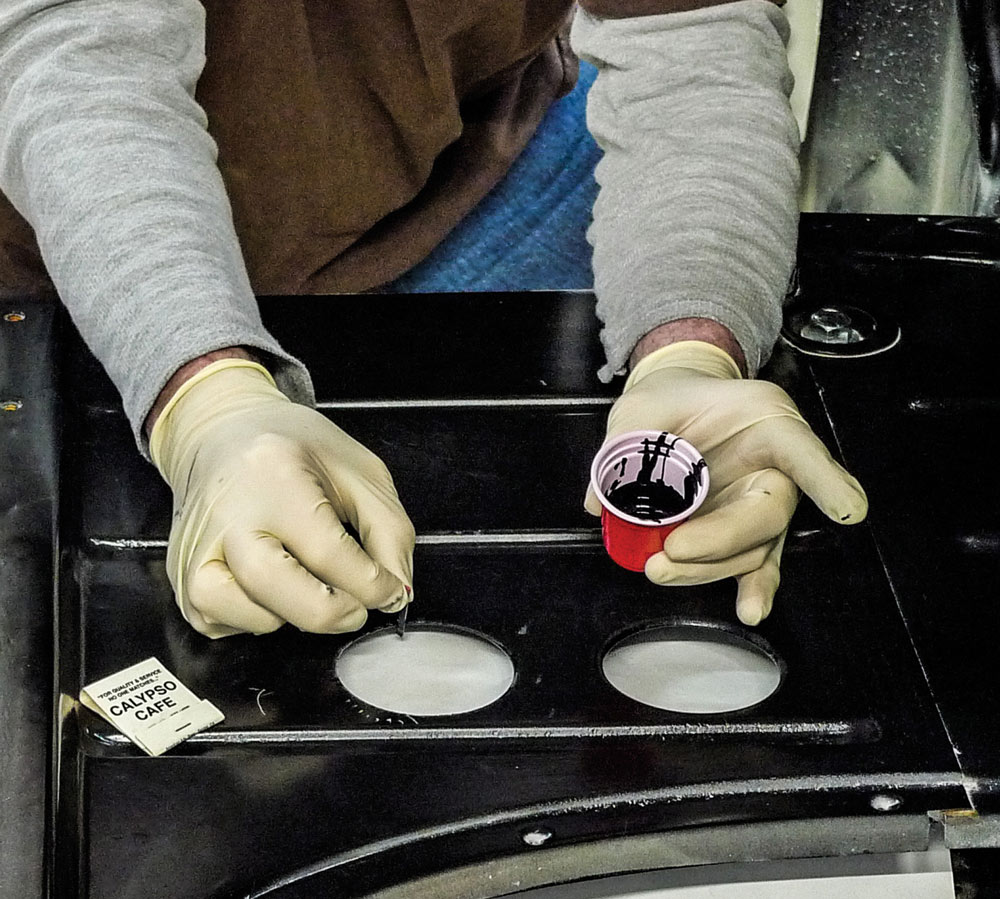
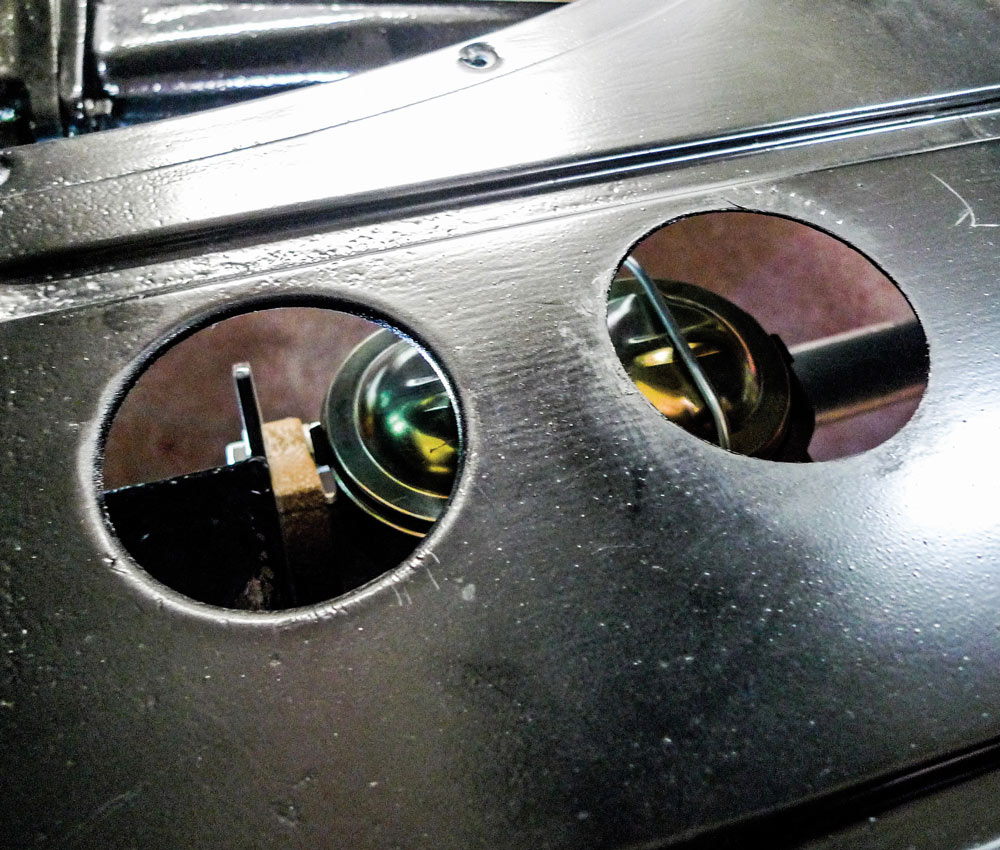
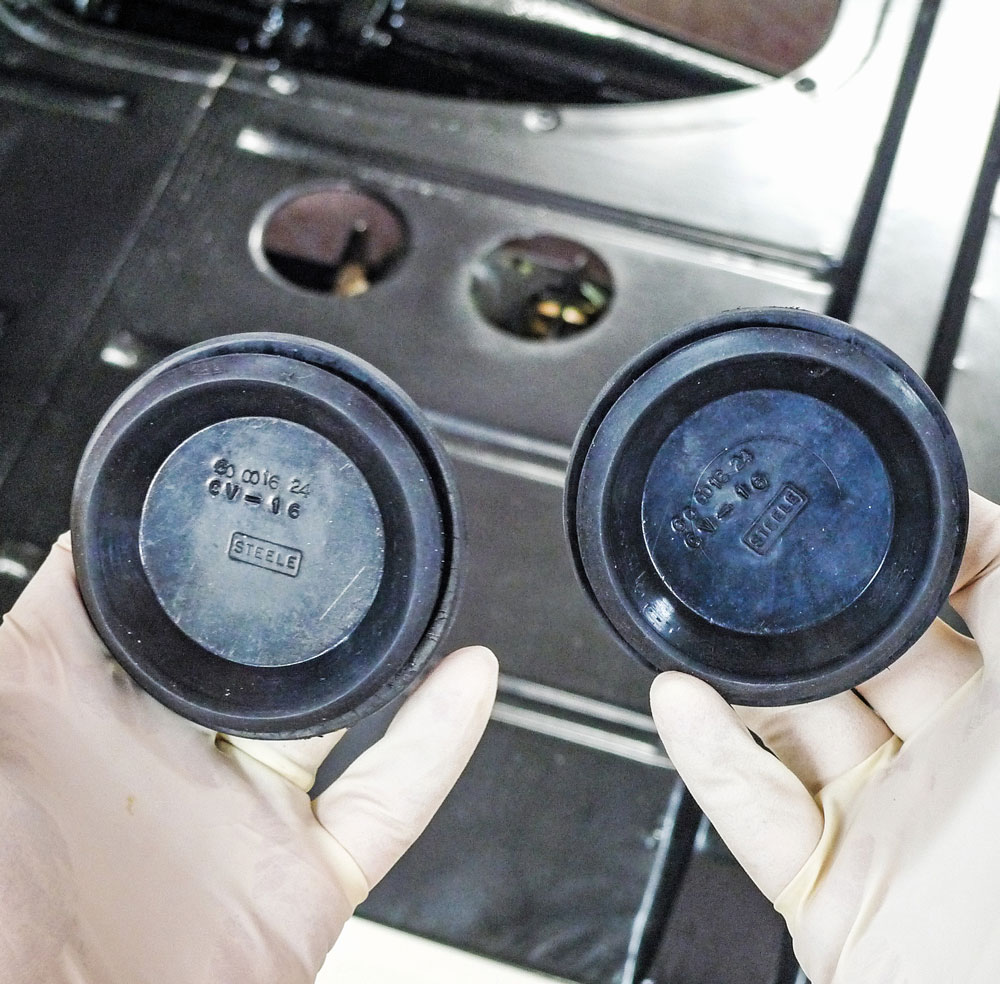

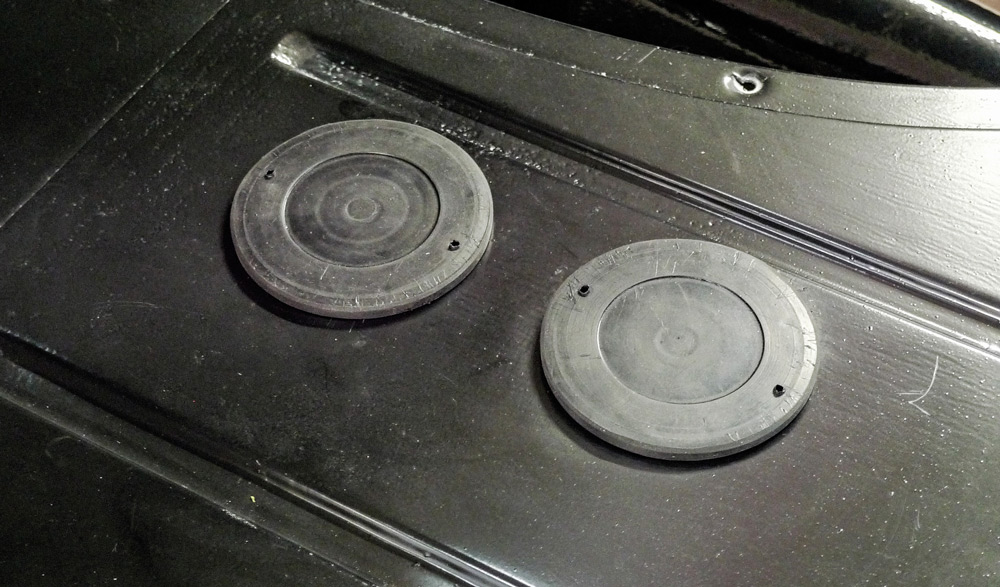
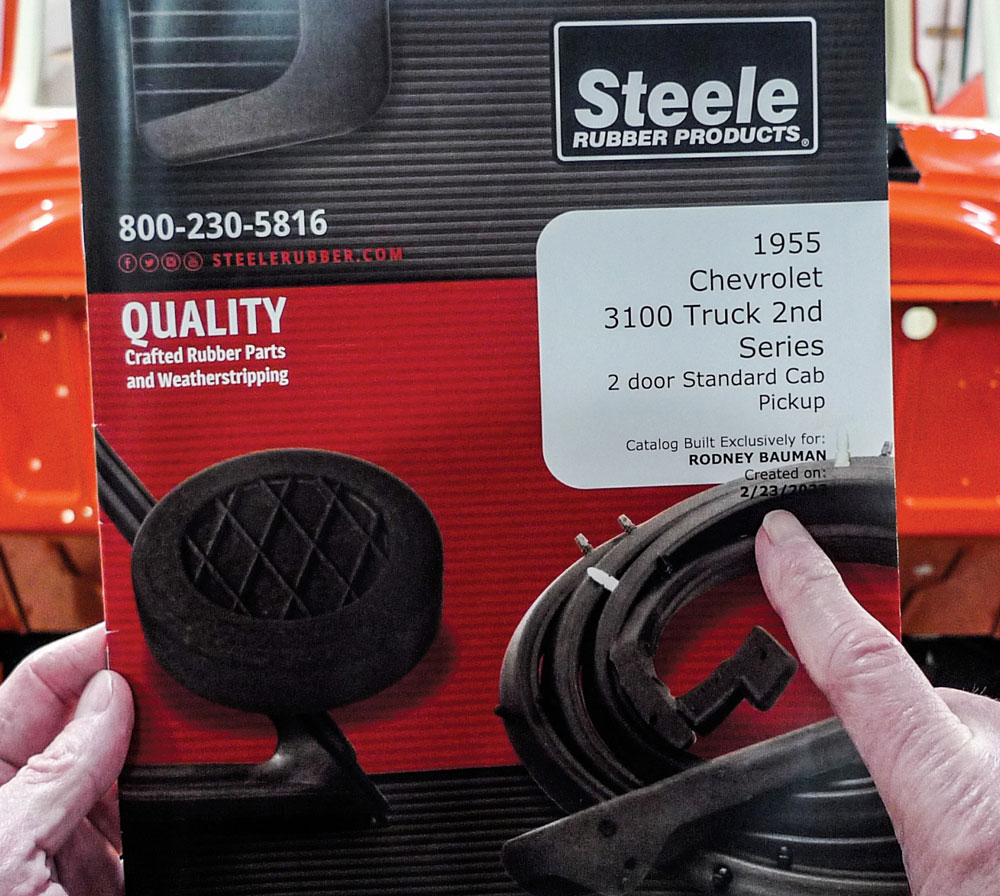
