IN THE SHOP
InTheGarageMedia.com


ou know the saying (even though some now want to ban it from our language) “there’s more than one way to skin a cat”? Well, no offense, but there’s also more than one way to flush-fit the windshield on a ’67-72 Chevy/GMC C10! Obviously, there’s the direct-to-consumer method of obtaining precut glass from someone like AM Hot Rod Glass or Fesler and having it professionally glued in (or attempt the install yourself, if so inclined). The fellas at Scott’s Hotrods ’N Customs, on the other hand, have a different method. To explain their intricate process, we gave installer Shawn Holloway the mic … er, paper?! Take it away, Holloway:
“We wanted to be able to use a factory C10 windshield for this flush glass process instead of an oversized replacement ‘flush-style’ glass. The factory glass is easily replaceable and will seal correctly with the quality glass that we accurately fit.
“I began by making the top pieces that match the same shape as the exterior of the cab above the windshield. Next, I made 90-degree flanges the length of the A-pillars. Using a factory windshield (removed from the truck), I matched the shape of the side of the glass by shrinking the flange that the window will sit on. We knew we wanted a 1/8-inch gap all the way around the outside of the windshield, so I used 1/8-inch spacers while fitting the new flange to the existing A-pillars. We make our flush glass flange depth 3/4 inch to allow for the width of the windshield and urethane that will hold it in later. Bending a 1 1/2-inch strap at 90 degrees makes for a perfect 3/4-inch depth and a 3/4-inch flange for the window to rest on, while also being a short enough depth to easily shrink and stretch.
“After fitting the 90 flange to the factory window with the correct spacers I corner-welded the flange to the pieces that I had previously made fit the exterior of the body, essentially making a Z-shaped flange. Using Cleco fasteners I attached the sections of flanges to the body with the window in its correct level position so that I could ensure the look, fit, and gaps—also, to move anything around before marking out the existing window surround with lay-out fluid and scribing a cut line. Once I had both A-pillar pieces and both of the two upper roof sections fit to the window I connected them in the upper corners. Finishing out the corners and leaving them separated in the top middle allowed me to have access to hammer, dolly, and grind the areas that will be harder to get to once on the vehicle.
“Next up, I cut my scribe lines and removed the spot welds along the old windshield frame one side at a time. While this area is exposed (for hopefully the first and last time ever), I went ahead and prepped and painted all the areas possible along with the back sides of all the flanges before encapsulating them permanently. Once the new flange is fit flush to the body and pillars I tacked it in place (repeating the same steps on the other side of the truck so that all the new pillar and upper flanges are tacked in place). We place the factory windshield back in its new window surround to make any adjustments needed and to ensure the overall look is as desired.
“Once I knew everything fit up perfectly it was time to weld about 8 feet of 18-gauge flanges onto the face of this ’67 C10. This-year truck has a fully welded interior headliner/inner roof pane, making the access to the back sides of all the welds almost non-existent. Knowing this I knew that it was very important to keep the weld small and as low heat as possible to attempt as little warping as possible. The A-pillars being radiused and having some shape to them made them much easier to weld on without much distortion compared to the top middle sections. I welded, ground, and sanded both pillars before fully welding the top sections so that I would have one long, continuous weld along the top from corner to corner rather that going up one side and down the other. Once figuring out that I could slip a skinny dolly between the new flange and the old inner roof structure I was able to plannish out the weld along the top.
“Since we installed our window frame and window level we knew that we could hold the window (with spacers) up against the top and sides to be able to make the lower pieces fit the contour of the glass. Making both of the lower window flanges involved a lot of shrinking and stretching to make it fit perfectly to the curve and the bow of the windshield. While making the exterior piece that will be flush and meet up the cowl, I decided to make them extra long so that I could get rid of the dip where the fender used to transition to the cowl. The A-pillars typically dive under the fender where there used to be a factory seam in the window channel. Since I had to replace the area anyway, I figured that a nice sweeping body line across the truck between the cowl and window frame would look better than the dips that no longer had a purpose.
“Next, I welded in both lower corners and boxed in the underside that meets up with the cowl. Making the bottom middle flange was the easiest part, one last simple 90-degree flange lining up the bottom of the window. After metal finishing and DA sanding everything down the last thing to do to complete this area was to modify the back edge of the cowl on each corner to match up to the new body line. This was my first time doing a flush windshield. There are a few things that I would do slightly different (like making access to the roofskin to be able to hand plannish easier), but overall, I’m very happy with the outcome and I personally think it looks sick—but I’m biased!”
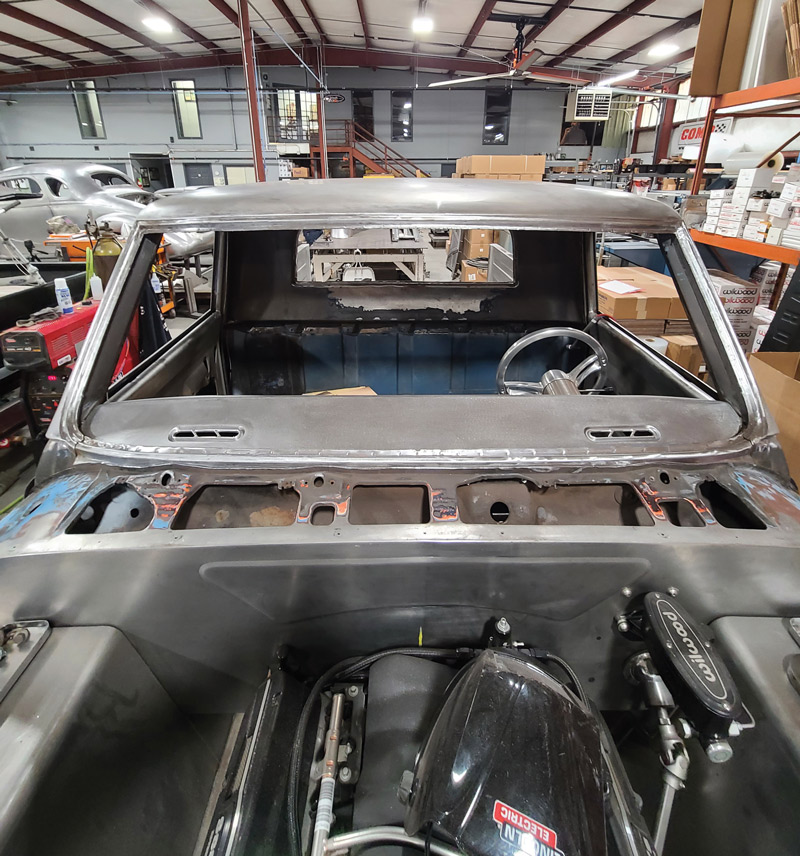

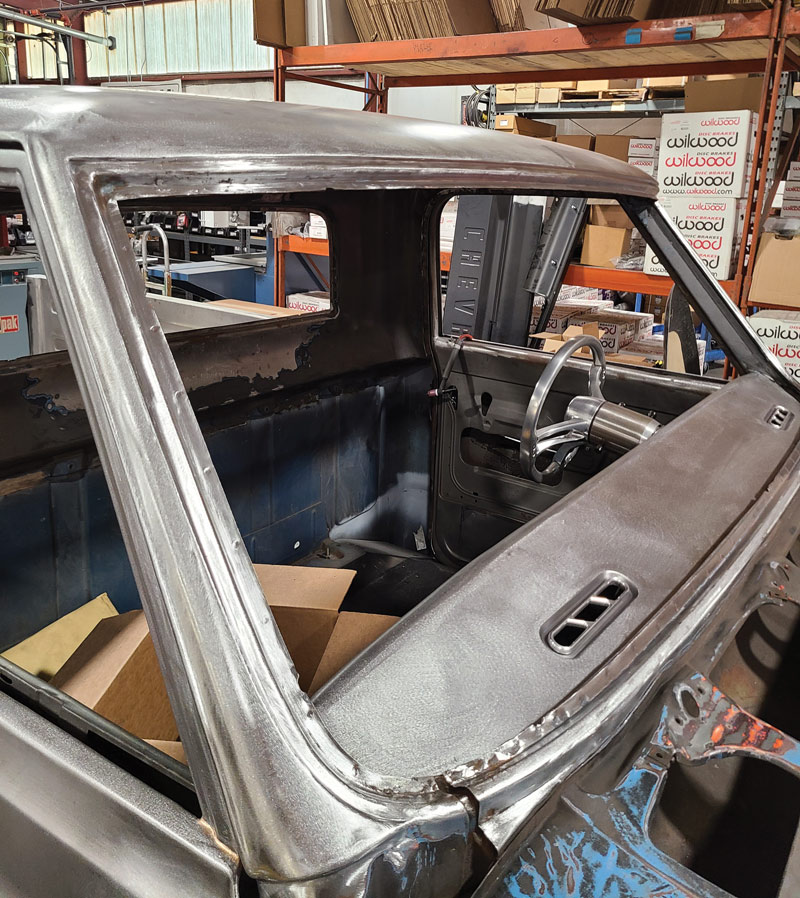
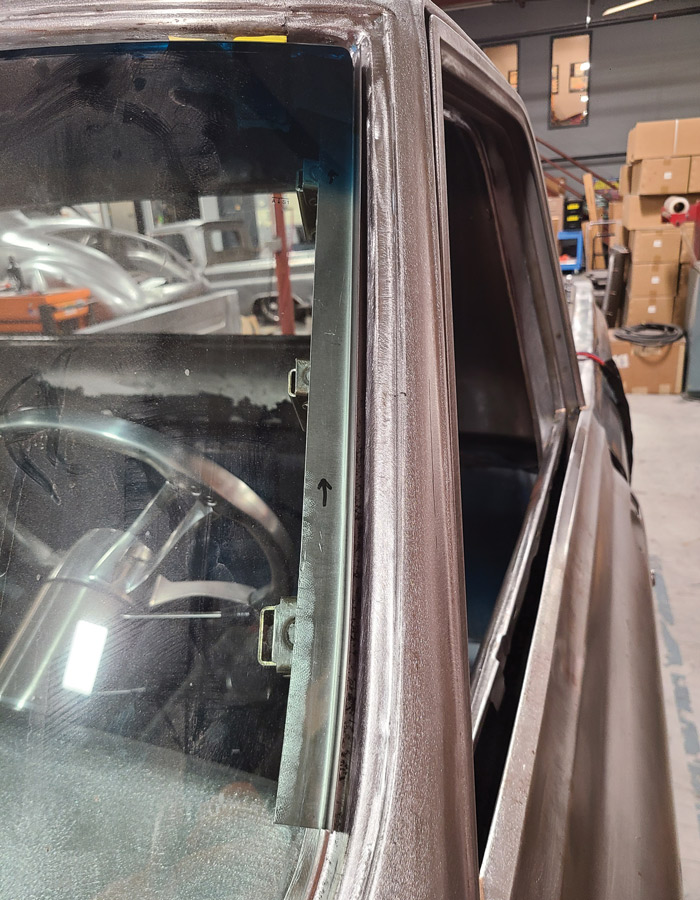
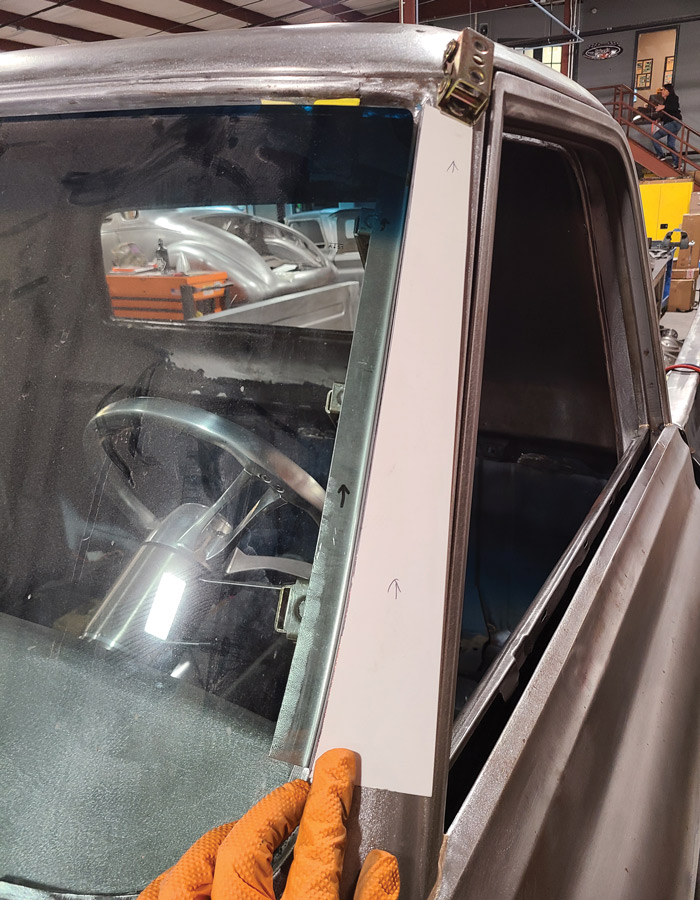
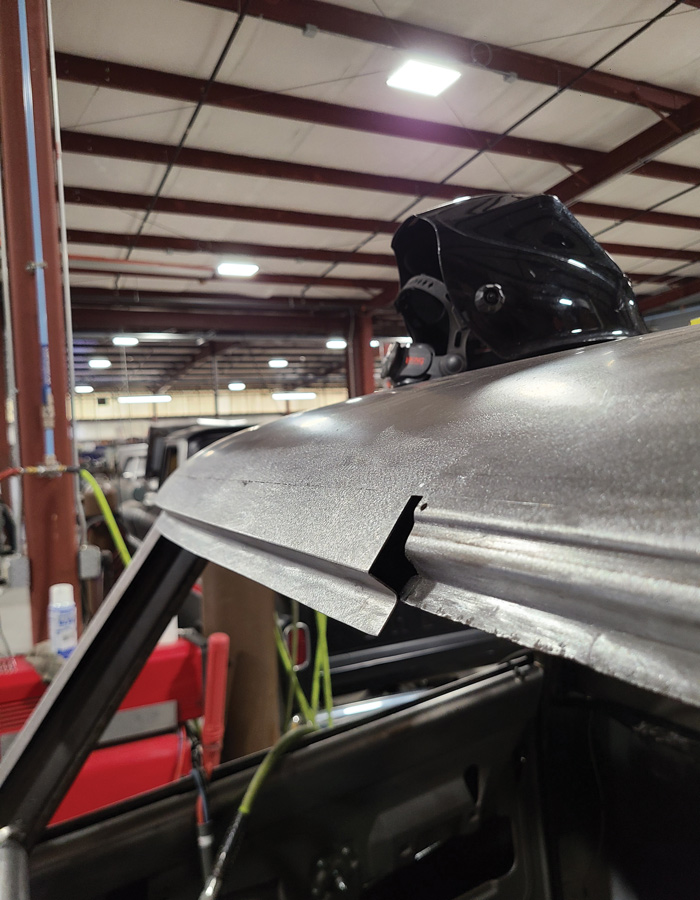
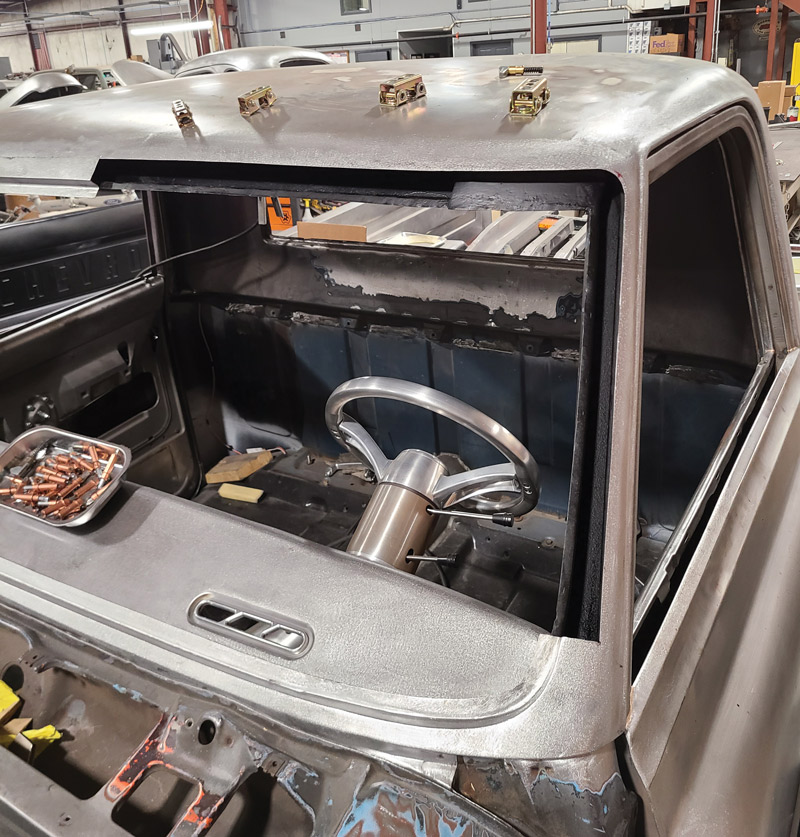

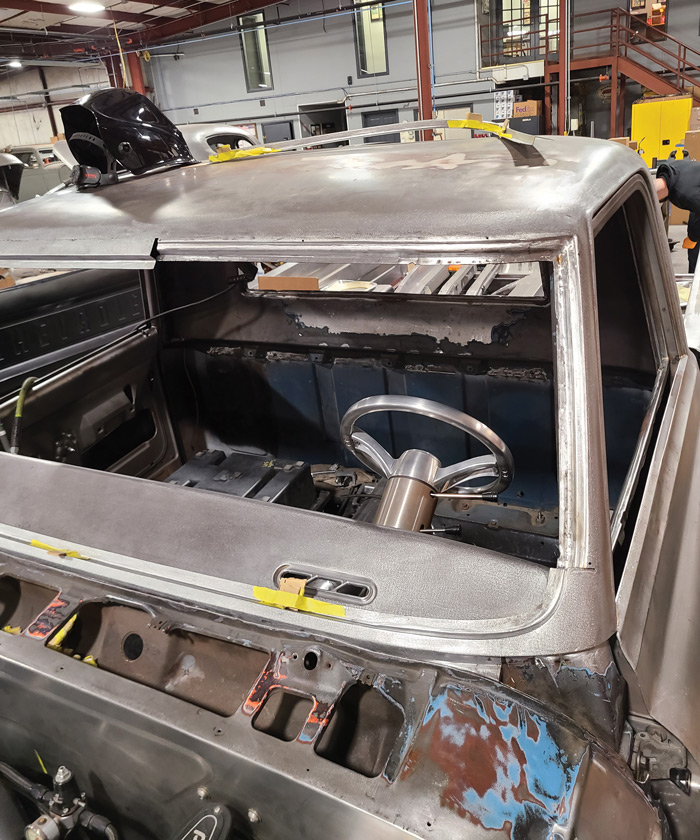



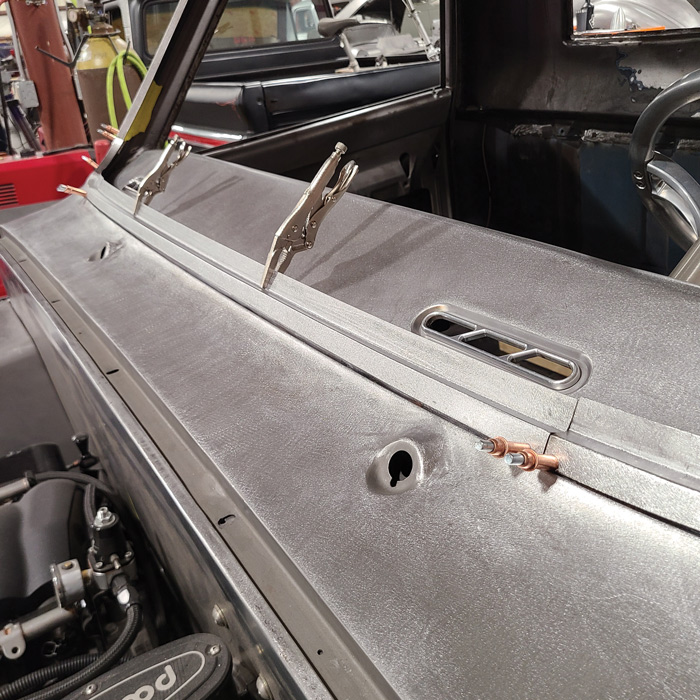

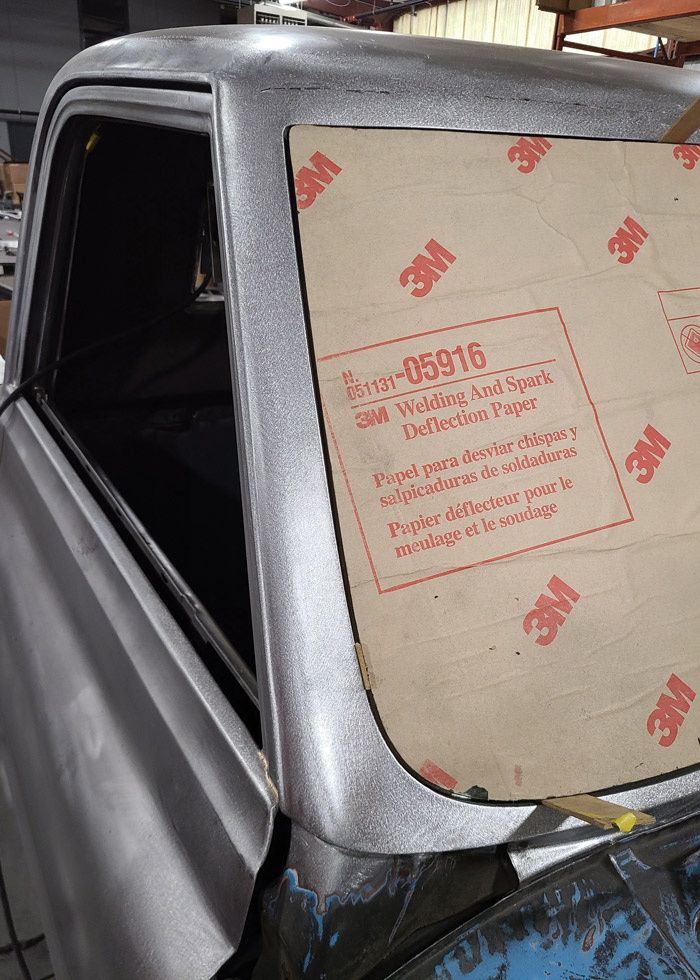
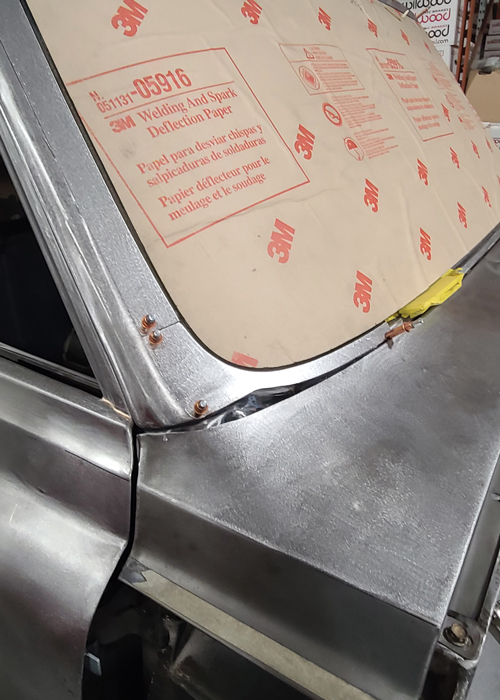
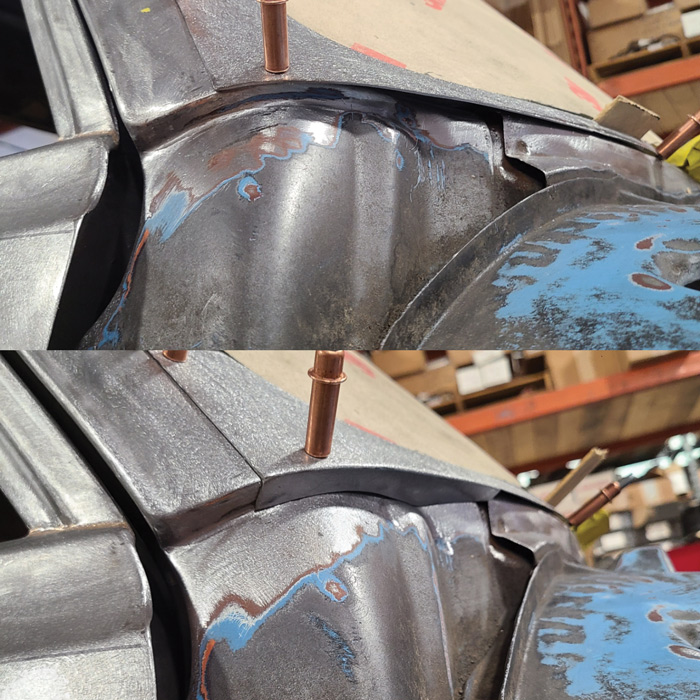


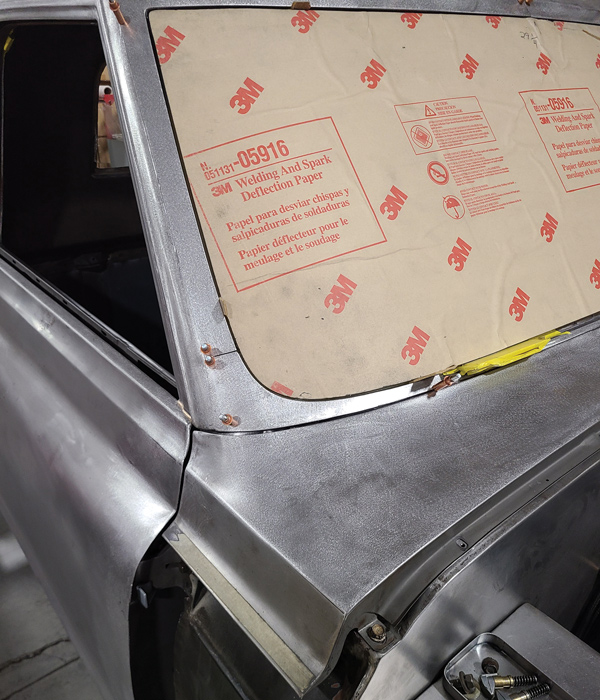
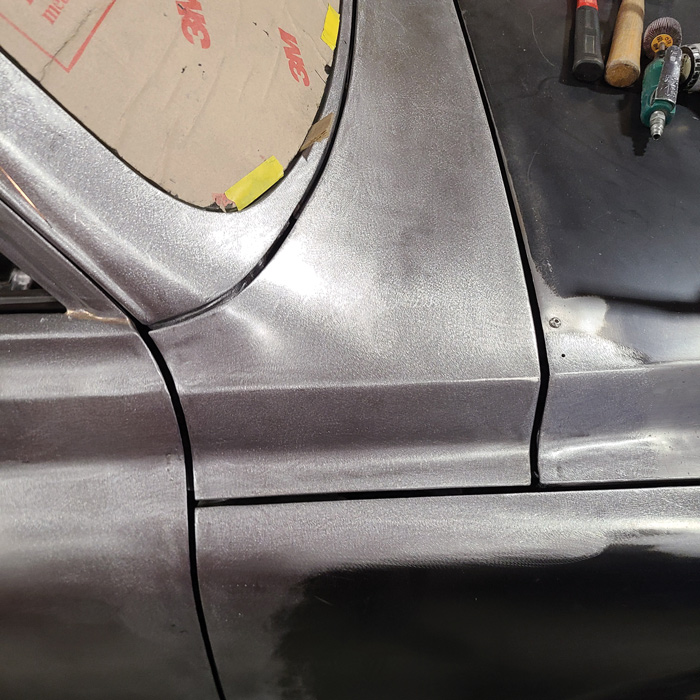

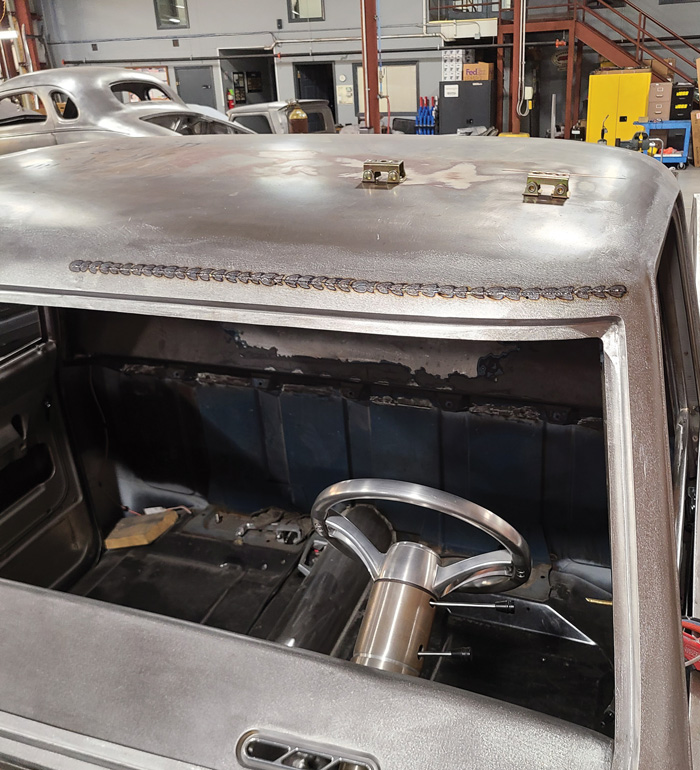
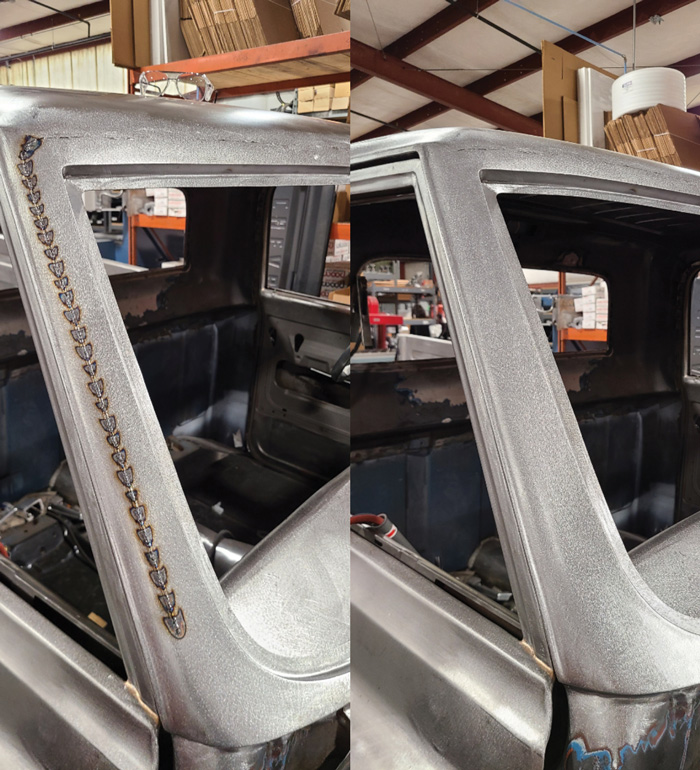
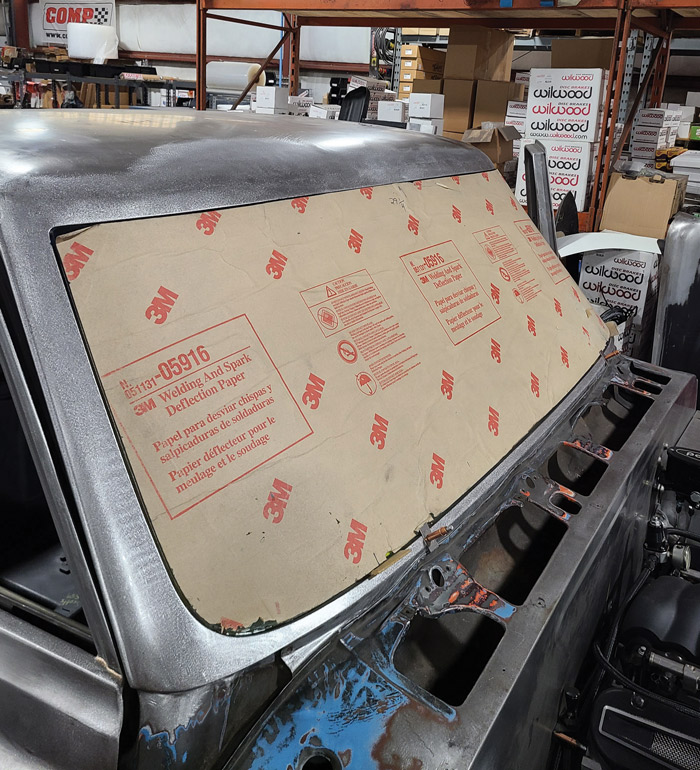
