

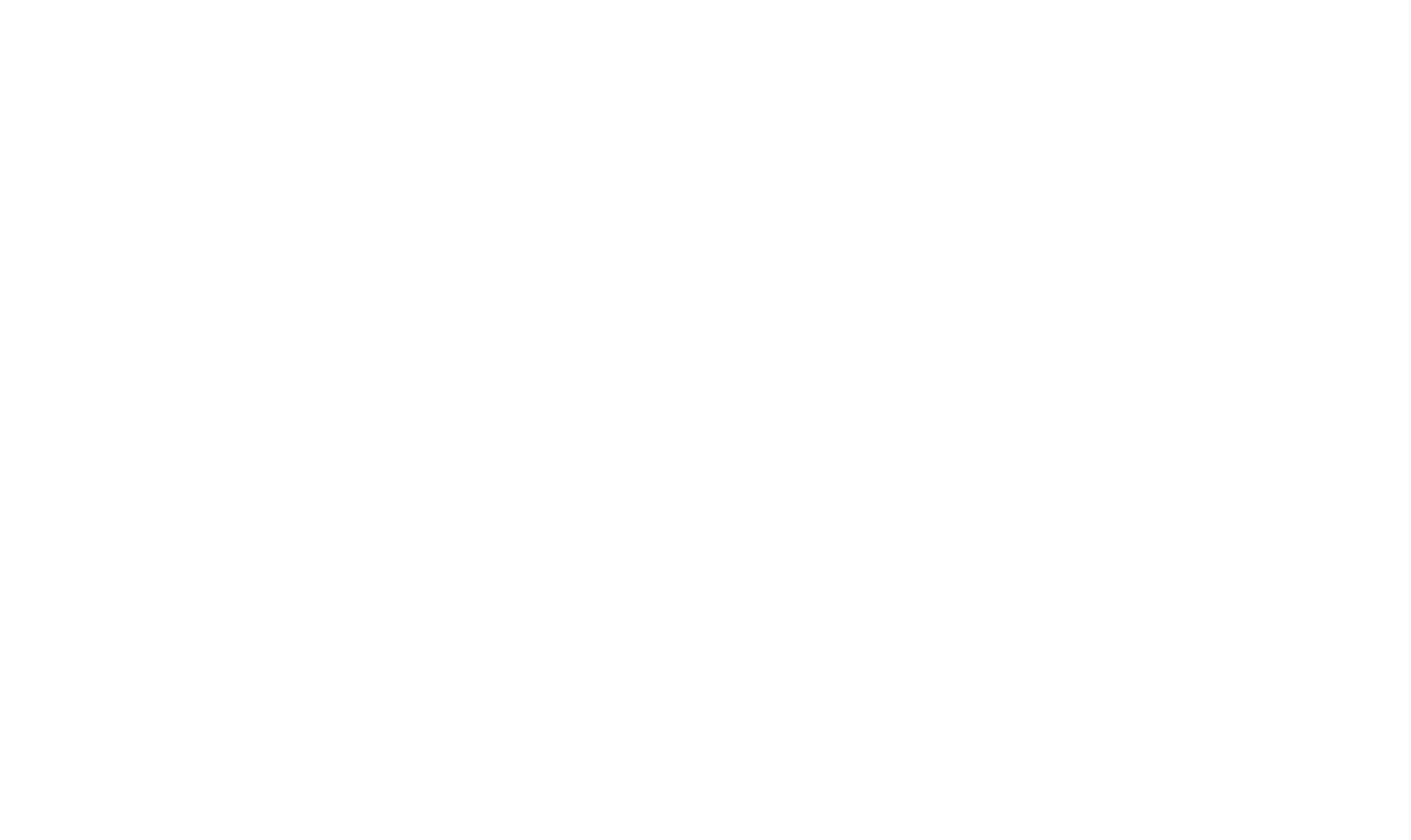
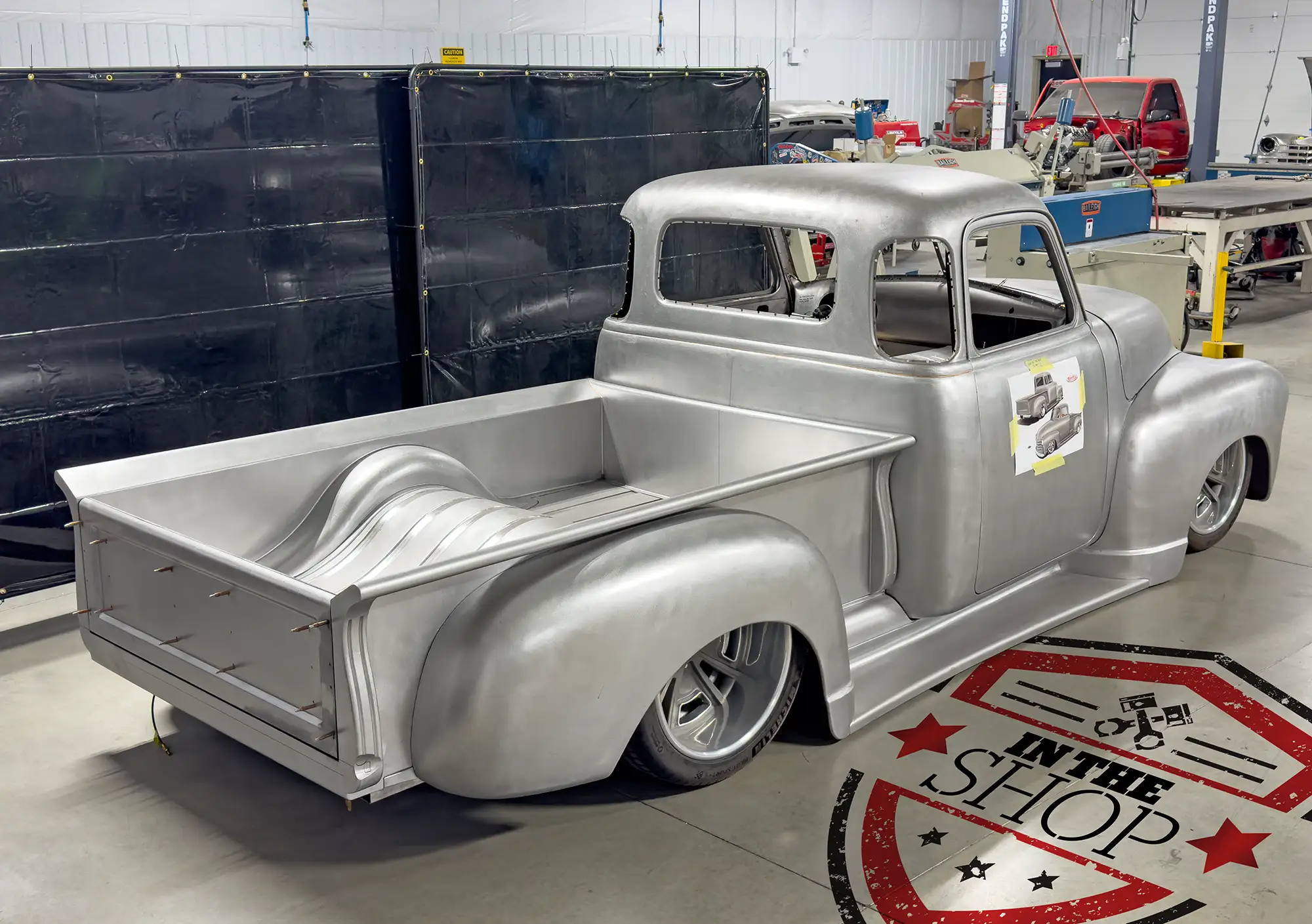
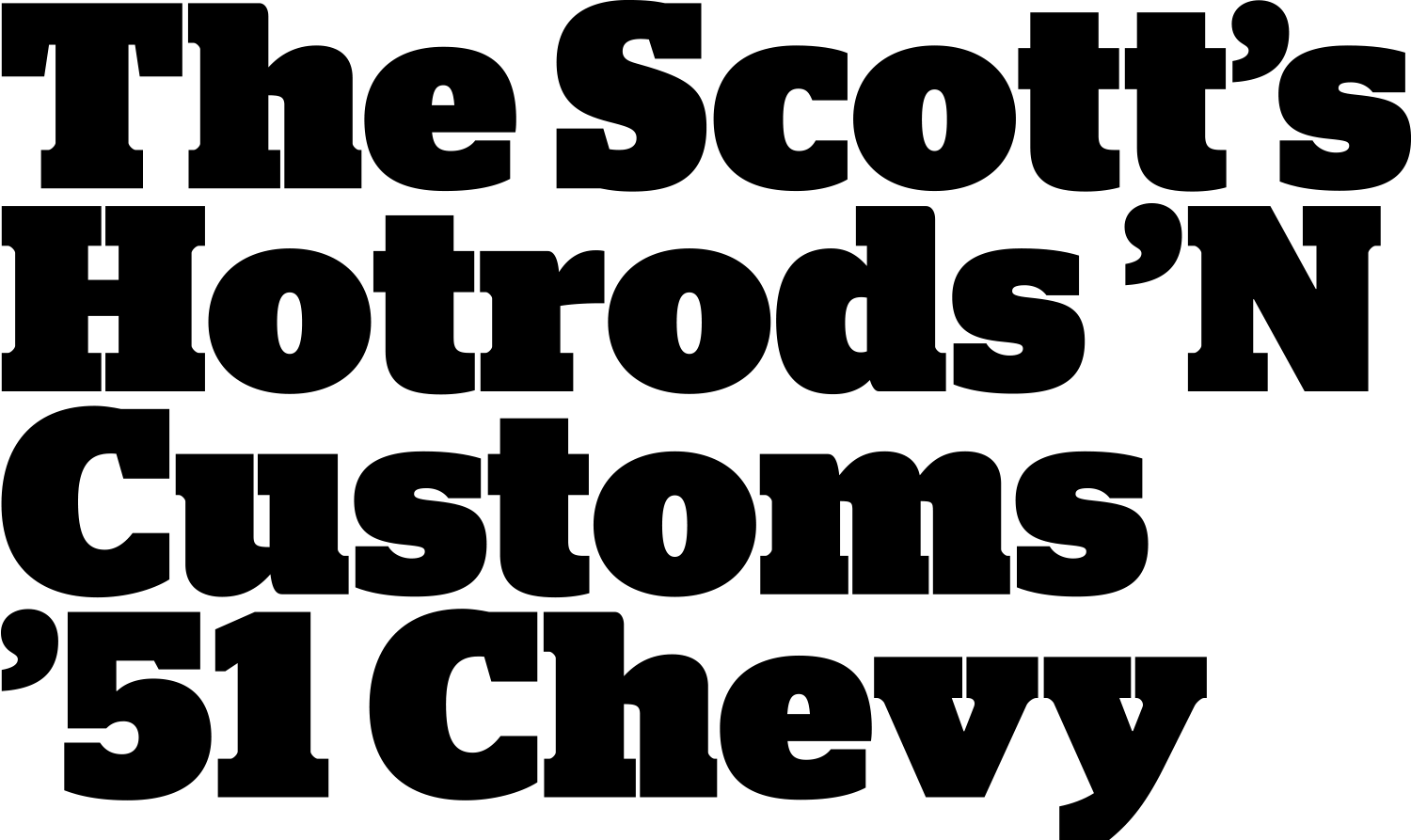
Images BY Camren Beatty
ailgate time! Let’s go back a bit and talk about the fabwork on the tailgate for Scott’s Hotrods ’N Customs’ Brian Schutte’s truck.
When we initially got around to making the tailgate, there wasn’t much that had been planned for. Ultimately, we just knew we needed a tailgate. I had the idea of trying to somehow incorporate a soft-open feature like newer model trucks have today and Justin Padfield was on board with the idea, so we did a little research and decided to call up one of the local GM dealerships and get our hands on the entire tailgate hinge assembly for an ’18 Silverado. These trucks use a torsion rod in the bottom of the tailgate that connects both hinges and applies resistance the more you open the tailgate. To keep the torsion rod from acting like a spring, a damper is put at one end, making the force on the torsion rod much more even, providing the “soft” opening motion. So, after getting all the parts and figuring out how they work, that determined to some extent how the hinge assembly and bottom of the tailgate would be built.
Planning ahead a little bit, I knew a smooth tailgate wouldn’t look right on this truck, but I didn’t want to do something so uniquely custom (like some sort of feature/design on the Pullmax or bead roller) that it would seem out of place either. So, I decided on a very simple step down for a nice, clean look. With that now planned, I started mocking up where the top and bottom tubes for the tailgate structure would be, and with Ian Kinzler’s help, we designed and cut center structure bars to be welded up. During this time, I had to notch the bottom tube in a few locations and add guides in the tube to hold the torsion rod in place. (We had to cut about 16 inches off the torsion rod because modern tailgates are longer.)
With the tailgate structure now built, I could locate the driver side hinge and finalize both the hinge pocket and torsion rod pocket on that side and begin planning out how to modify the passenger side hinge. This hinge took heavy modifications to both fit in the cramped space I had to locate it in but also provide an easy and effective way to remove the tailgate and longevity through hundreds, if not thousands, of opening/closing cycles. At this time too, I was building the rear roll pan, which both hinges and rear bed mounts were connected to. Once I had both hinges functioning and tacked into place on the truck I started making the exterior tailgate skin. I knew I wanted to still have a radiused top edge, but I opted to make the outer bottom corner square so that I could have a nice, clean 3/16-inch gap along the bed/roll pan all the way around. I made the majority of the skin in one piece on our mag brake with some careful math, then made the outside edges separately and welded them on to complete the skin (notice the step that I had mentioned previously when planning out the structure).
With the outside skin finished, I was able to build the outside of the roll pan and tie everything together with consistent 3/16-inch gaps. The inner channel that the tailgate sits into is built on a slight angle, and I welded a stainless drain tube straight through the roll pan to allow for easy watershed. Once the outside façade was complete, I started working on the tailgate endcaps that house the modern tailgate latches (also from an ’18 Silverado). This was probably one of the most challenging parts since the latches were nearly the width of the tailgate, even after modifying them to make them fit. After making both of the endcaps and having the latches complete, I was able to locate the strikers and flush those into the bedsides. During this time, I still had the outer bedside skins as removable, so I was able to pull those off and reinforce the striker area so there would be no deflection or eventual weakening in the surrounding sheetmetal over time. With this latch assembly, shutting the tailgate is now a two-finger job, instead of having to slam it shut or use any sort of cable system to hold it open/closed. (When I was modifying the passenger side hinge, I added a 3/8-inch solid steel dowel inside to stop it from opening past 90 degrees.)
Fast-forward a longtime later, after fully welding the bed together, I finalized the tailgate endcaps and made the inside skin. I also added two 6-pound slugs into the top tube of the tailgate structure for pivot weight to aid in overcoming the force of the torsion rod. At this time, the tailgate still isn’t finished, but is fully functional. We still haven’t planned much on what we intend to do with the tailgate handle, but it’ll be a nice custom piece, likely designed and machined in-house. Before both skins get welded on, it’ll be insulated with Boom Mat just like the bed is and will weigh somewhere in the neighborhood of 65-70 pounds when fully finished, which I don’t think is all that crazy considering a new tailgate weighs anywhere from 90-110 pounds.
It was a very fun and interesting project to tackle. I’ve never built a tailgate before, let alone one entirely from scratch. I really enjoy the challenge of retrofitting modern parts into projects like this. It requires a lot of planning, as well as trial and error, to get everything functioning properly.




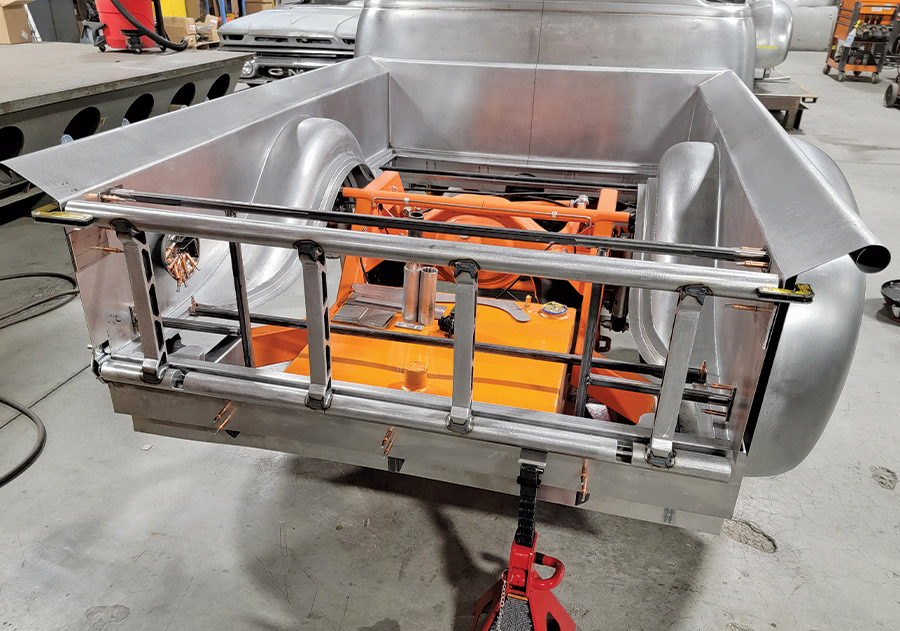

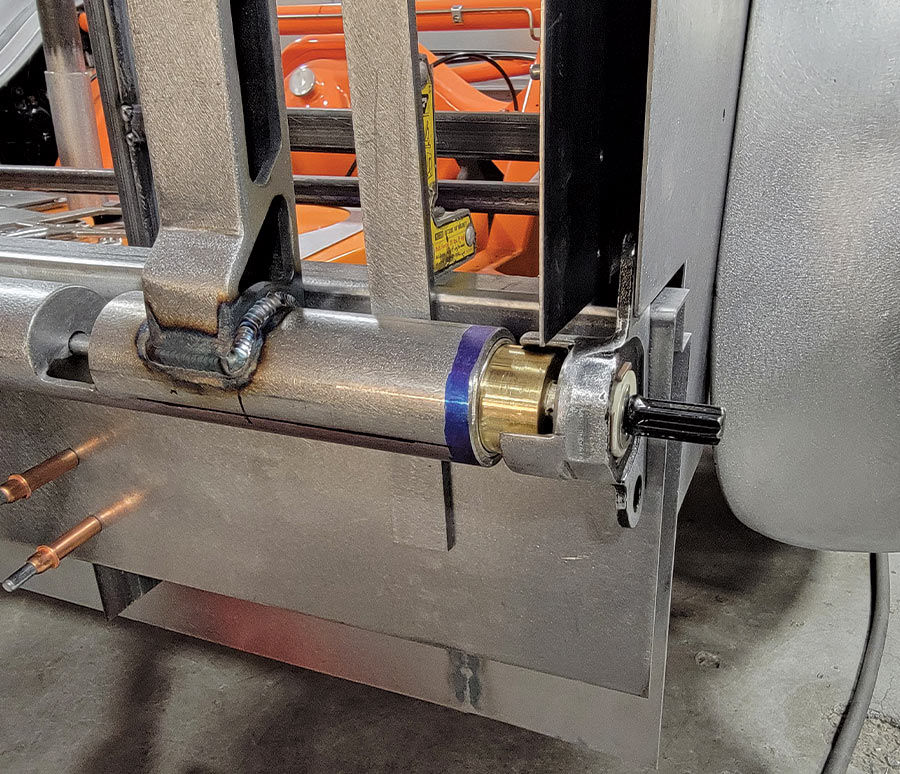





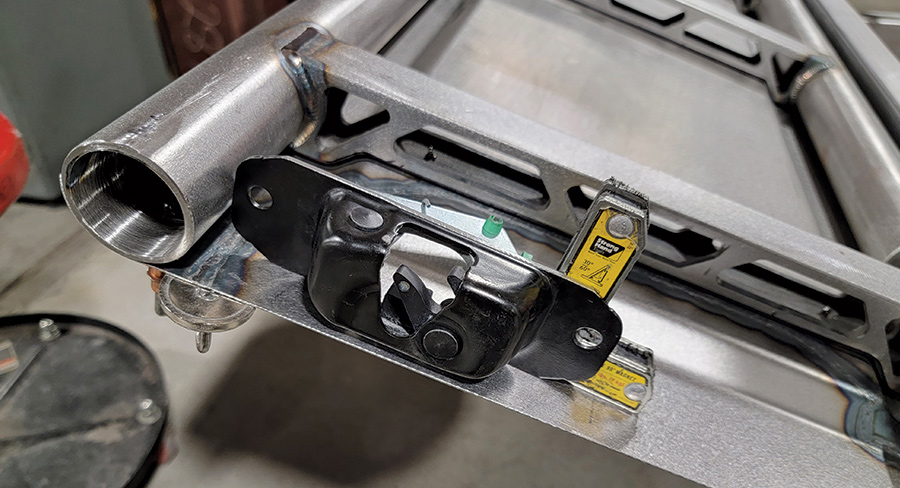
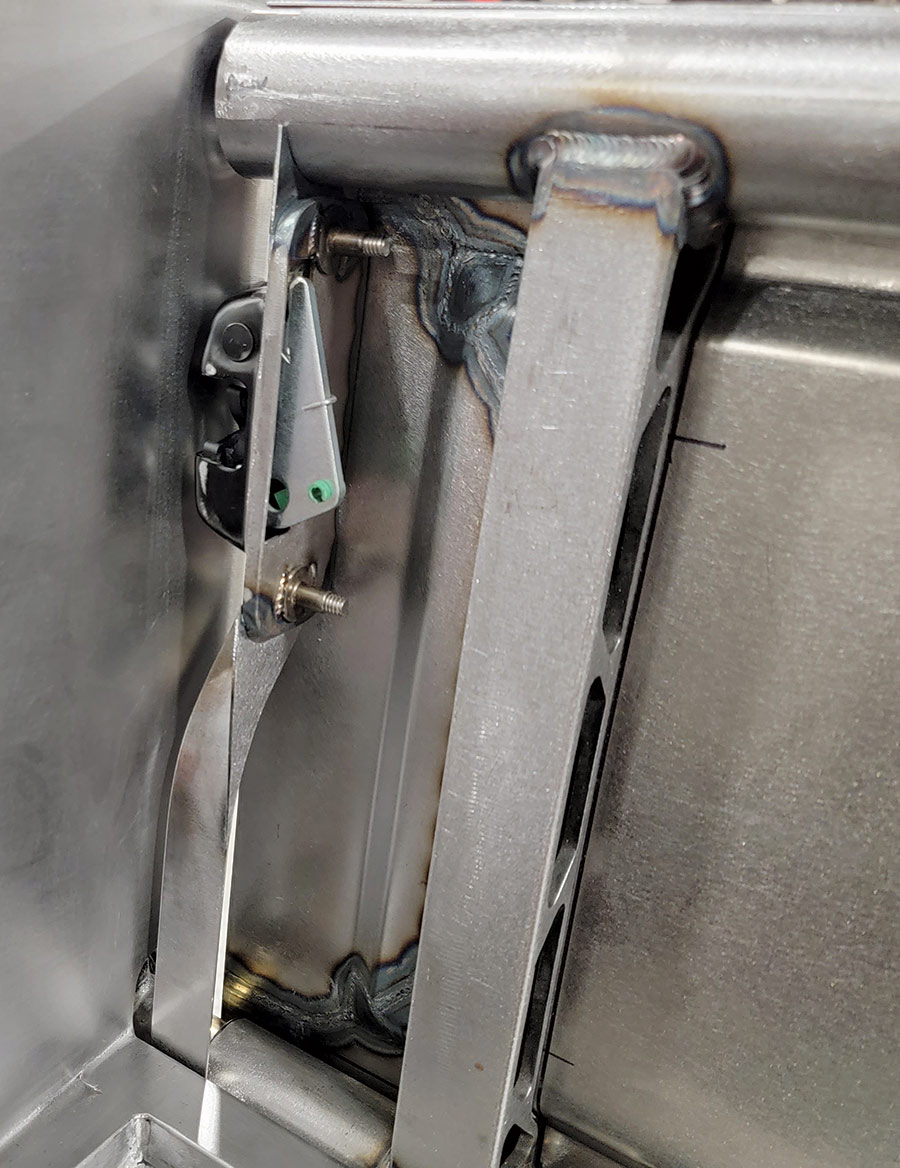
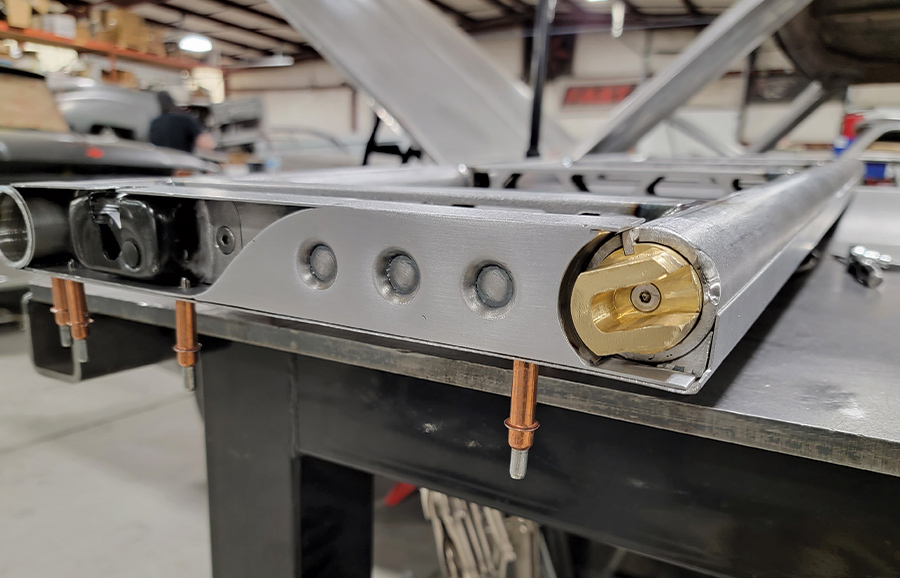

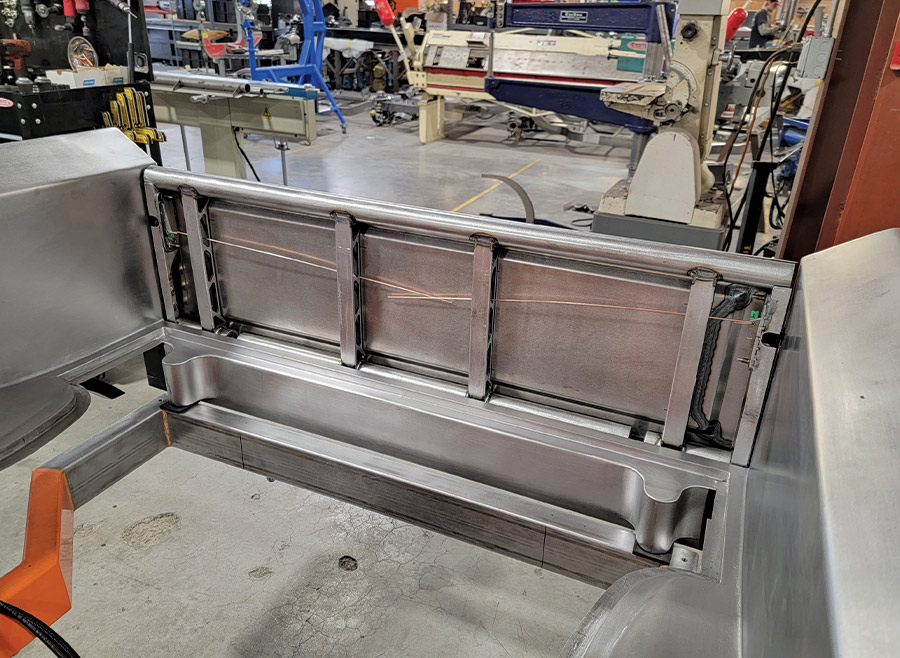
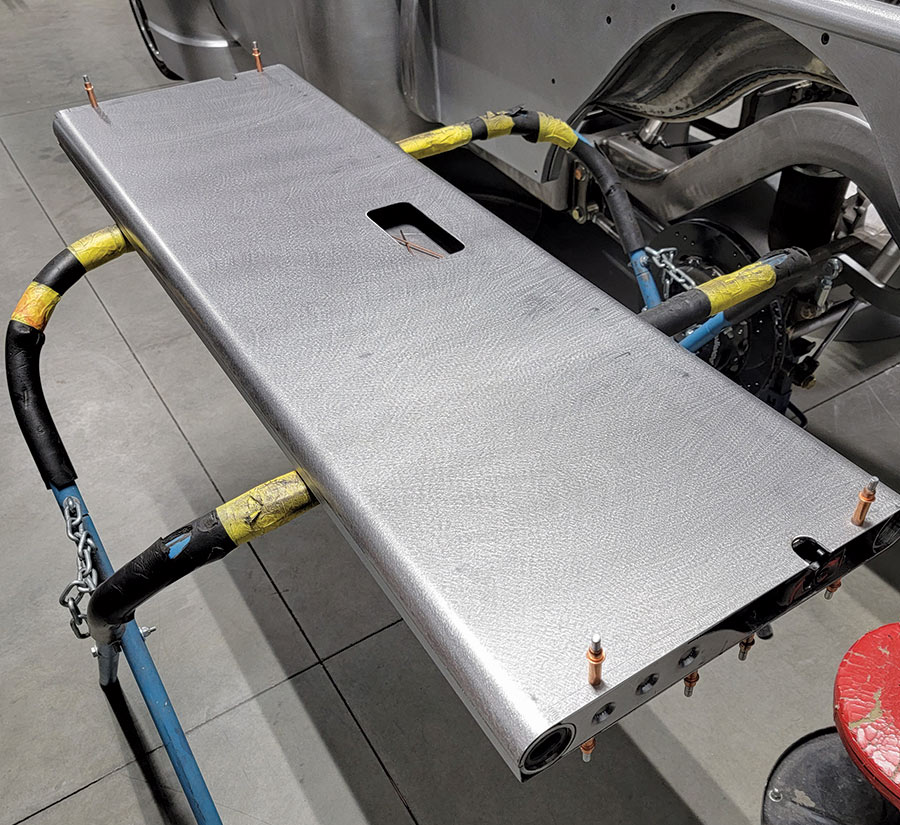
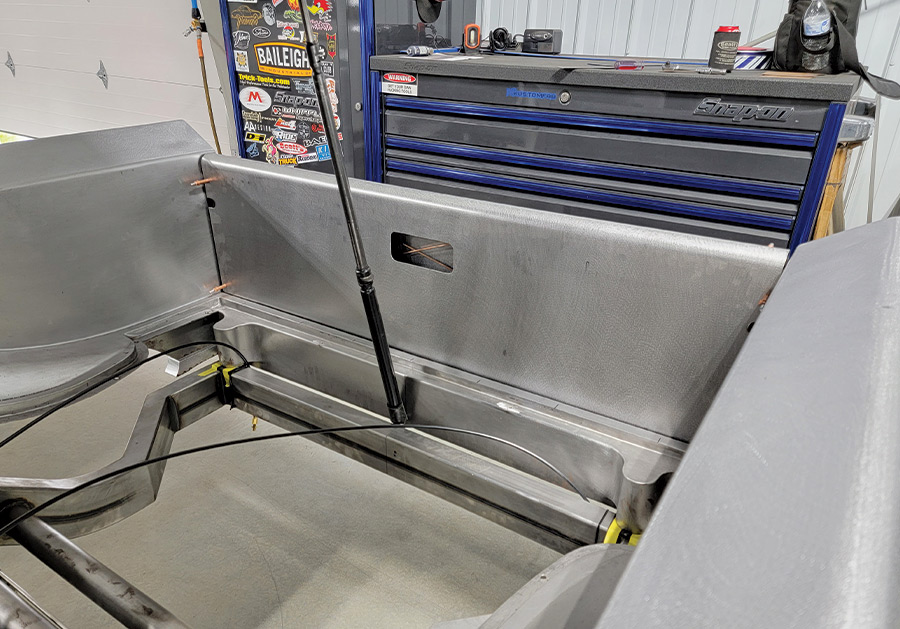
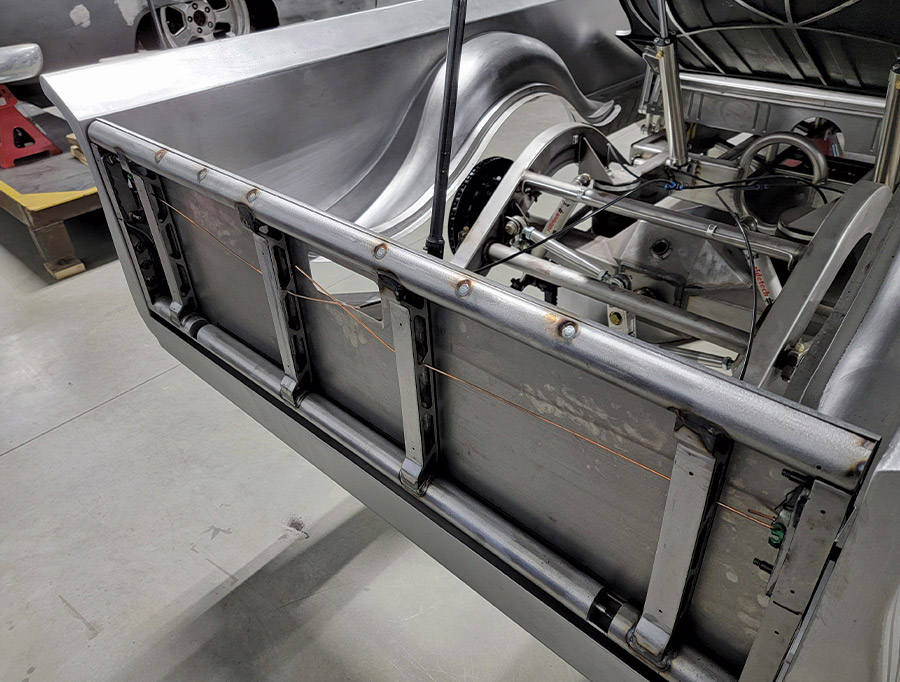
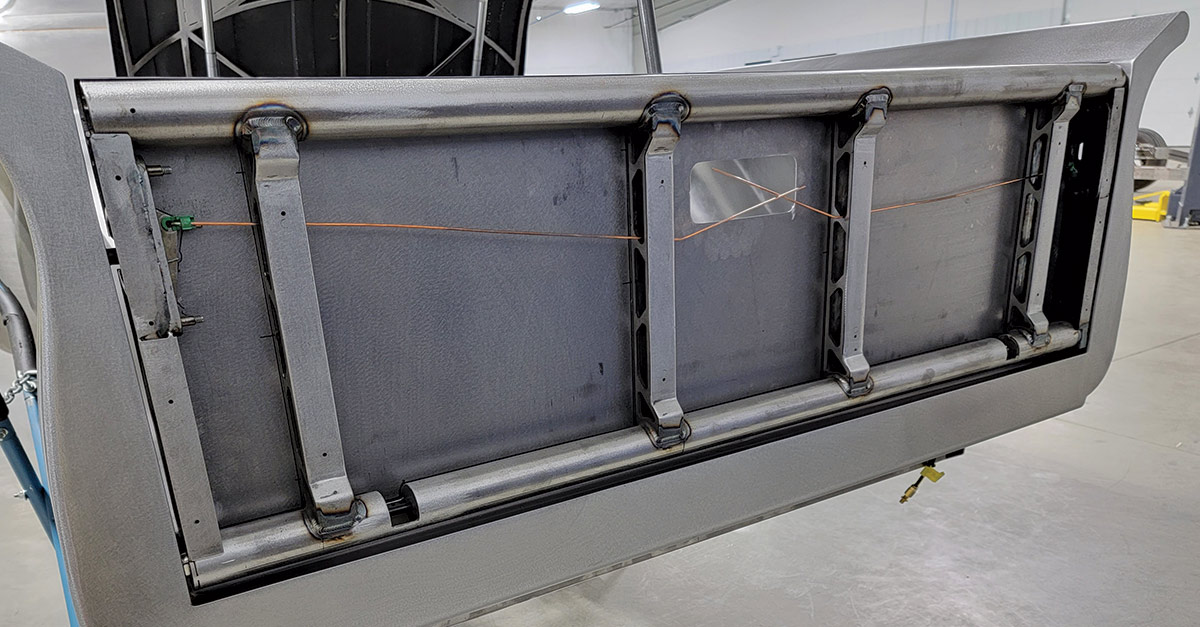



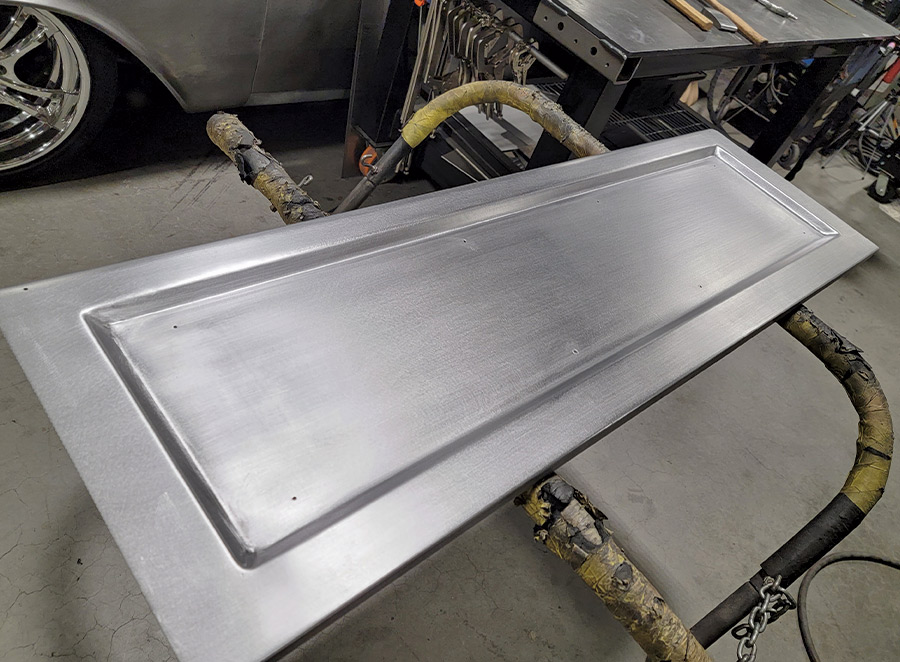



