

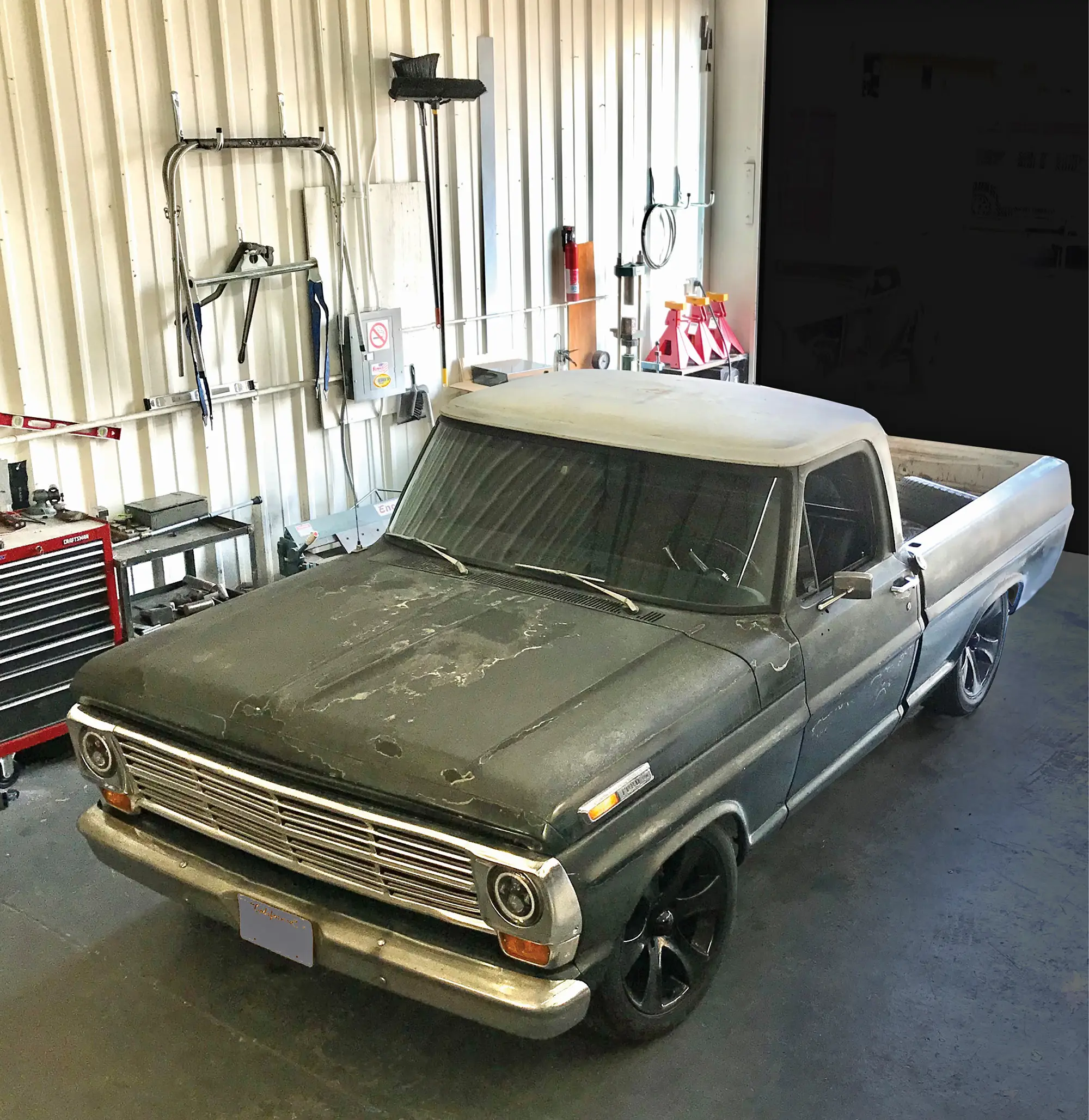


n the mid ’60s a new class for racing cars was launched. These were based on production sedans, which were extensively reworked to make them competitive for circuit racing. The cars were fitted with full rollcages, state-of-the-art suspension and brakes, and powerful but reliable engines. That was the beginning of the Trans-Am series, which continues to this day.
Casey Holm, of Holm Built Hot Rods in Northern California, has always been fascinated by the purpose-built design used in this class of racing. Shawn Arnold, a longtime friend and customer of Holm, wanted to build a new, truck-based project that was aligned with the Trans-Am theme. Arnold found a Boss 302 engine at TOE Racing Engines and had them build a street-friendly engine in the Trans-Am style using a number of rare, period-correct components. The plan for the build was to keep the same attention to detail and focus on the performance that was used in the Trans-Am series.
It took an extensive search to find a good truck to start with. Most 50-year-old commercial vehicles get pretty battered, and rust often takes a toll on metal that old. The search finally paid off and they found a solid candidate with minimal rust and only minor body damage. After disassembly, all the body panels were stripped by media blasting.
The plan included a new chassis that incorporated a high-performance drivetrain. A top priority was replacing the old twin I-beam front suspension with a race-tuned double-wishbone design. Penske Racing coilover shocks will be used front and rear, along with beefy antiroll bars.
There were a lot of factors to consider when designing the new chassis, such as tweaking the wheelbase, establishing the proper ride height, building in robust torsional stiffness, and allowing adequate room for wide tires and a large, free-flowing exhaust system that will exit through the bedsides. They started by purchasing a front suspension clip from RPM Classics in Ontario, Canada—designed for racing but robust enough for street use.
With the front clip as a starting point, the chassis was mocked up with the era-correct wheels and tires, 600-15s in front and 800-15s in the rear. TBM Brakes were selected and special brackets were needed to fit them inside the 15-inch wheels in the Trans-Am style.
It quickly became apparent that the wheel openings in the front fenders were too large, so Holm moved the front fenders and cab reward 1-1/2 inches and moved the rear portion of the front fender forward 2-1/2 inches. This gave the perfect look at the front of the truck, and the bed was next. The bed was moved forward a 1/2 inch to reduce the gap at the cab. The bottom rear portion of the bed was moved forward 2-1/2 inches and the rear of the bed was shortened 1 inch. The rear axle was positioned so the wheels were centered in the openings, which resulted in the wheelbase being shortened 2 inches. The ride height was established so the wheels were shrouded just the right amount, and the width of the rear axle was calculated to give the tires adequate clearance with the bed. These subtle changes were essential to give the truck the purpose-built look of the Trans-Am cars of the era.
The engine was moved back as much as possible, which required extensive modifications to the firewall and transmission cover. This work was beautifully executed to have an OEM look—no hack and patch job here.
As with any major project like this, the devil is in the details, and the photos give you a taste of some of the intense work that has been lavished on the truck so far. This will truly be a one-of-a-kind project when it’s finished!
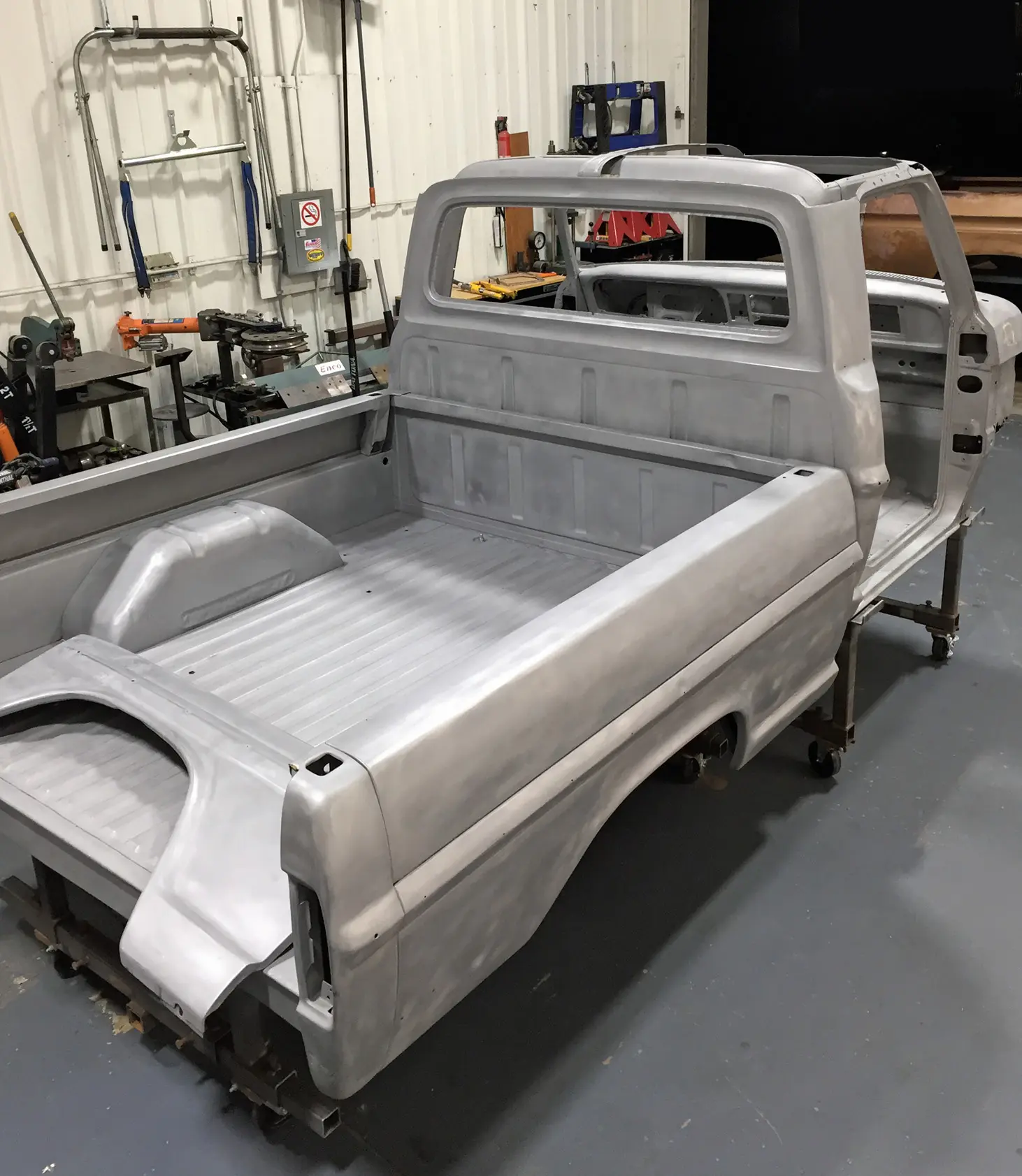
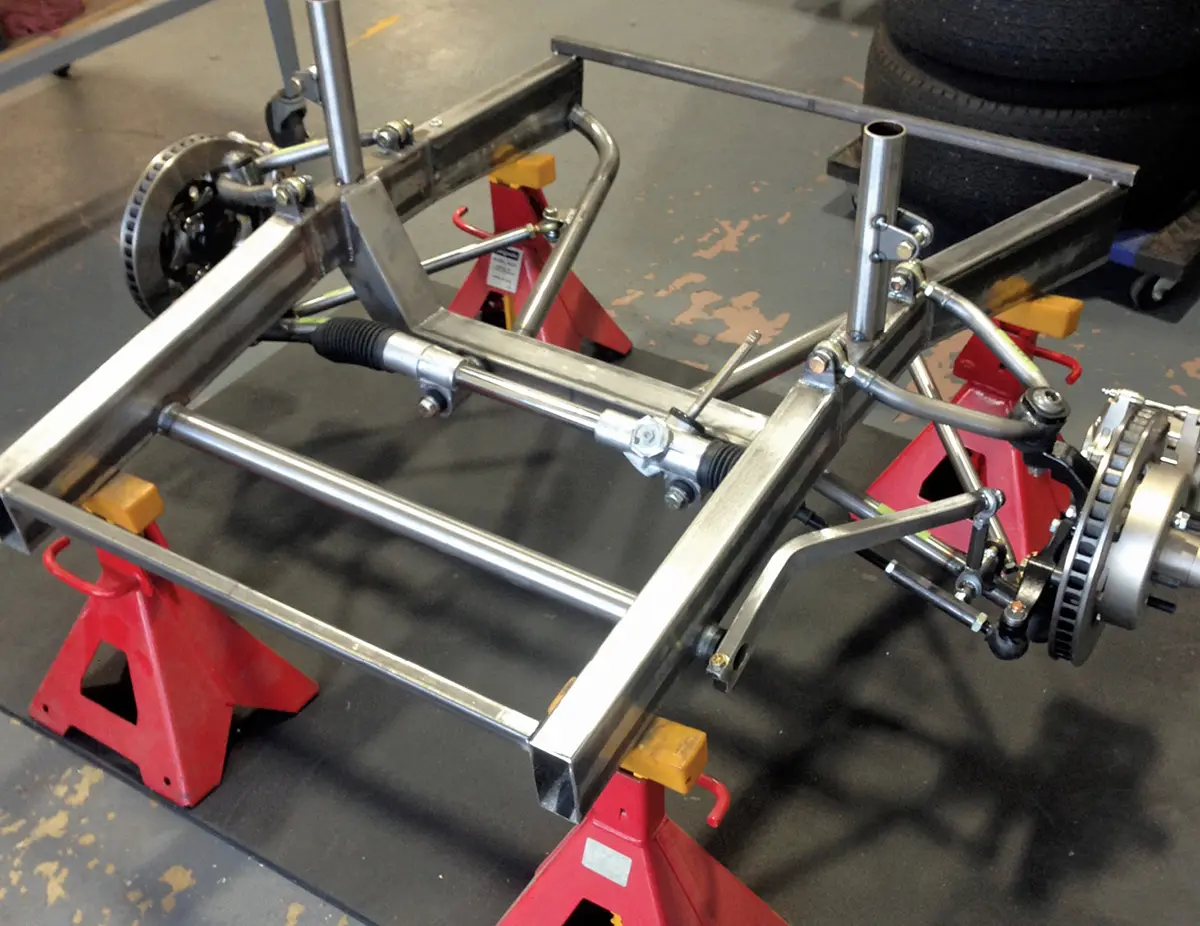
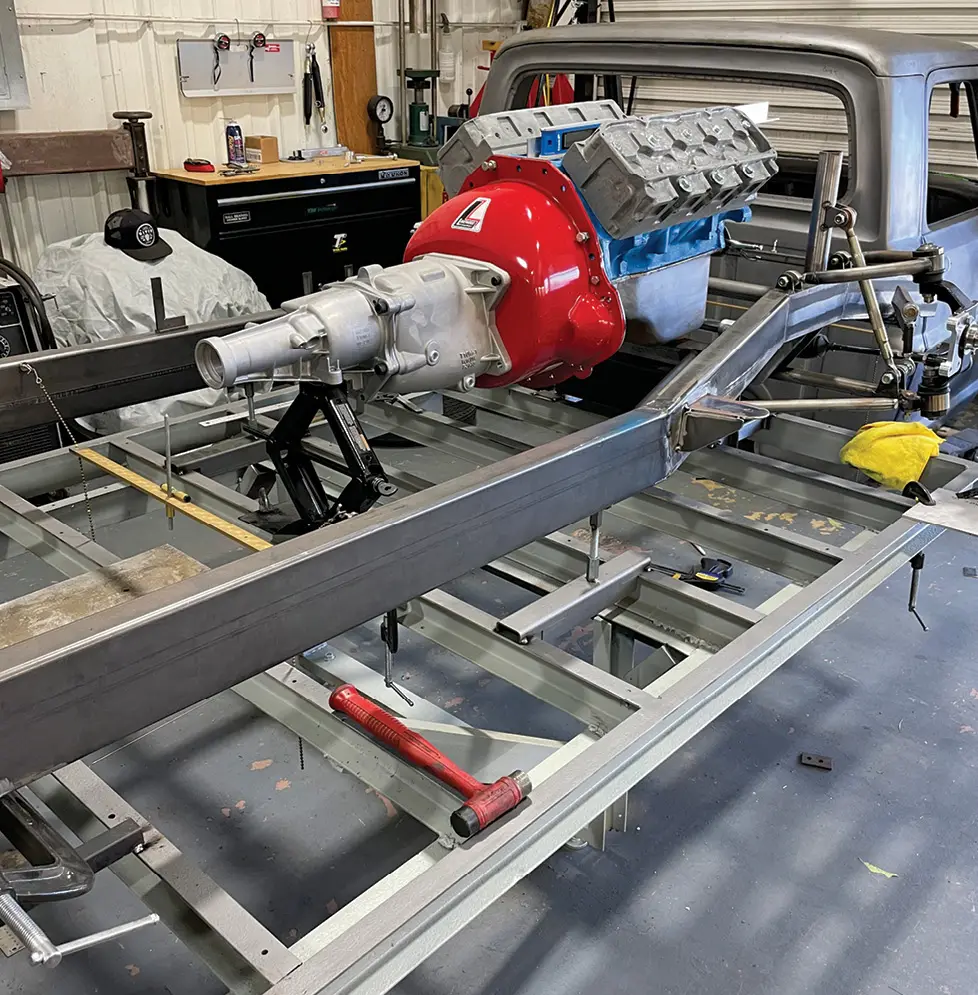
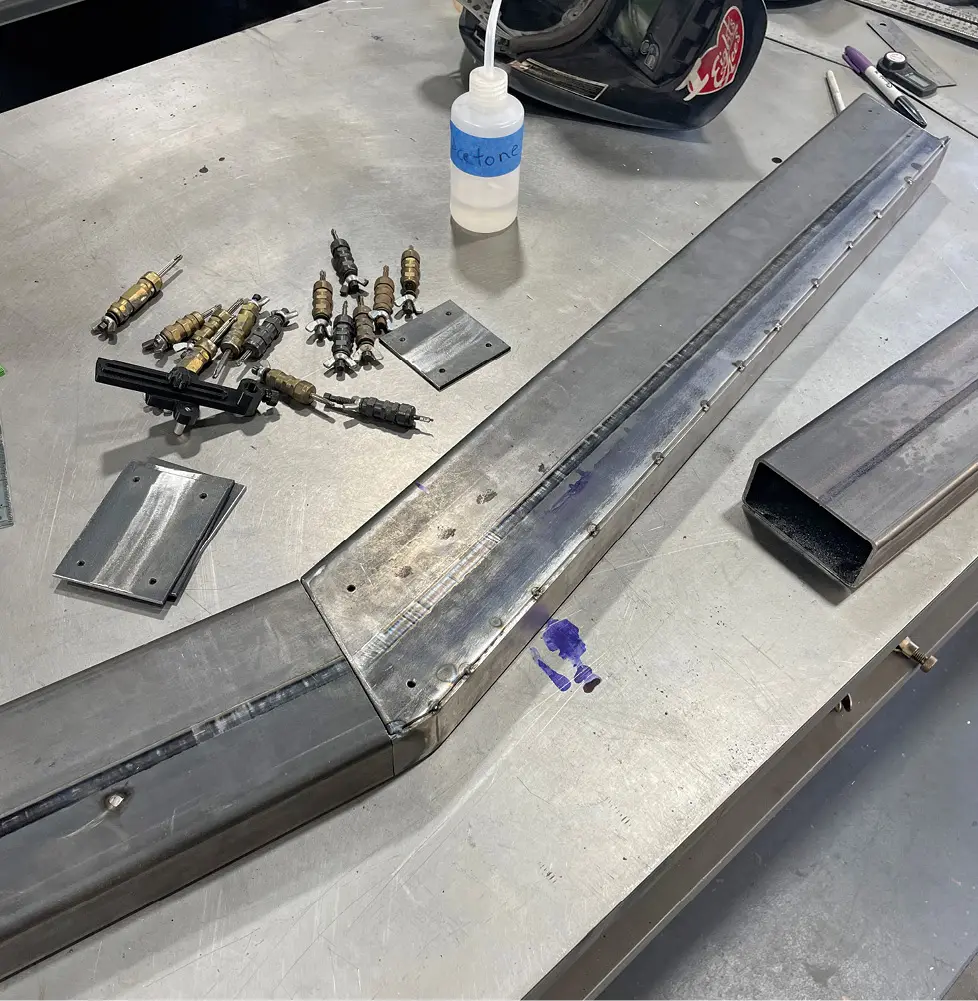
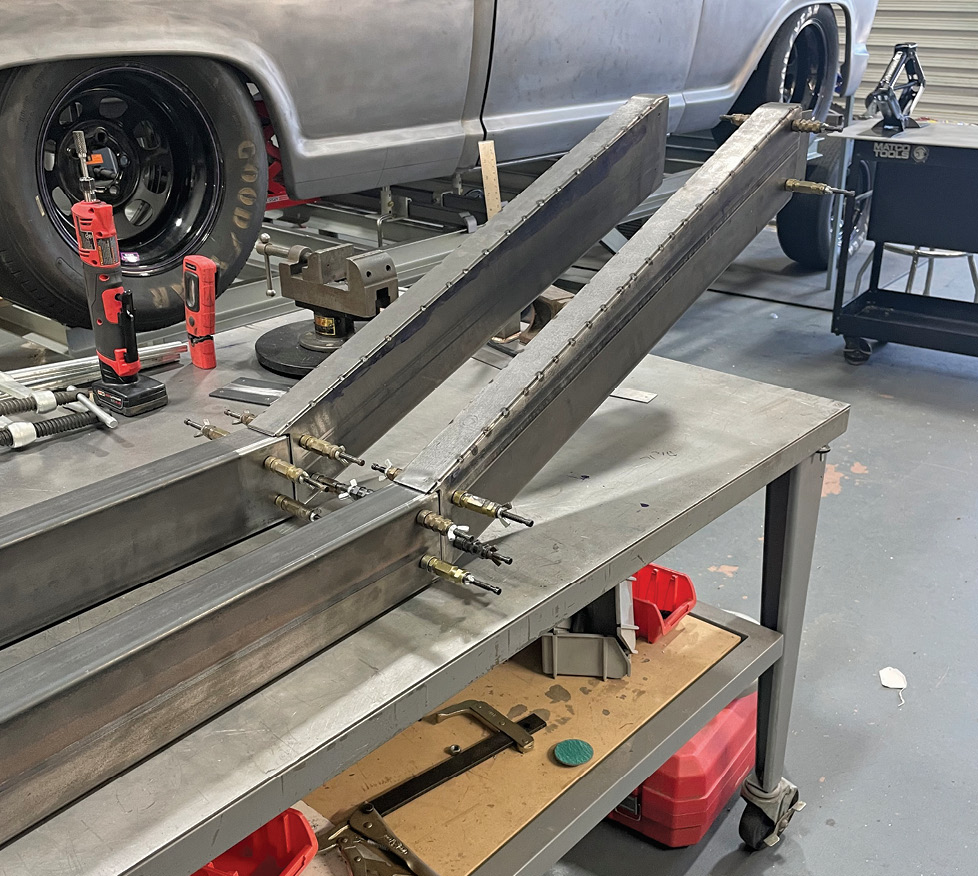
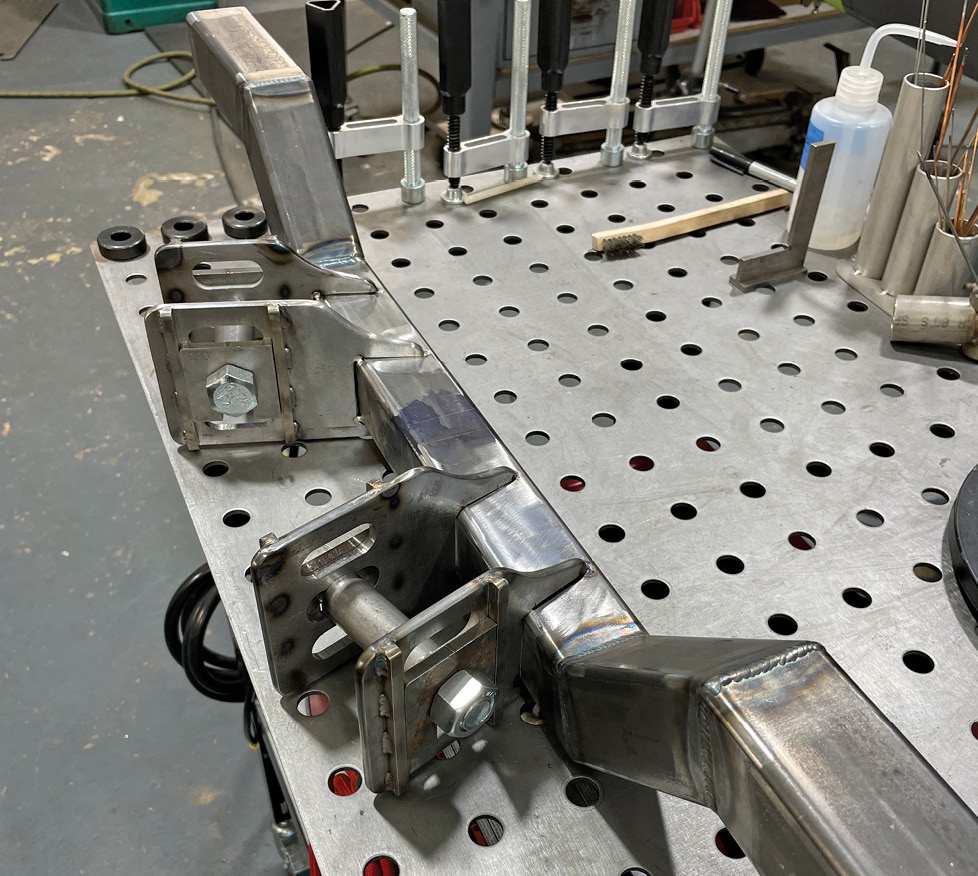
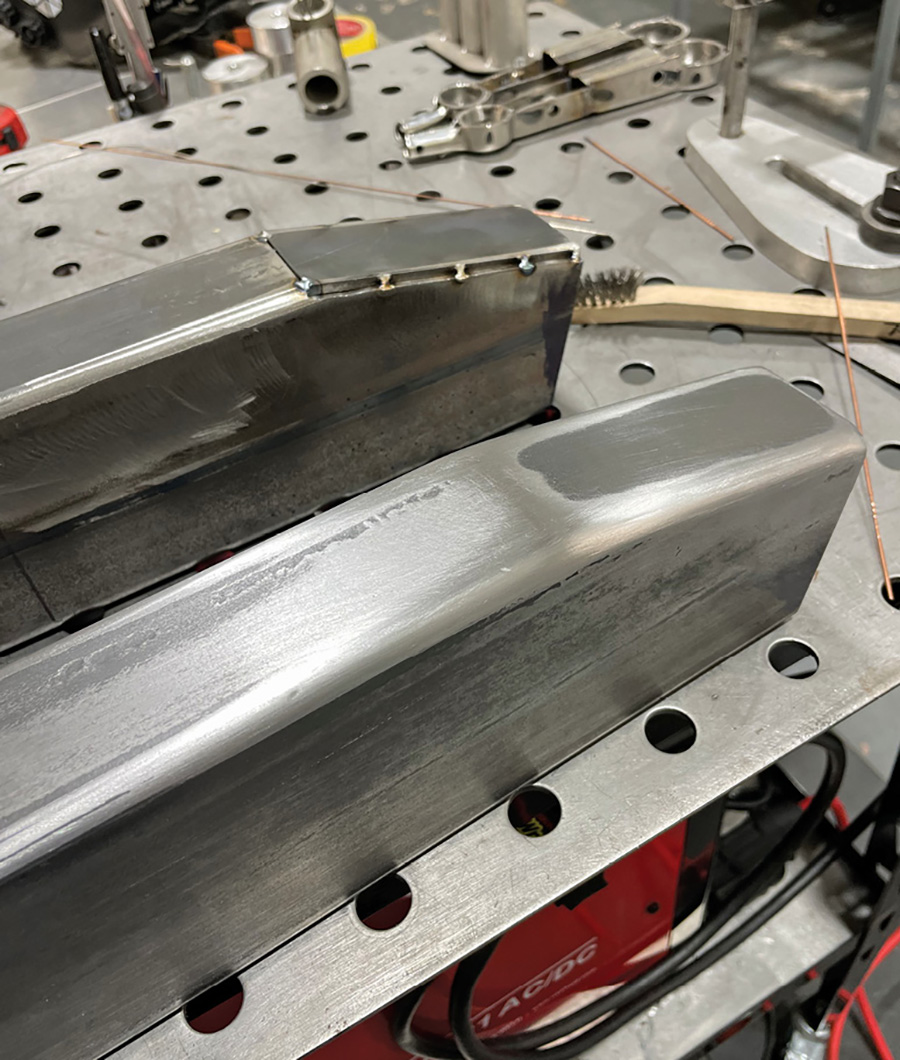
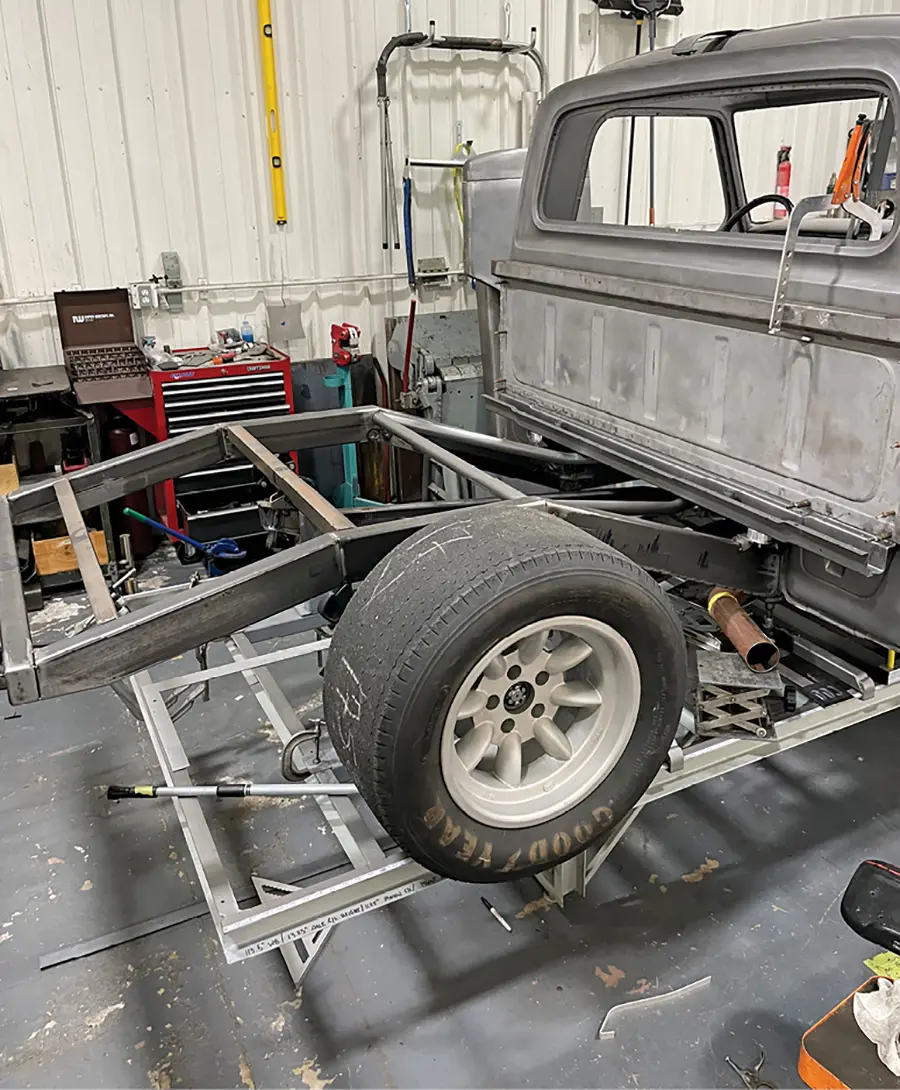
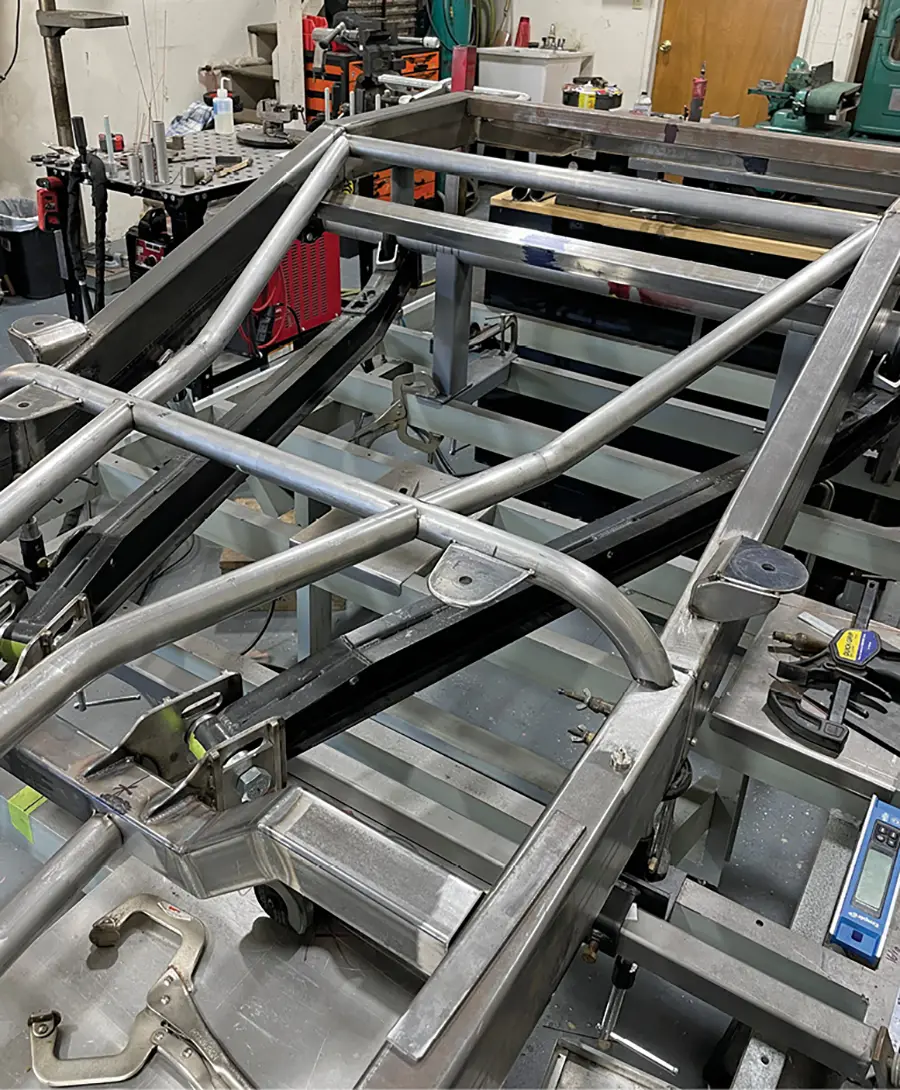
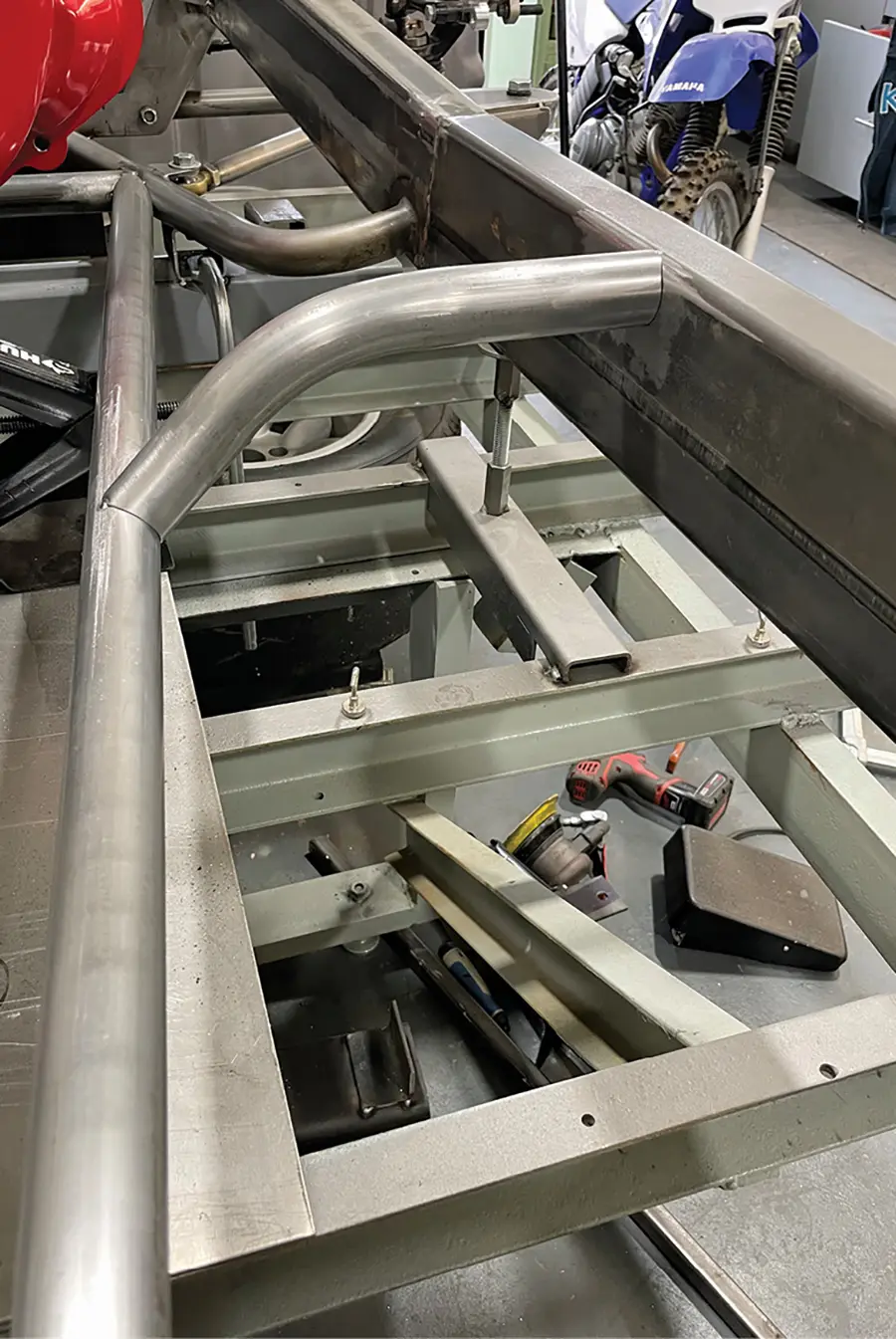
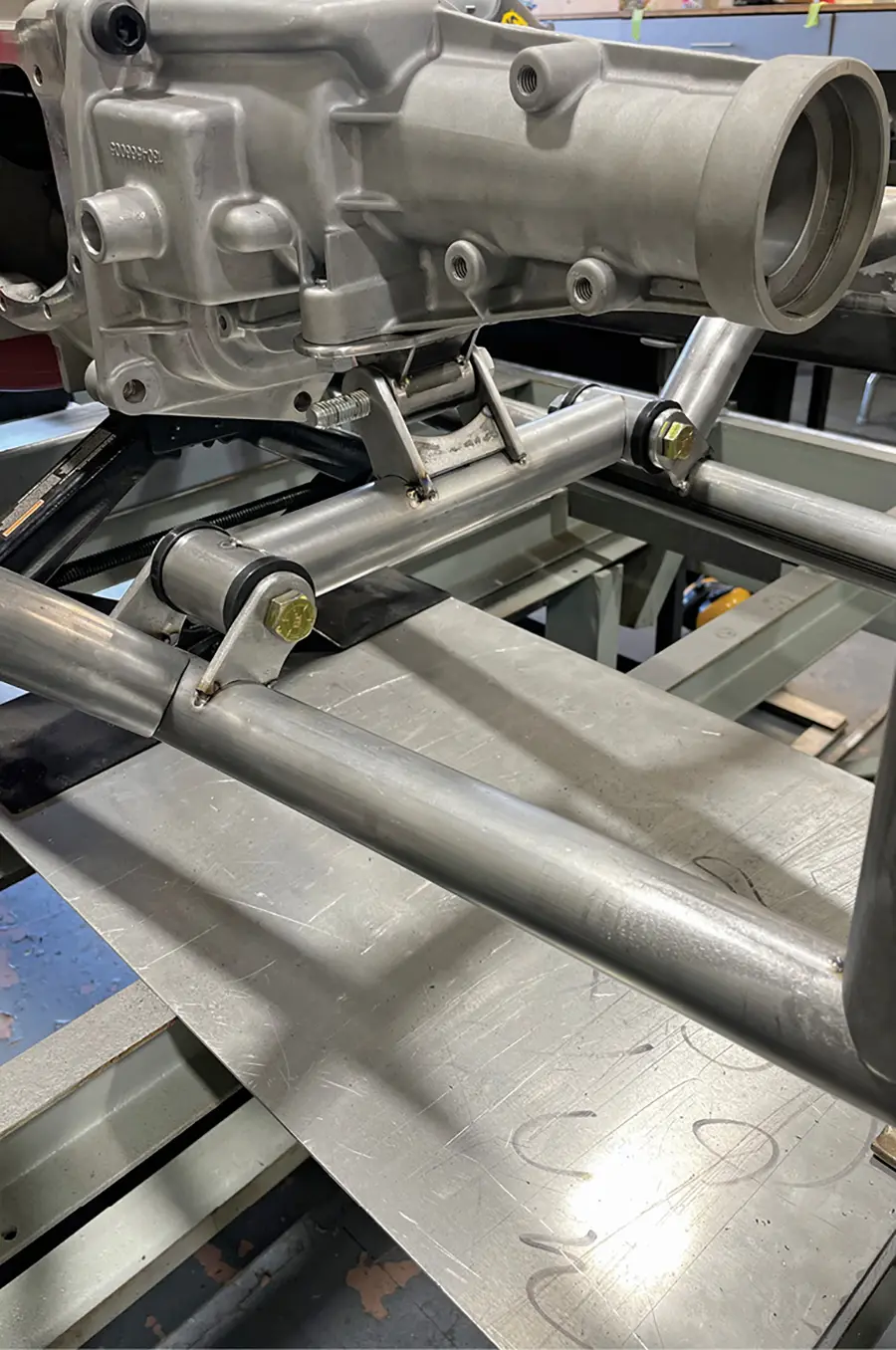
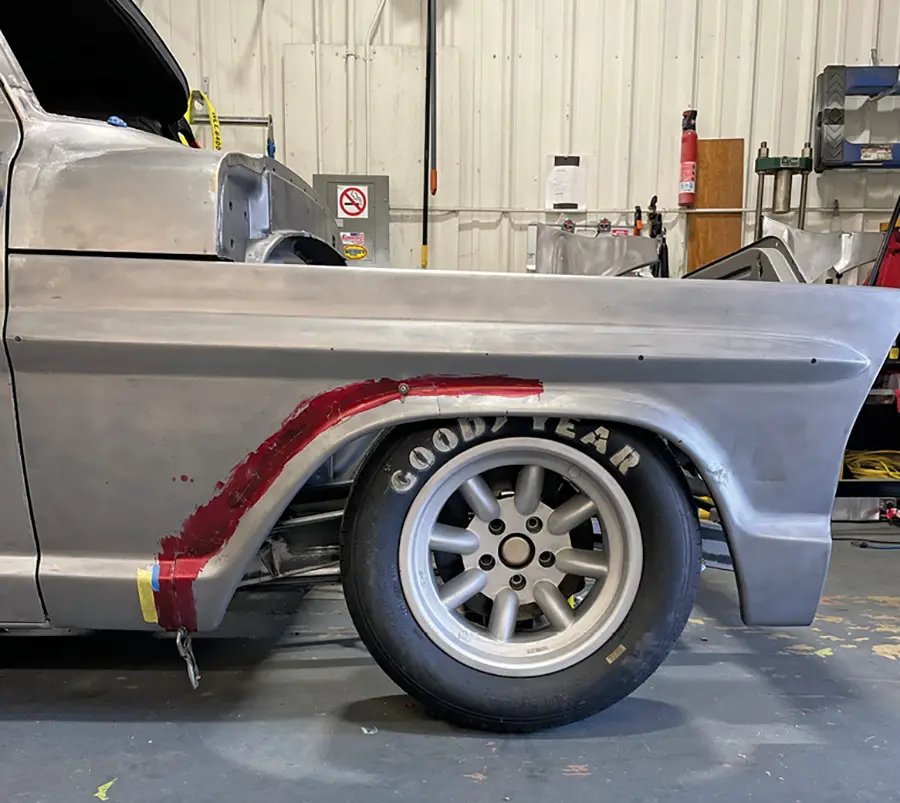
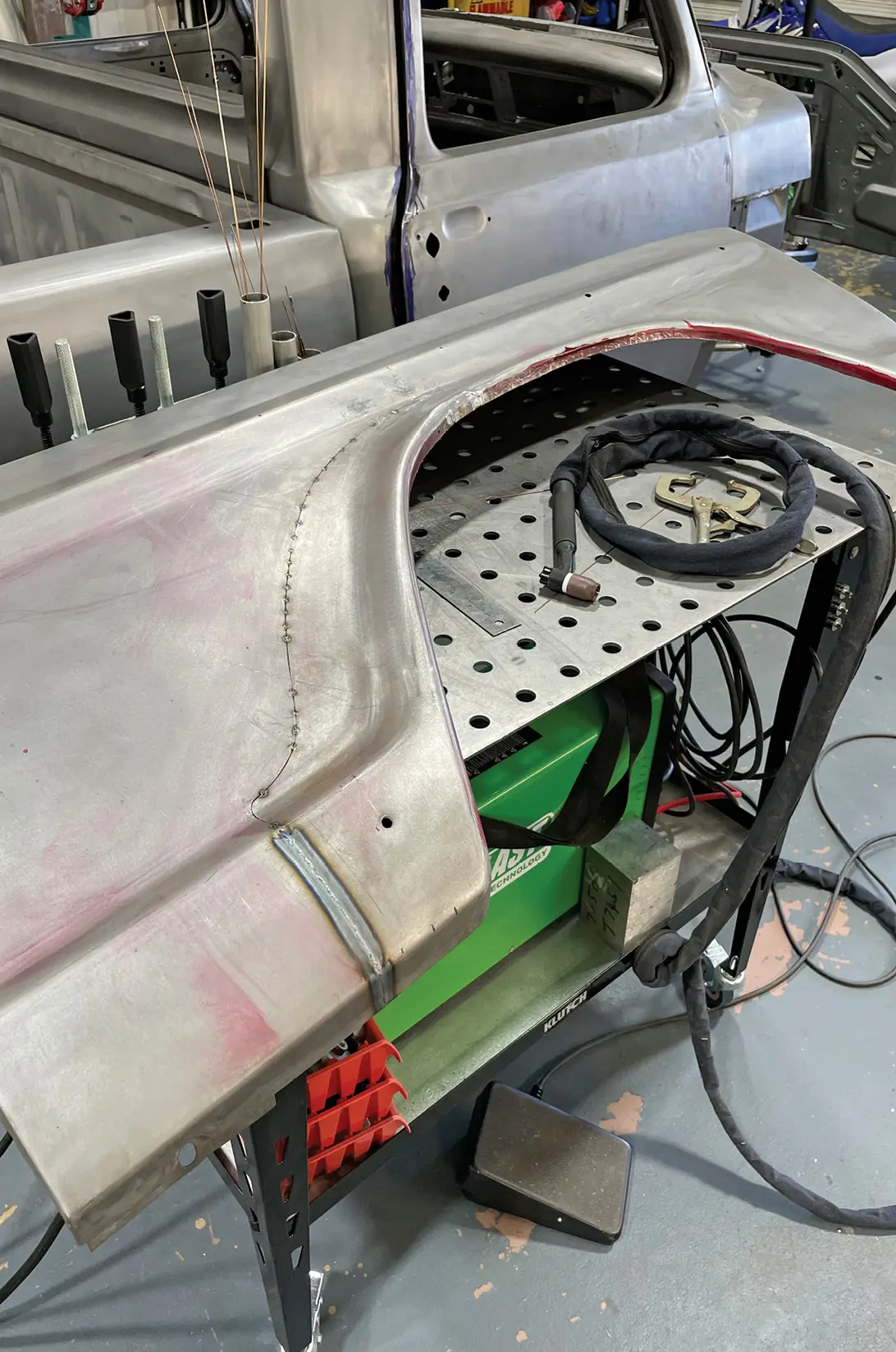
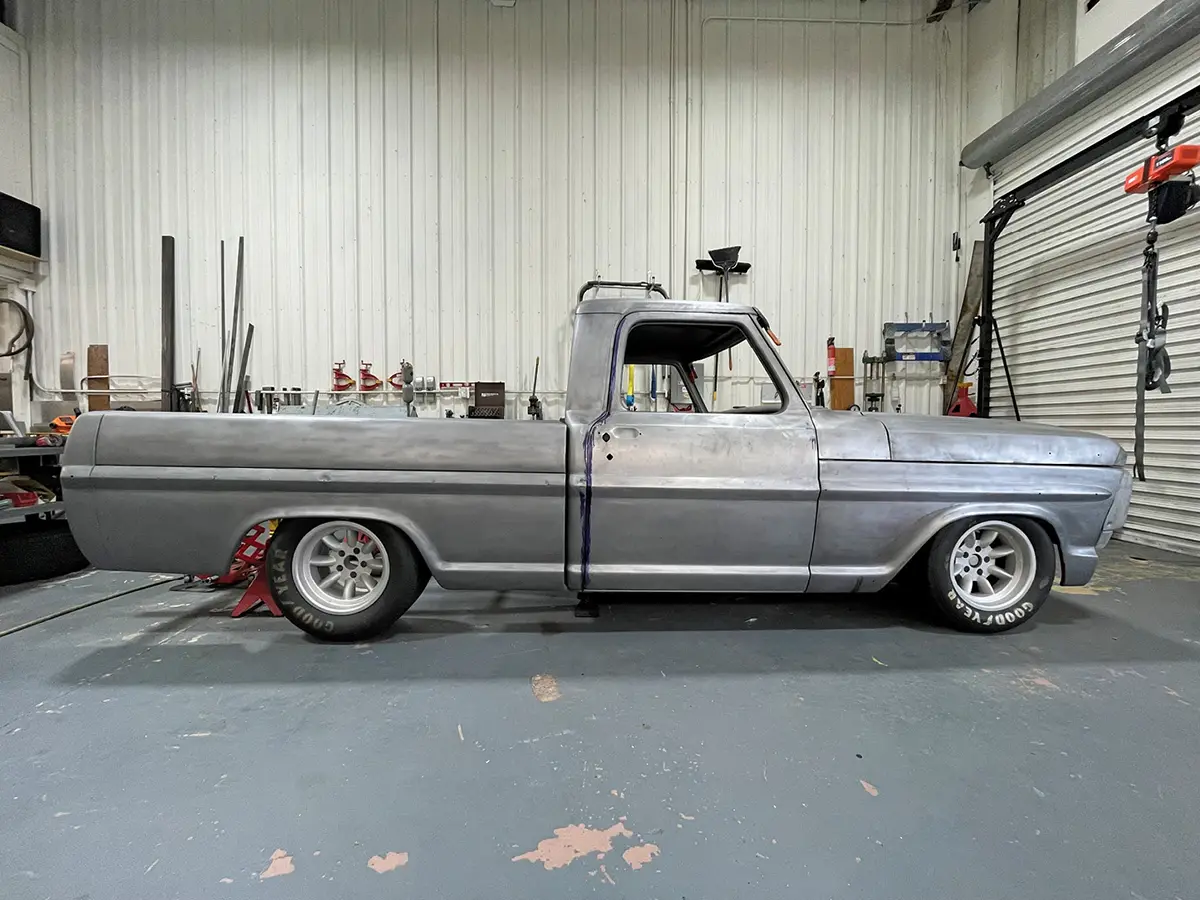
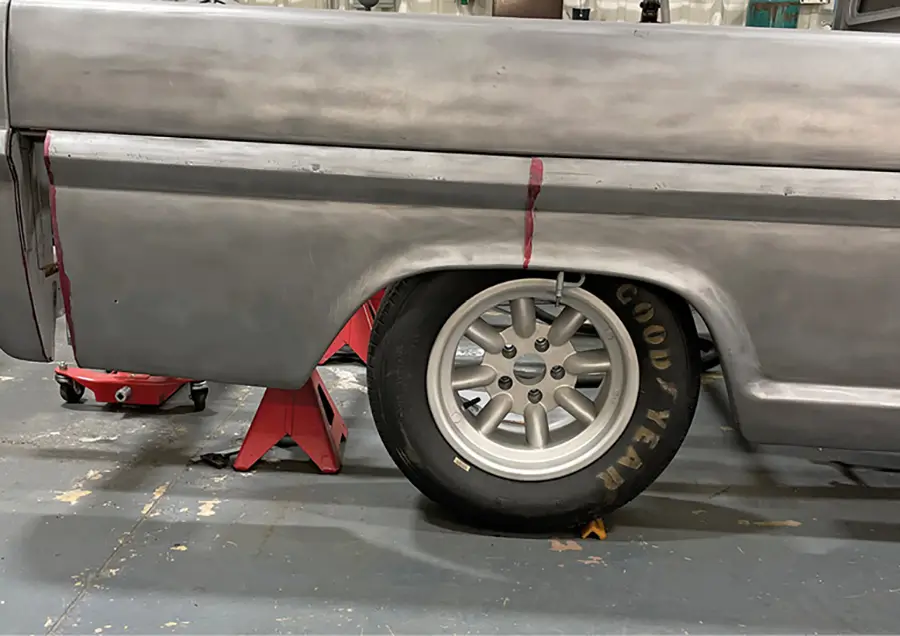
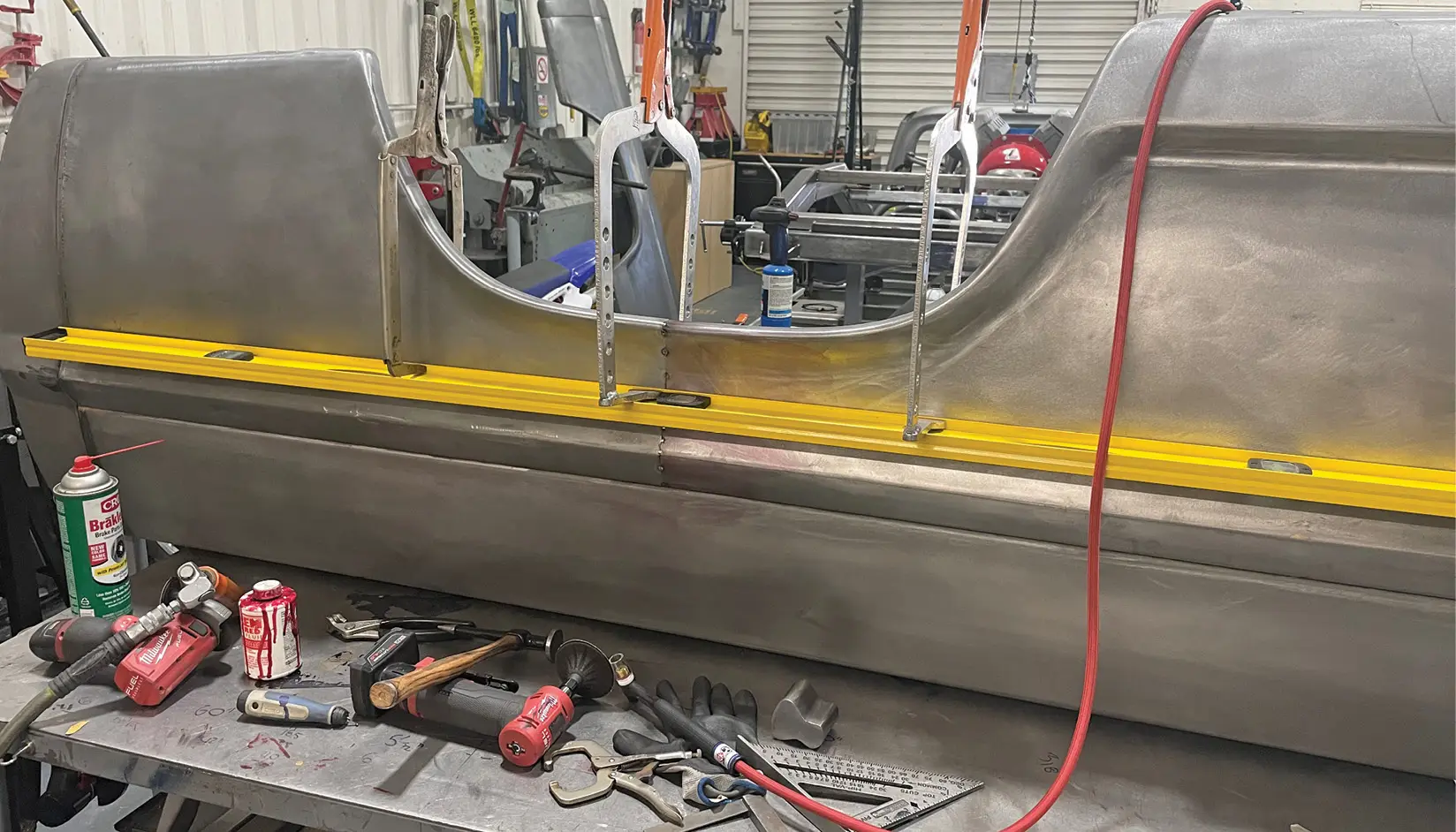
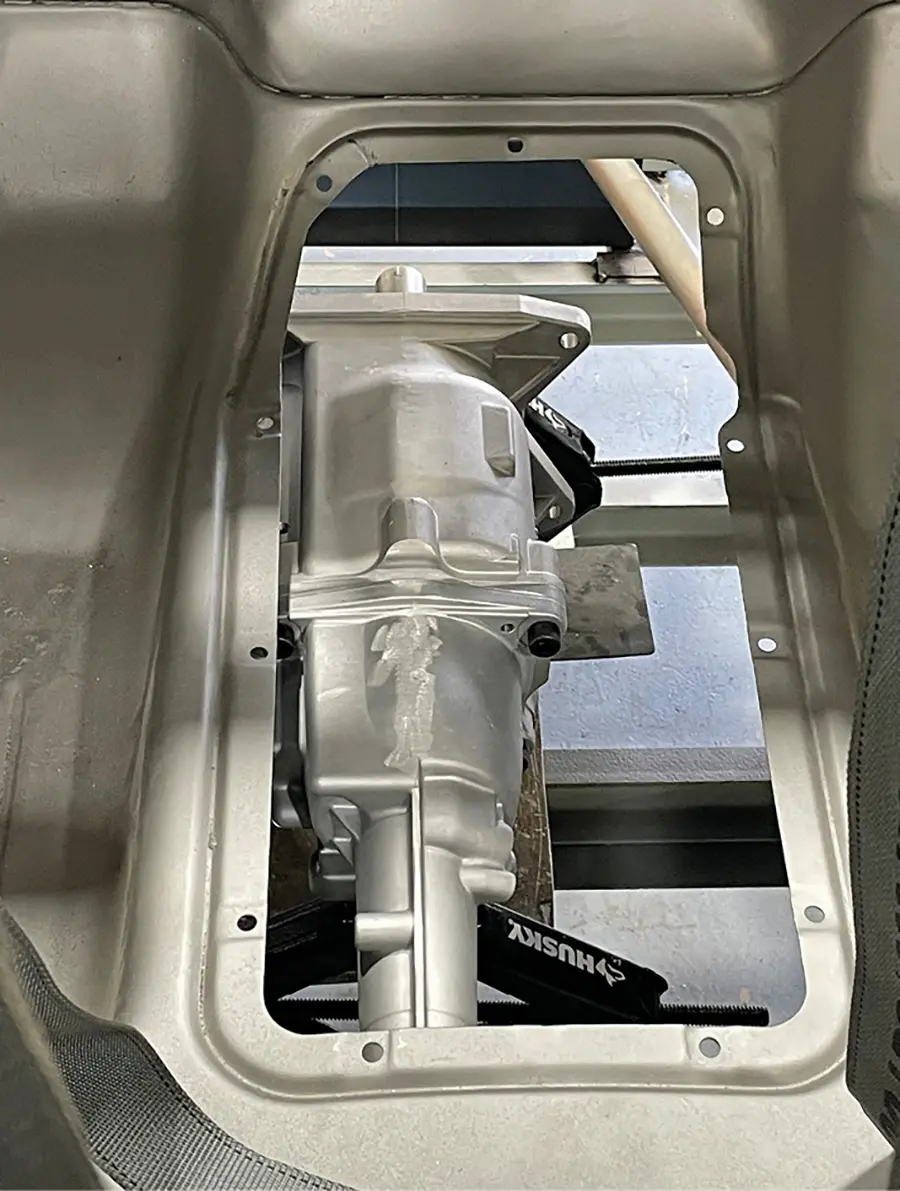
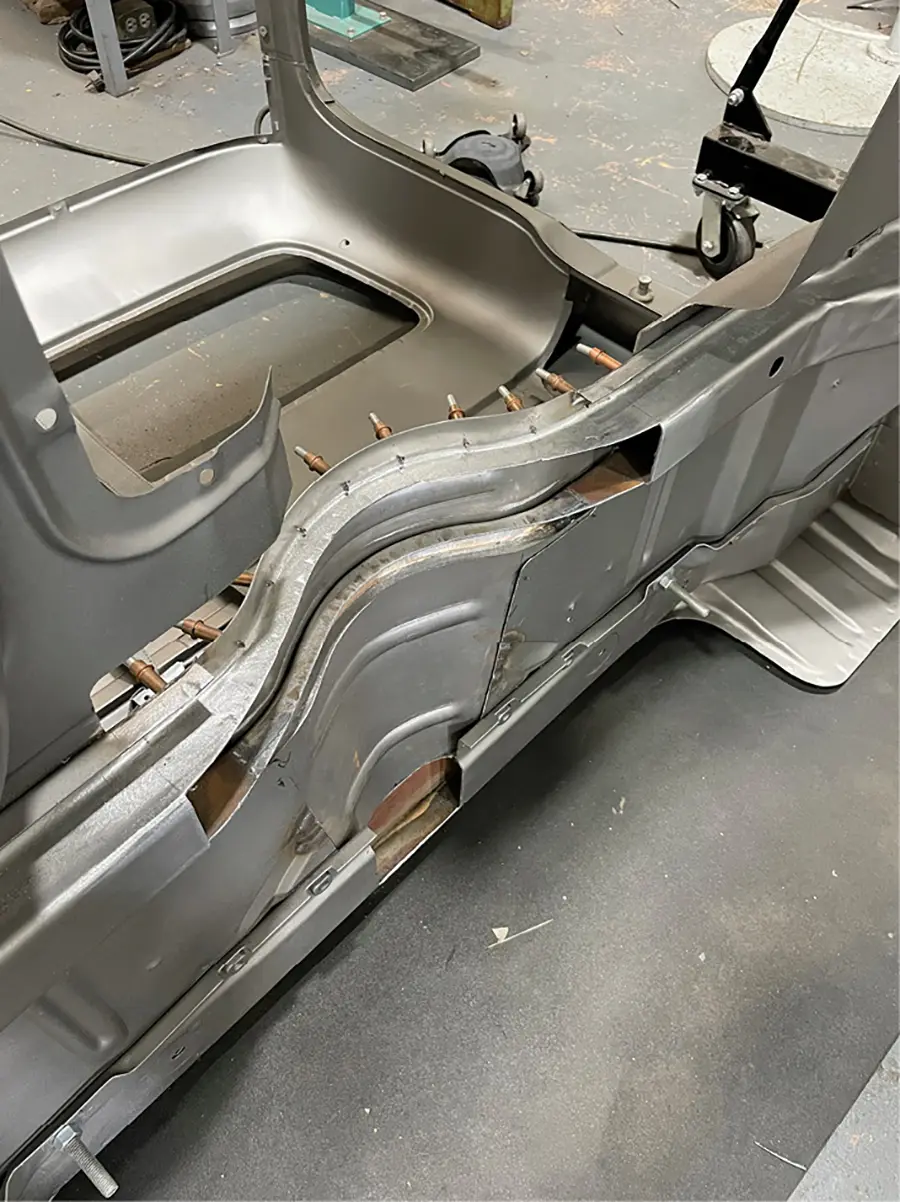
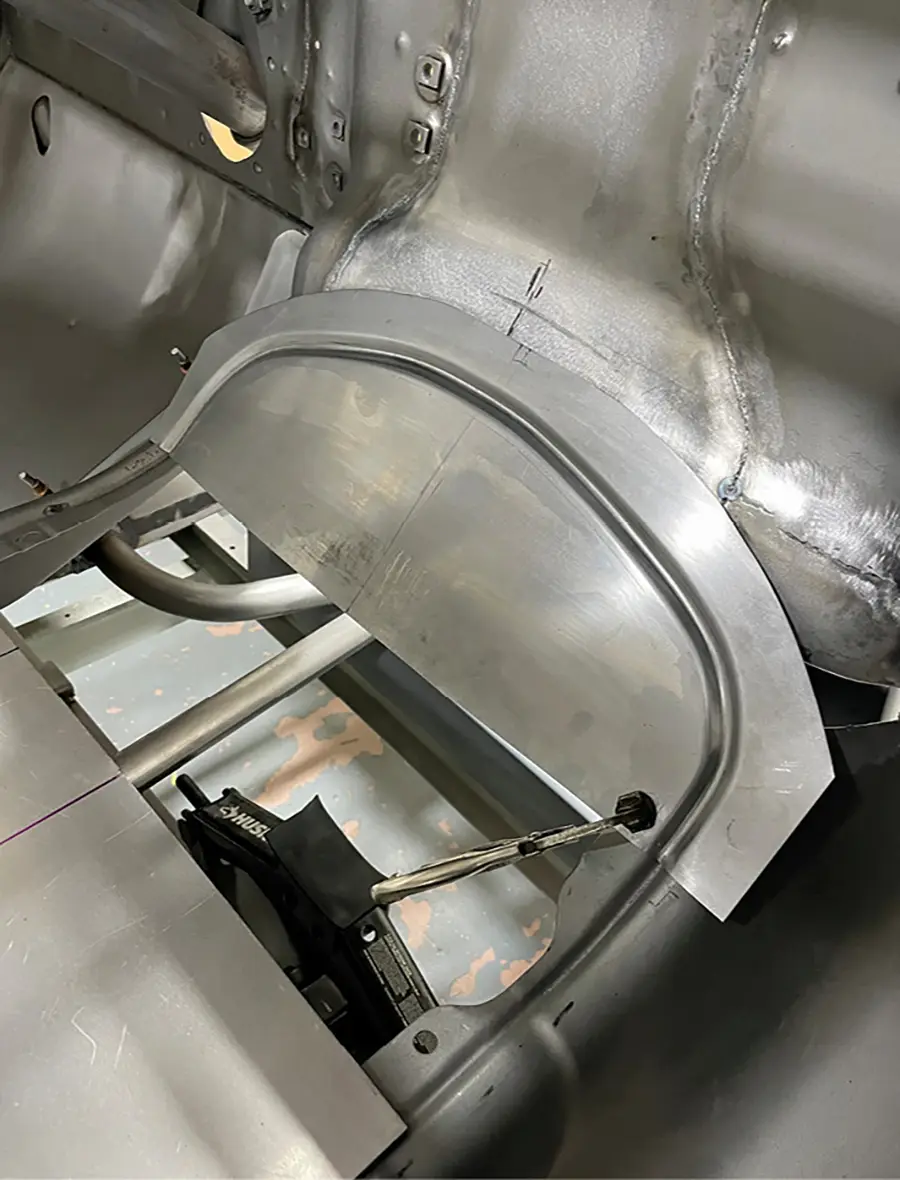
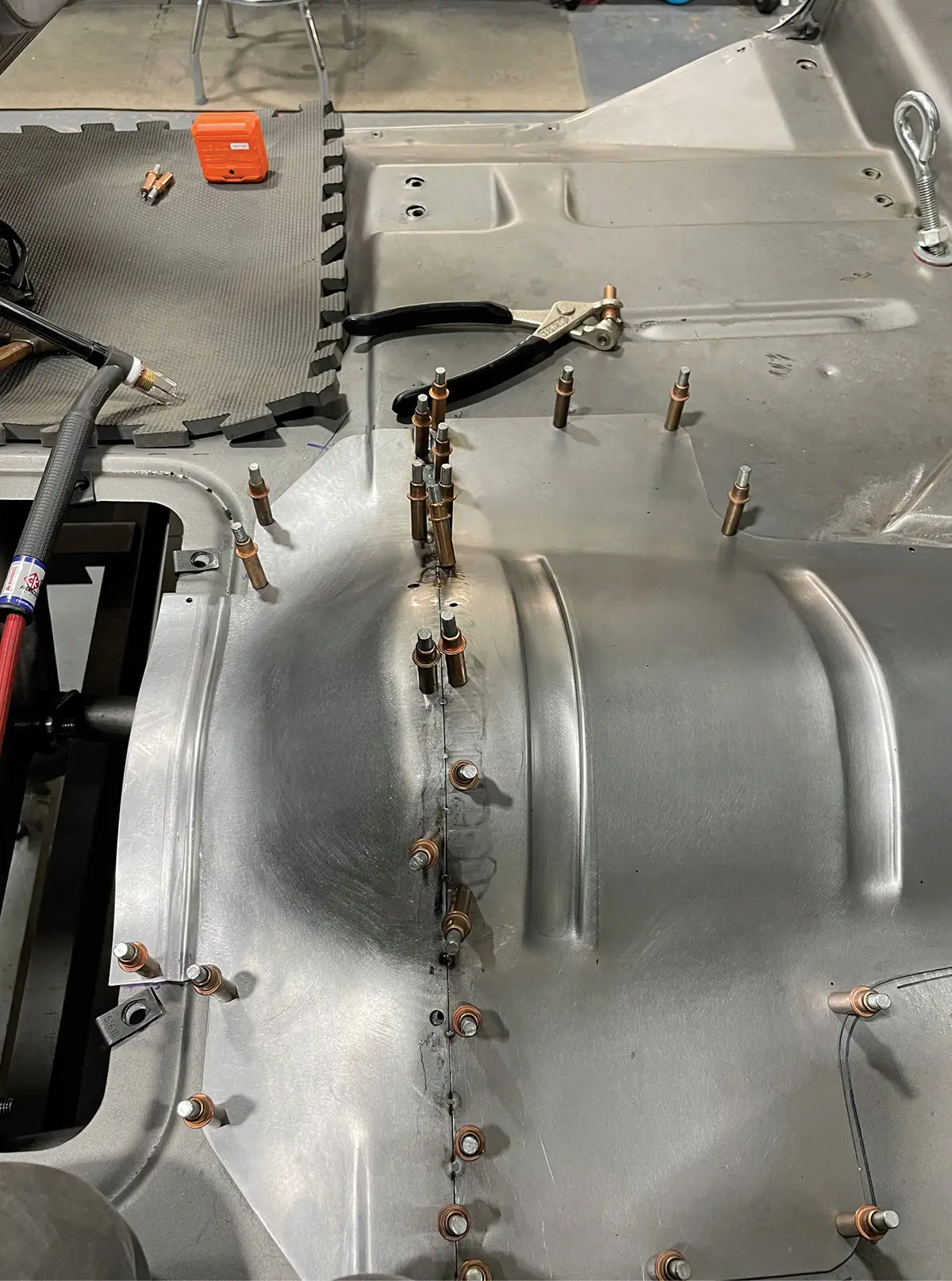
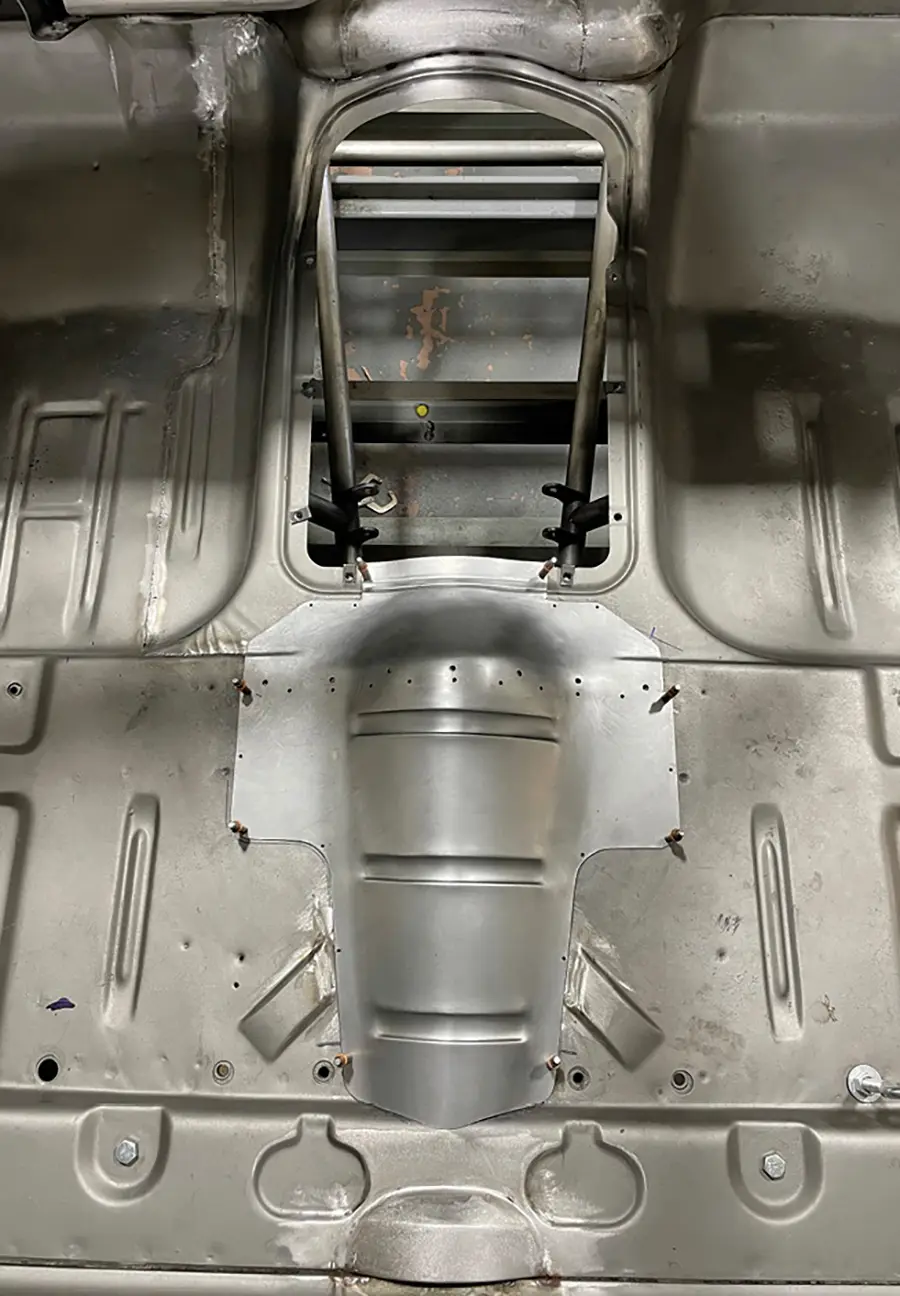
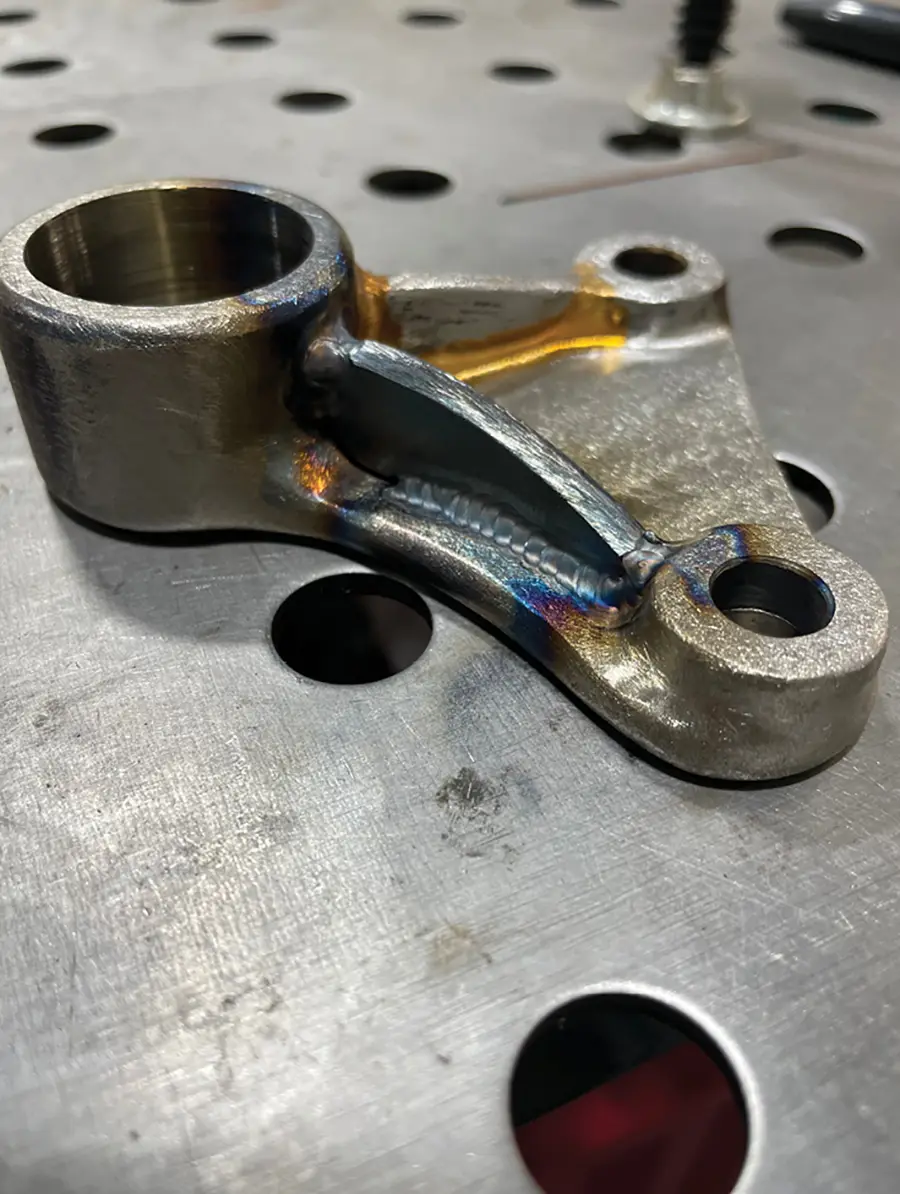
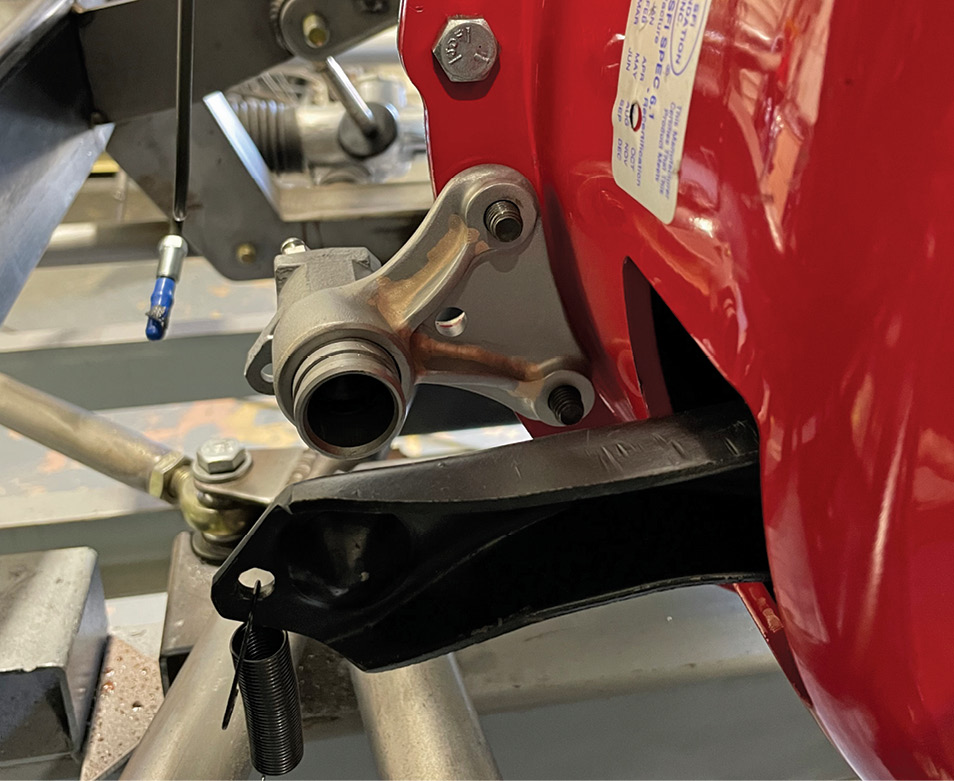
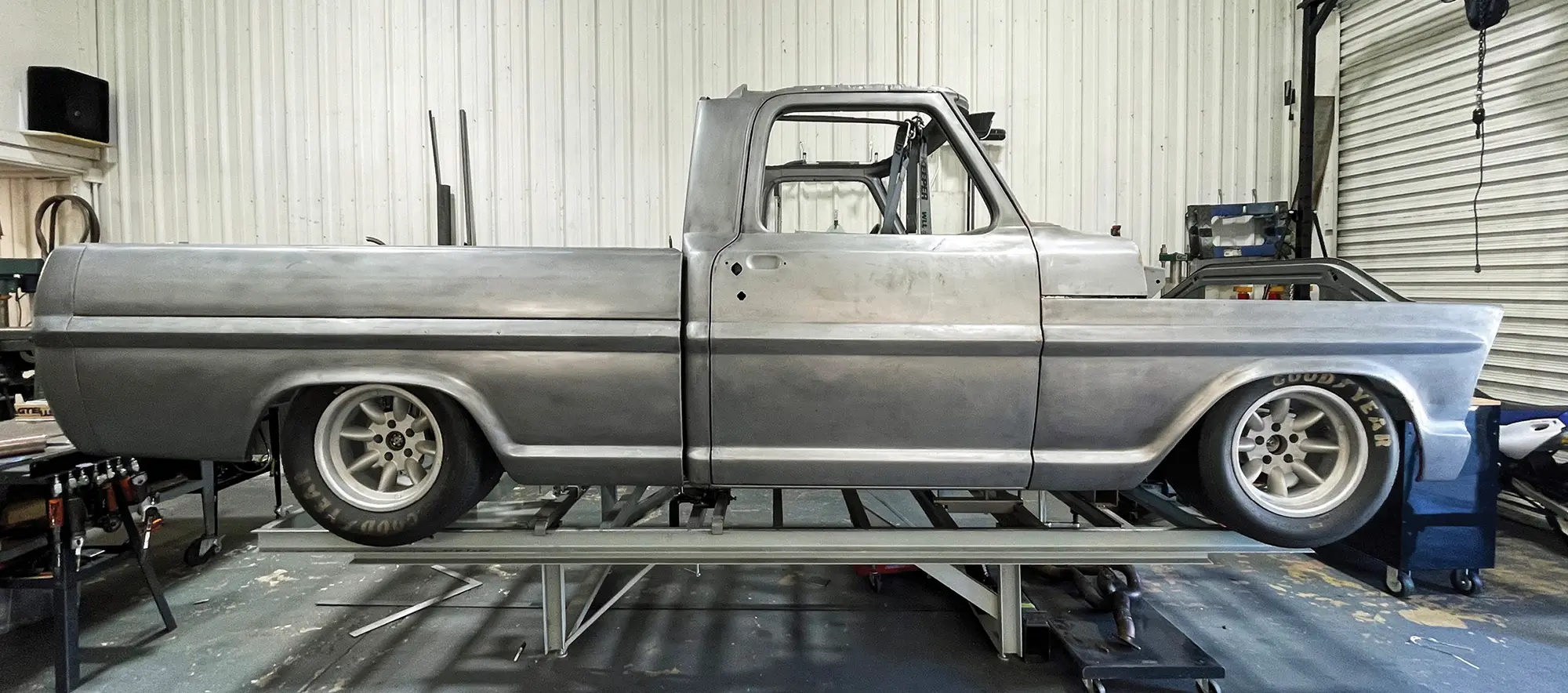
