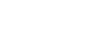

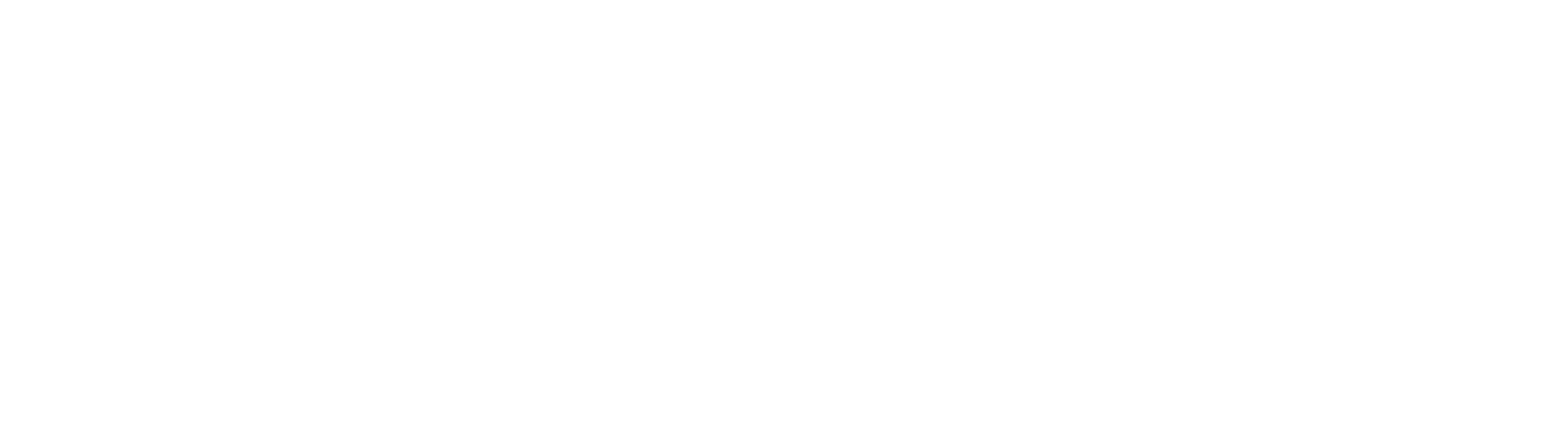

ne of the greatest aspects of the classic truck hobby is the act of completely un-utilizing the characteristics of the trucks we drive! Whether it’s massacring the suspension or, as a result of that, obliterating the bed floor beyond the point of usability, we’re professionals at ruining old trucks, aren’t we?!
All kidding aside (for the most part), the more we lower our trucks, the more we have to deal with collateral damage, as it were—be it removing/severely modifying the inner front wheelhouses or, in this case, adapting a Fleetside bed floor and inner bedside panels to a recently installed, airbagged rear frame section with a huge kick-up/notch. The latter scenario is something we recently encountered at Jimenez Bros., and as it would turn out, I was able to do more than just observe.
Early last year, a customer brought his Silverado in for a Rydman Ranch rear notch install. At the time, the bed had already been completely modified (elevated bed floor, widened/sectioned wheeltubs, and so on) for a similar suspension job, so it was assumed the “molded” box would bolt back on with minor adjustments. Well … you know what they say about assuming.
Upon attempting to reunite said bed with said back-halfed C10, it was discovered that not only was there no way the bed was going to fit without major surgery, the manner in which the previous work had been done was, well, let’s just say “hack job” would be an extremely polite way of putting it. All toll, the existing bed was junk, and the amount of time and labor to rectify that would be insurmountable, to say the least.
Here’s where I come in. Ironically enough, my pals at Auto Metal Direct (AMD) had just released their all-new 4-inch-wider wheeltubs and an accommodating bed floor for the ’73-78 GM shorties—and I’d just run a release on it, so it was rather fresh in the memory banks. Of course I suggested scrapping the efforts on the stock bed and, along with AMD’s new Squarebody Fleetside bedsides and front panel, build a bed the better way. Jimenez Bros. agreed, and the rest is this story!
The first order of business once the new sheetmetal had arrived was to build the outer box and square it up on the Silverado’s modified chassis in relation to the (body-dropped) cab. Though not easy by definition, with all things considered that was the easy part; plotting and locating the raised bed floor and then surgically fitting the widened wheeltubs took a bit more mental—and physical—time to accomplish. But as the accompanying photos should help attest to, it was a task Jimenez Bros. was able to achieve, save for the custom rear panel!

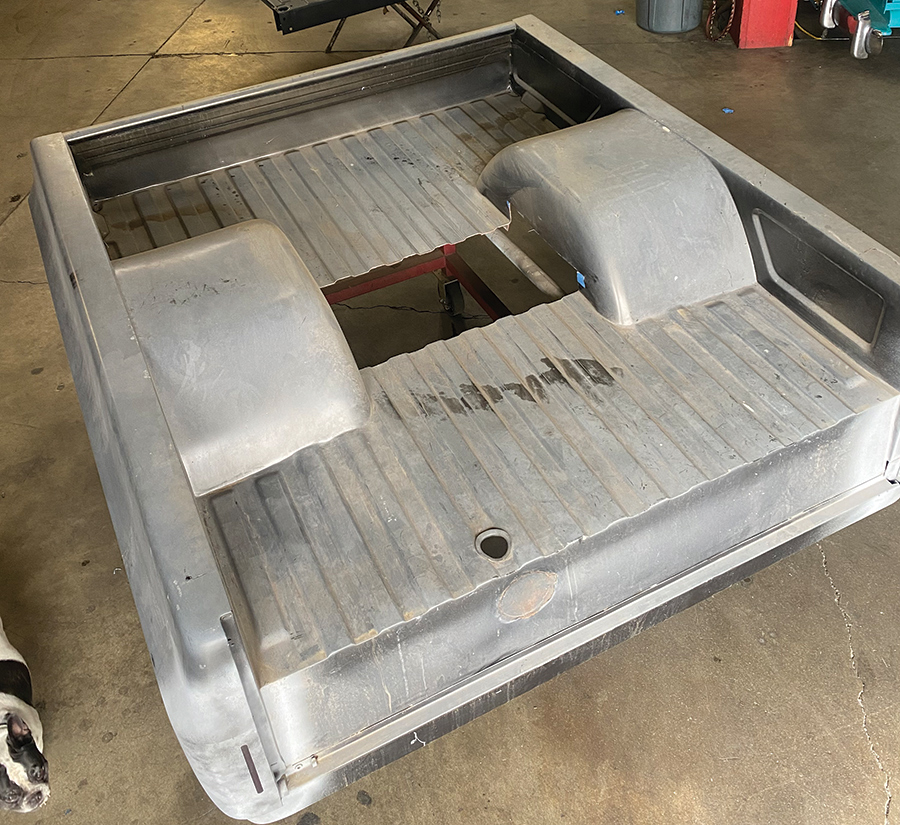

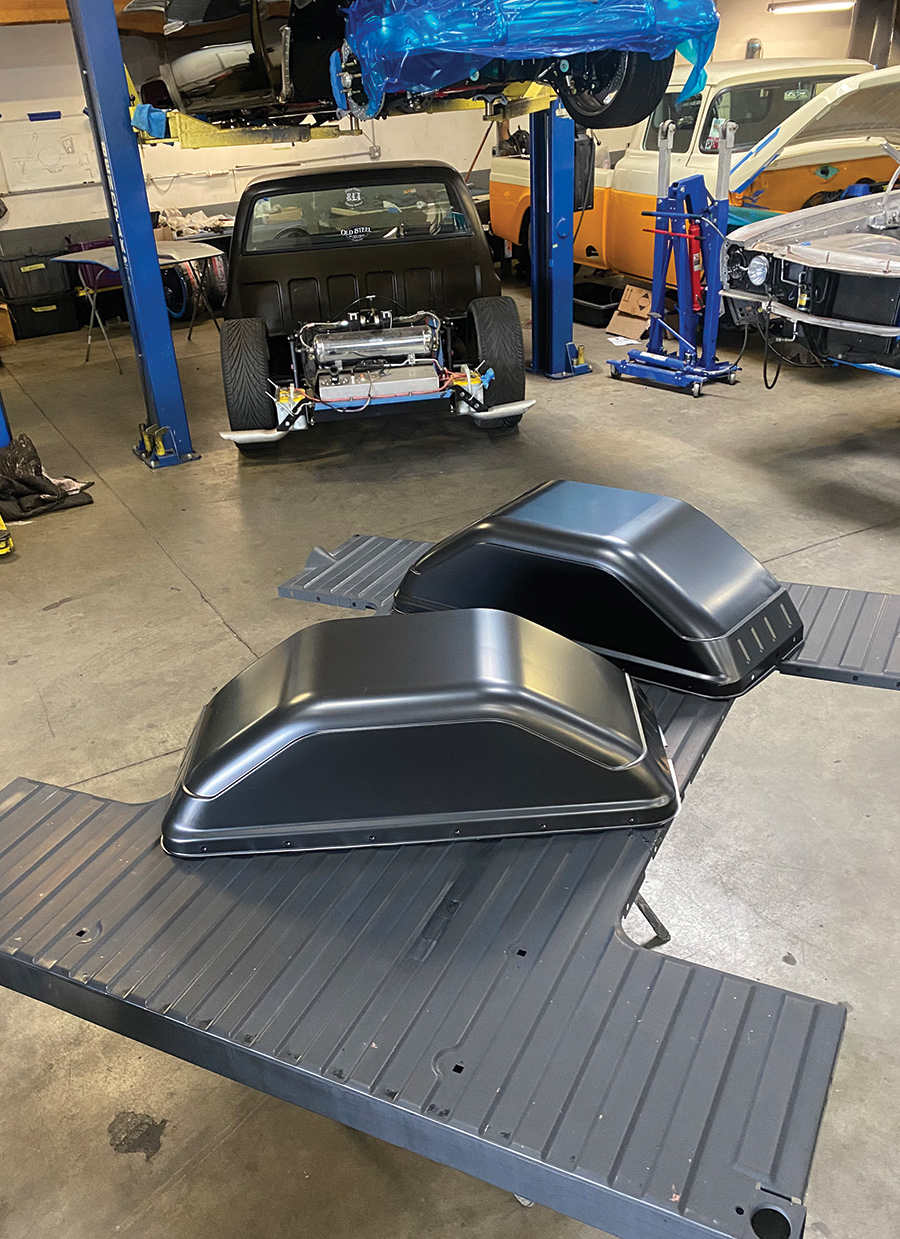
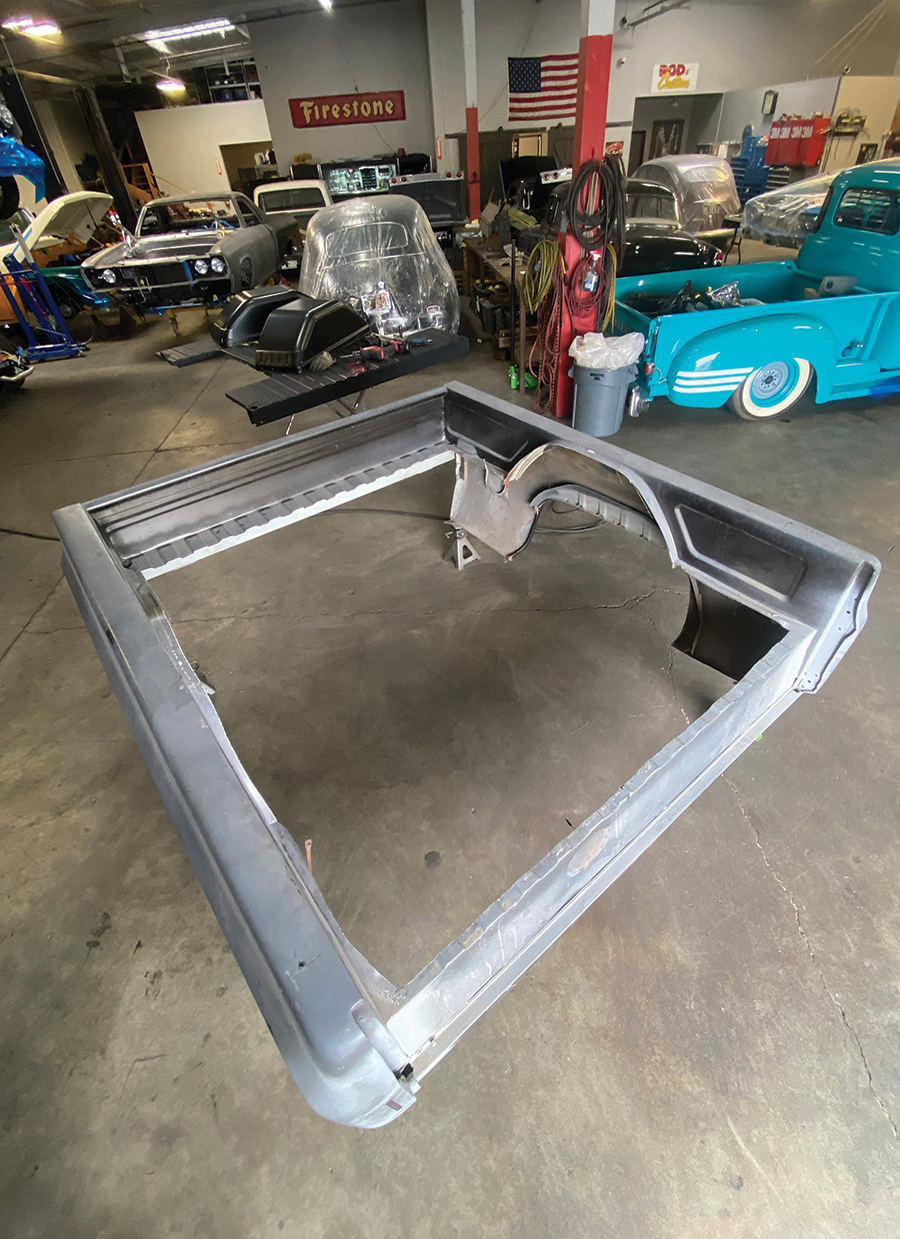
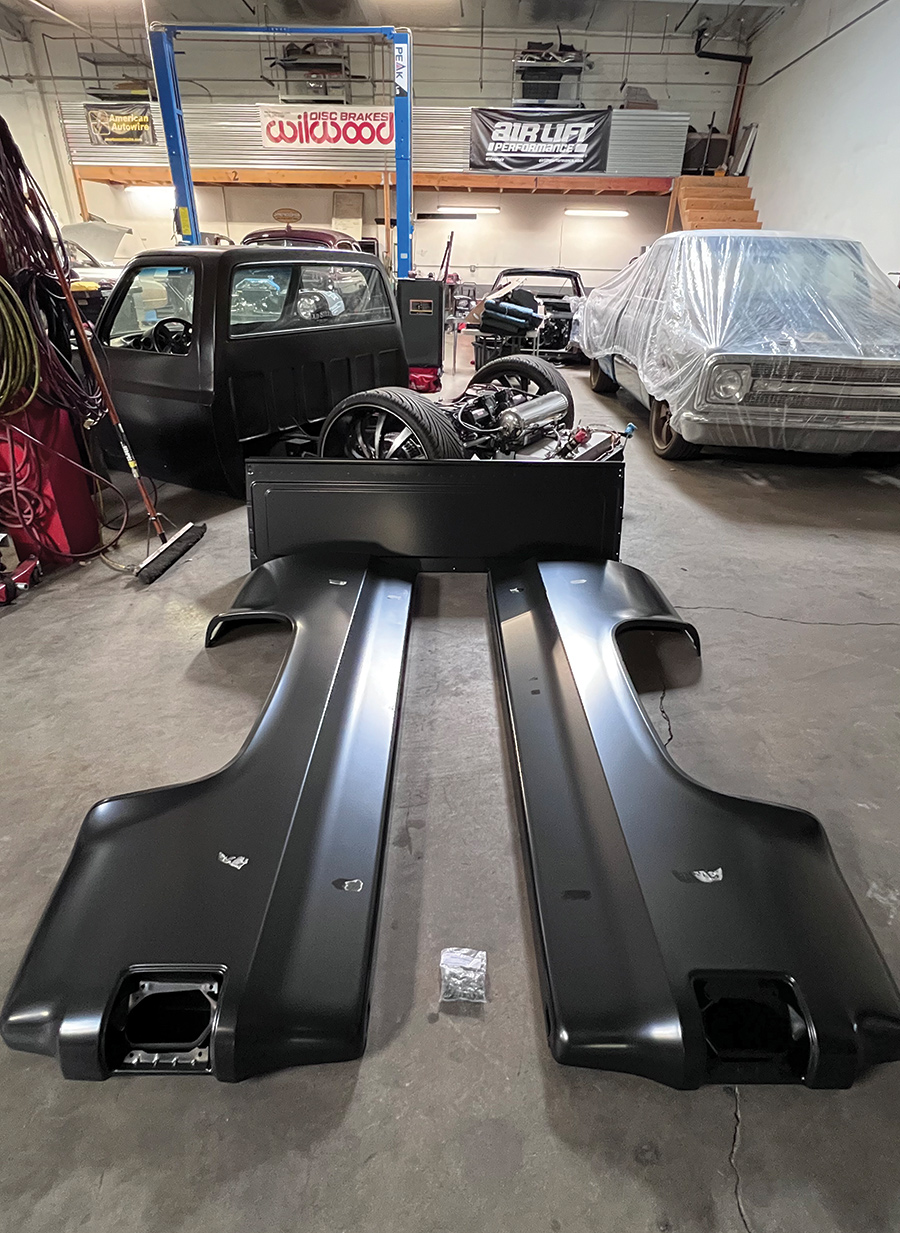








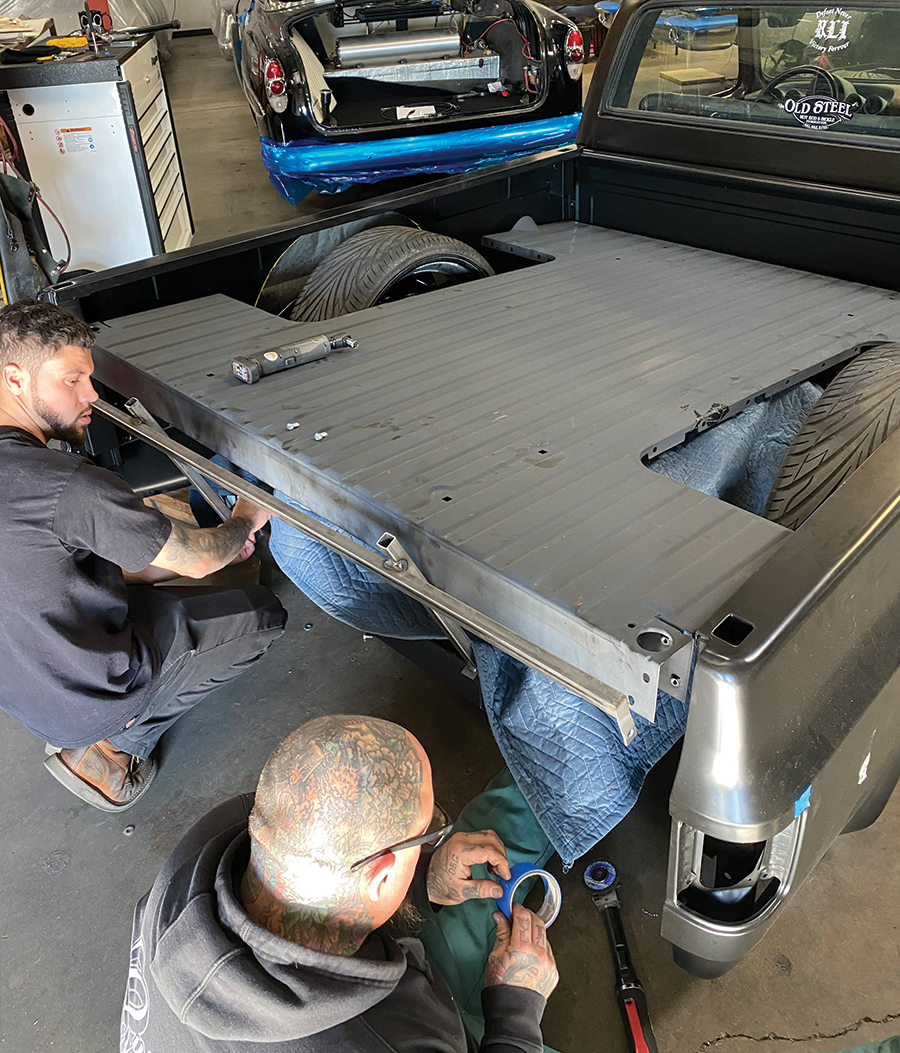






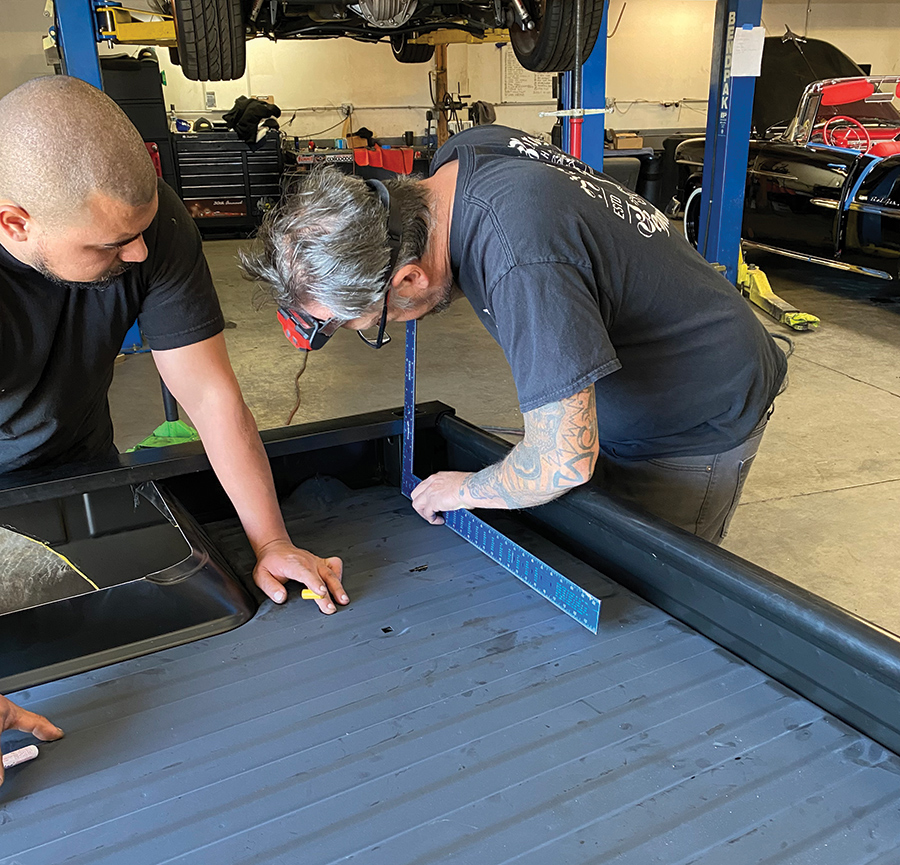



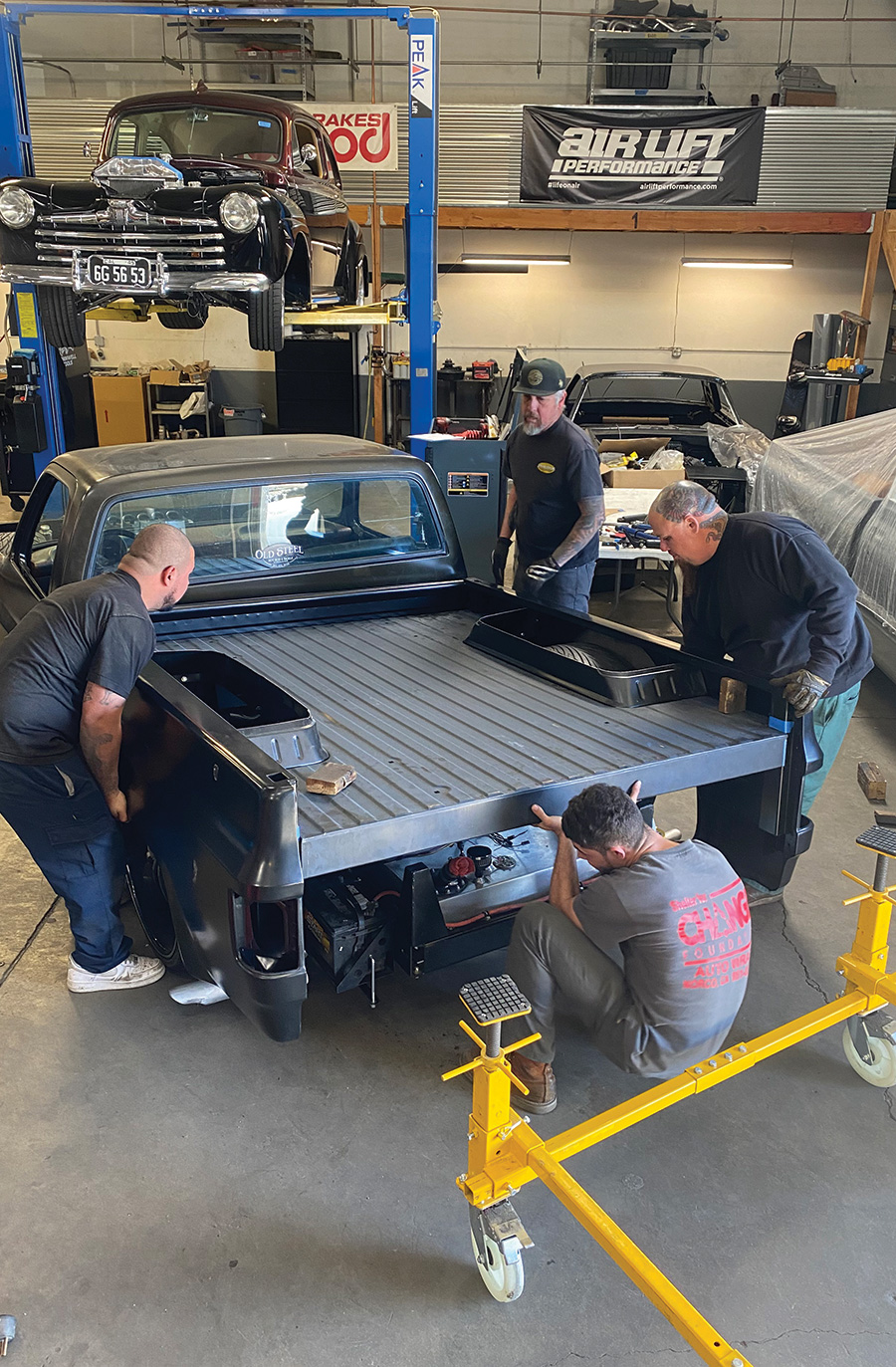


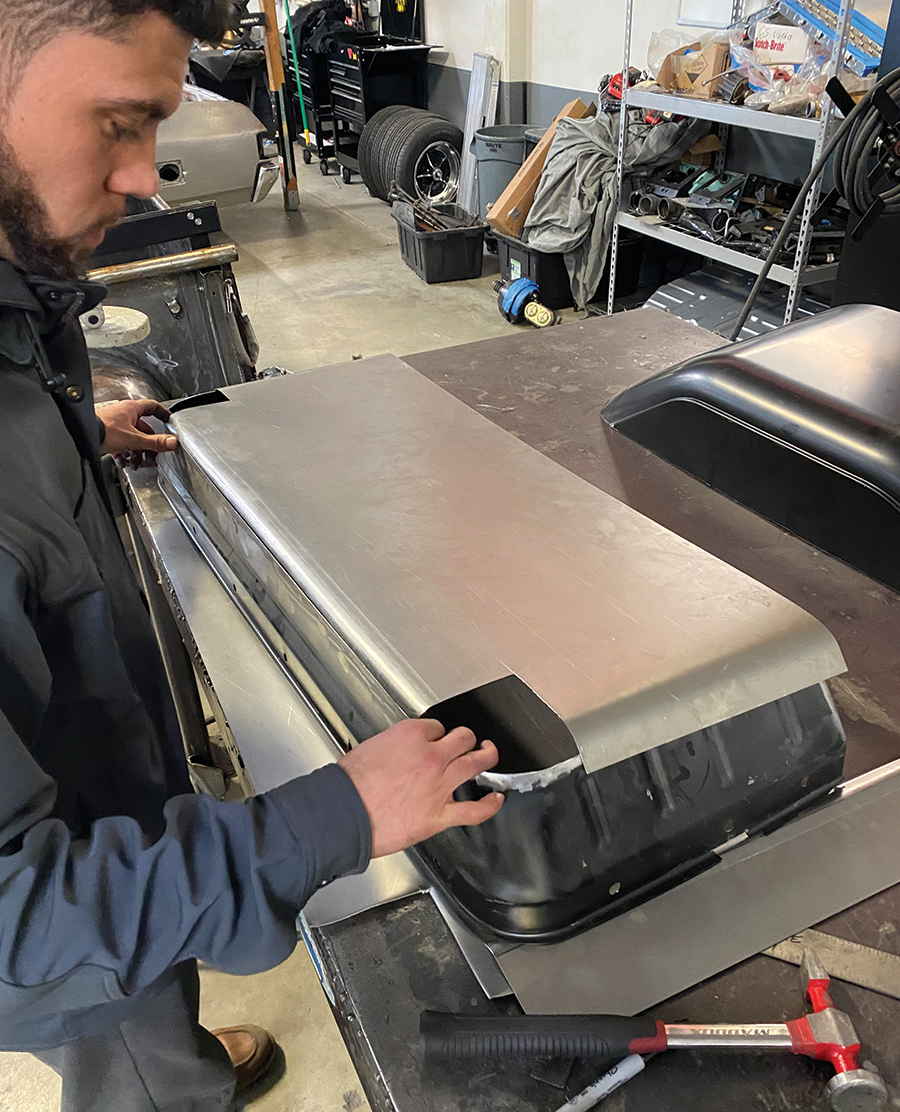


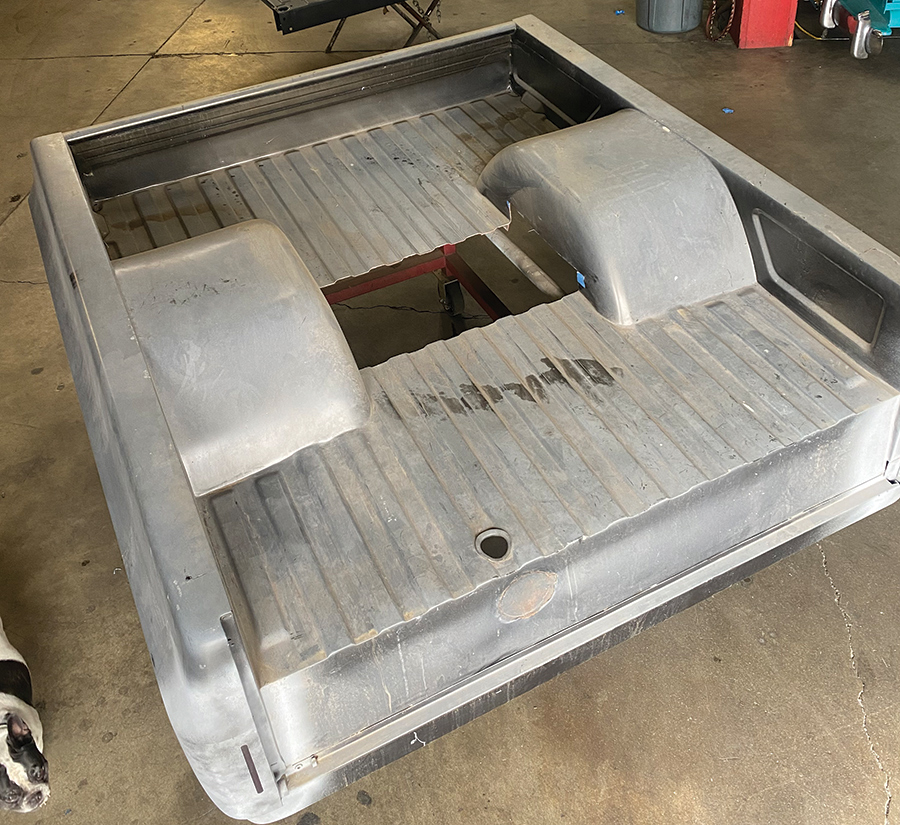
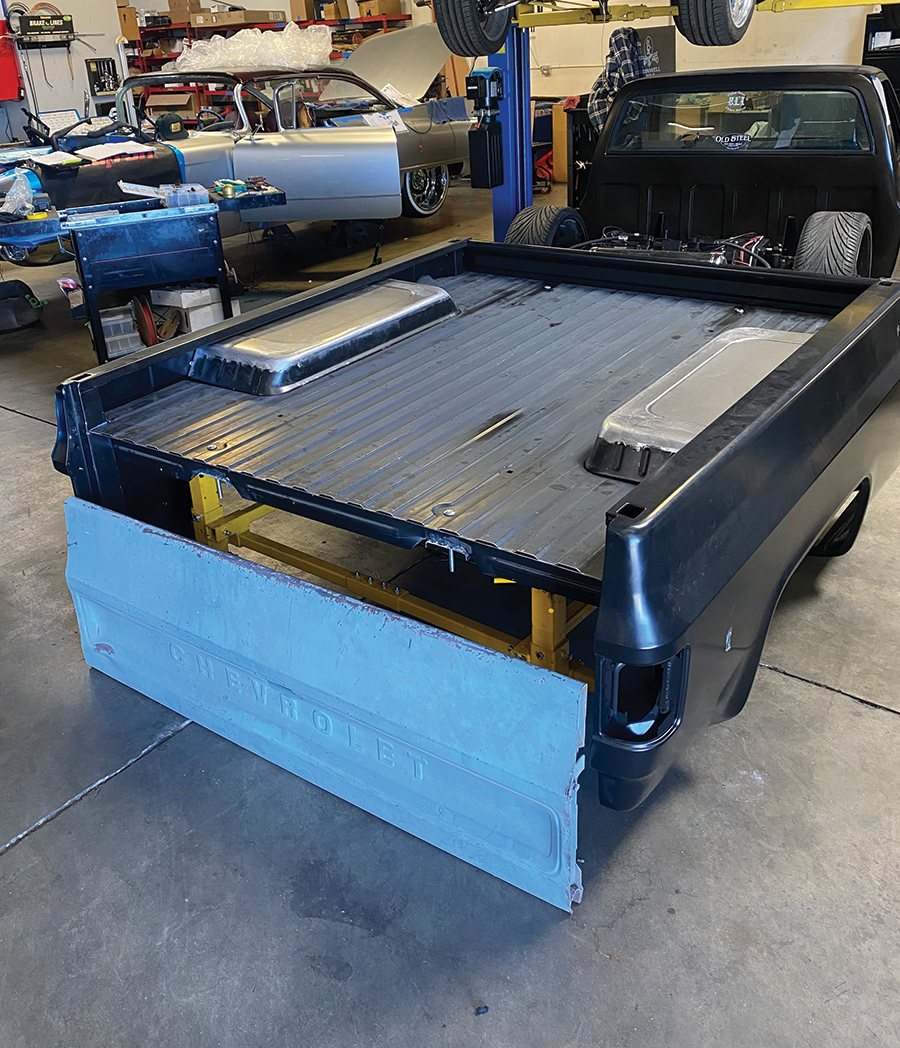