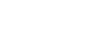

1. The first step in constructing the inner fender panels was to modify the inner fender edges, filling the original holes for the mounting bolts and adding a flange so the new fasteners would be hidden.

Part 4: Inner Fender Panels
BY Ron CovellPhotography BY THE AUTHOR
ork is continuing on the Souza F-100 at Gary’s Rods & Restorations. The most recent areas to be completed are the inner fender panels. The goal was to dramatically clean up the look of the underhood area and to use hidden fasteners to hold all the panels together. It certainly takes a lot of extra planning and work to make panels that fit perfectly when you don’t want the screws to show, but this level of detail has come to be expected for high-end builds like this one, and everyone involved is delighted with the outcome.
As with most projects like this, making paper patterns is a good way to get started since it’s quite easy to cut, trim, and even discard a lot of paper as the design develops, but once the patterns are finalized, often one pattern can be used to cut the blanks for both sides of the vehicle. Also, it’s very likely that after building one side you will find lots of ways to streamline the construction of the other side.
Great care was taken to ensure that the new inner fender panels provided adequate clearance for the large wheels and tires for all possible movements of the steering and suspension components. The front wheels go through a wide range of movement, going from full right to full left steering lock, in the full bump and full droop condition. You don’t want to find out too late that there isn’t quite as much clearance as you would like!
When panels require flanges on the edges there are a variety of techniques that can be used. Long straight flanges are usually made on a sheetmetal brake, but if the flanges need to be curved other strategies may be employed. In some cases, flanges can be shaped over a hammerform, or with a tipping die on a beading machine, but for most of the long flanges on the inner fender panels, the flange was formed as a separate part and then welded to the main panels. When using this type of construction, it’s generally a good idea to avoid welding on the corners of a panel, so a good strategy is to bend an angle from sheetmetal, then contour it as needed by working the flanges with a shrinker and stretcher. When this angle is welded to the larger panel it positions the weld in a place where it’s much easier to work out the distortion, and the brake-formed corner will be very smooth and consistent. This is one of the hallmarks of high-quality metalwork.
There are many other tricks of the trade that the photos will display, so follow along as we show you how this complex assembly of panels was designed, fabricated, and finished. There’s a lot going on here that could be useful for your own projects!
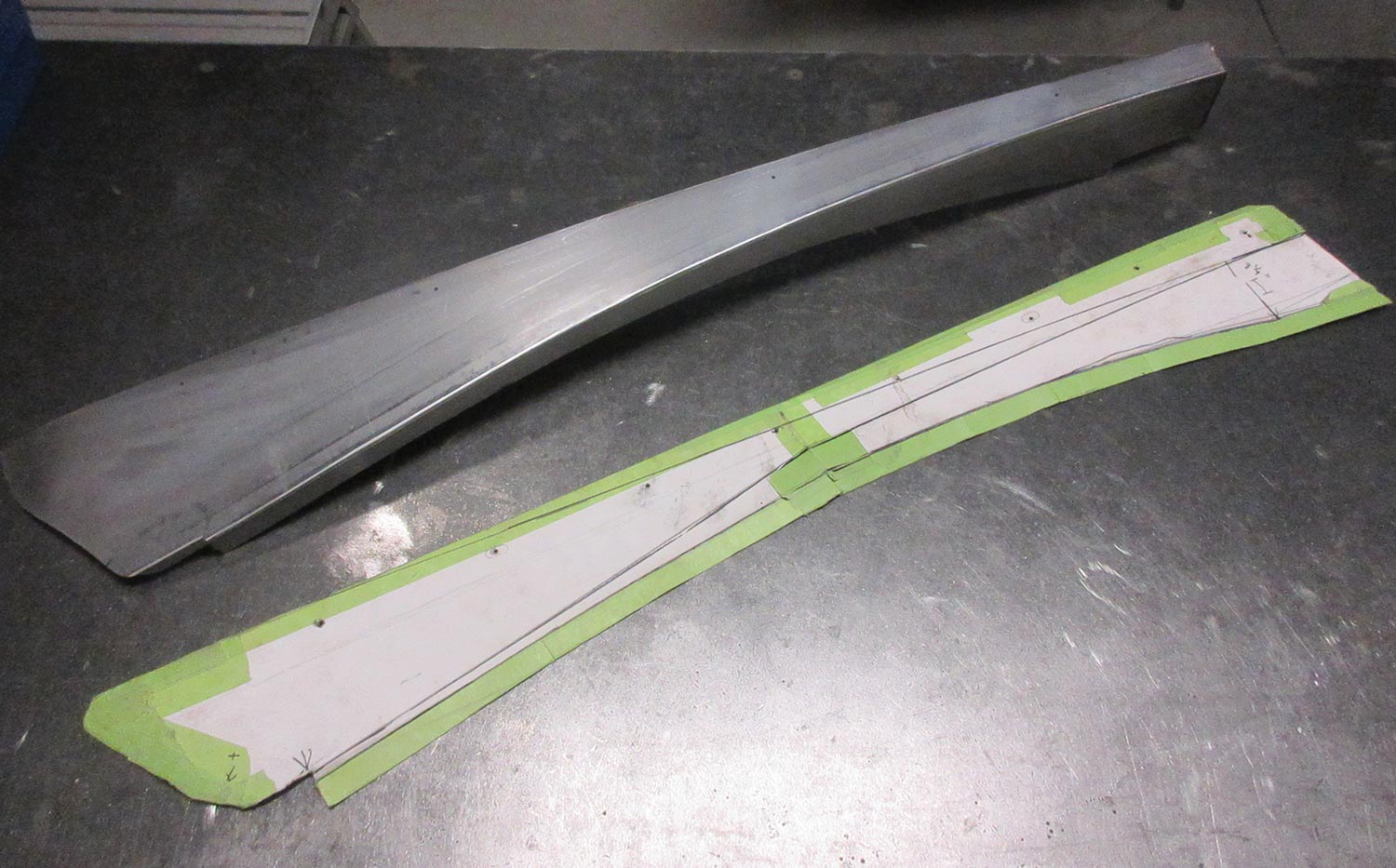
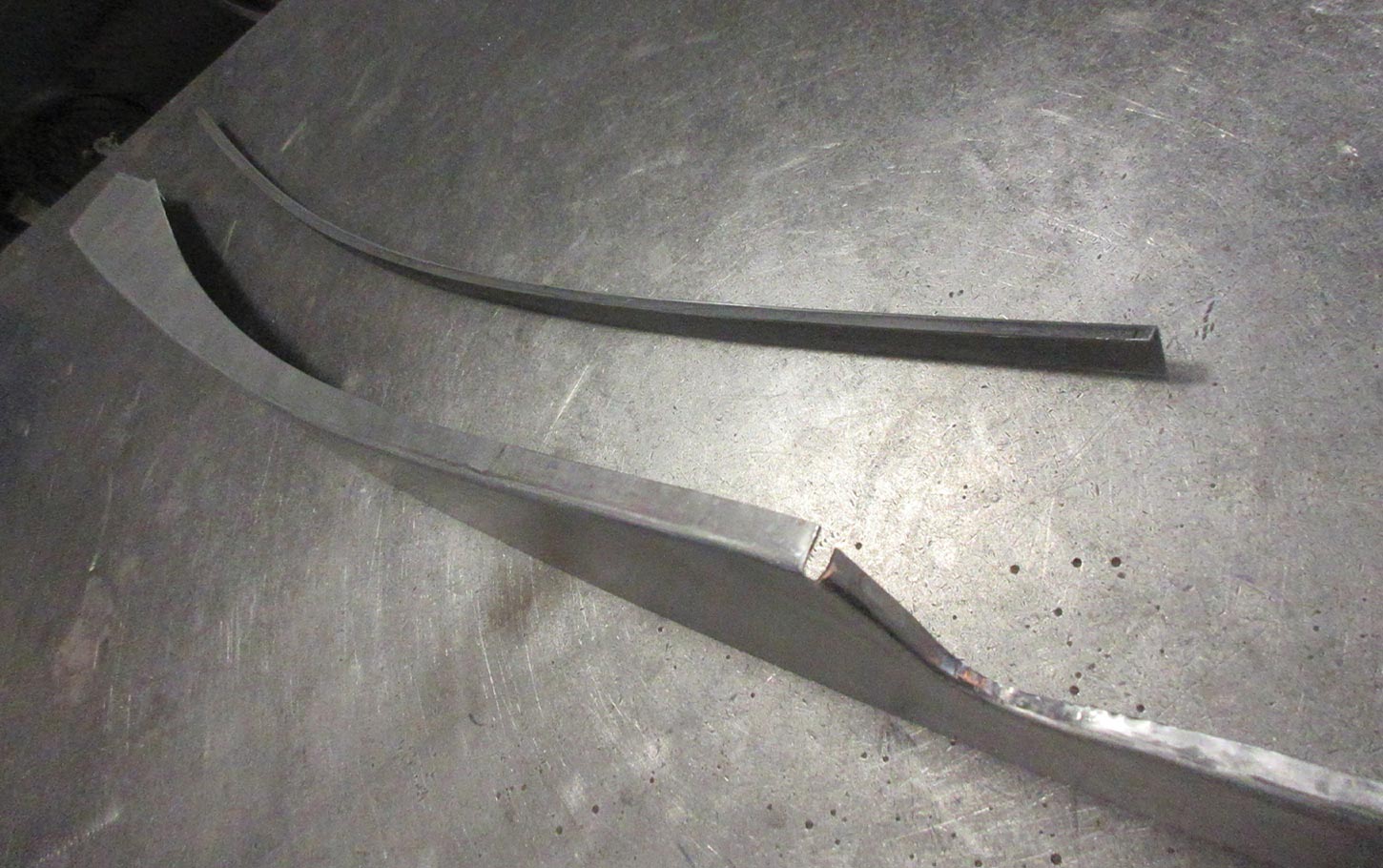
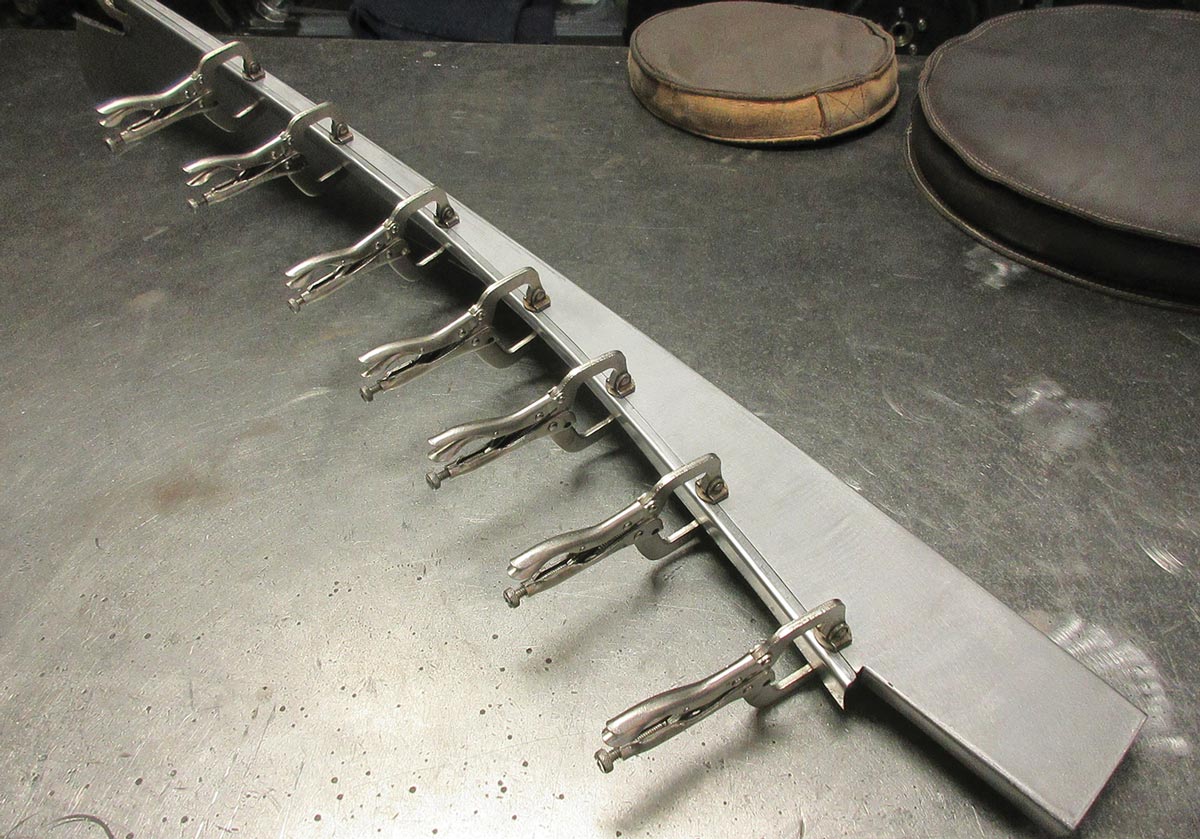
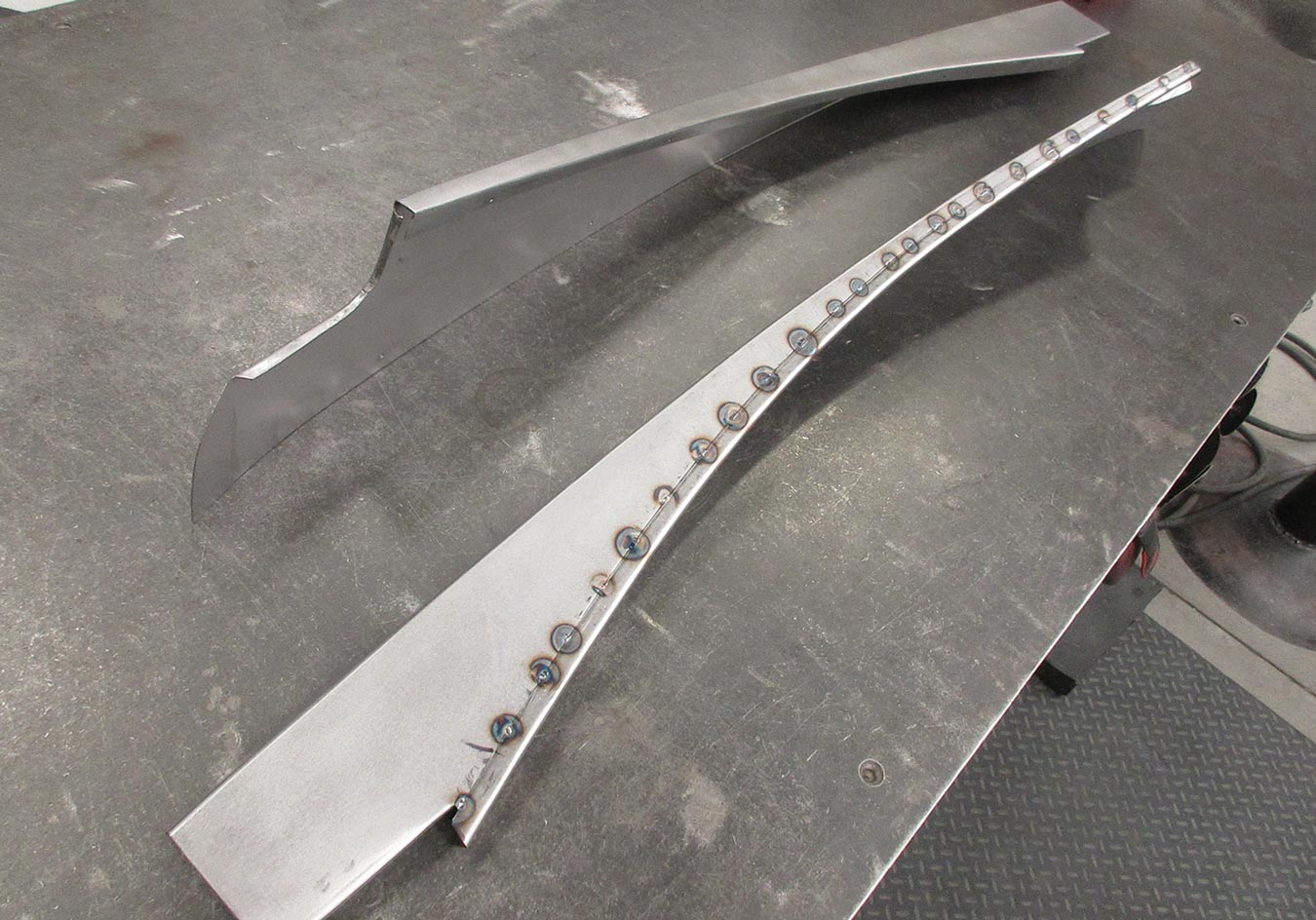
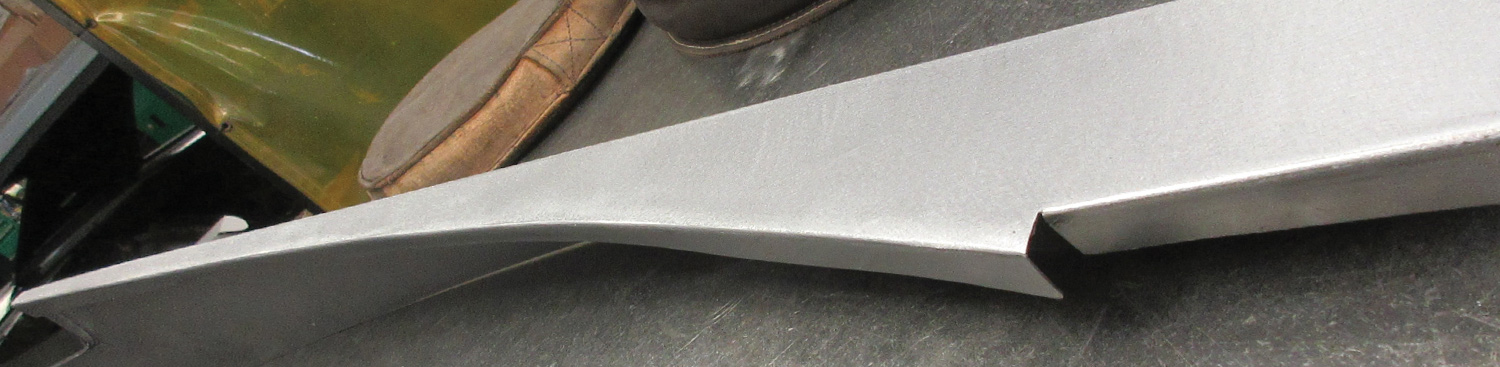
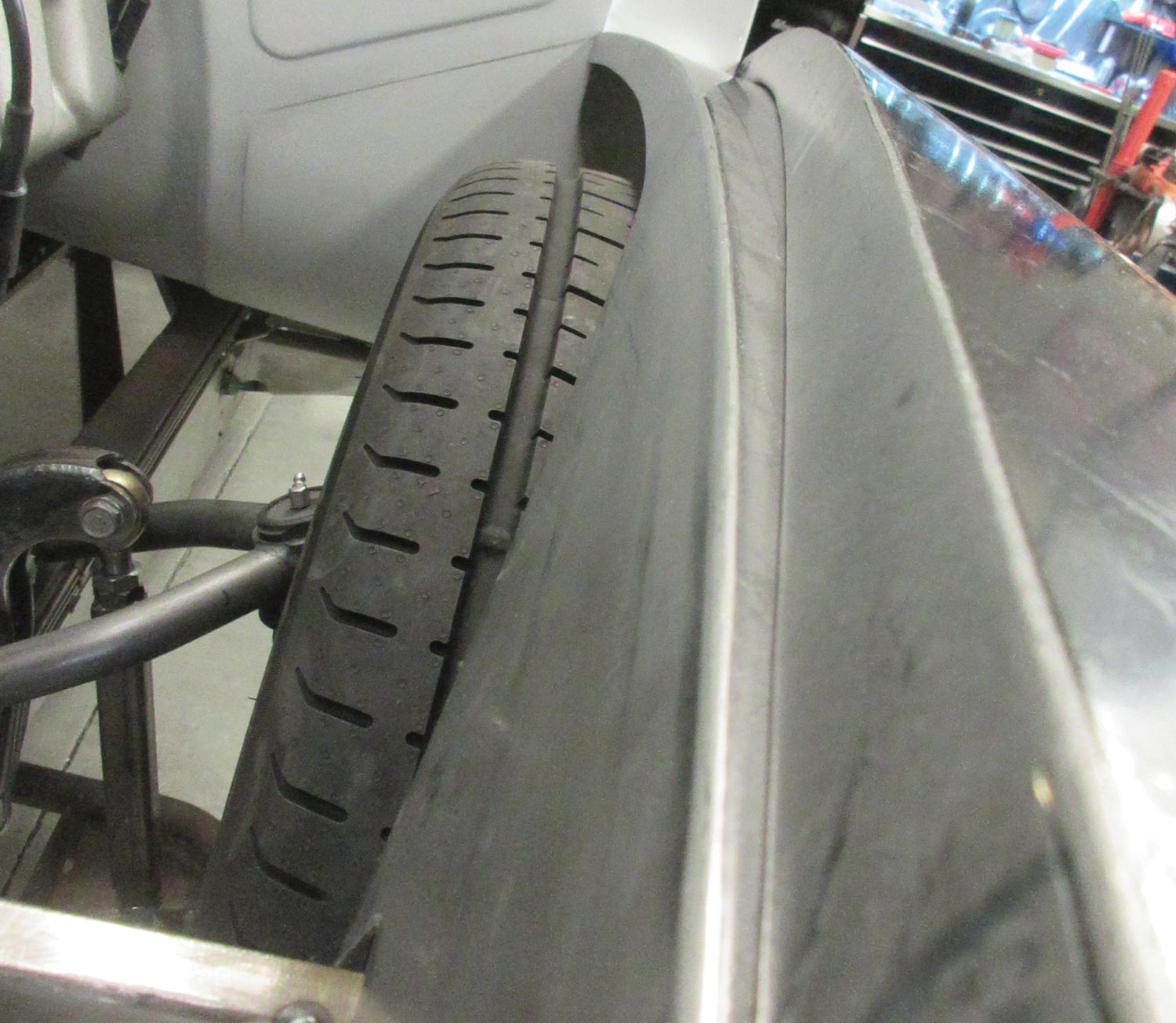

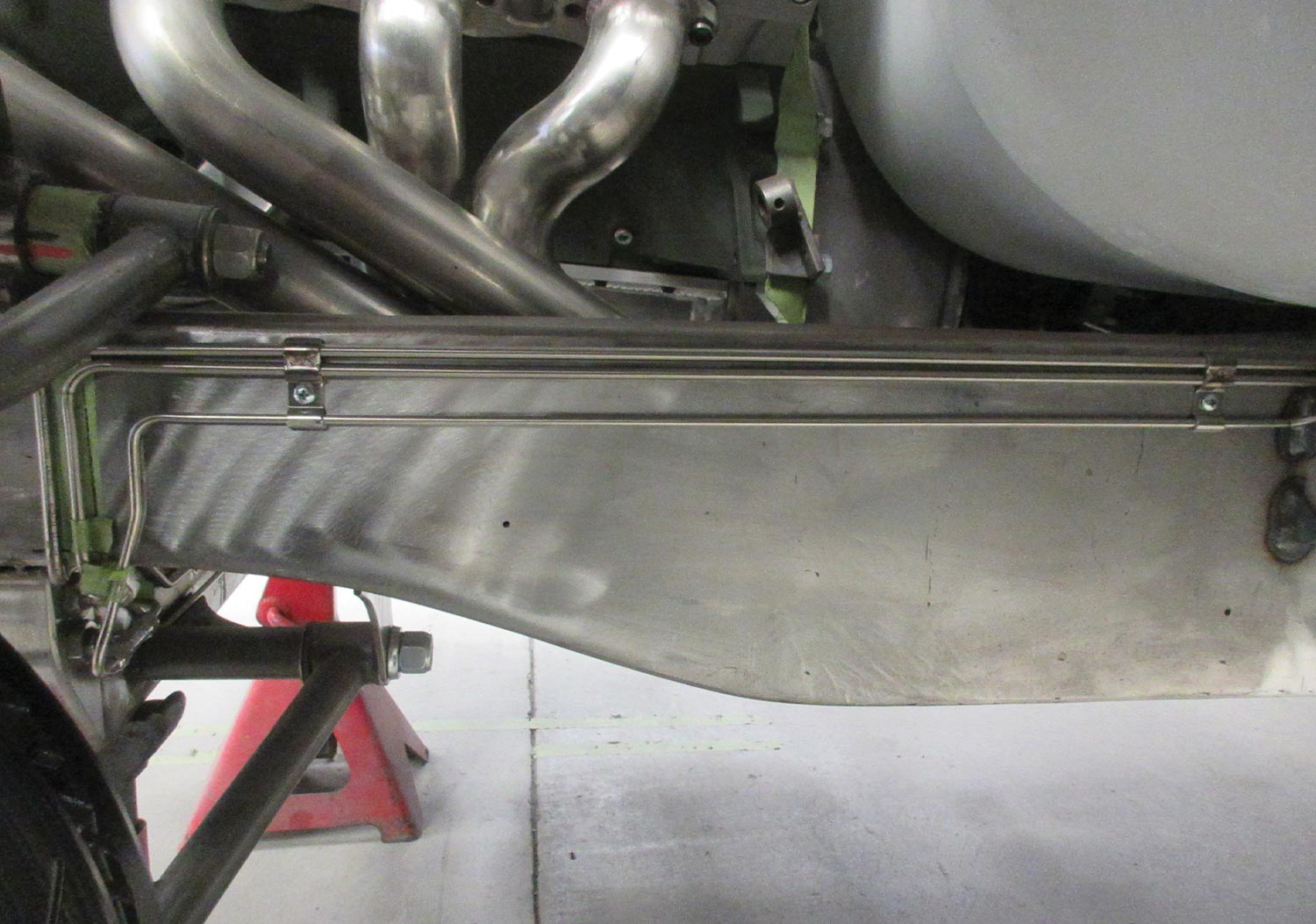
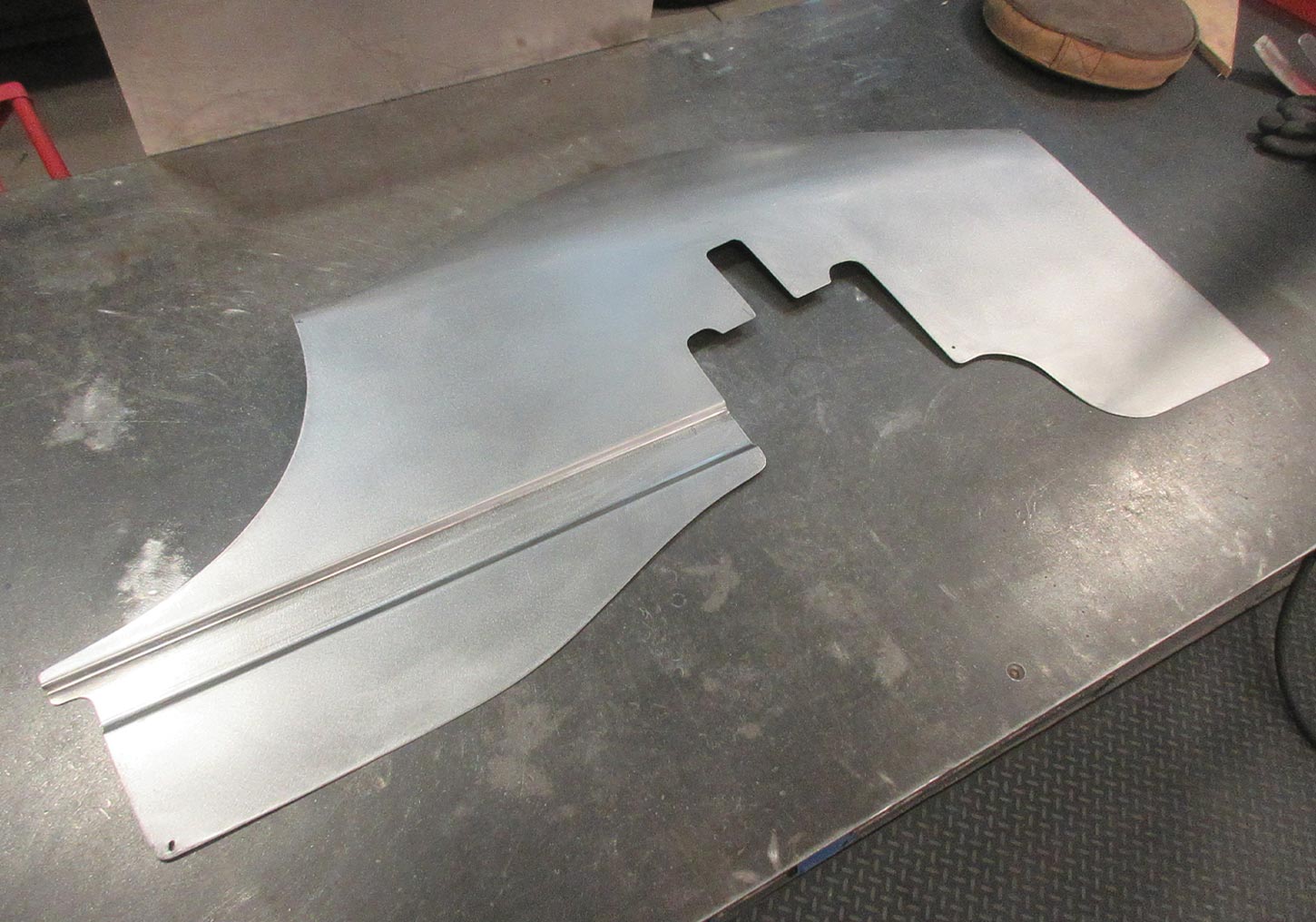
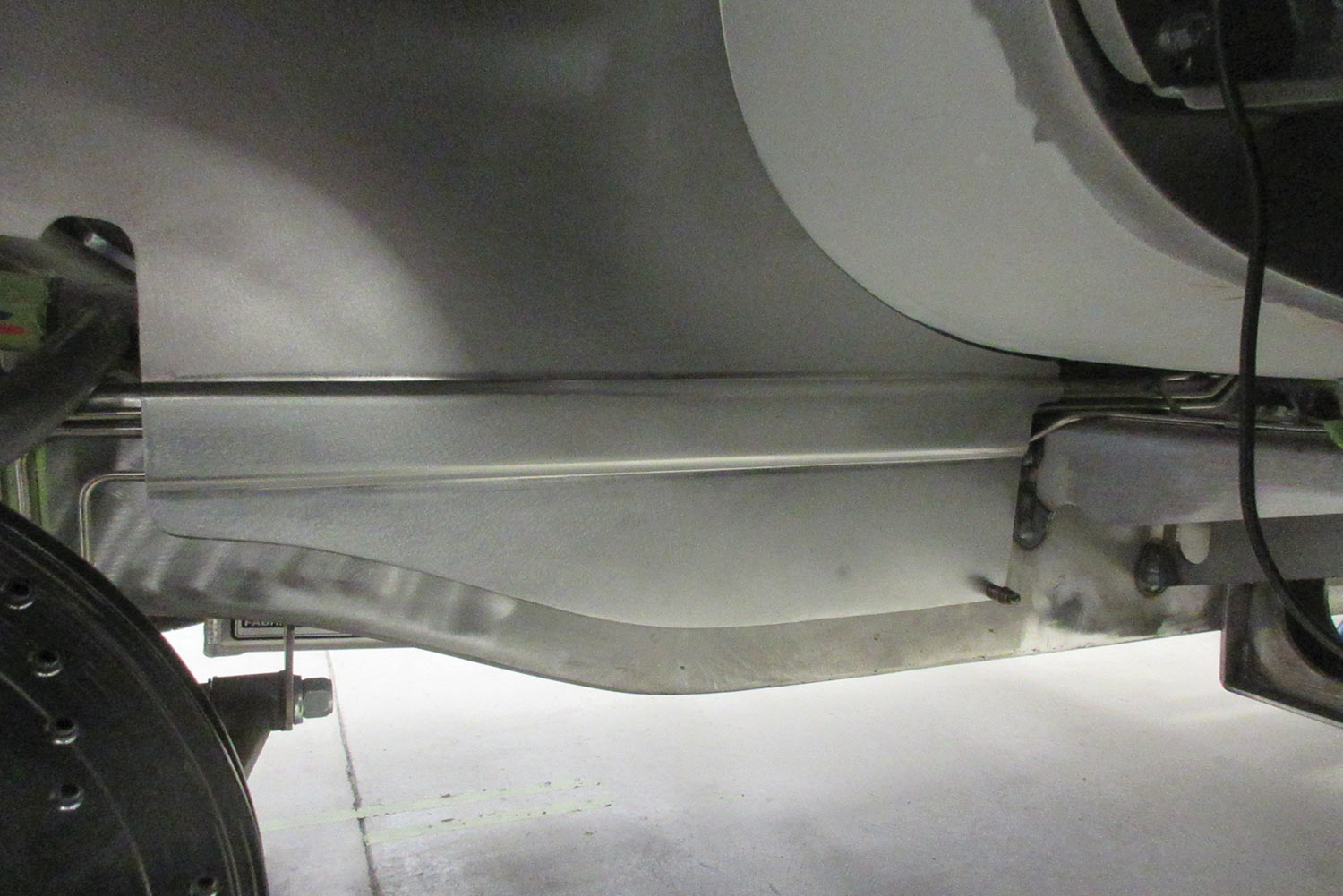
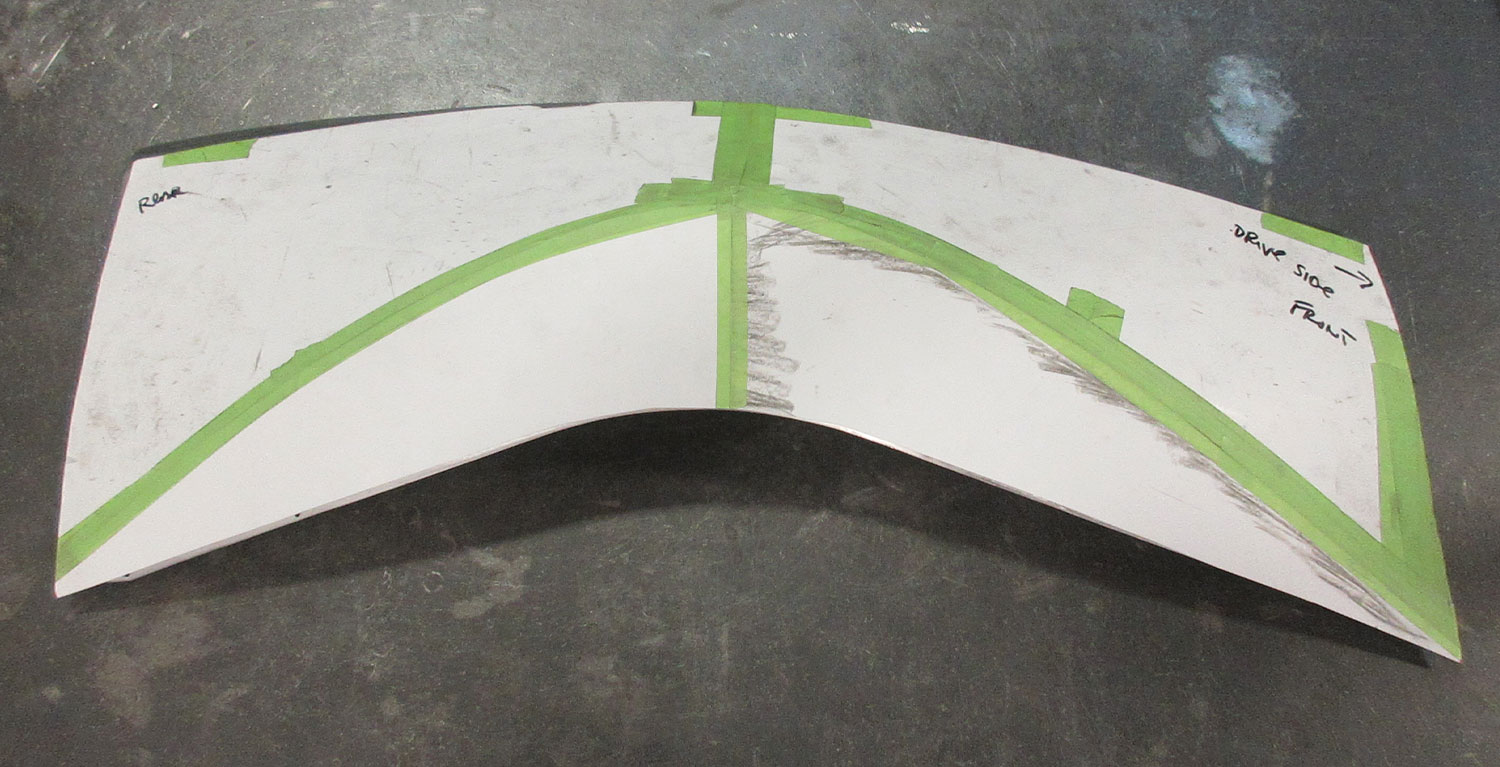
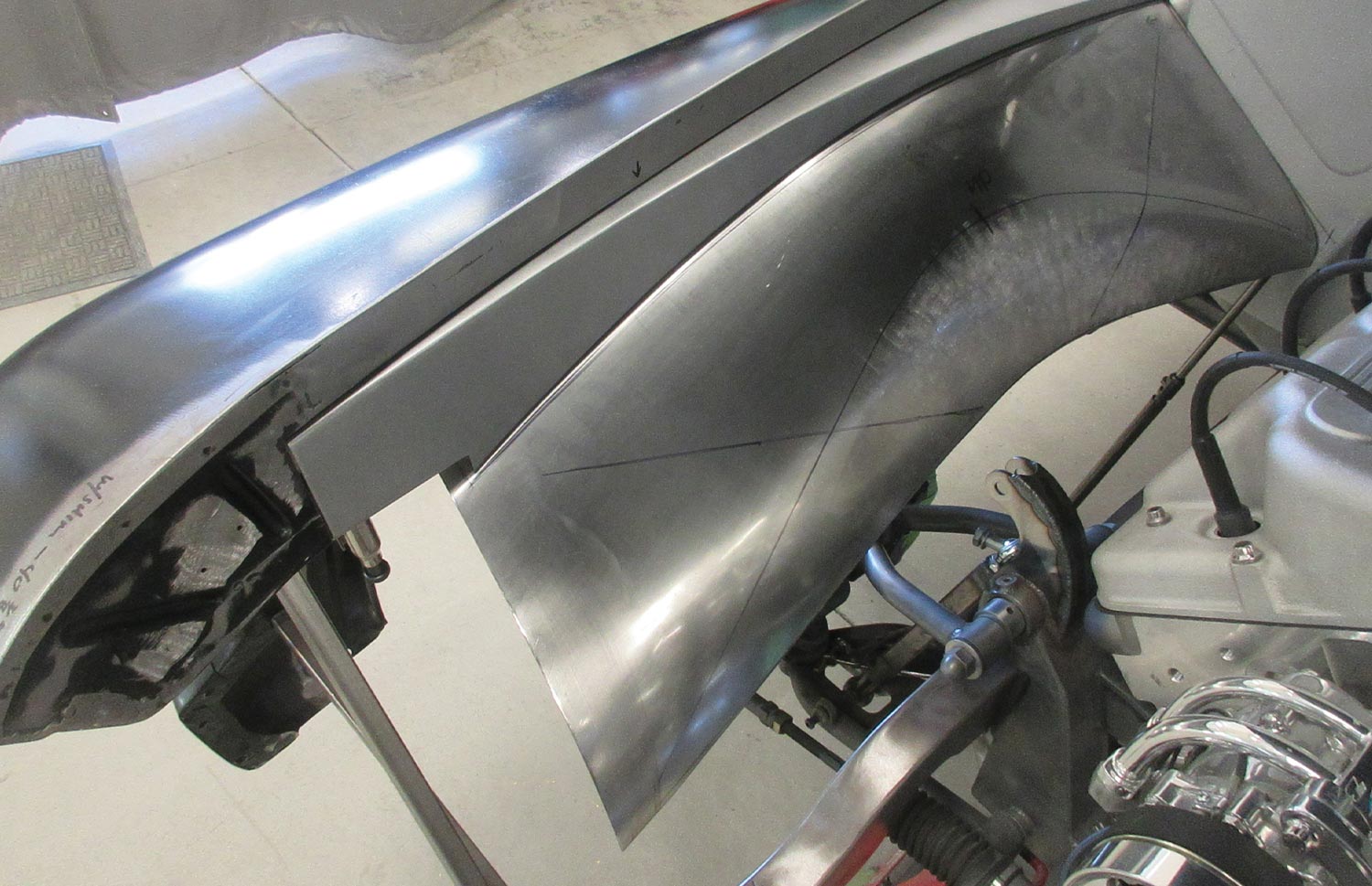
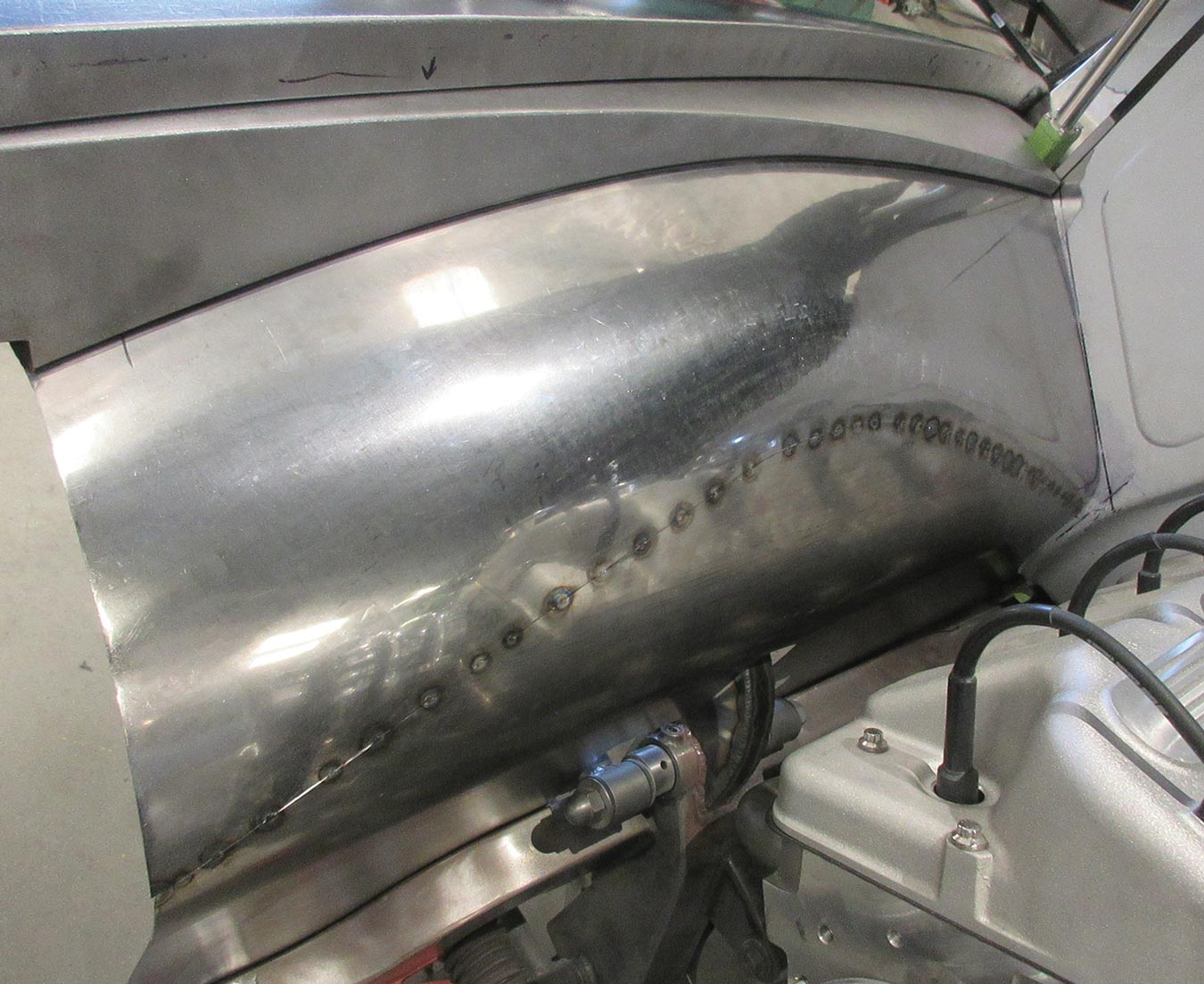
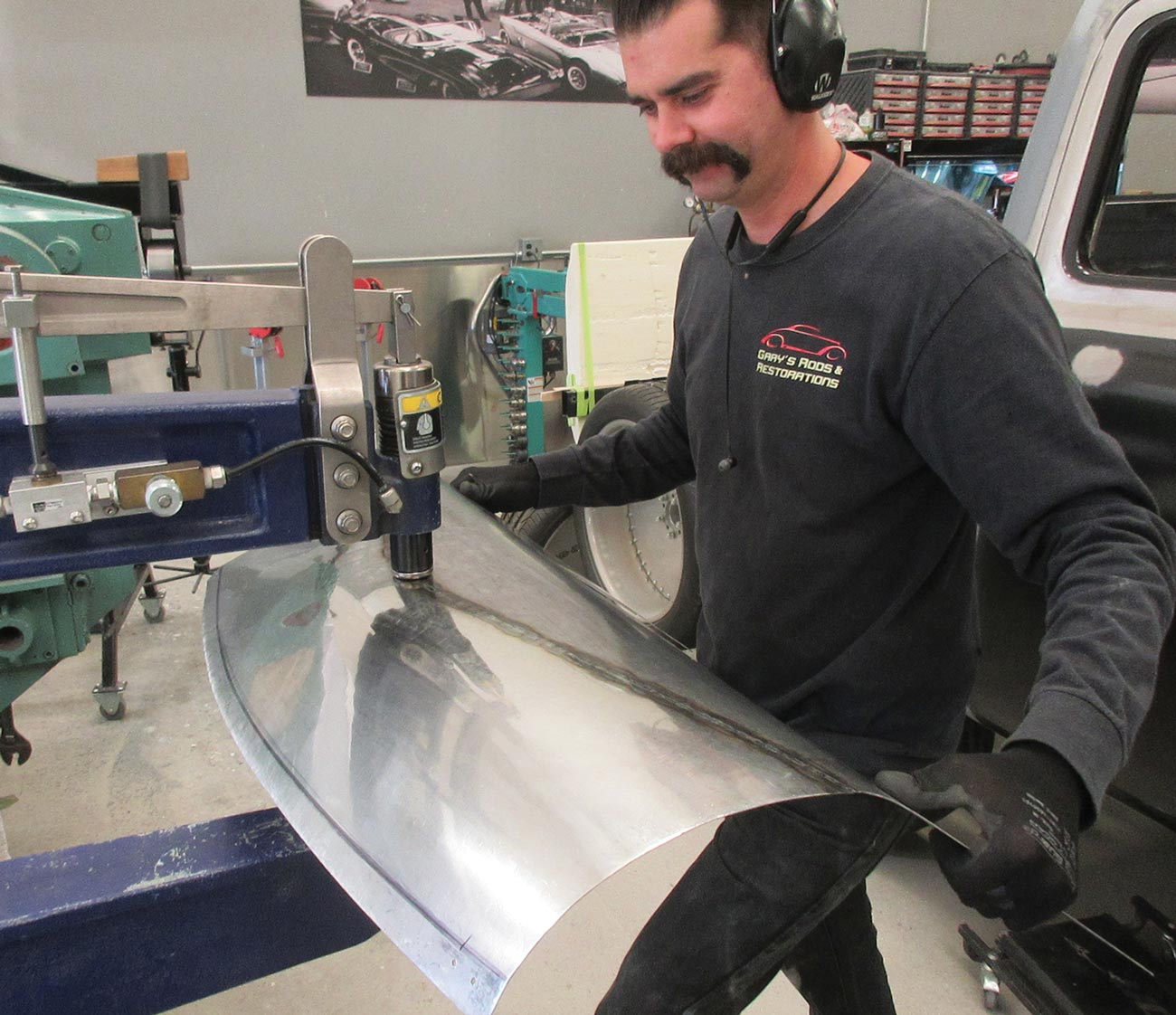
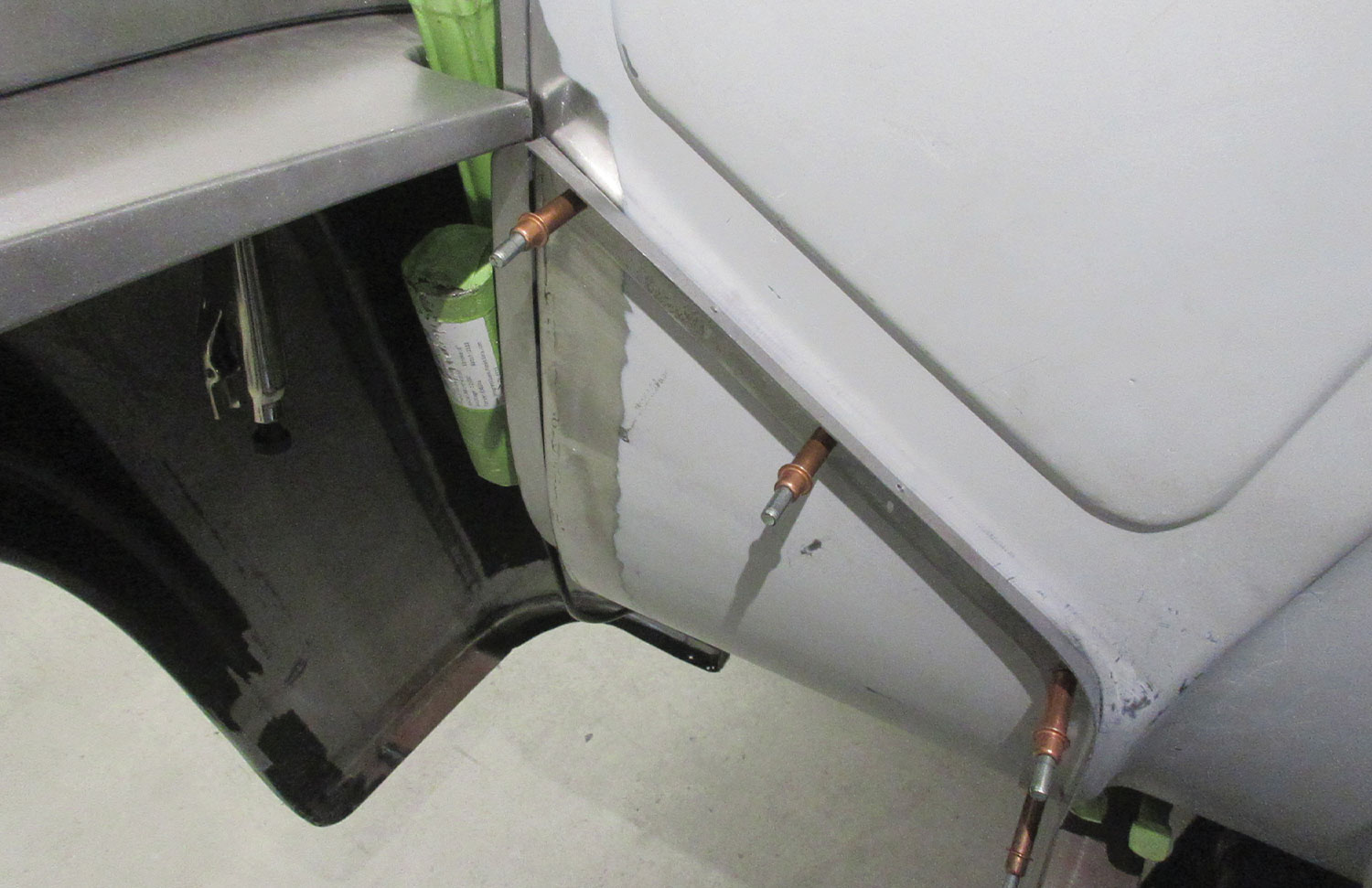
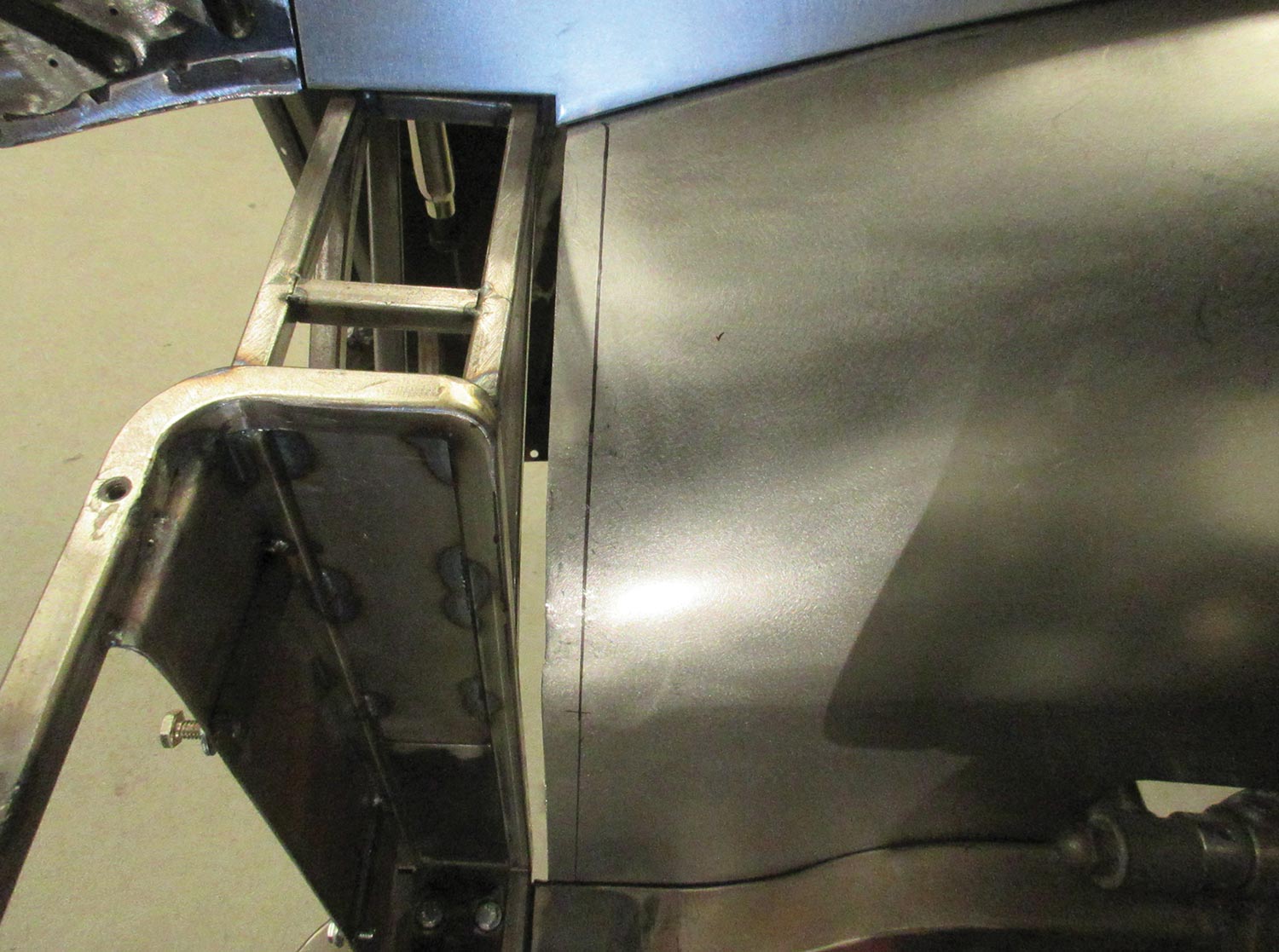
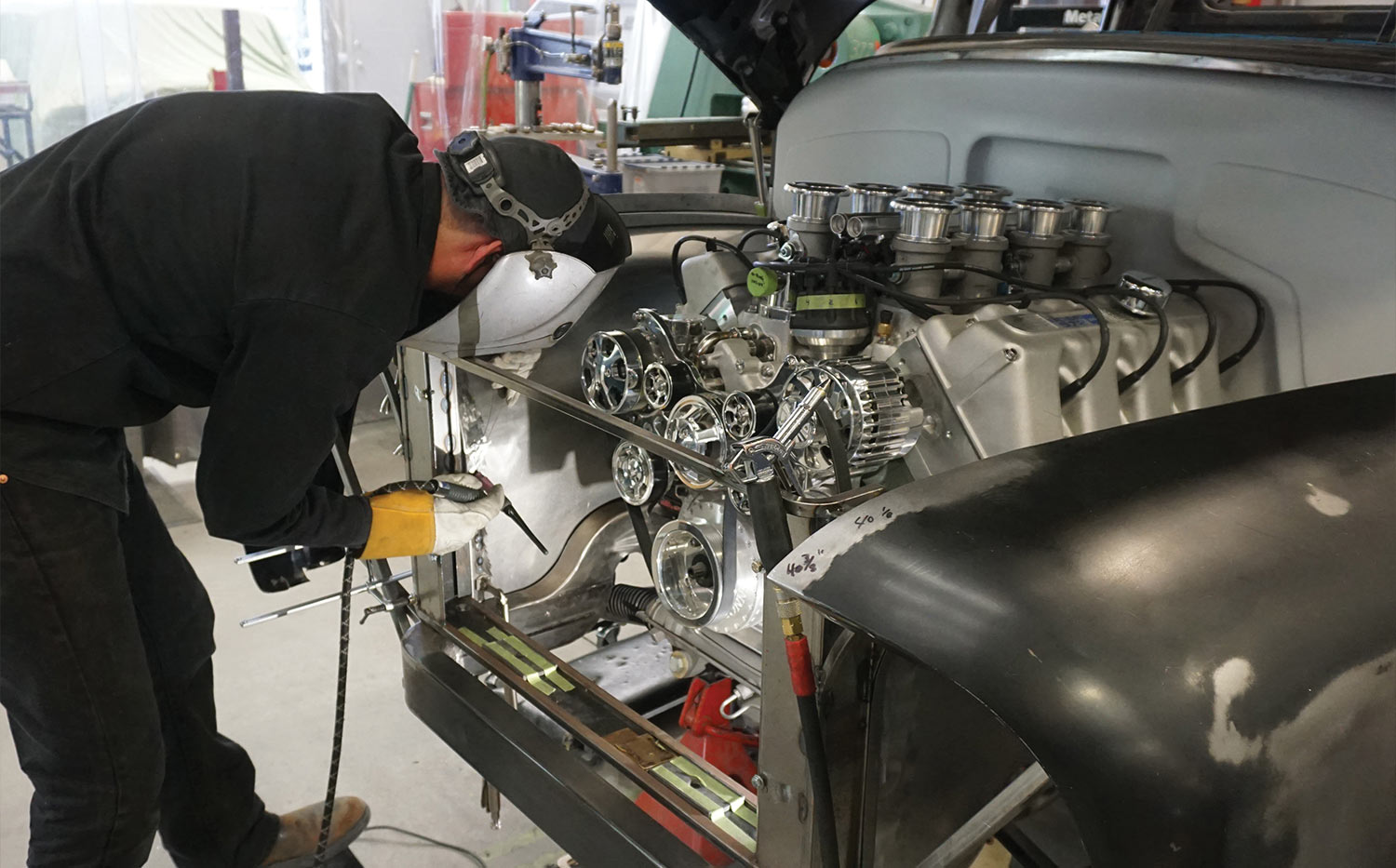
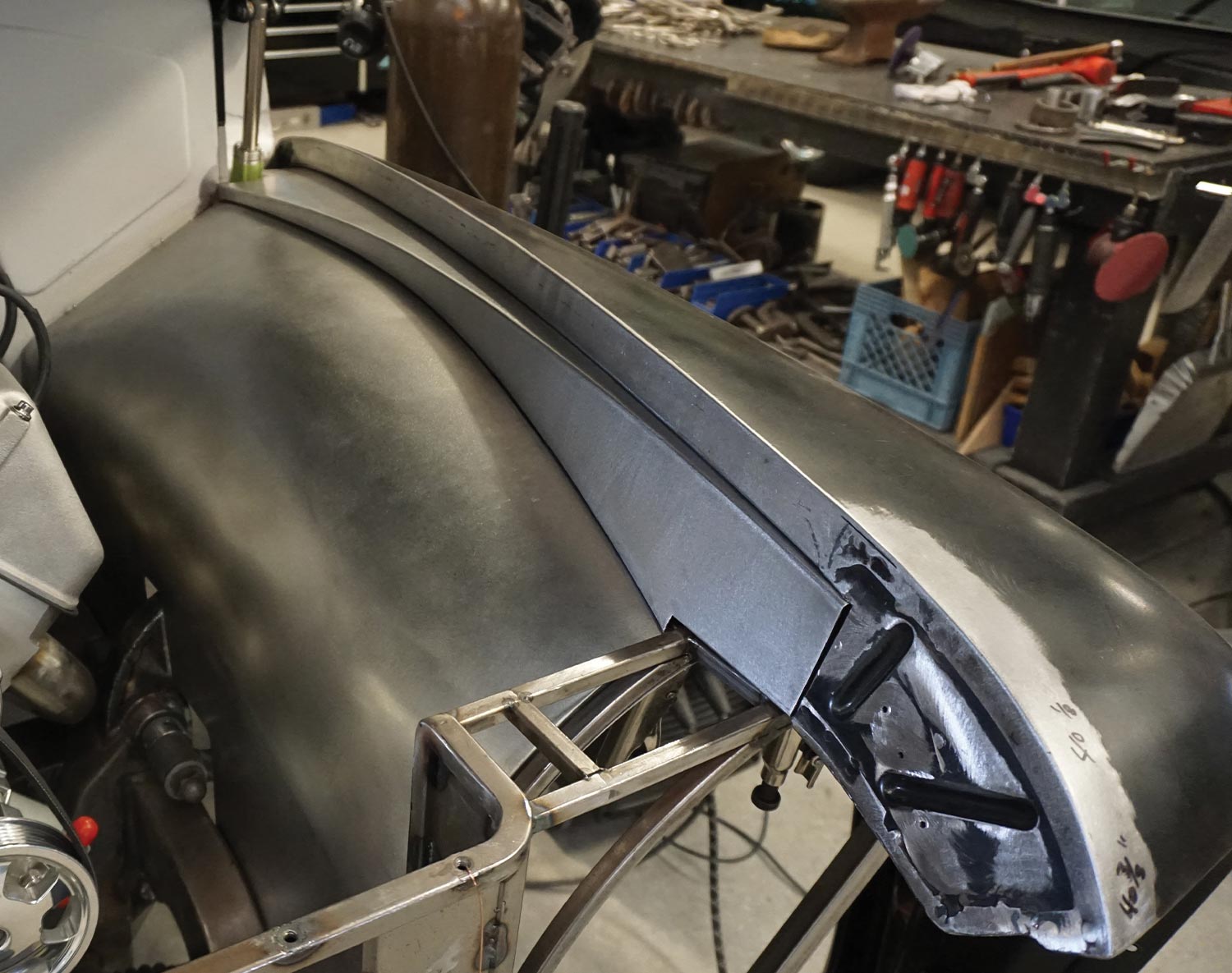
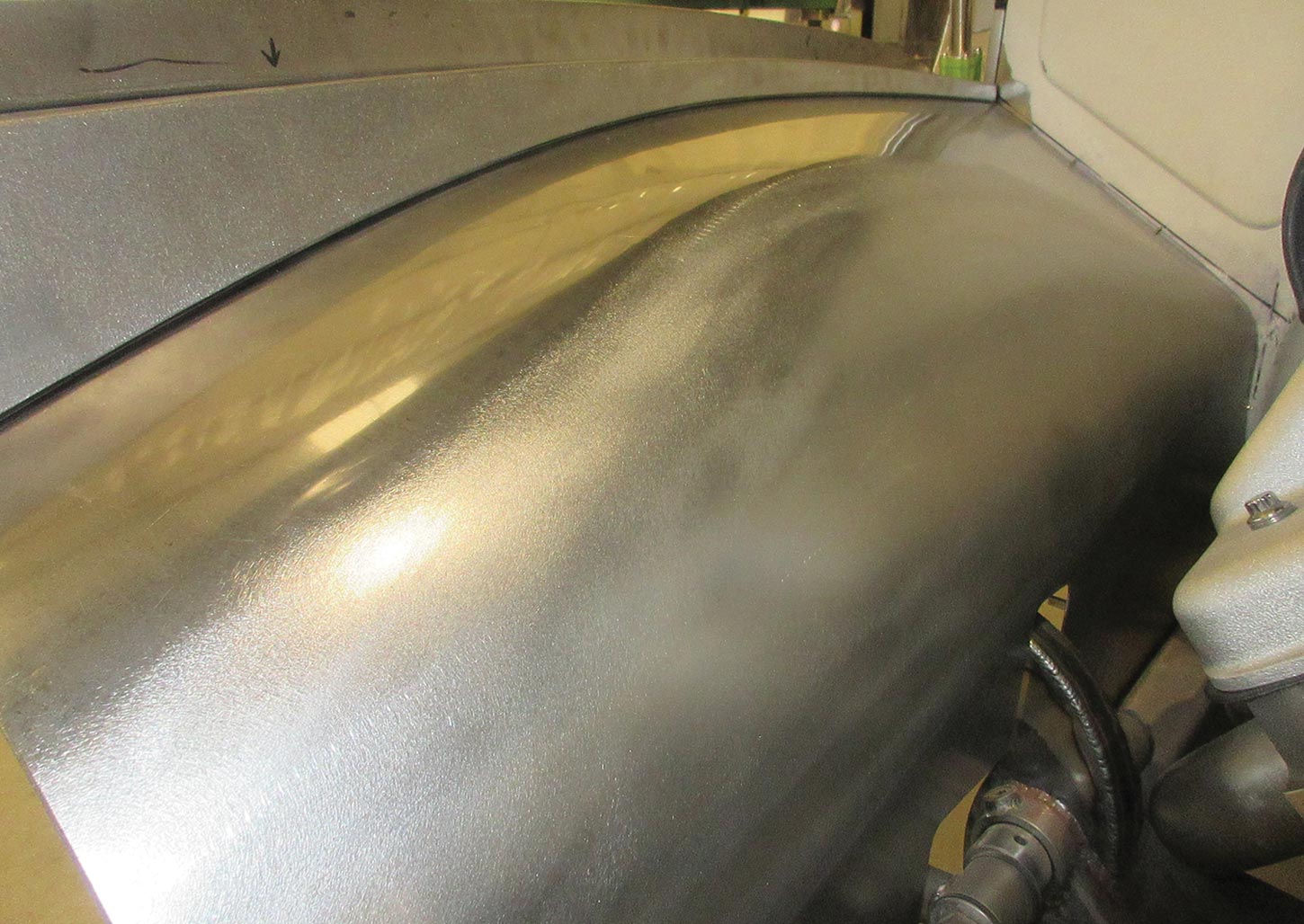
