Tech
InTheGarageMedia.com
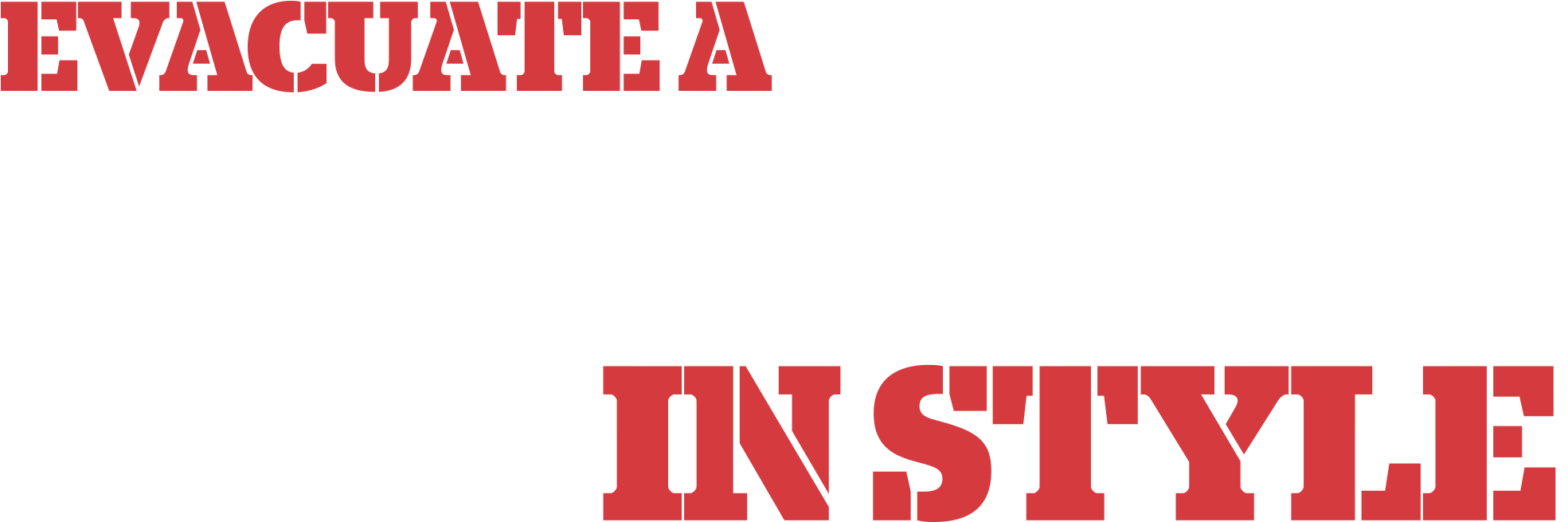

he use of stainless steel components on high-end truck builds covers a myriad of parts, from suspension components to fasteners. Its aversion to rust and corrosion makes it a perfect material for such use. Stainless steel is one of the only materials that can be polished to perfection or left in a raw state with little change in appearance over time. What makes this possible is the addition of at least 10.5 percent Chromium in the base metal that, when combined with oxygen, forms a thin, transparent boundary layer of chromium oxide, effectively protecting the material. Both stable and self-renewing, this layer or film makes the corrosion resistance a permanent feature. In addition to its attractive appearance, stainless steel also tends to retain its mechanical characteristics at high temperatures. This makes the material a great candidate for use in an exhaust system.
Editor Fortier’s own C10 project is nearing completion and when it came time to fabricate the exhaust system, there was no question as to what material would be used. Yet while stainless was the hands-down option, traditional round tubing wasn’t going to cut it. The big-block Chevy installed underhood necessitated a well-breathing exhaust system, preferably with a large, 3-inch diameter. But with the C10’s altered height (low!), Rob had legitimate concerns when it came to dragging the exhaust across every speed bump and manhole cover across town.
To thwart this issue, and to allow Eddie Legliu of All American Metal Shaping and myself (Ryan Manson of Clampdown Competition) craft an exhaust system that tucked up nicely into the Chevy’s chassis, Rob elected to use stainless steel exhaust components from Granatelli Motor Sports. Measuring 2.40×3.45 inches, their 3-inch stainless oval tubing is the perfect solution for those low trucks that want to run a true, 3-inch ID exhaust system with increased ground clearance. Available in straight sections as well as both vertical and horizontal, 45- and 90-degree mandrel bends with a 4.50-inch bend radius, mufflers, and an assortment of various adapters, a laundry list of needed components was put together and sent over to the folks at Granatelli Motor Sports.
Fabricating a stainless steel exhaust system does take a fair bit of skill (TIG welding is a plus), but it isn’t beyond the scope of the homebuilder. A handful of various tools is necessary, but nothing one might consider exotic. A lift is definitely helpful, but the same results can be achieved fabricating a system on an assembled bare chassis.
While crafting the exhaust on Rob’s C10, we decided to pick out a couple tips and tricks for working with stainless tubing in the hopes that it might help out those hobbyists trying to improve their fabrication game!
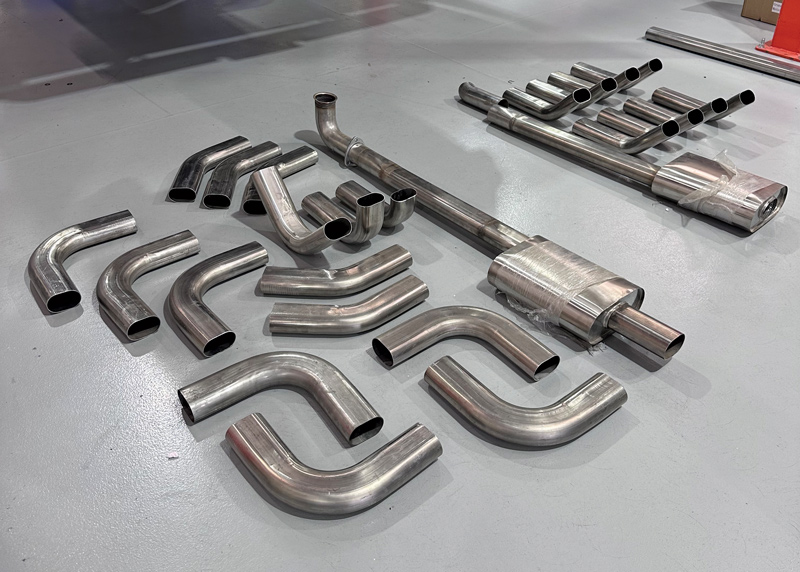
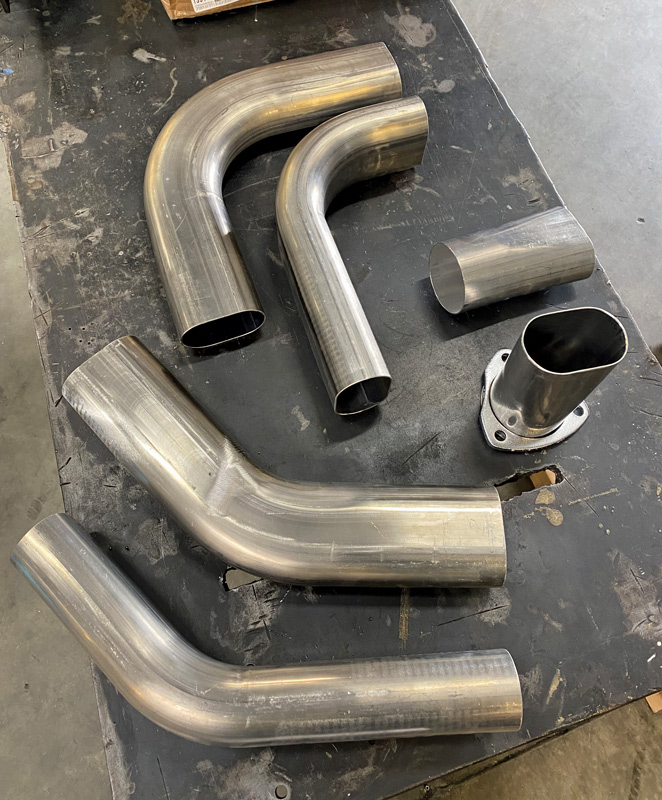
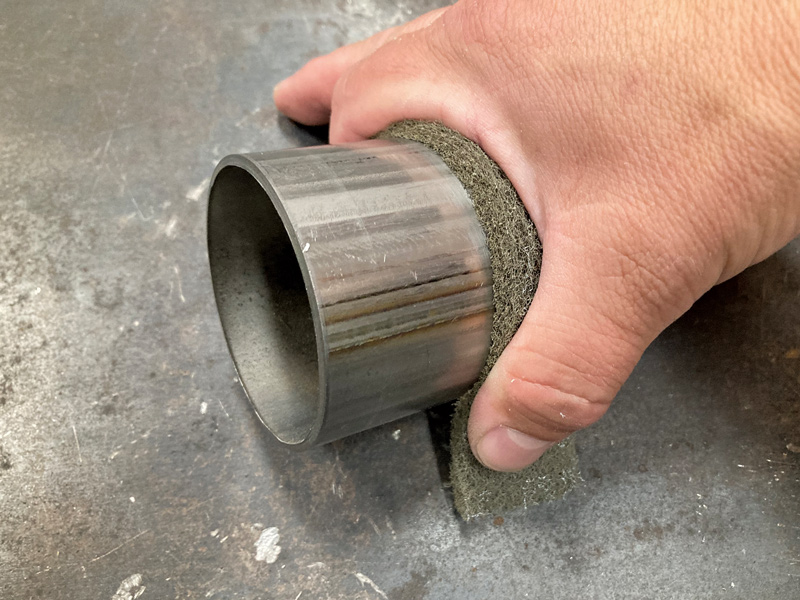
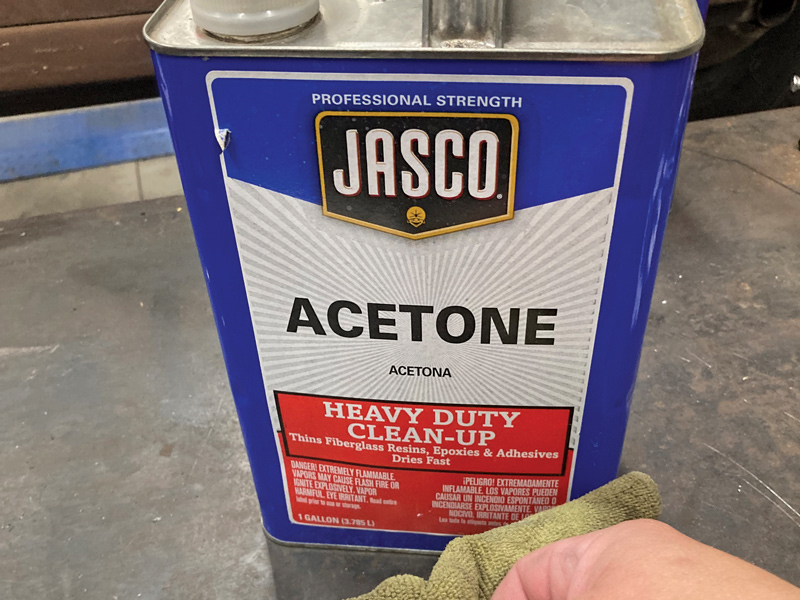
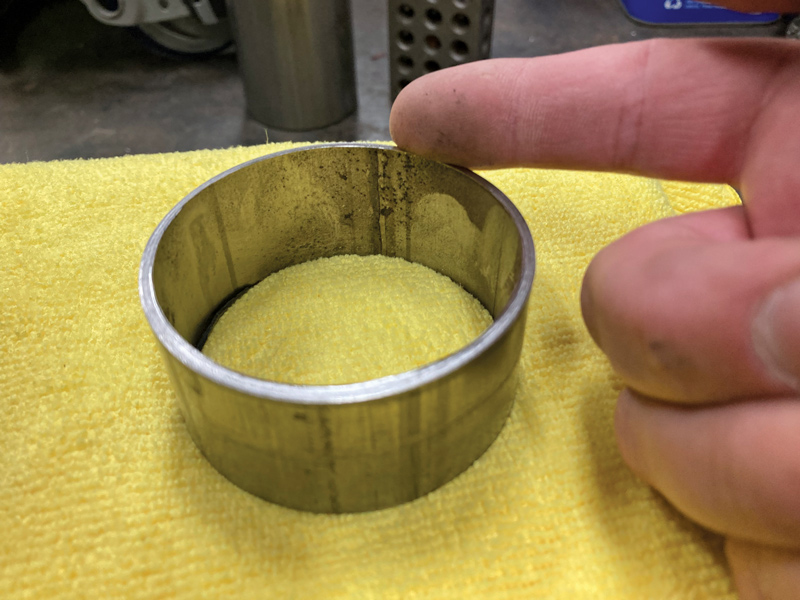
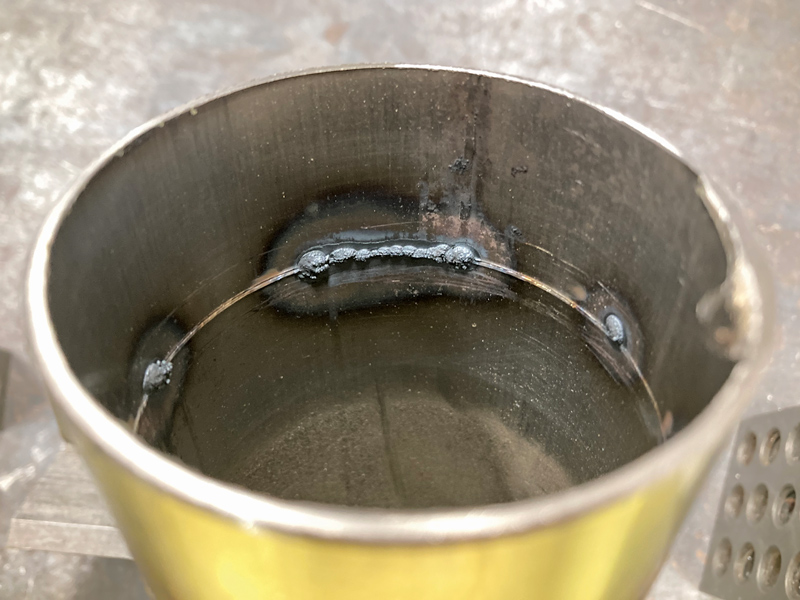
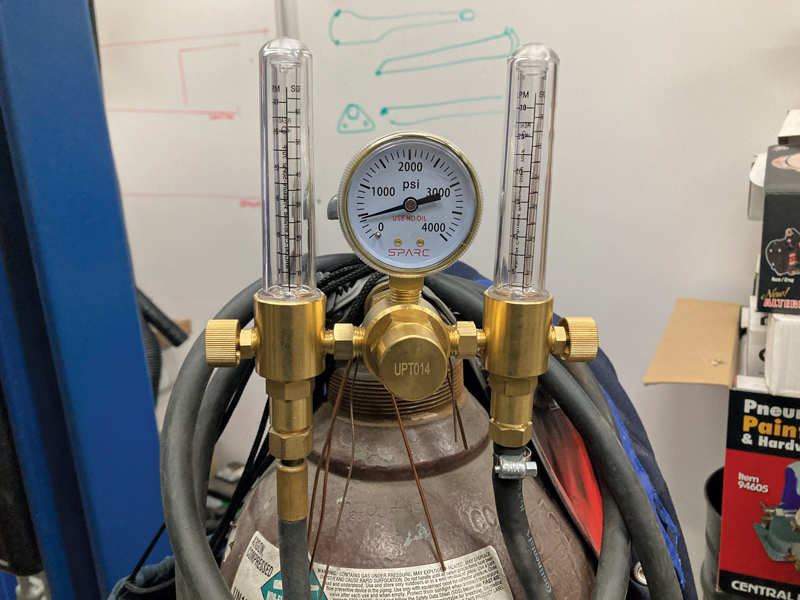
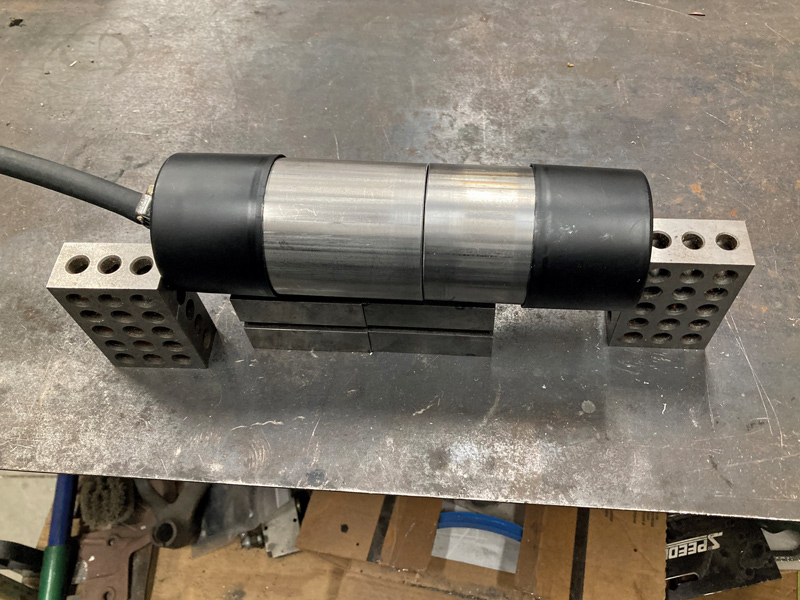
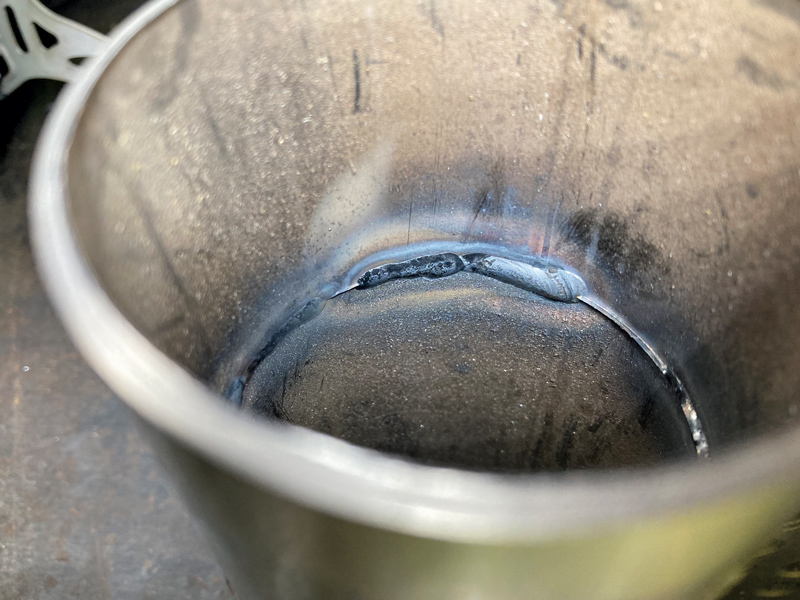
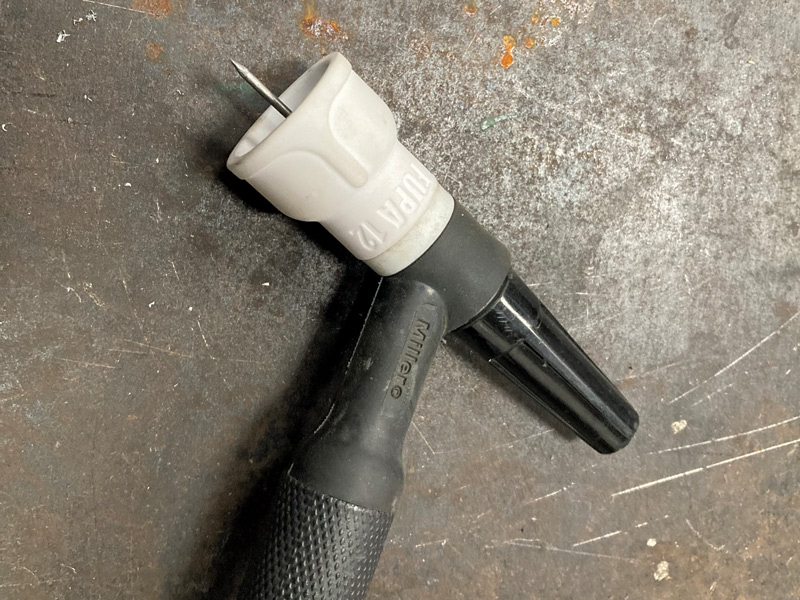
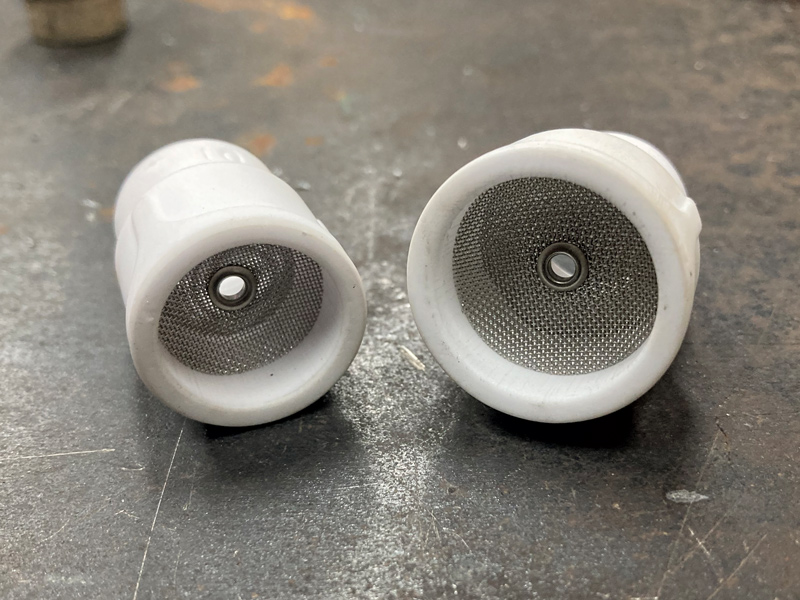
10-11. Stainless steel likes a fair amount of gas coverage and these massive #10 and #12 cups, combined with a gas lens diffuser, not only provide great gas coverage of the welded area, they also allow for some pretty massive tungsten stick out as well.
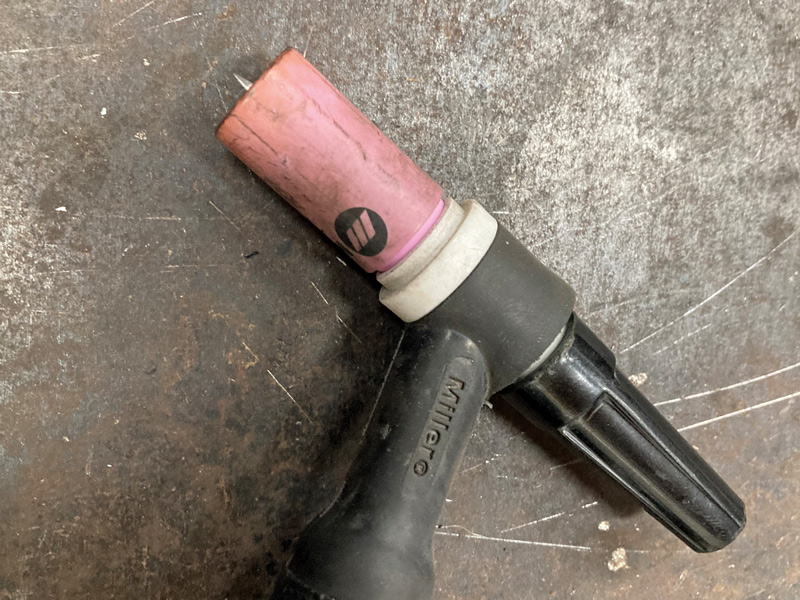
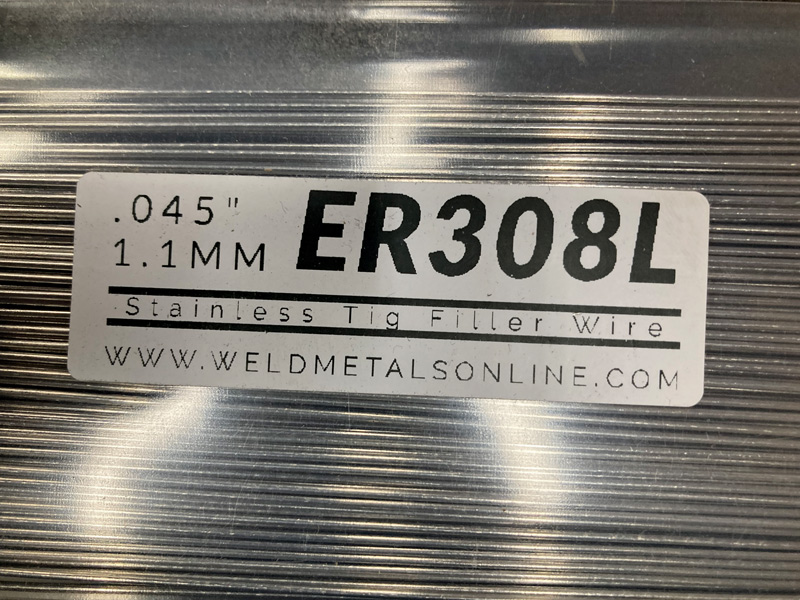
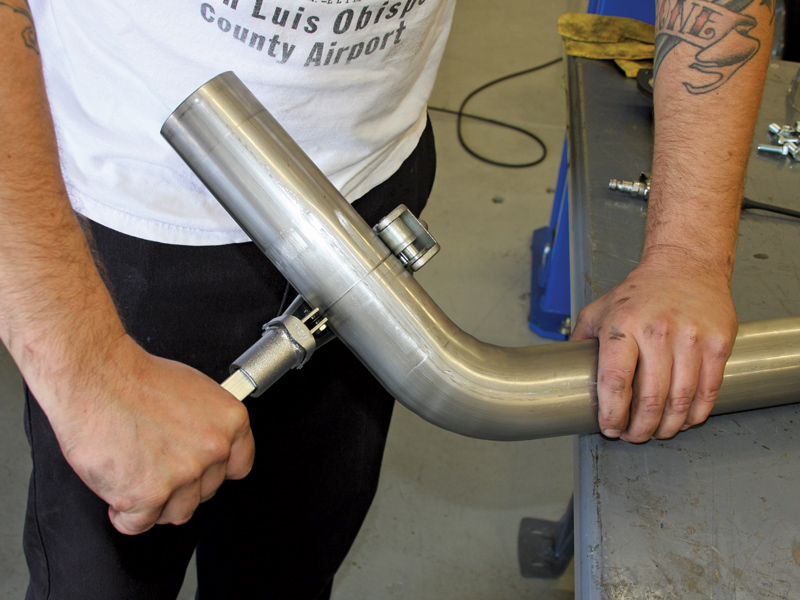
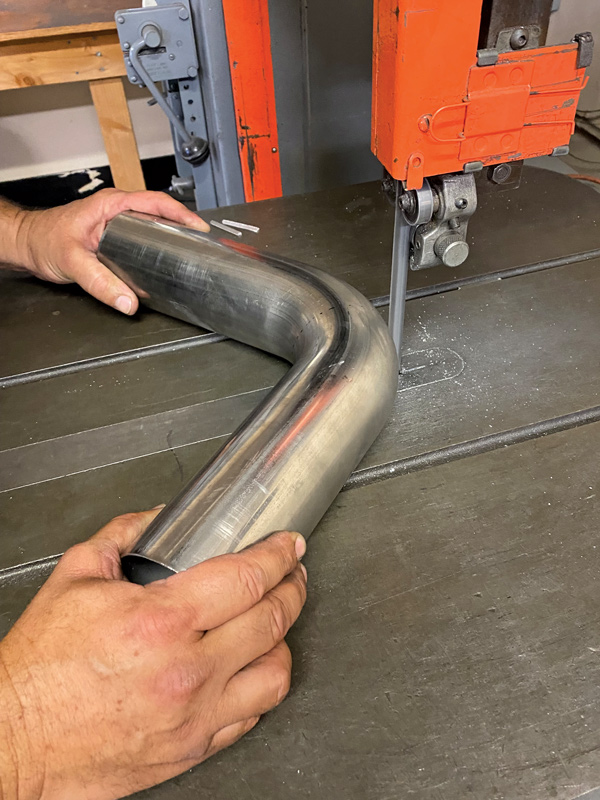
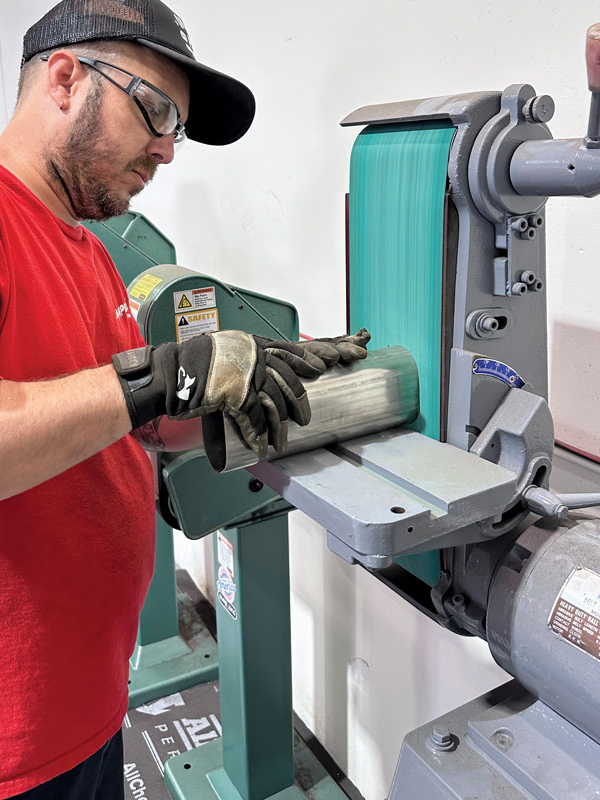
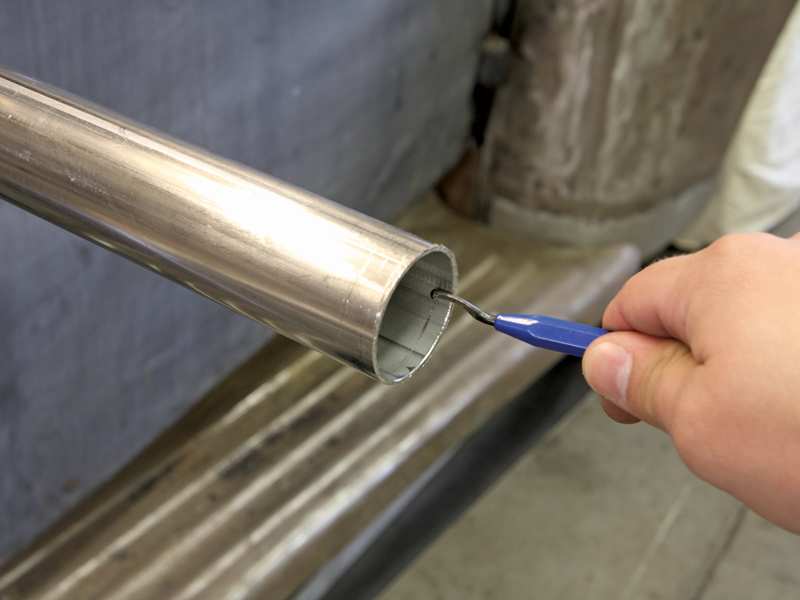
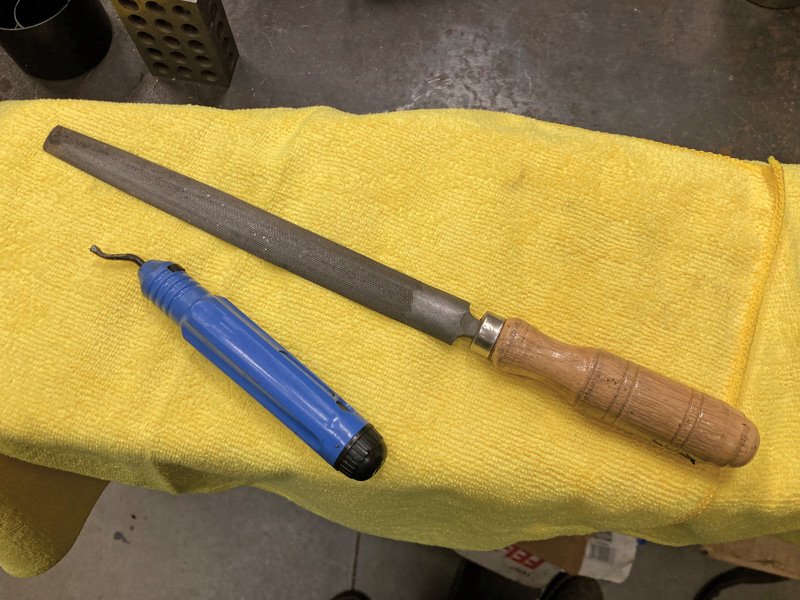
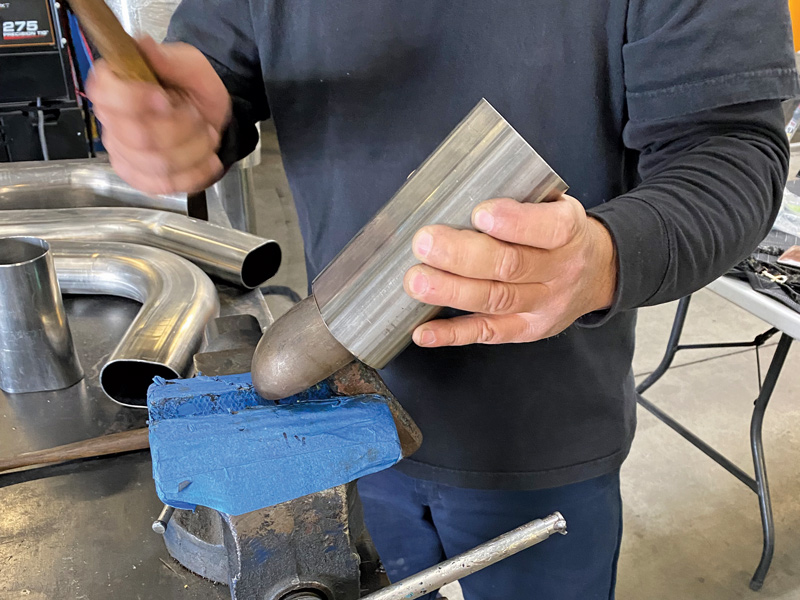
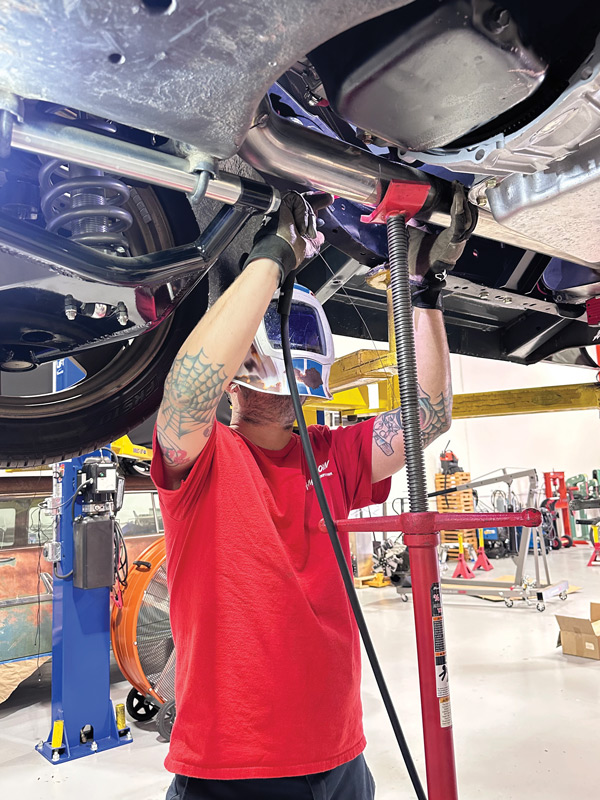
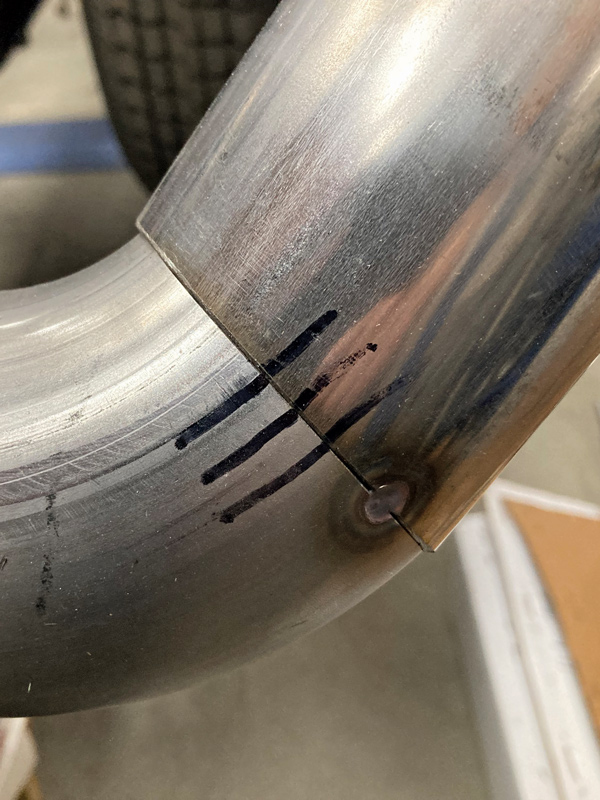
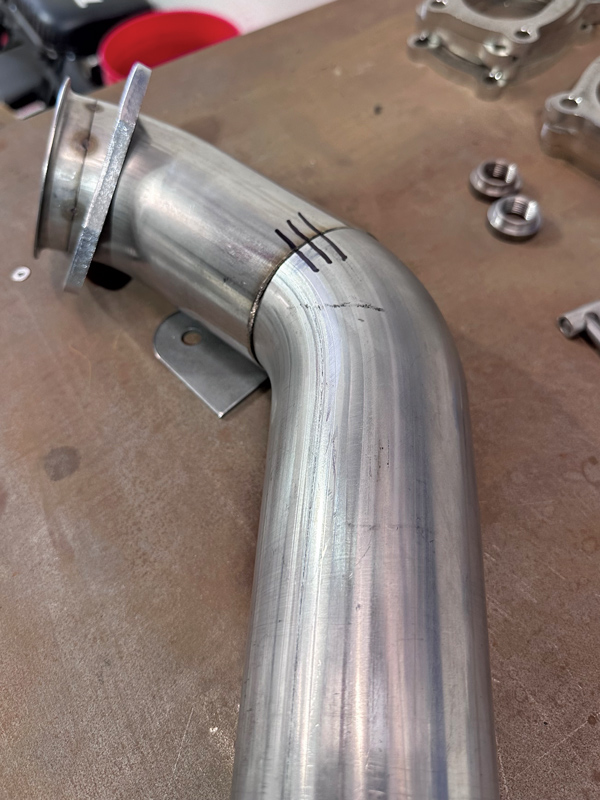
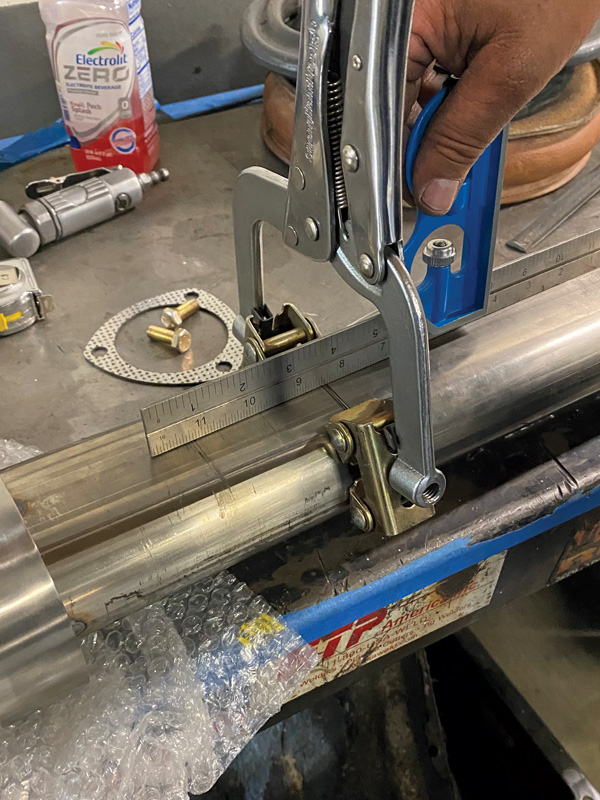
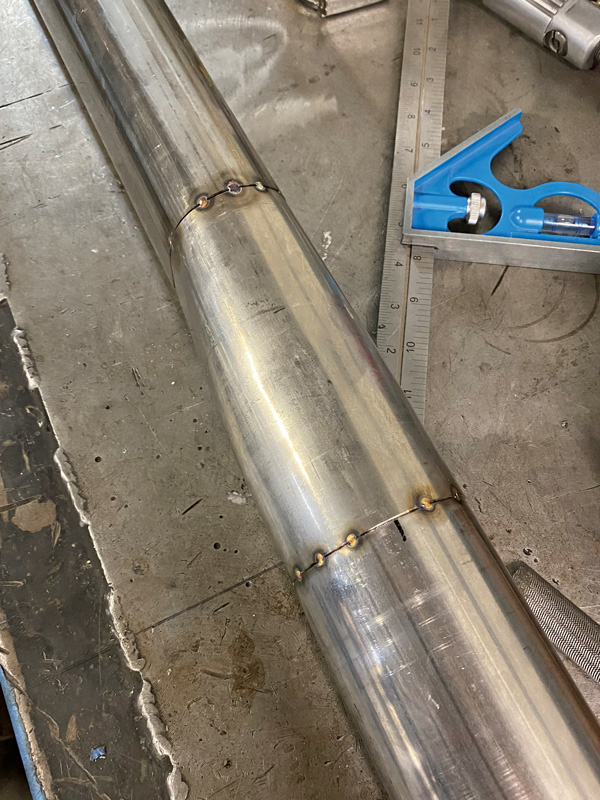
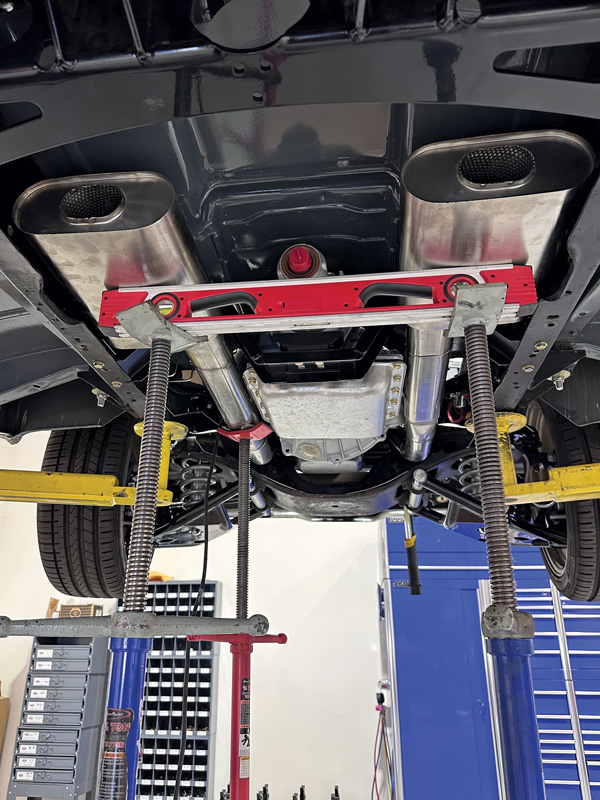
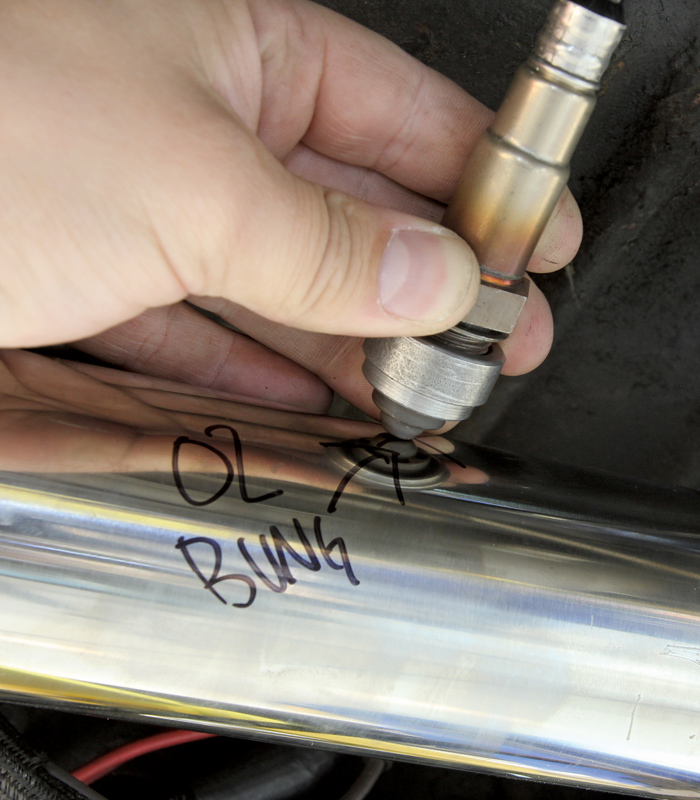
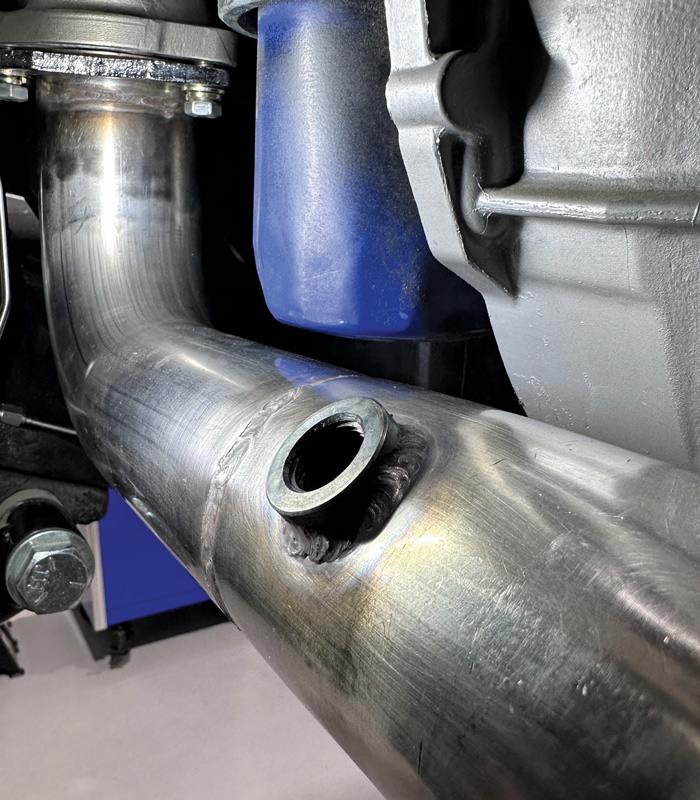
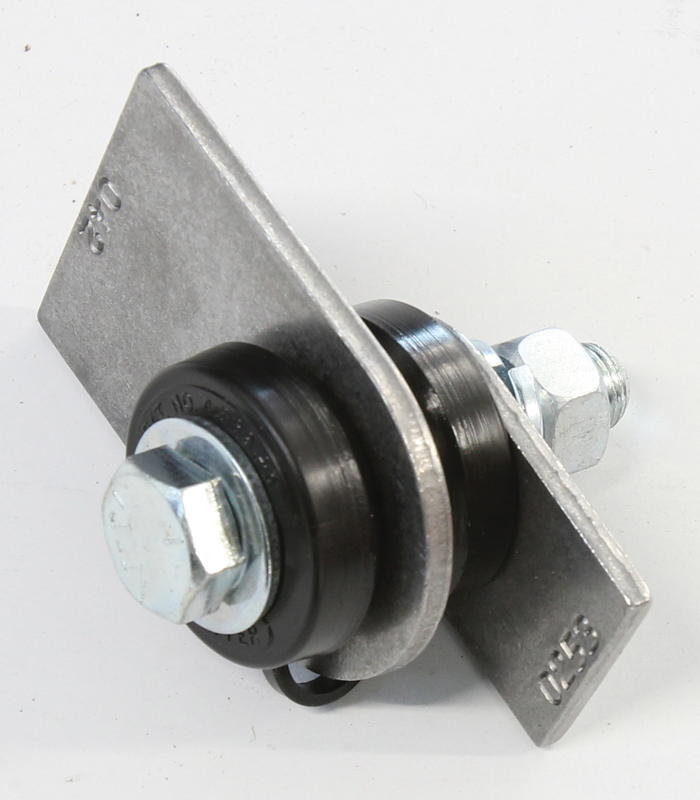
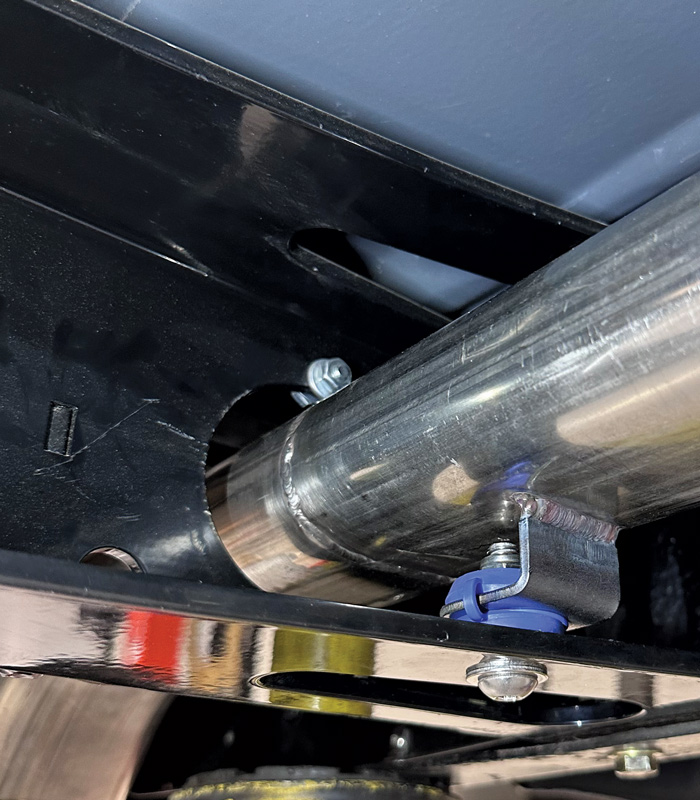
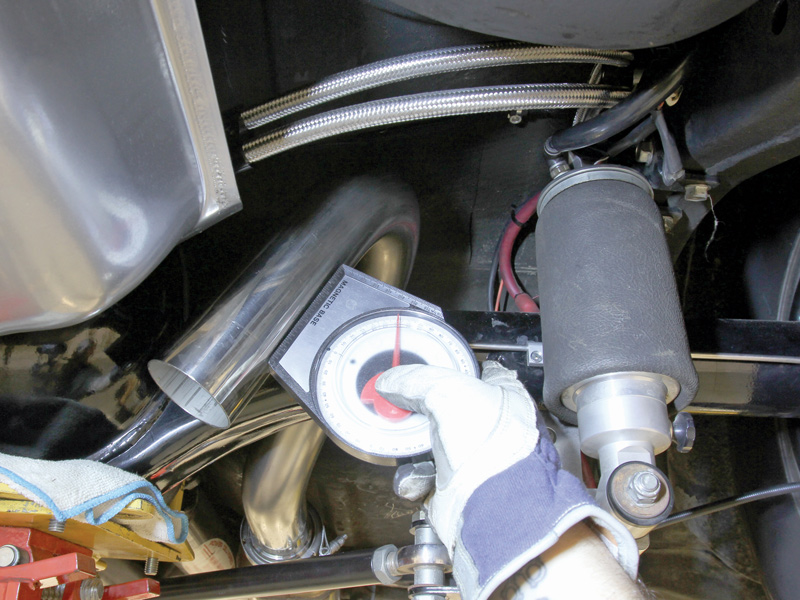
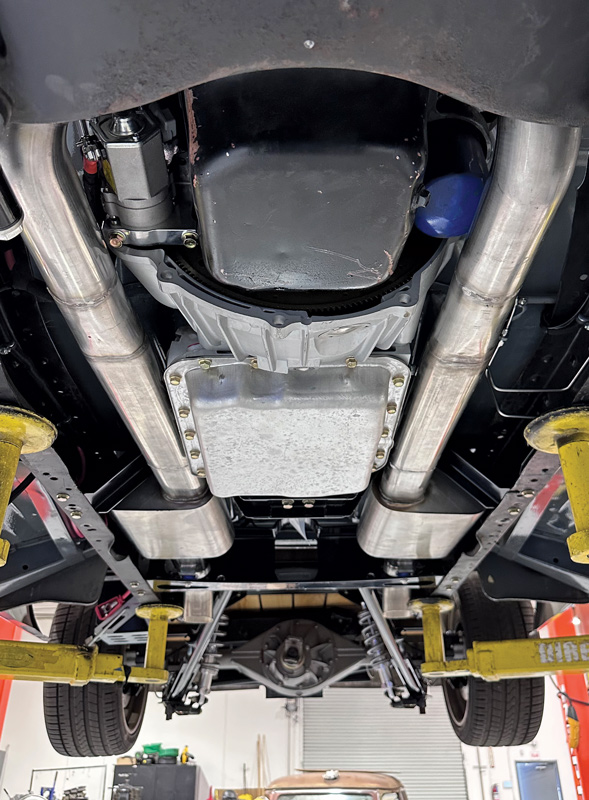
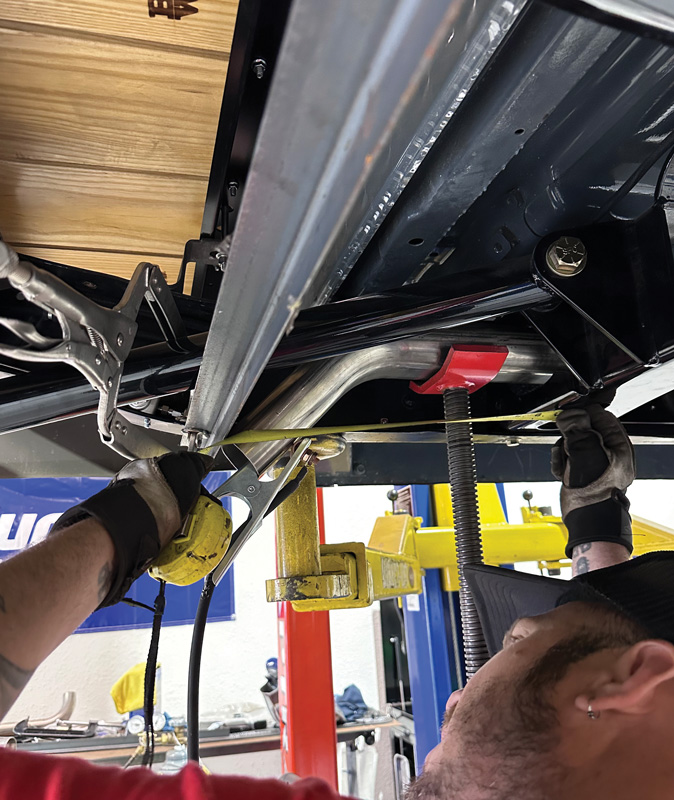
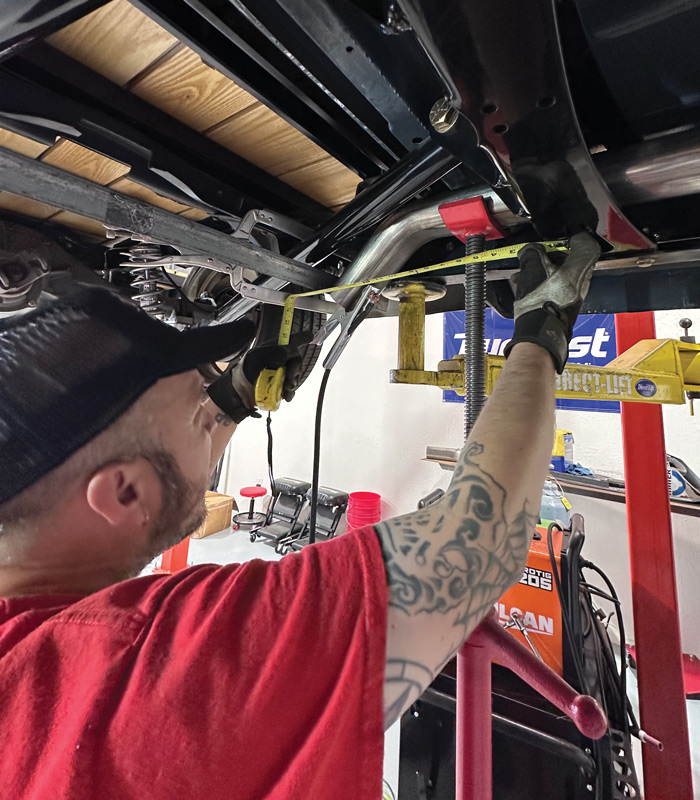
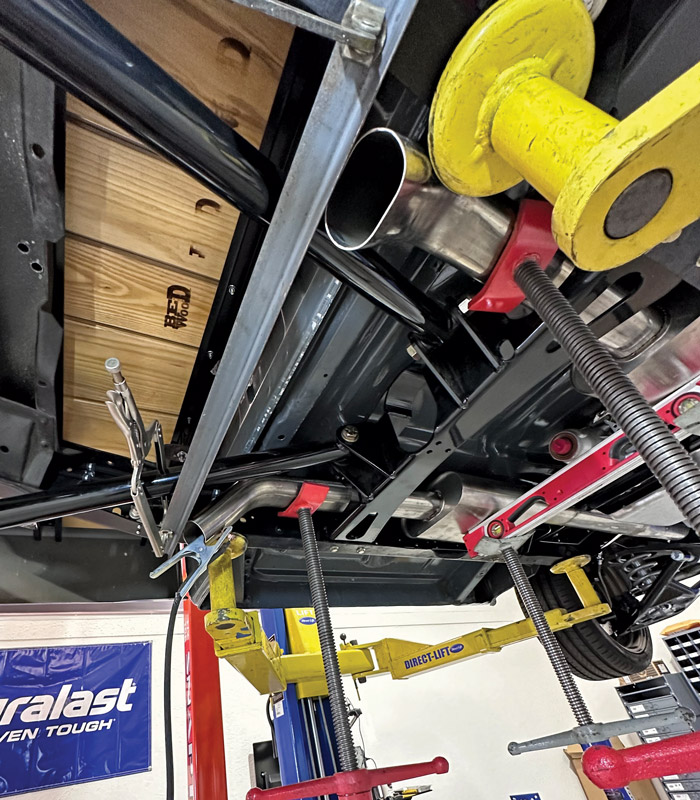
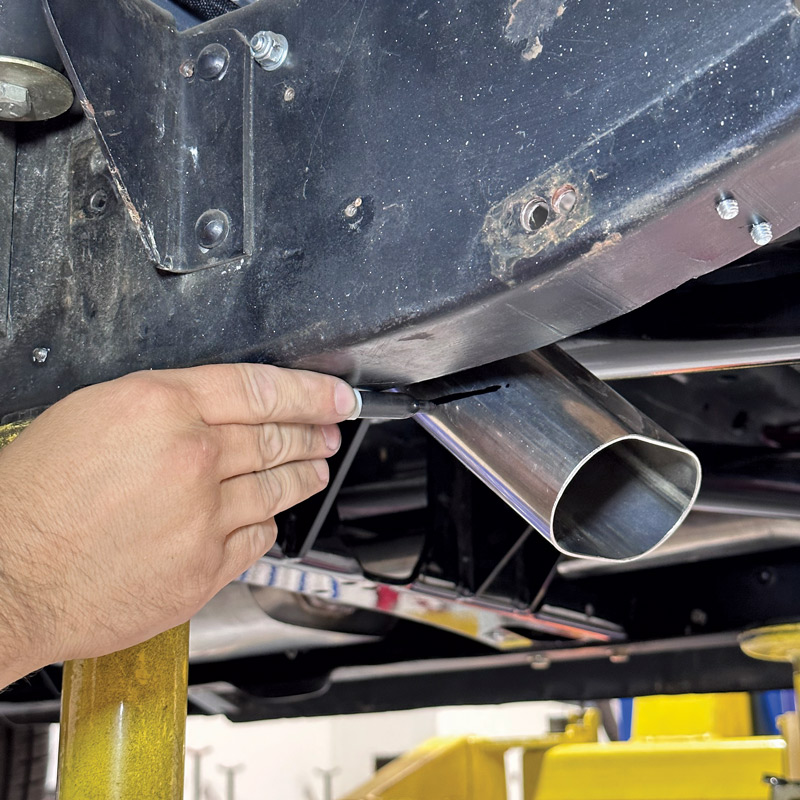
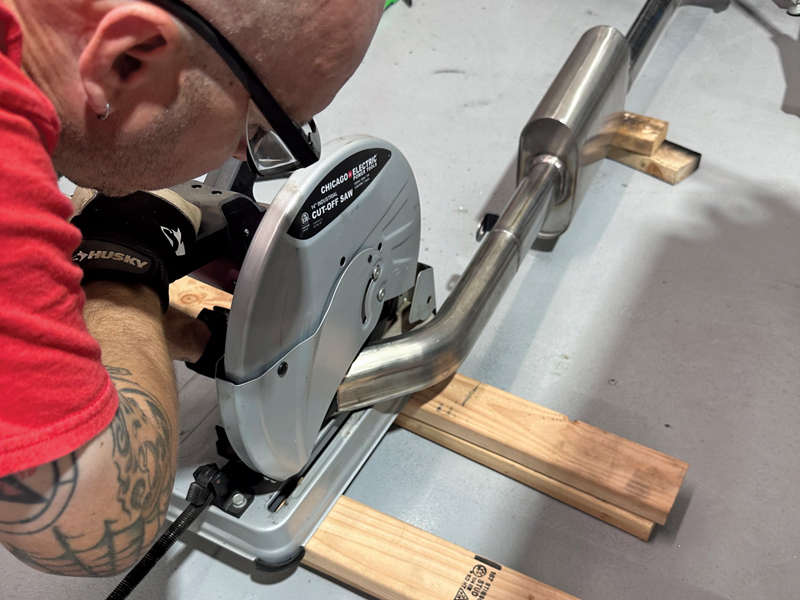
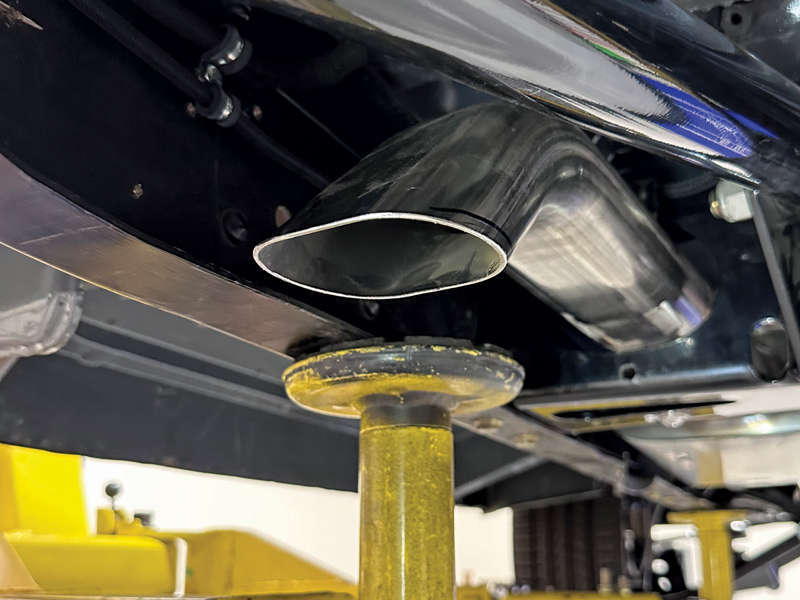

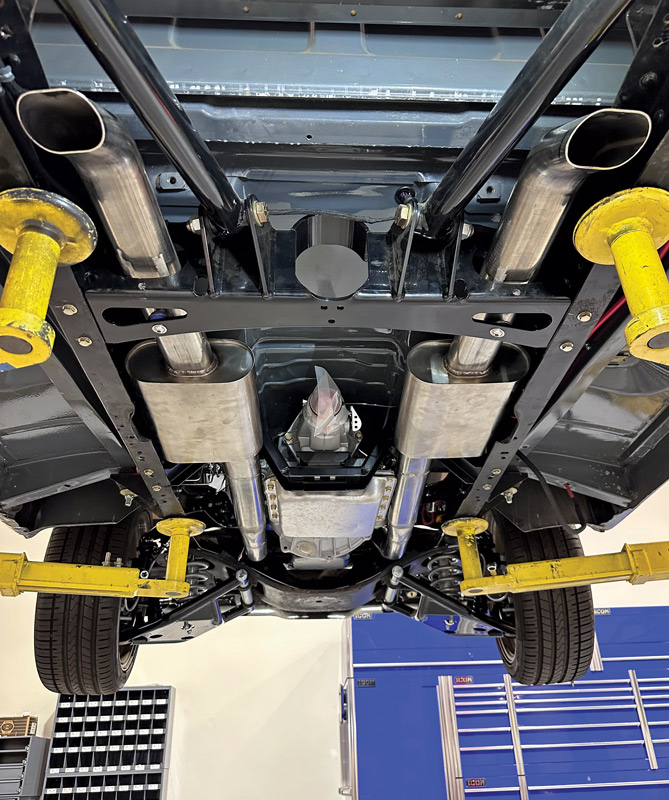
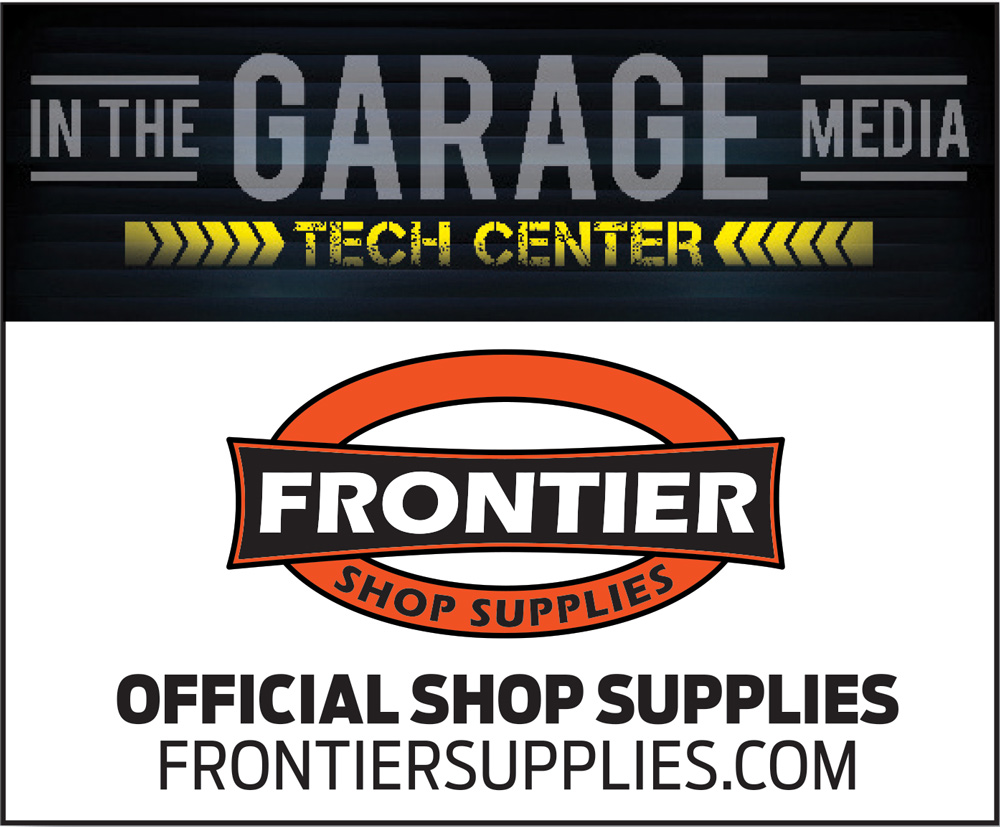
