

InTheGarageMedia.com
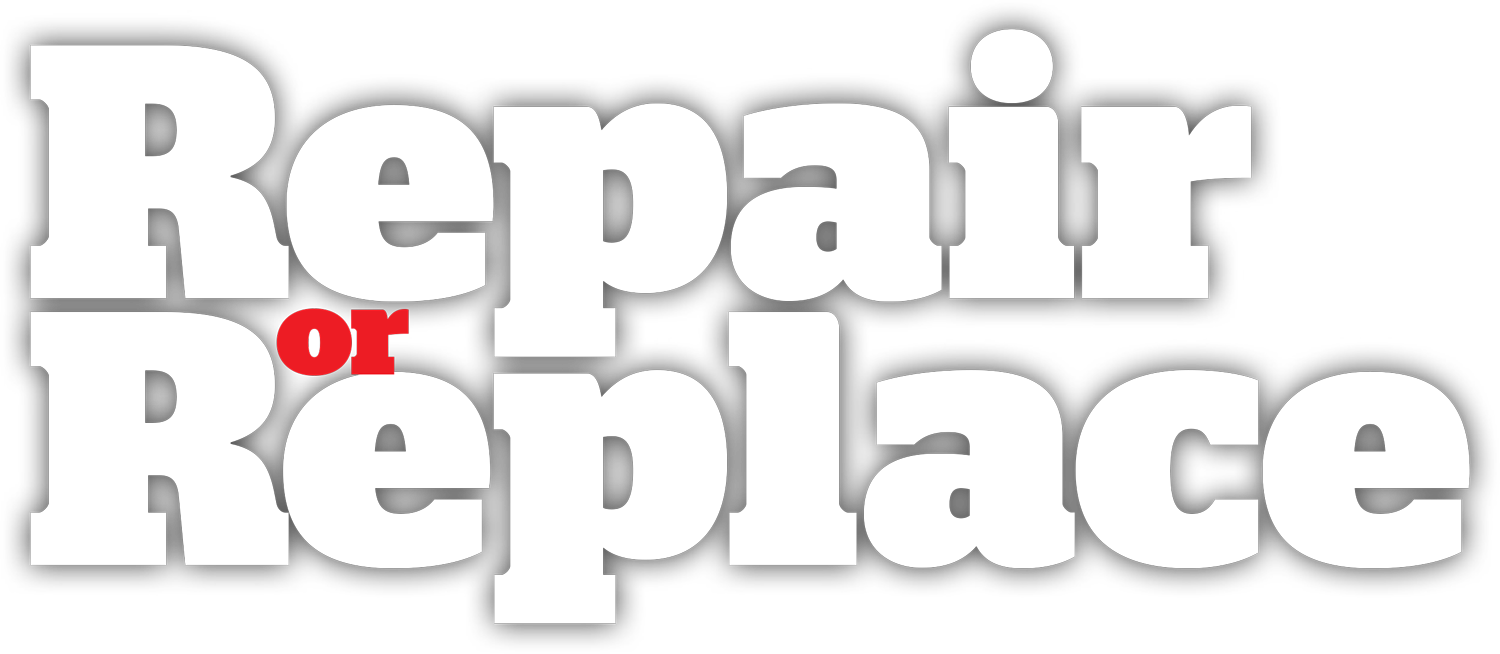
BY “Rotten” Rodney BaumanPhotography BY THE AUTHOR
ure, we can salvage an original door. Lately, however, our salvaging efforts haven’t been so cost-effective. As you may recall from last month’s installment, our ongoing ’55 Chevrolet second-series project’s passenger side will retain an original front fender and door. For the driver side we’ve procured a reproduction front fender and door, both from Brothers Trucks.
Last month’s comparison focused on fenders. This time around we’ll focus more on doors. The right side original had the usual issues that we’ve pretty much come to expect. From the gate we saw the need for outside corner patch panels, so we ordered up a lower doorskin from Brothers early on.
Certain sections of the old used door required abrasive blasting. As usual, blasting exposed other needed rust repairs, mostly along the inner doorskin’s lower edge. In the end our skin-grafting procedures were successful. Some door-edge modification rendered better-than-new gaps. That went quick and fairly easily. Necessary fillerwork, however, totaled up to more than we’d like to admit.
When we do begin on the new-reproduction door we’ll call out any flaws we may discover. Truth be told, it’s an older reproduction that’s been leaning against the body stall wall now for years.
Years ago, our reproduction door was test-fit to the truck. At that time we managed to achieve acceptable alignment without adding or subtracting edge metal for gaps. It’s a good fit. It’s a Brothers door, but not necessarily the same-brand door that Brothers stocks today. The one we have is silver. In our most recent catalog, the newer ones are black—and quite possibly further refined.
It’s been a while or two since we’ve actually checked, but last time we did, a brand-new reproduction door shell was just under $500 from Brothers. Shipping to our Northwestern Montana location would have cost about as much, but even so the reproduction could still prove to be a bargain. Here as we go, we’re intending to find out for sure!
First, we must ask, have you ever latched onto a Morgan Nokker? For those unfamiliar, it’s just another age-old body shop tool. Think of it as a heavy-duty side-hammer set. As we go on to discover our doors’ minor differences, the Morgan Nokker will play a key role.
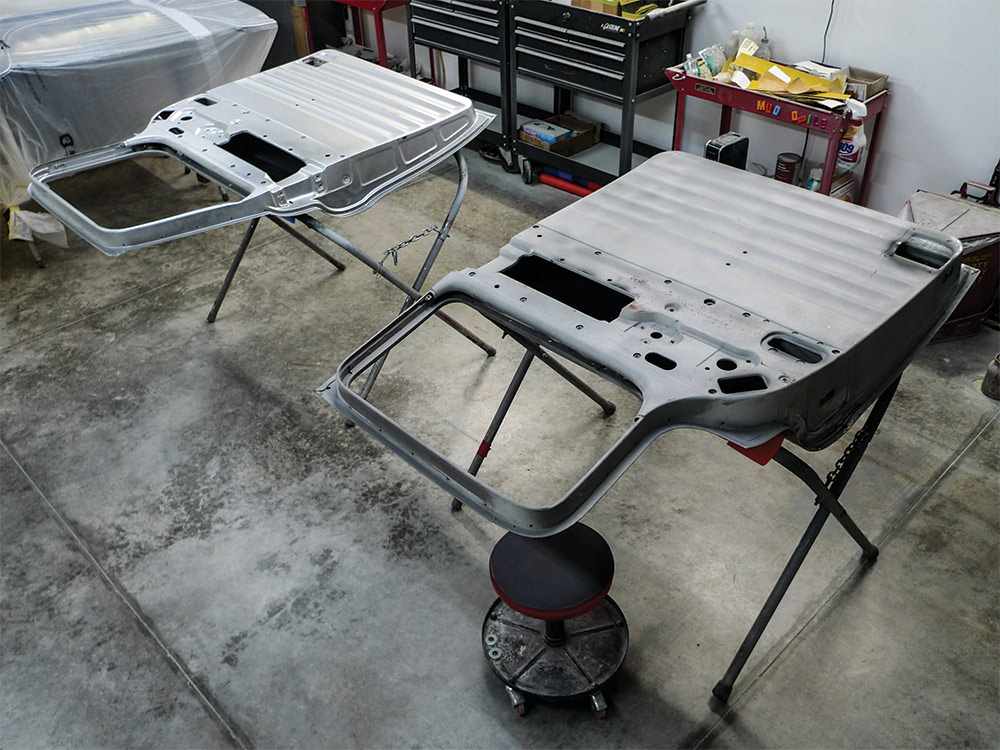
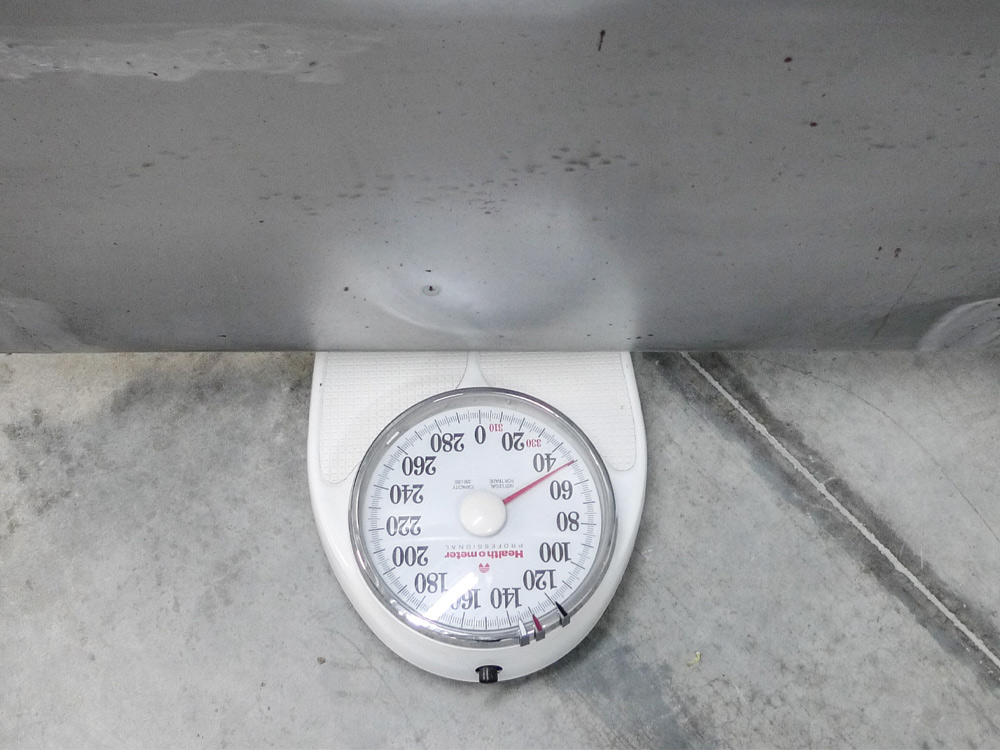
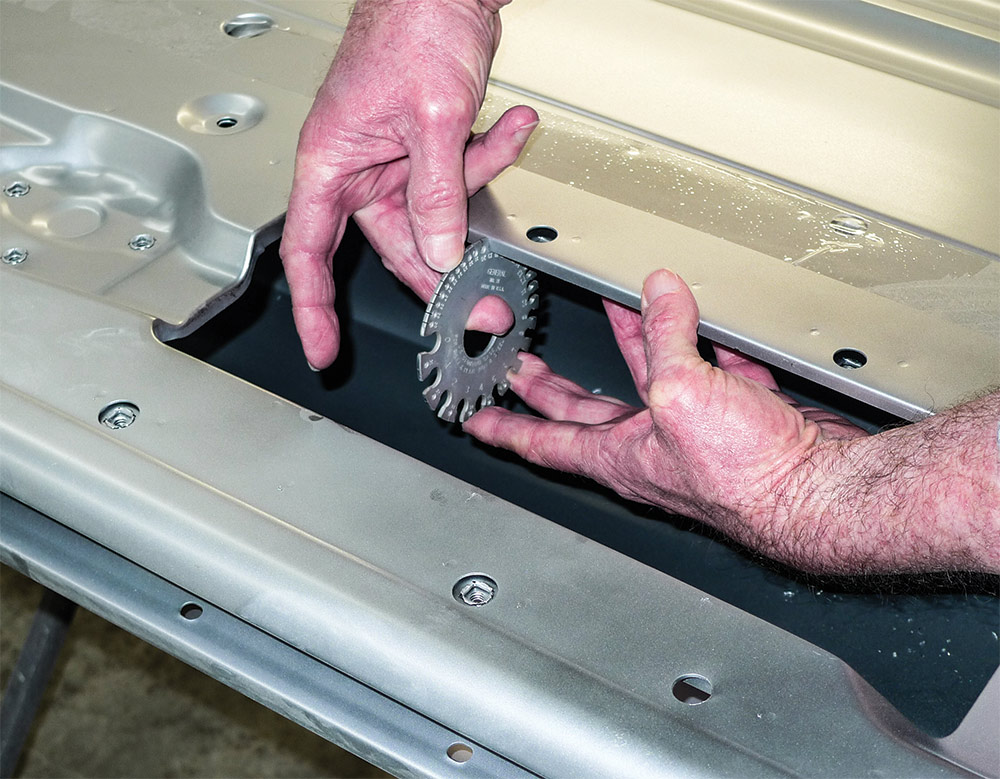
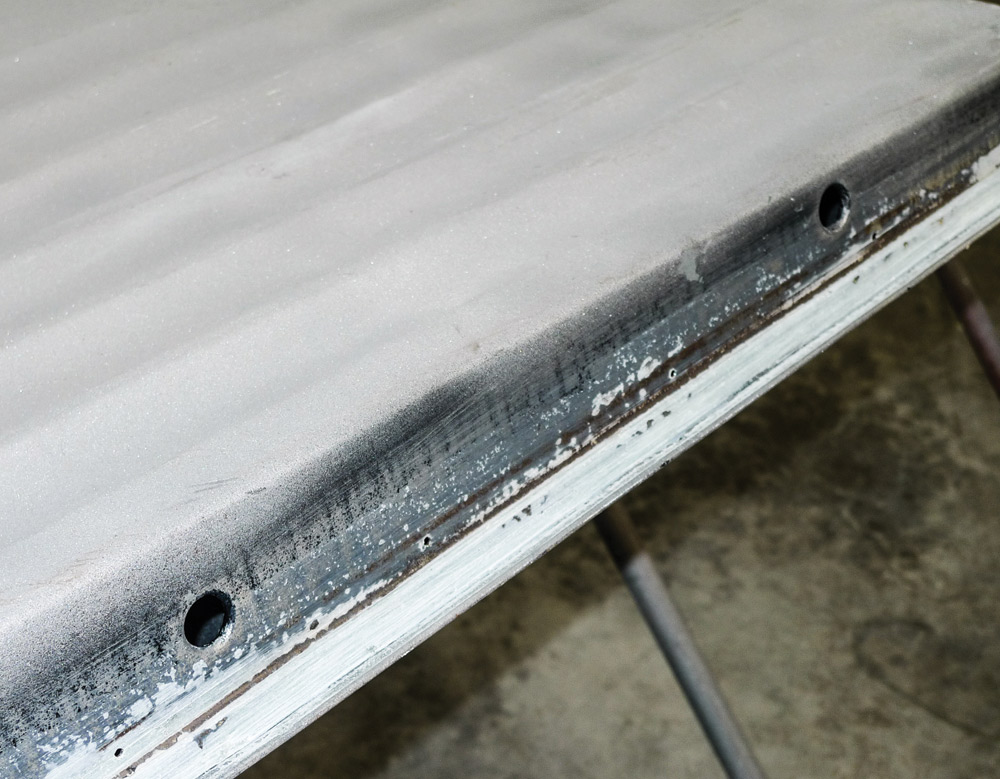
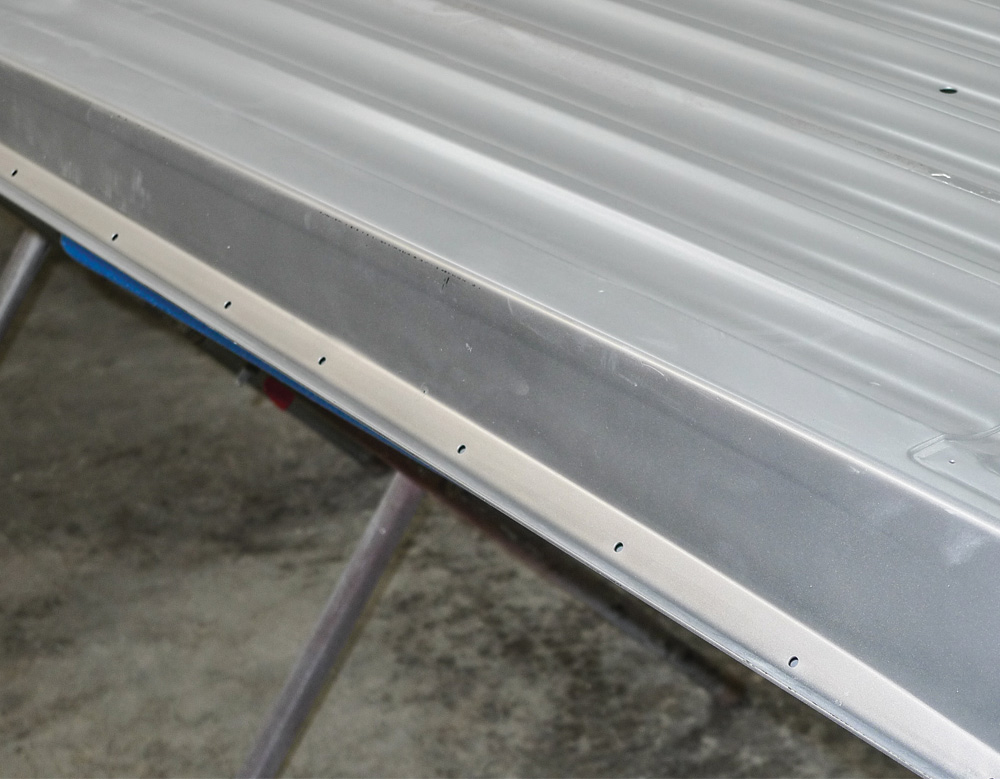
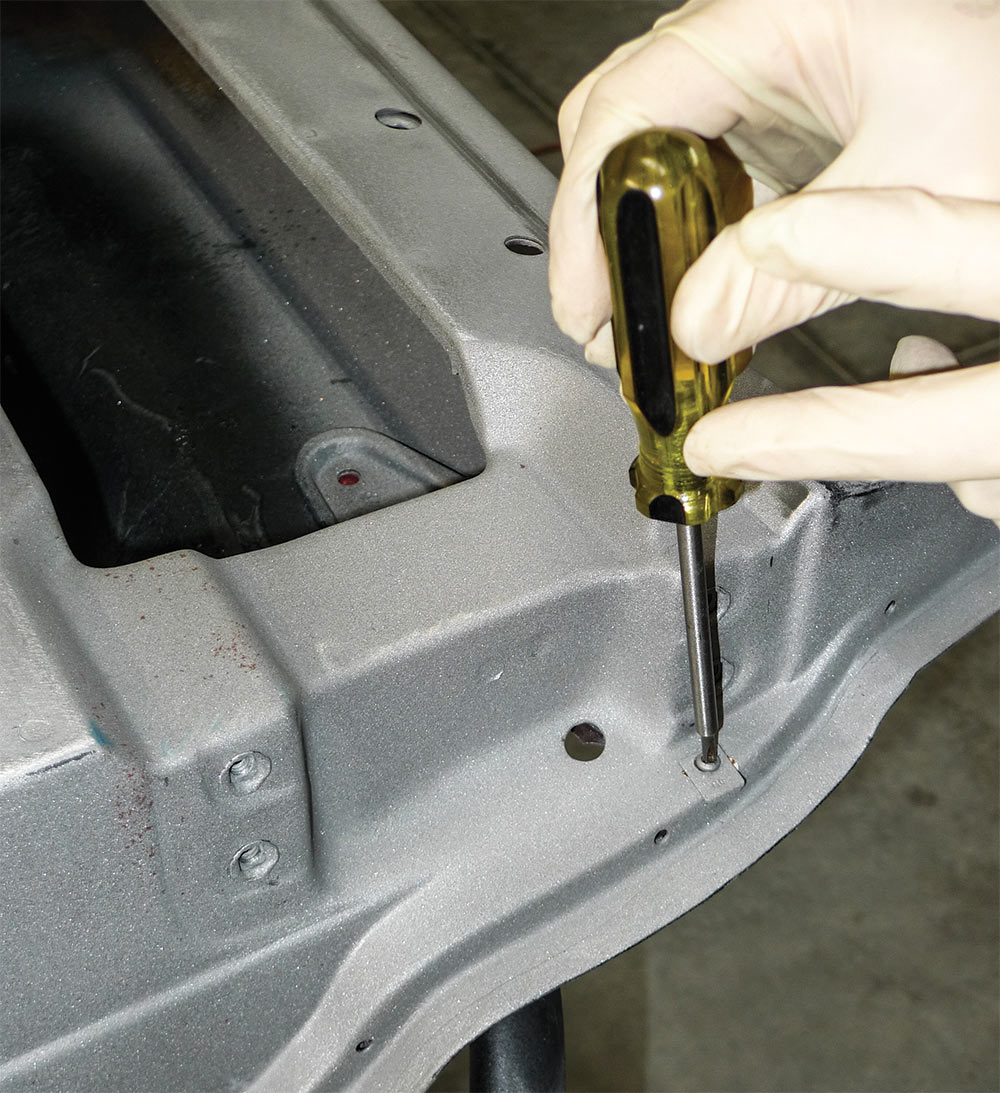
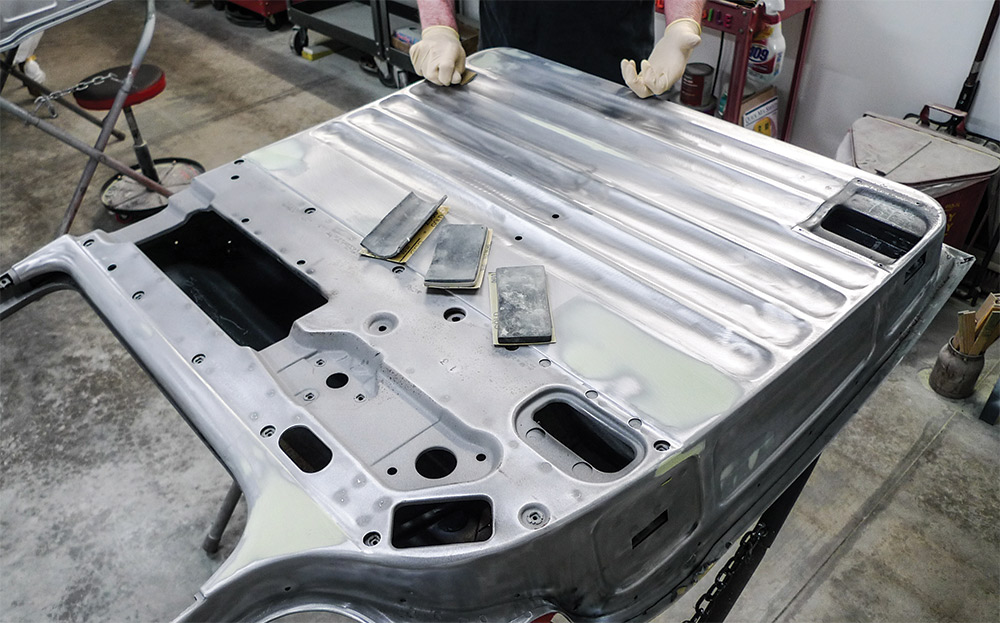
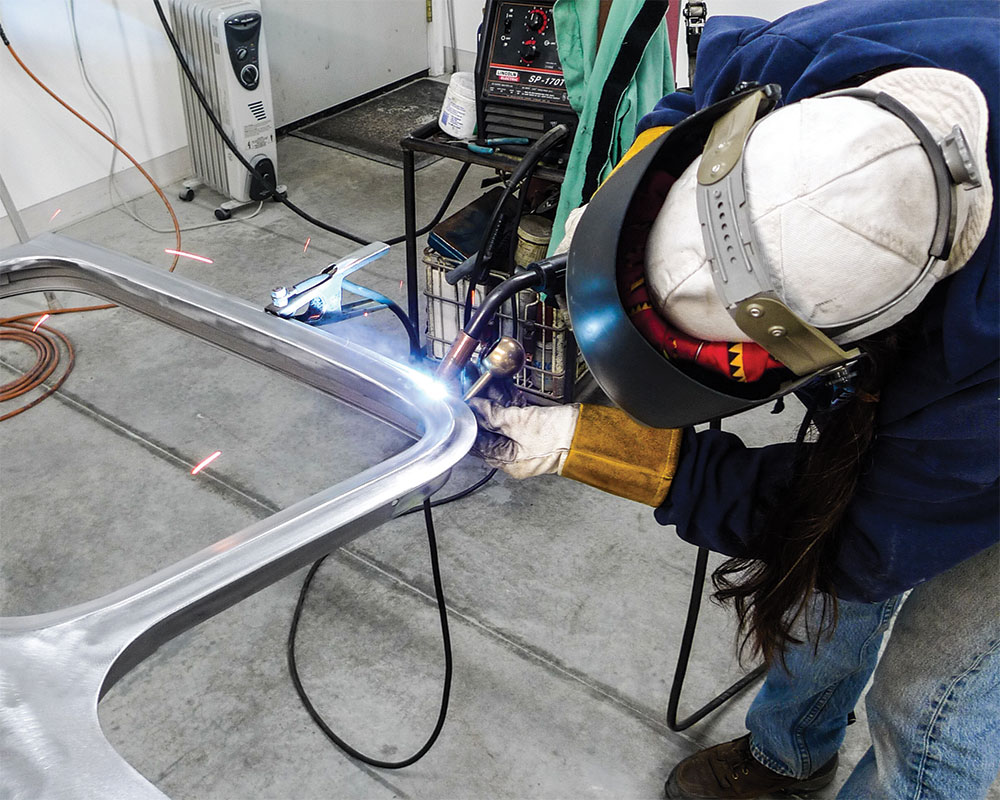
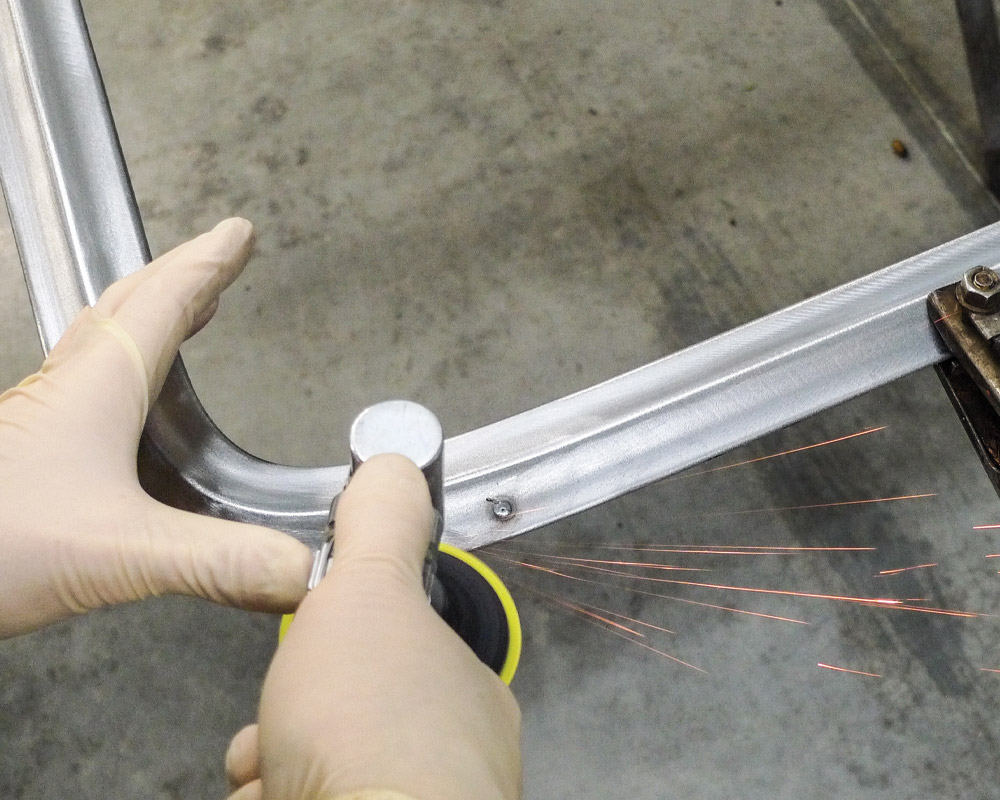
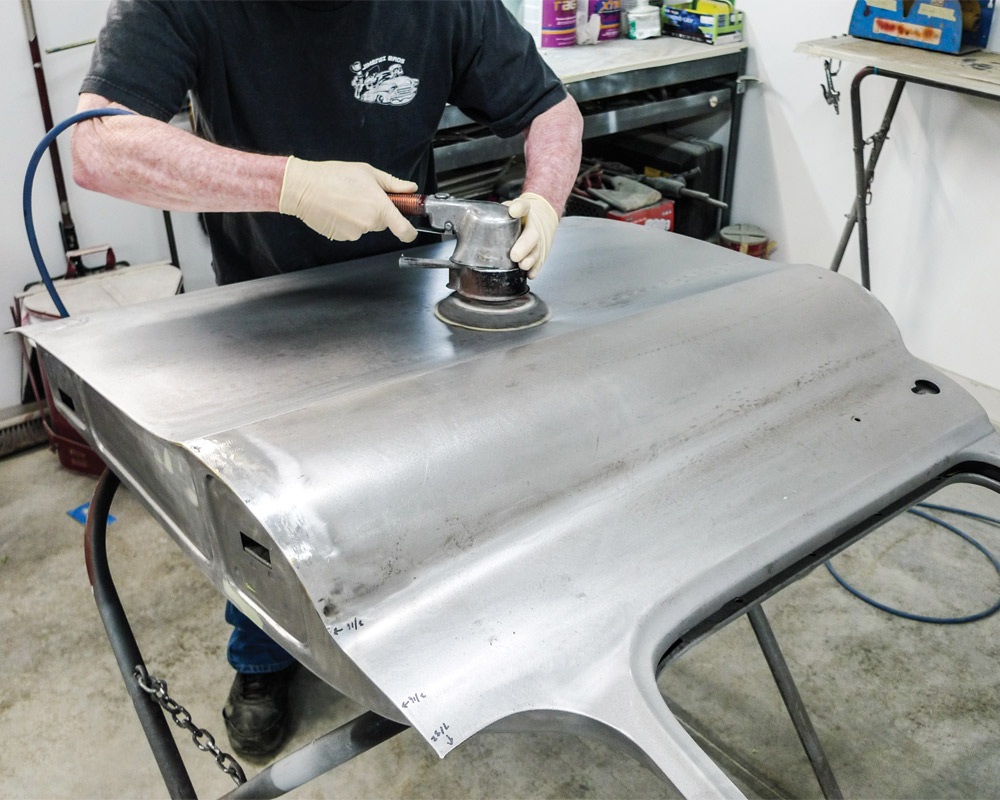
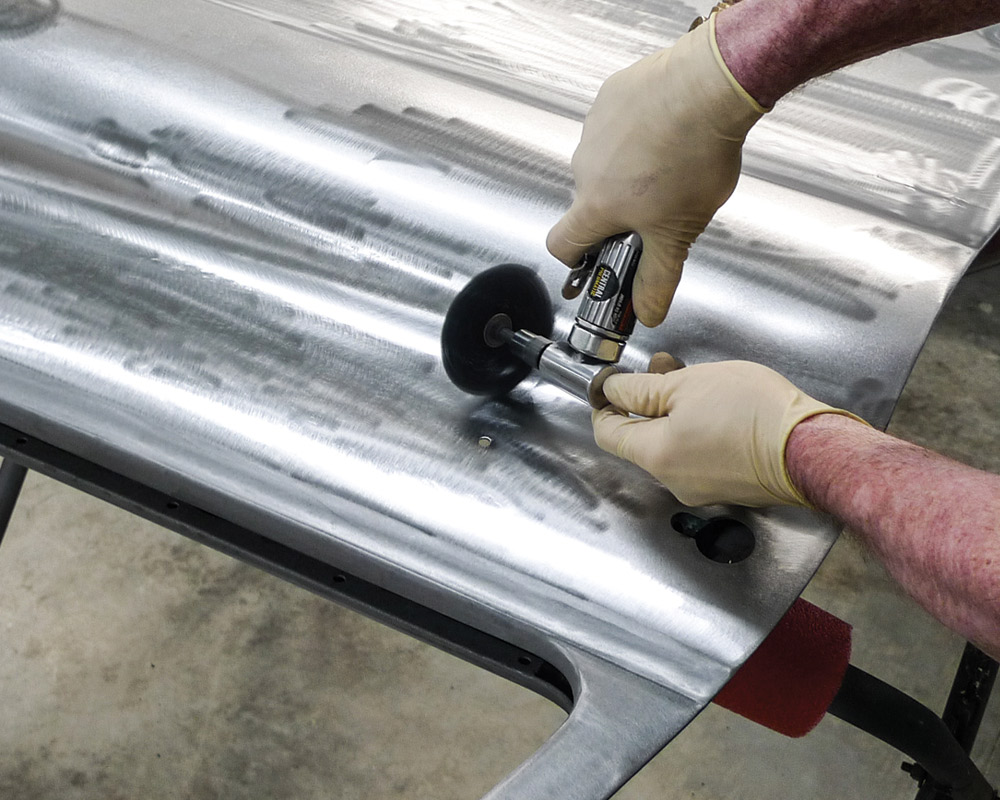
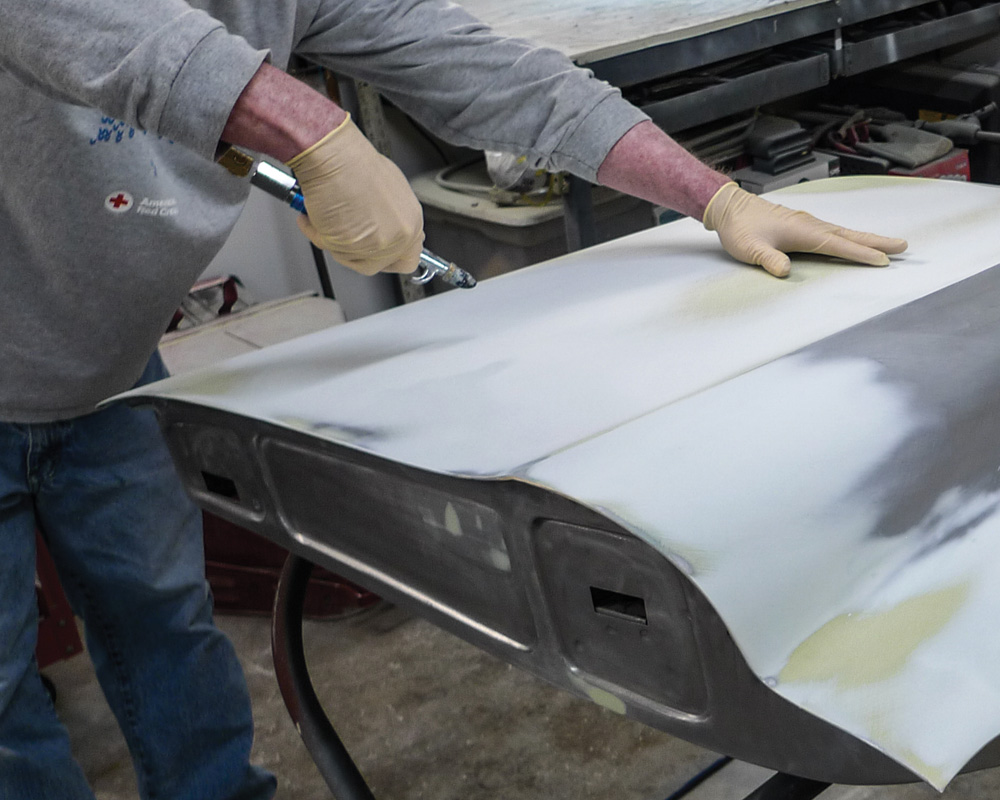
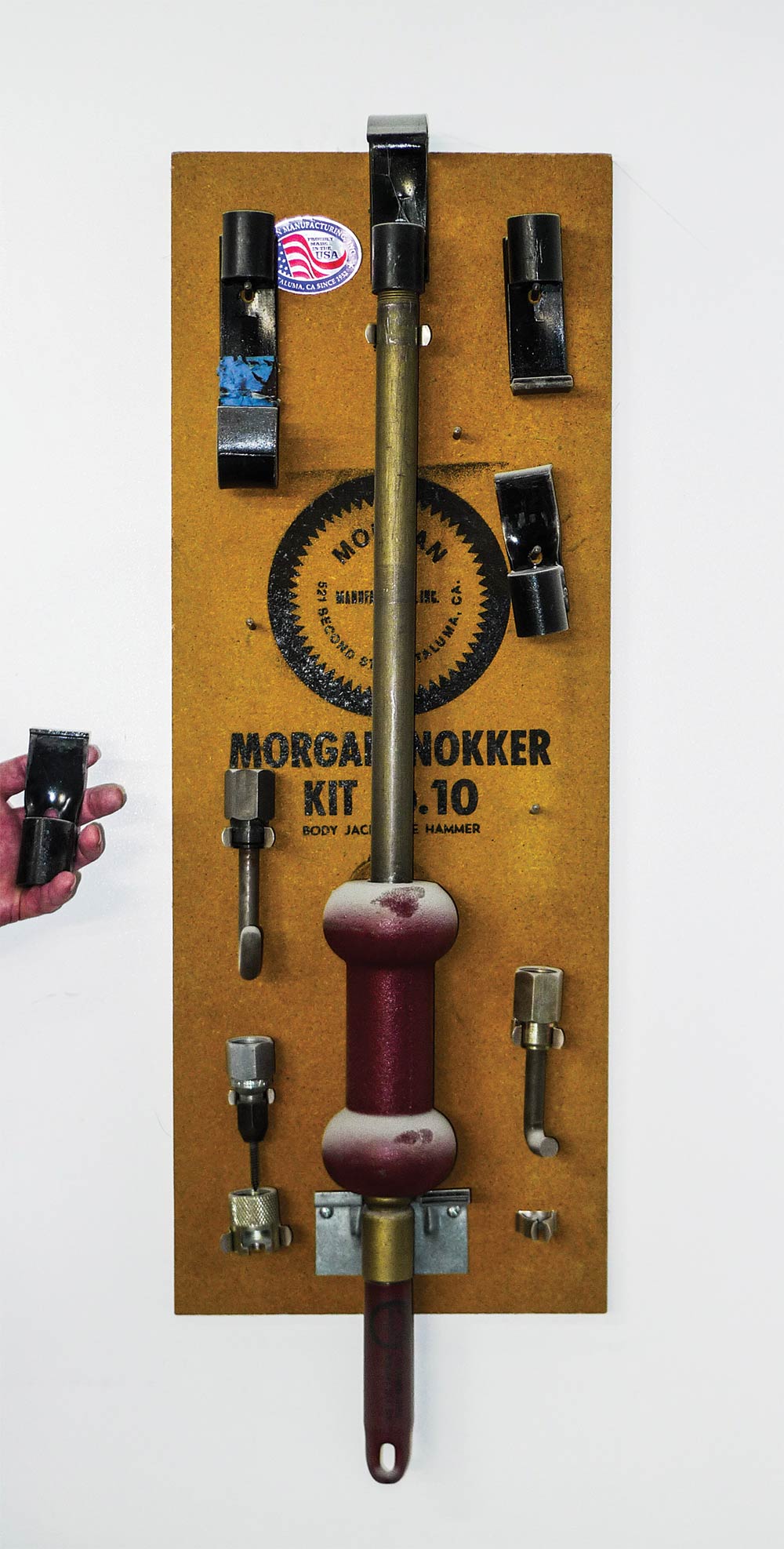
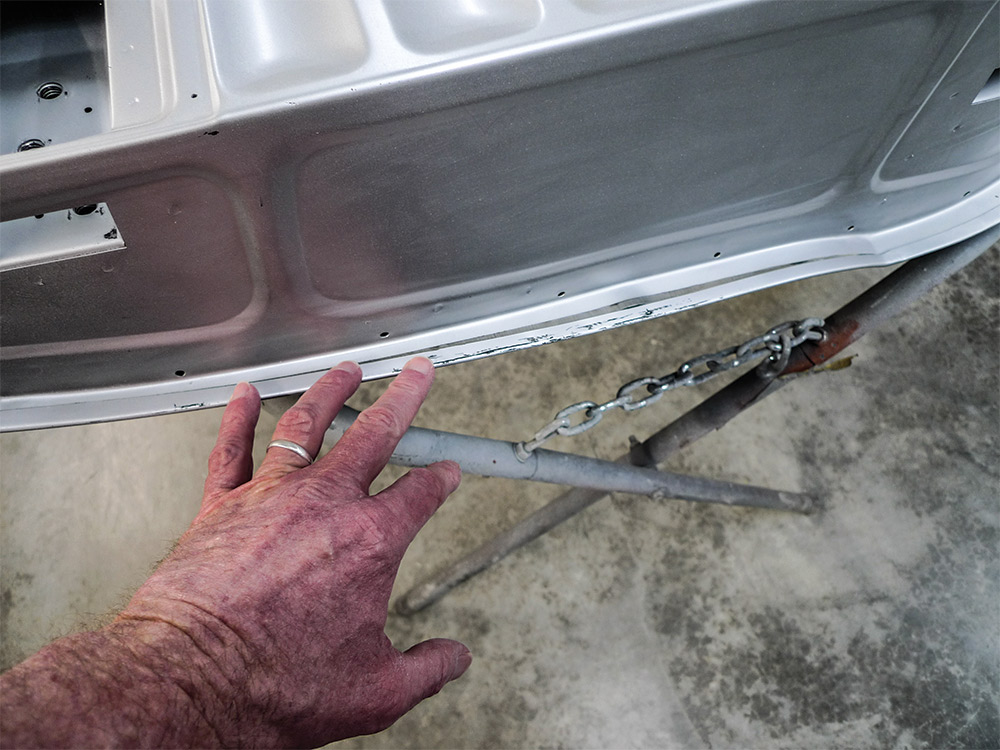
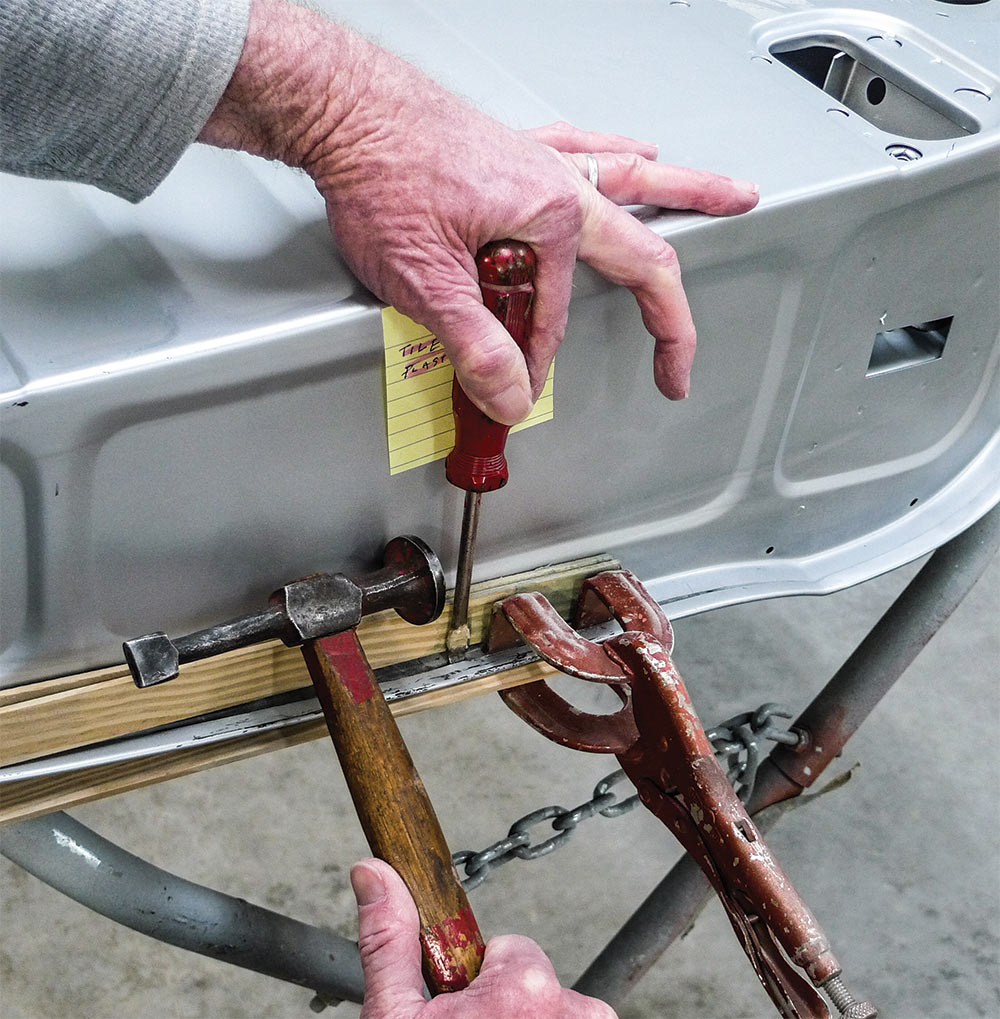
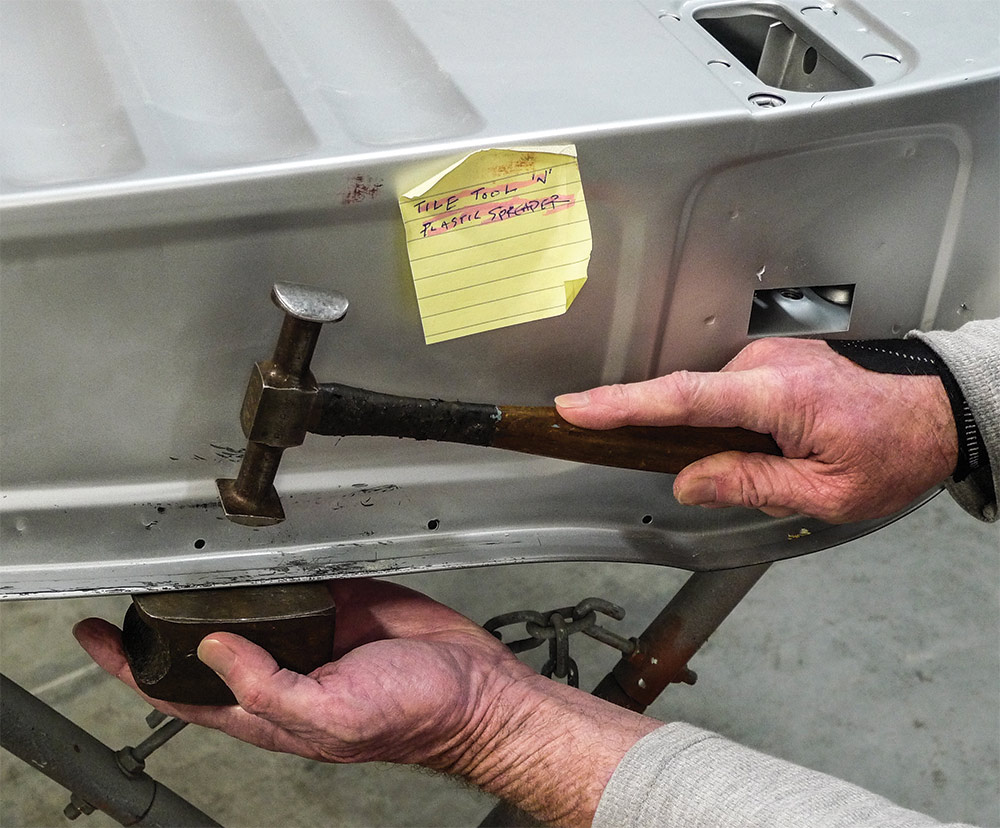
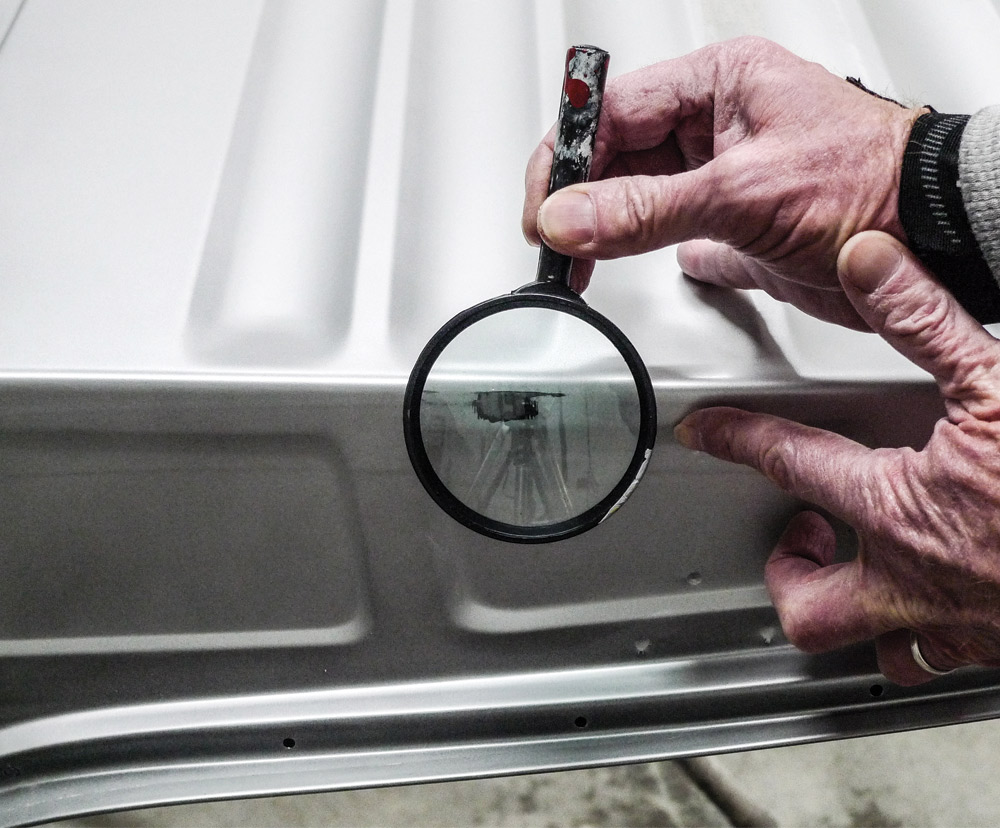
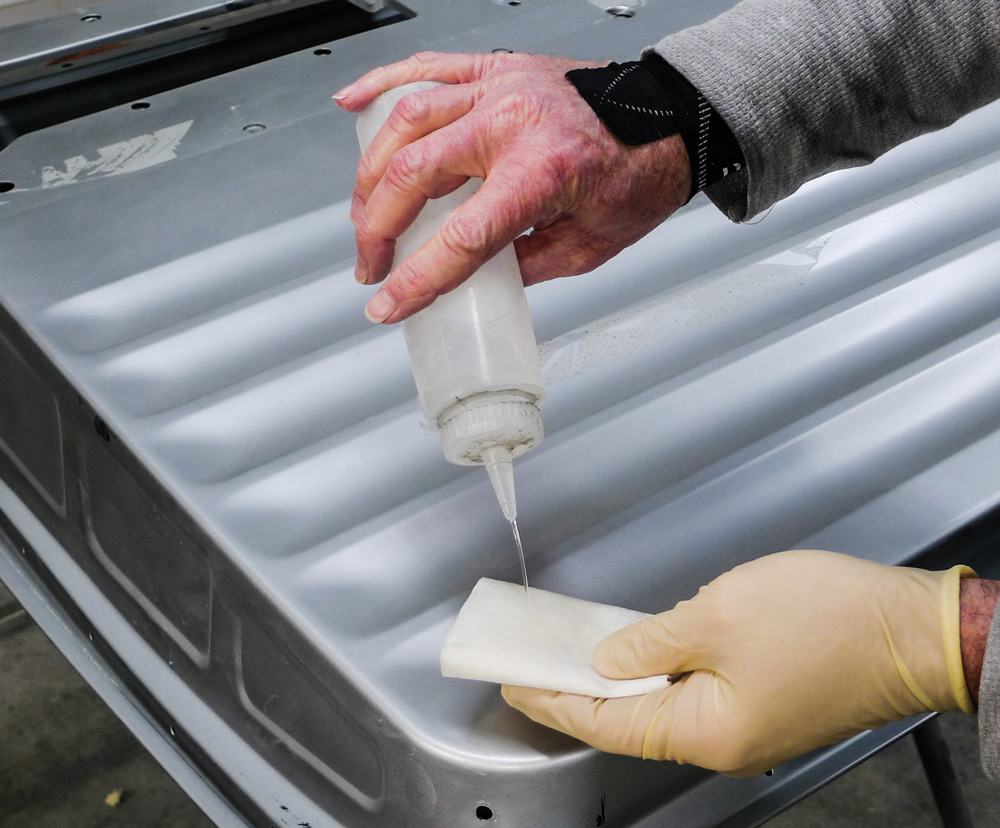
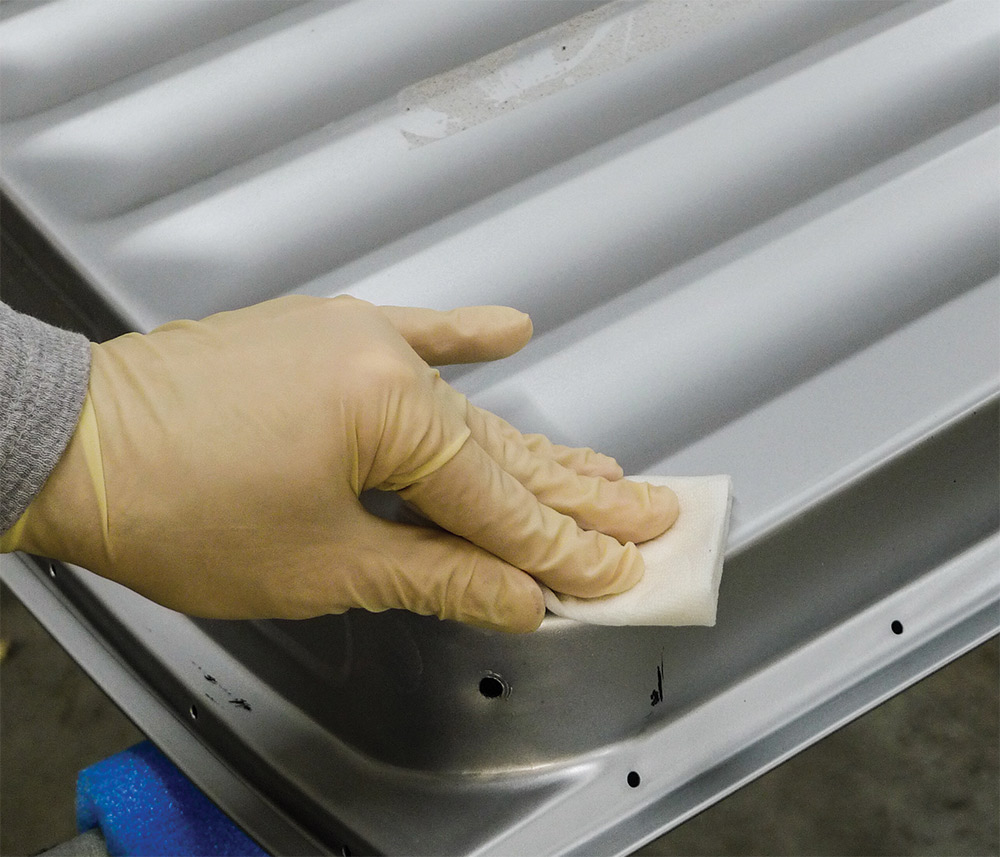
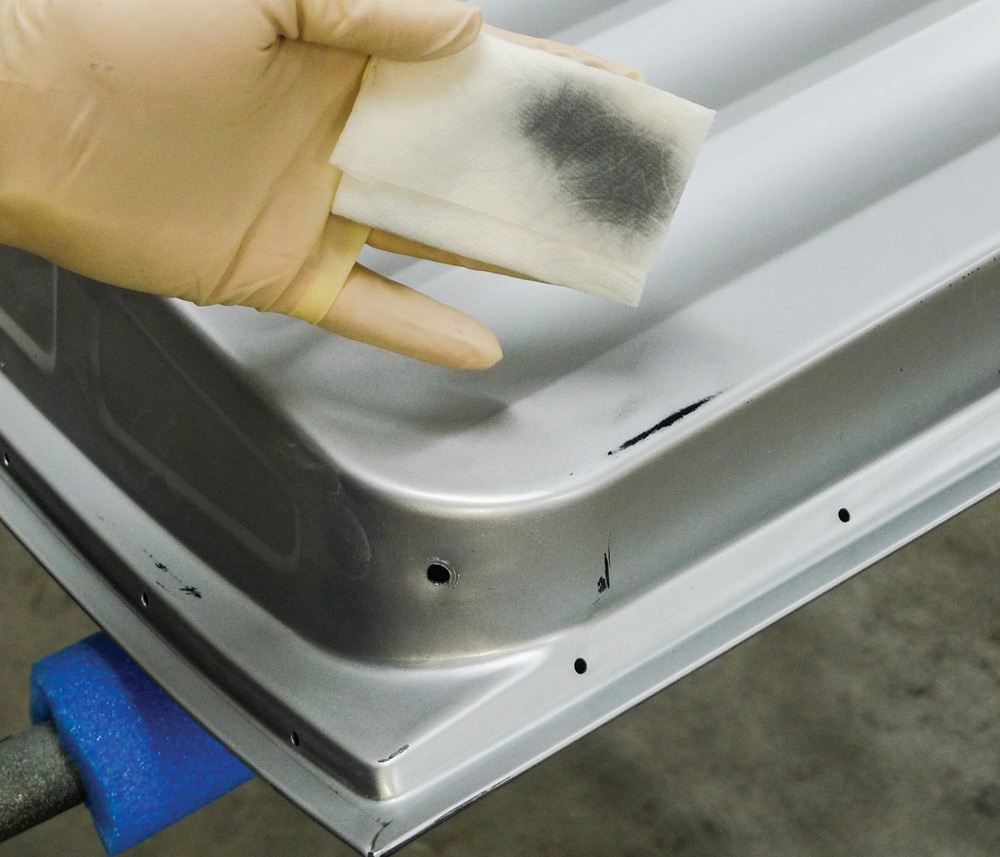
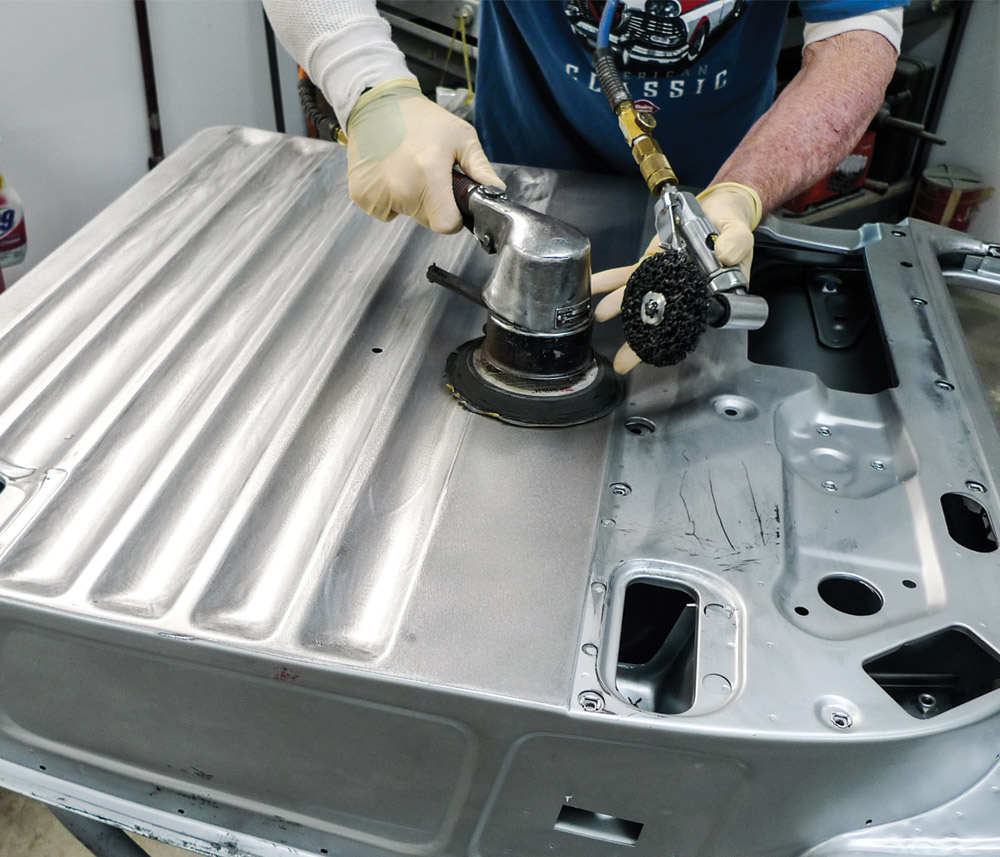
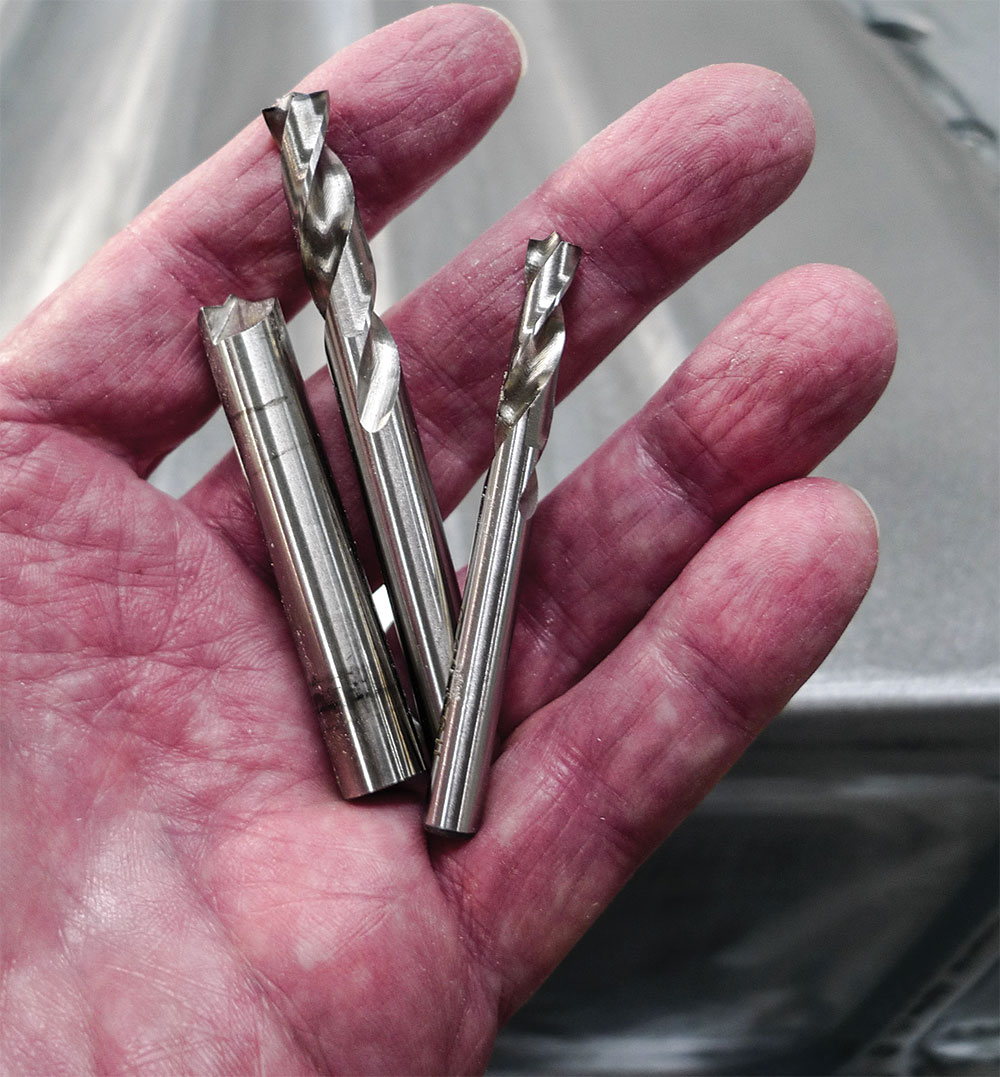
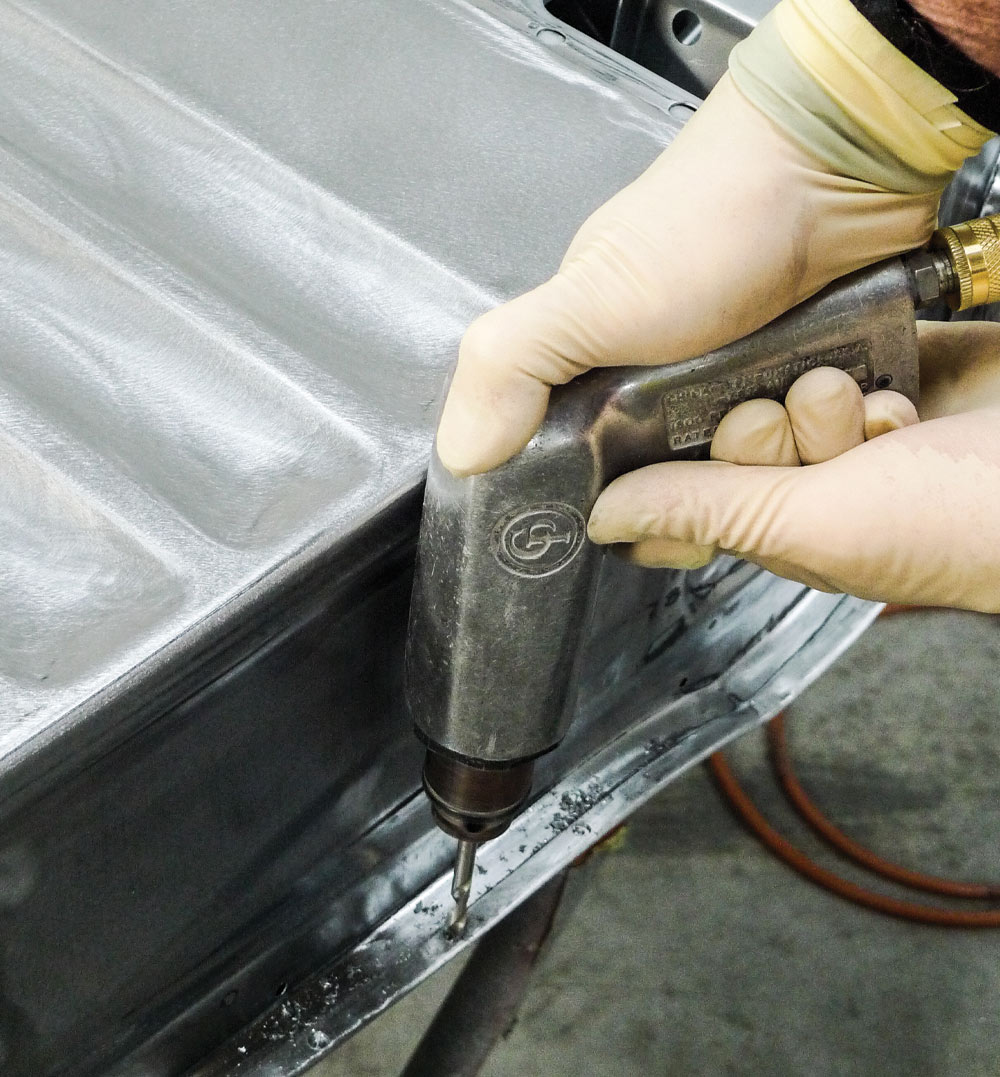
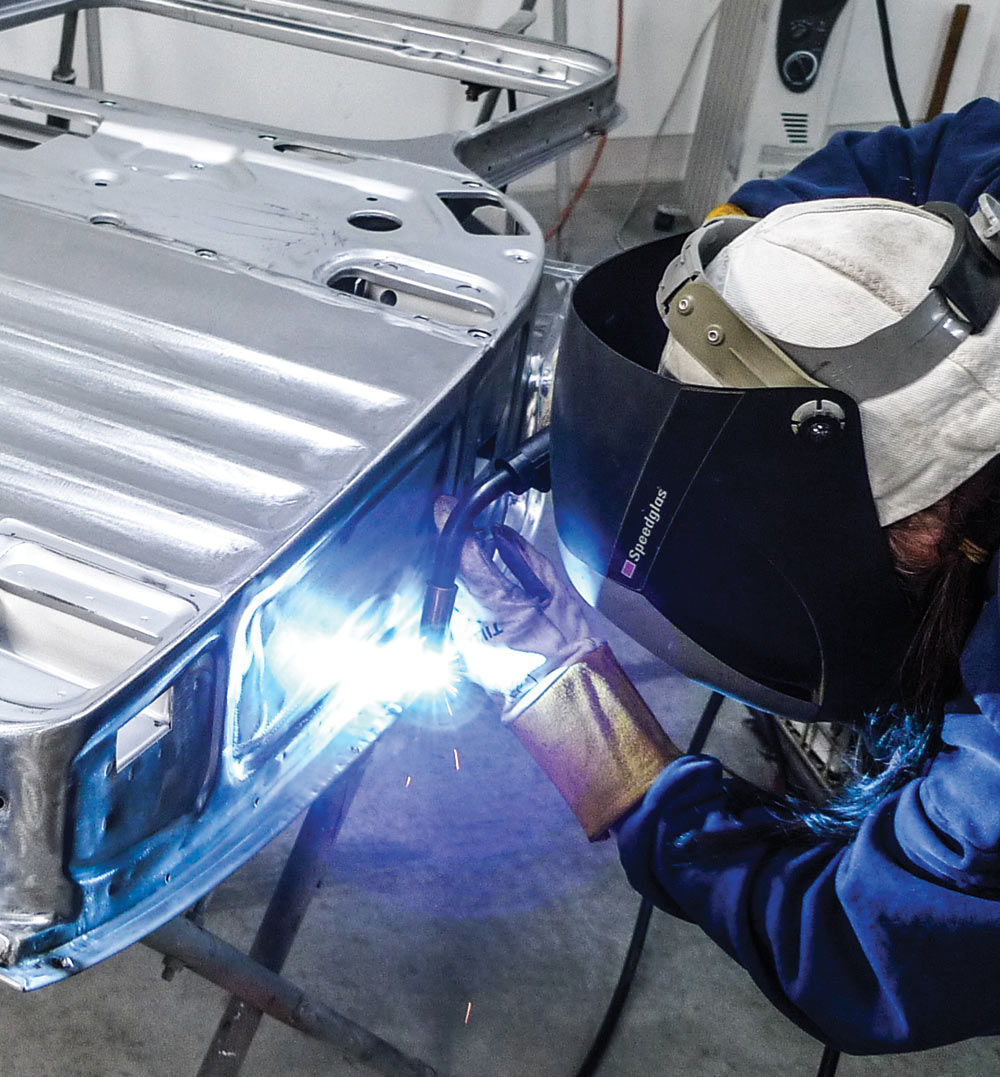
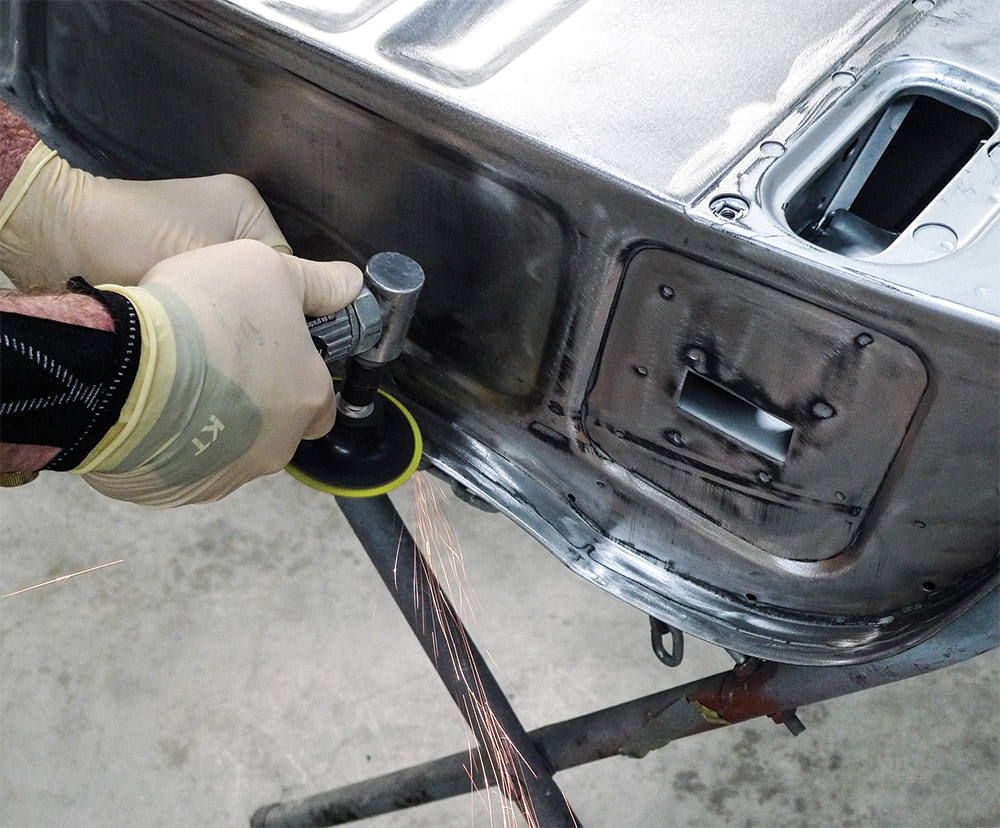
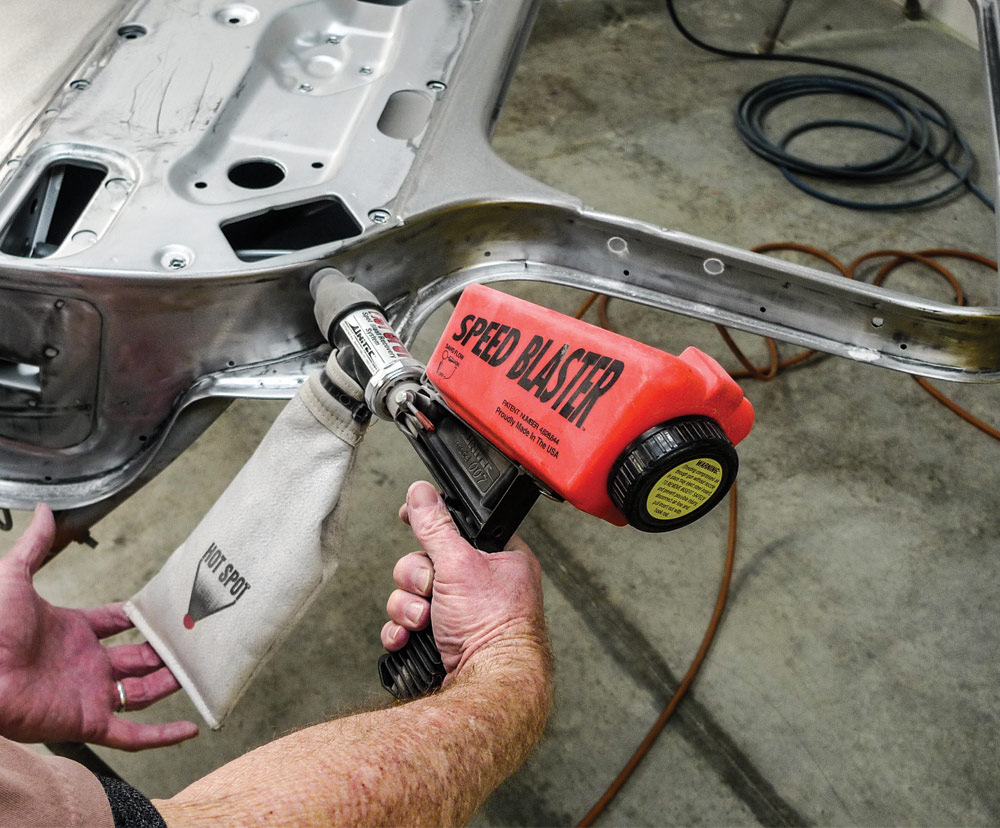
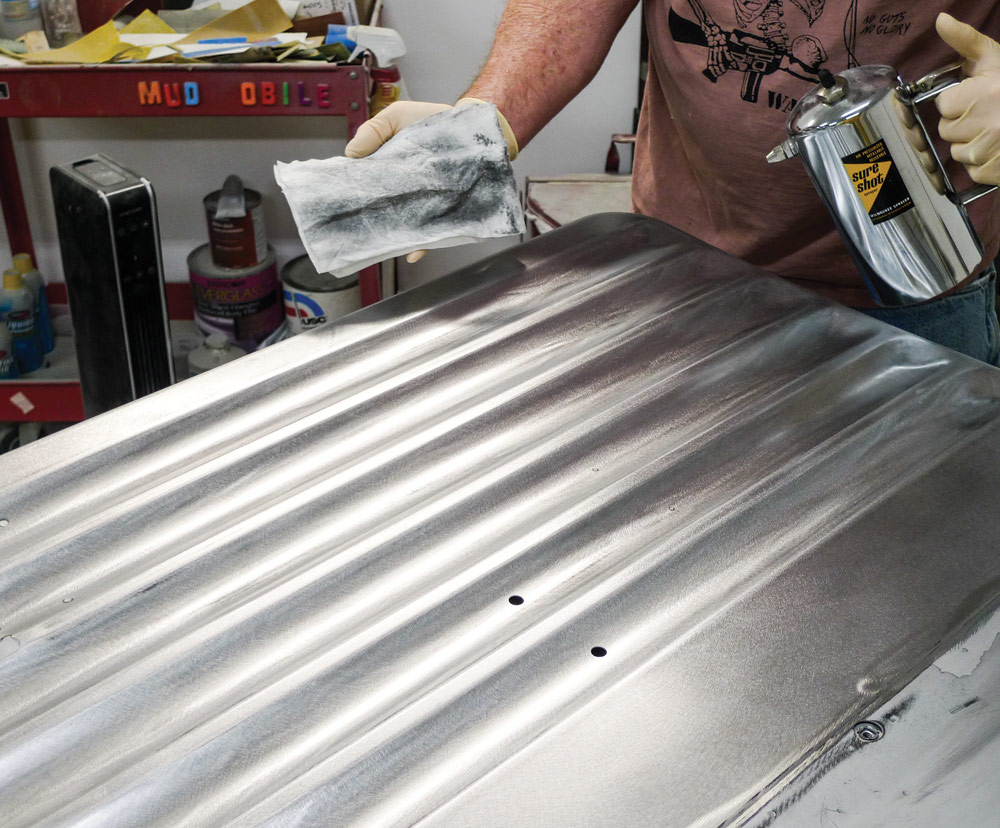
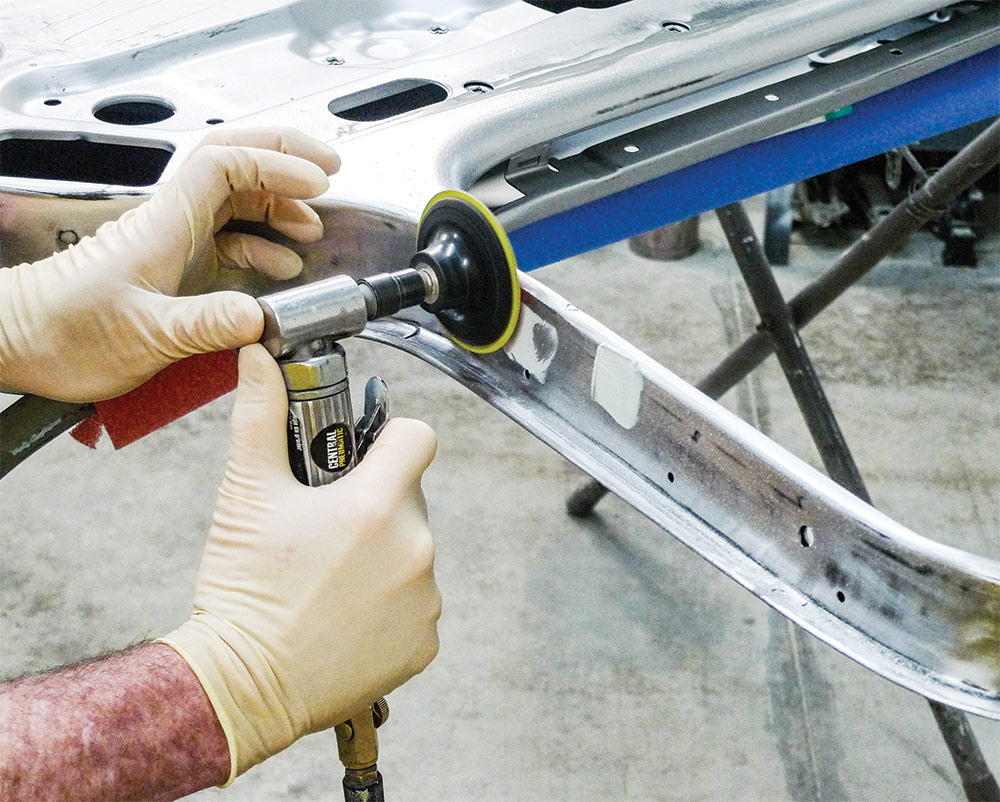
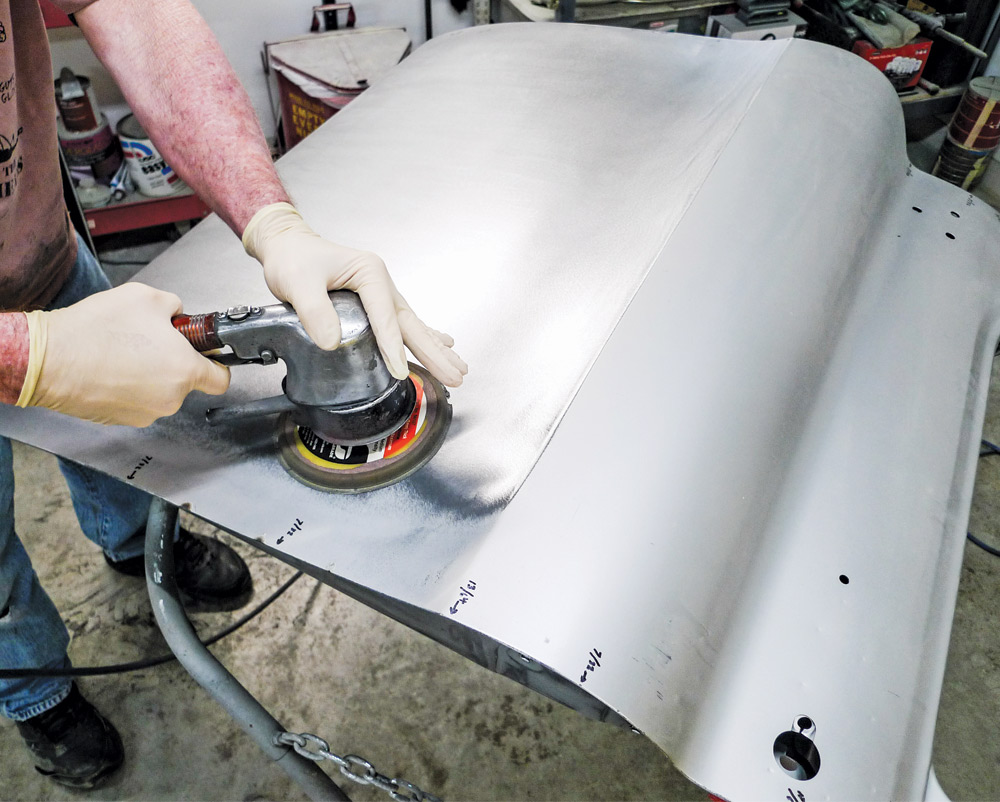
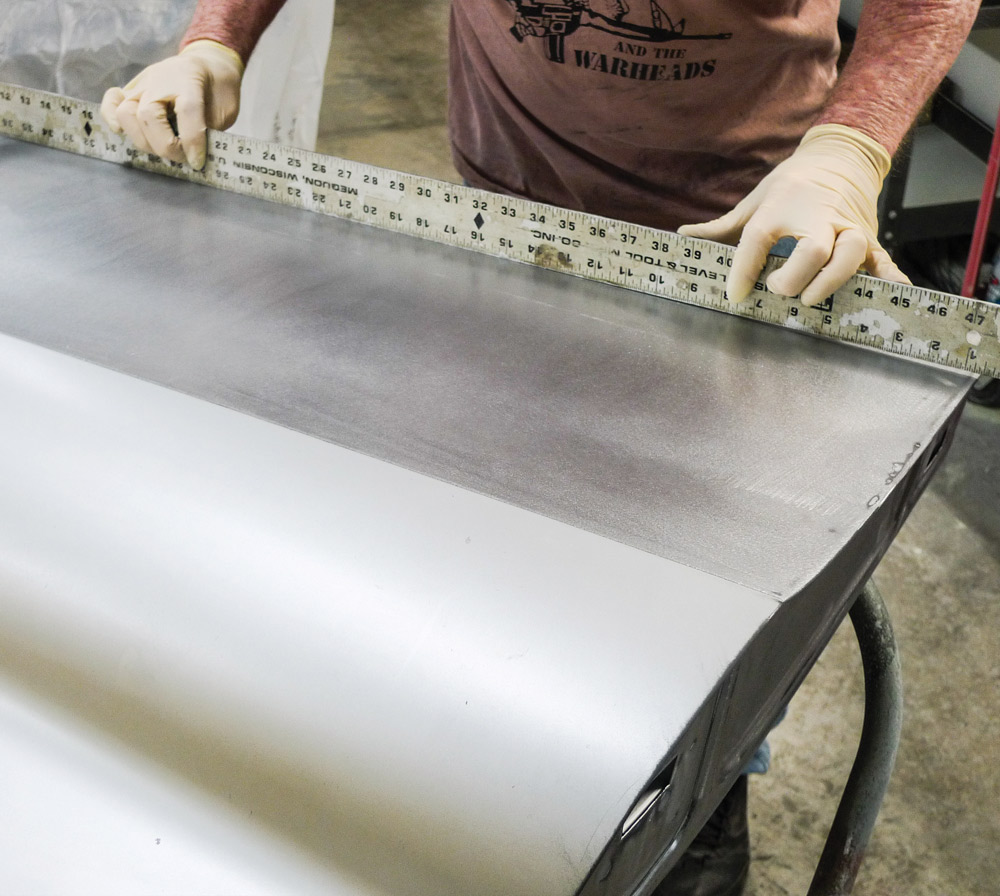
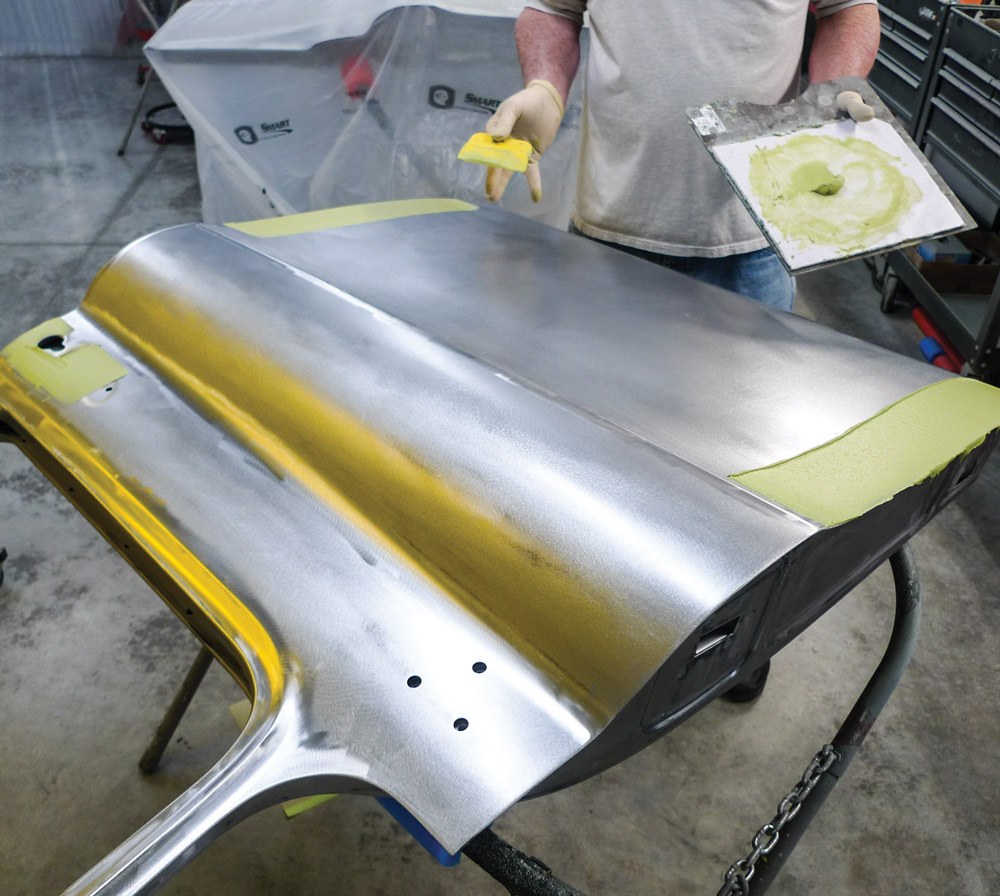
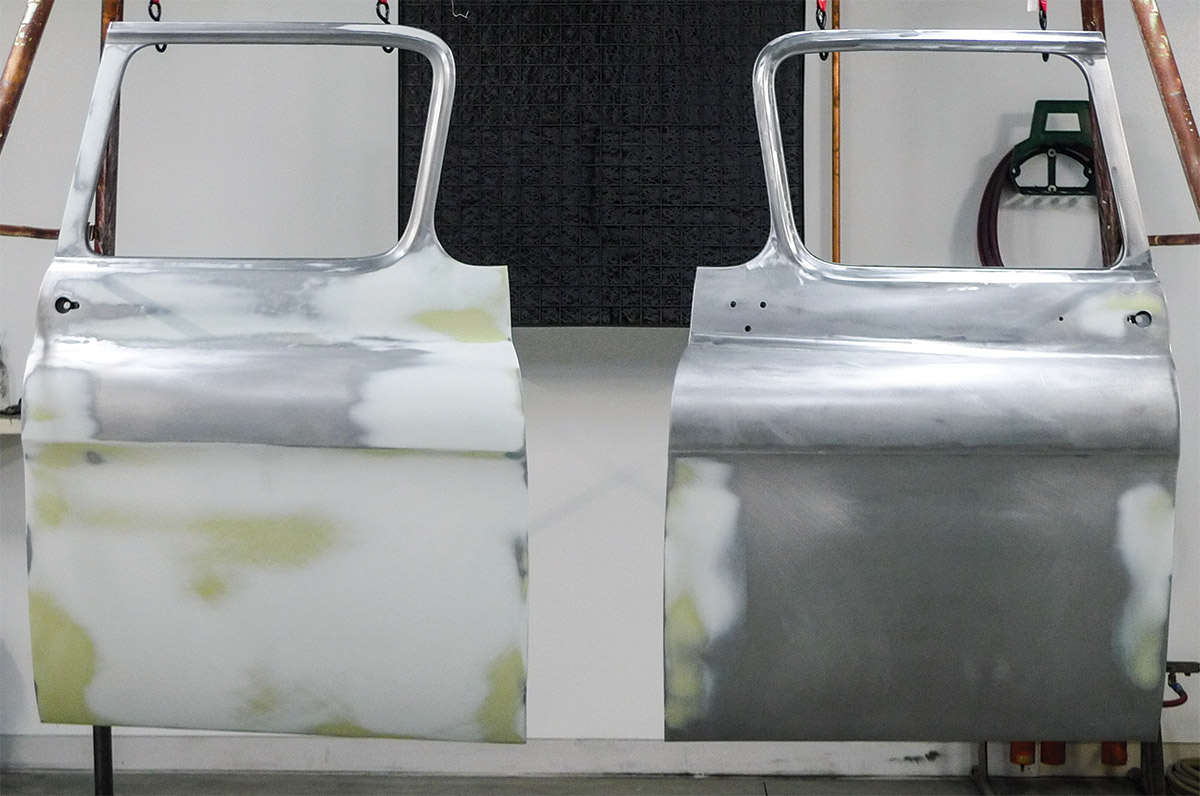
