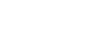

BY Rob FortierPhotography BY THE AUTHOR
elcome back! Assuming you left off where we last left off—with the conclusion of the ’73-87 Chevy/GMC longbed chassis shortening—we’re now all primed and ready to finish the job with the shortening of the ’76 Chevy’s factory bedsides at Brothers Trucks’ tech center.
Now, let’s let it be known: By far, the easiest/quickest way to shorten a longbed Fleetside is by acquiring a new set of short wheelbase bedsides … plain and simple. However, as is the case here, when said longbed has the cab-matching patina, and said patina needs to remain, well, then we take the long road, so to speak, and proceed with the semi-laborious task of cutting down the long wheelbase bedsides (same as the frame we just severed: 14 inches off the front, 6 inches off the back … but not quite as simple cut-wise, as you’ll see).
As the old saying goes, there’s more than one way to skin a cat and, as such, there are definitely a number of ways to go about shortening long bedsides. Though not as in-depth as we care to illustrate, due to space limitations, we’re presenting you with what we believe is the most straightforward method … one that (hopefully) won’t leave you having to call Brothers to order a set of those aforementioned “new” bedsides! (For the full, in-depth procedure, follow along with Dave Welch on Brothers’ YouTube channel: https://www.youtube.com/watch?v=sSi2gzylceU.)
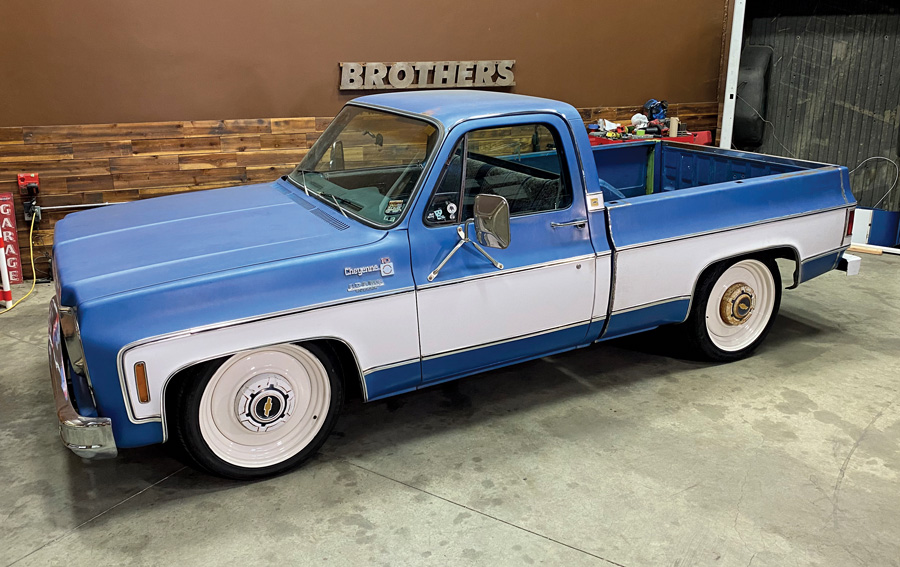
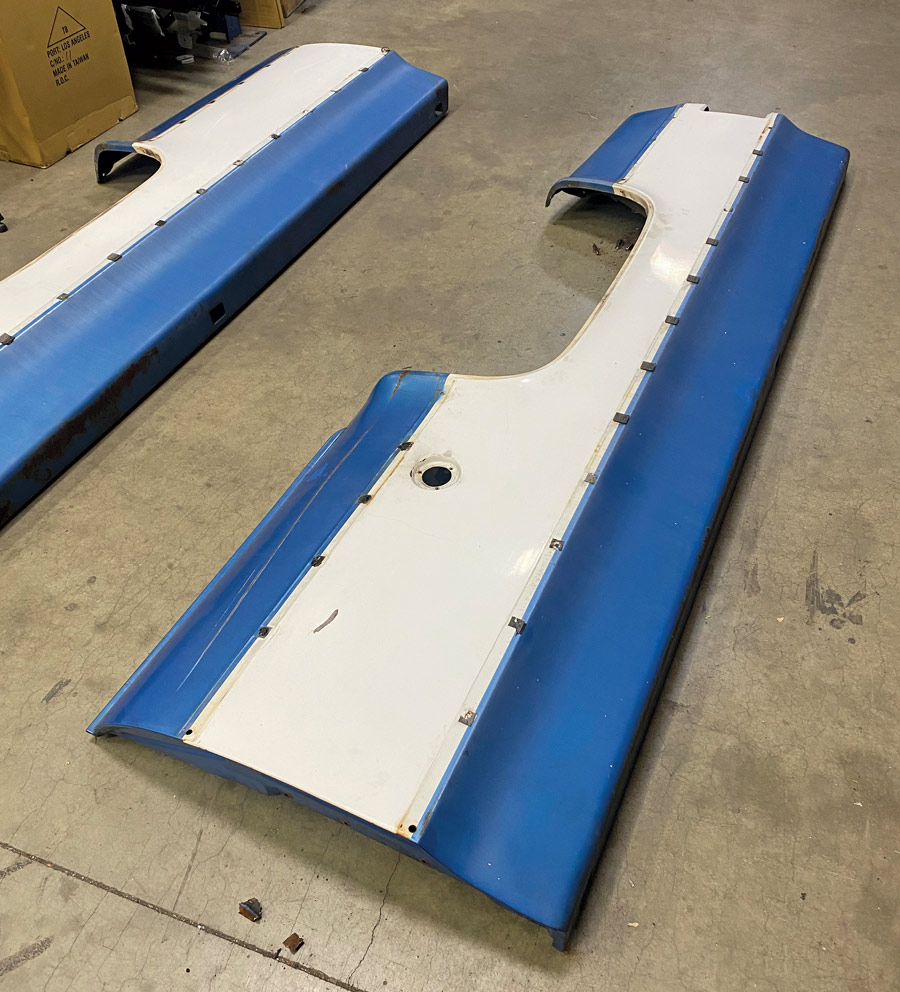
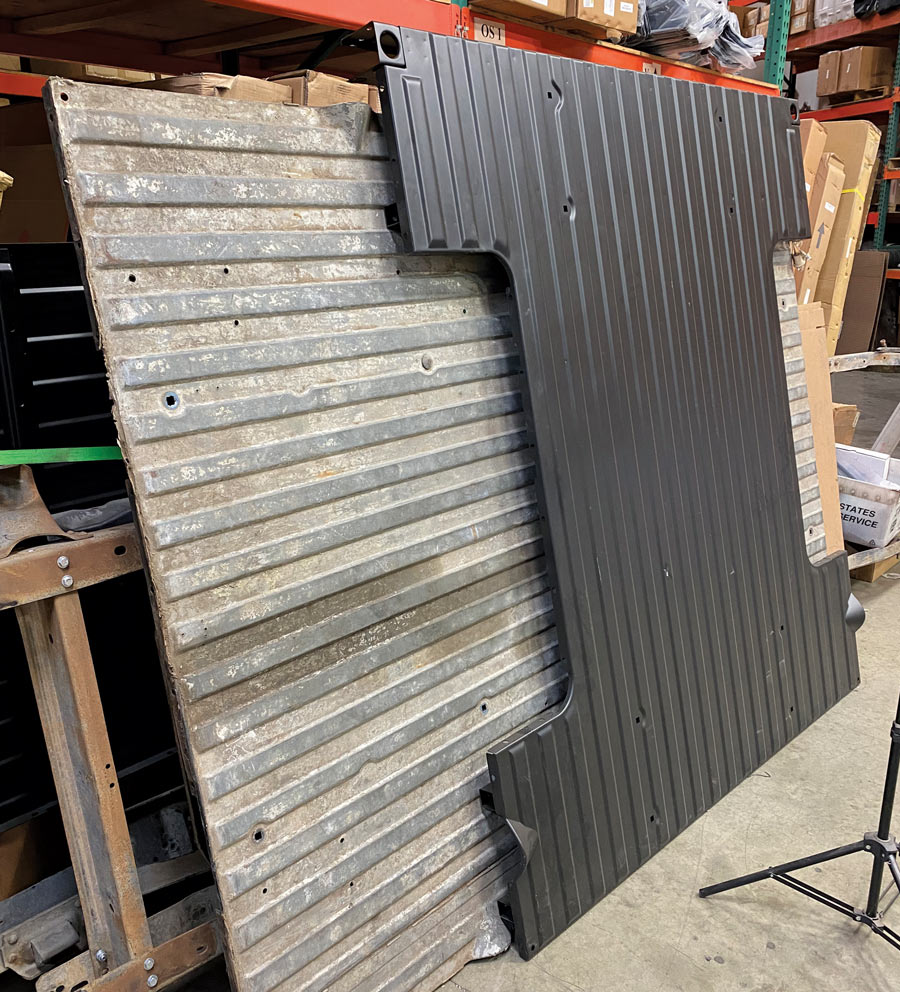
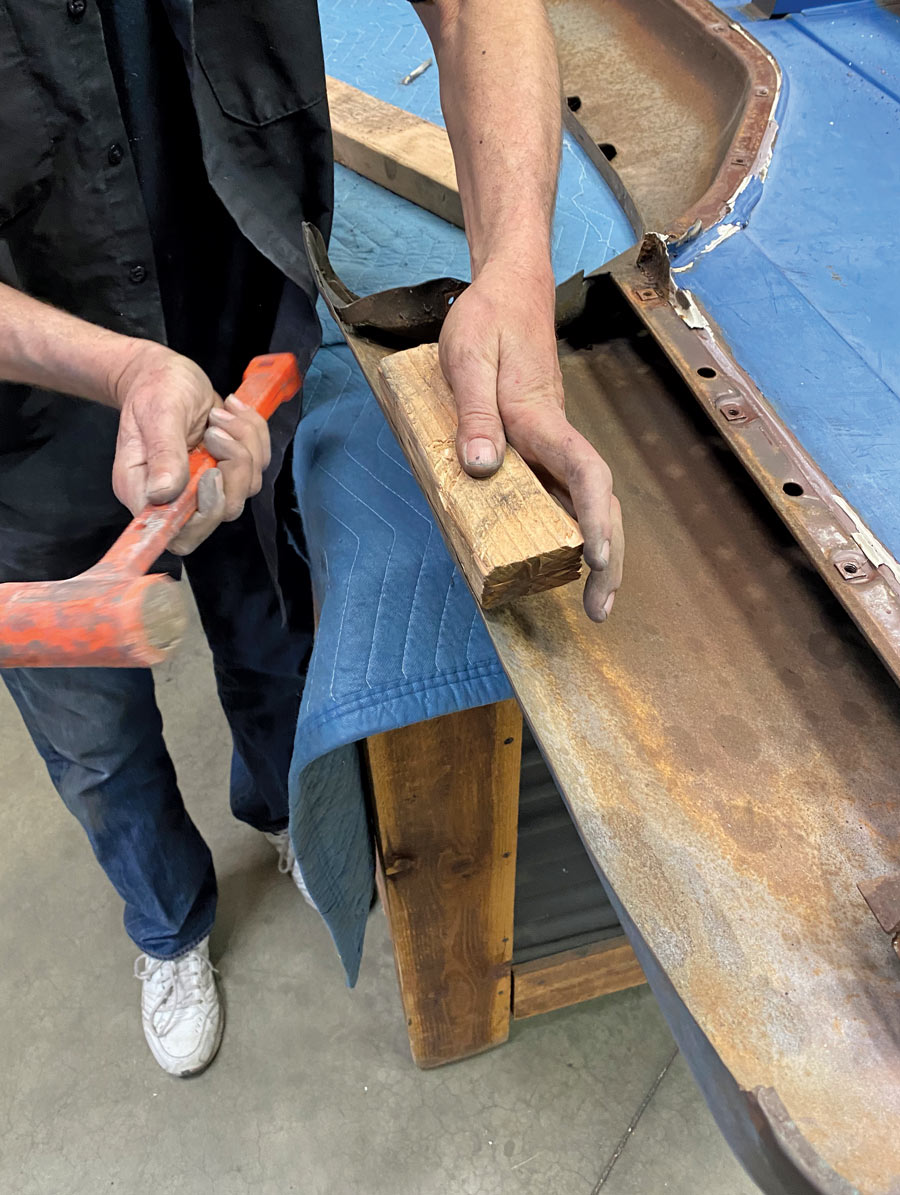
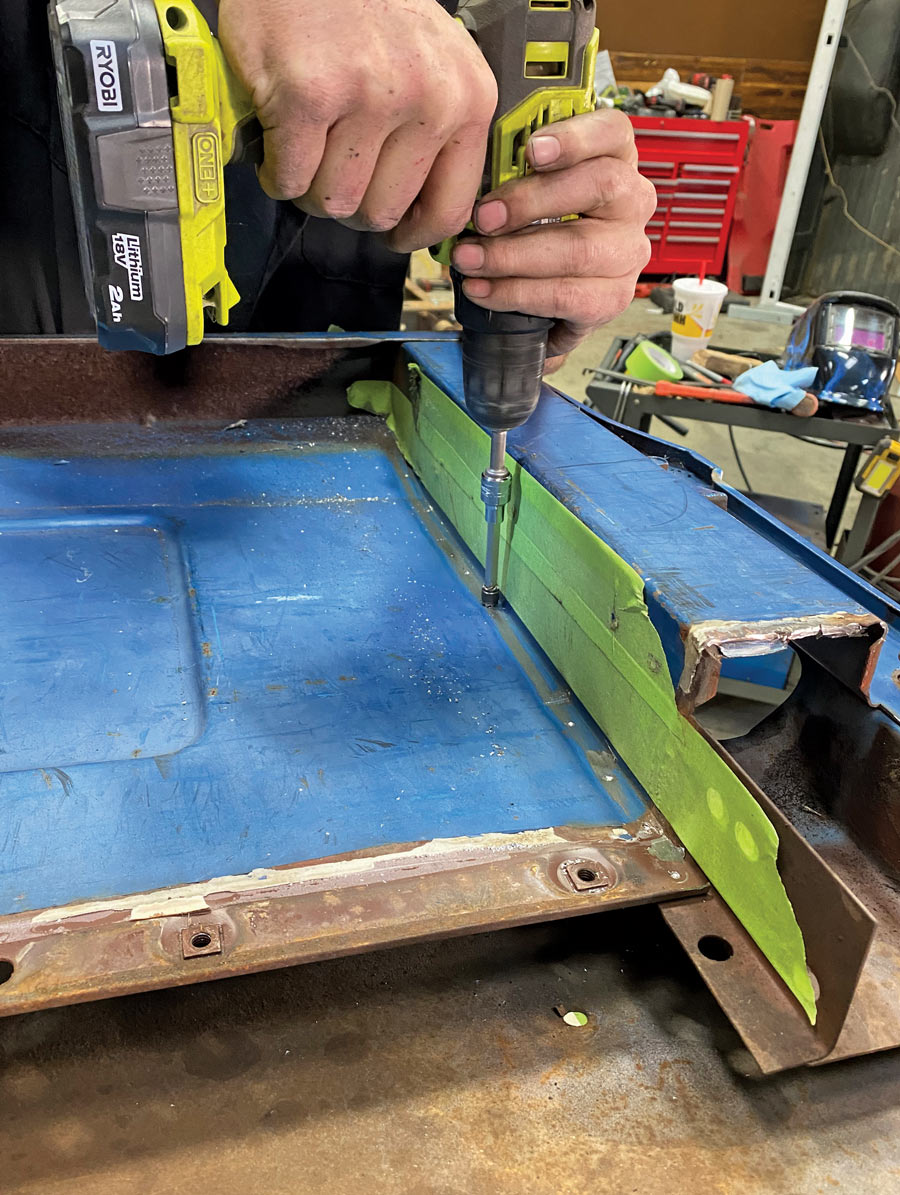
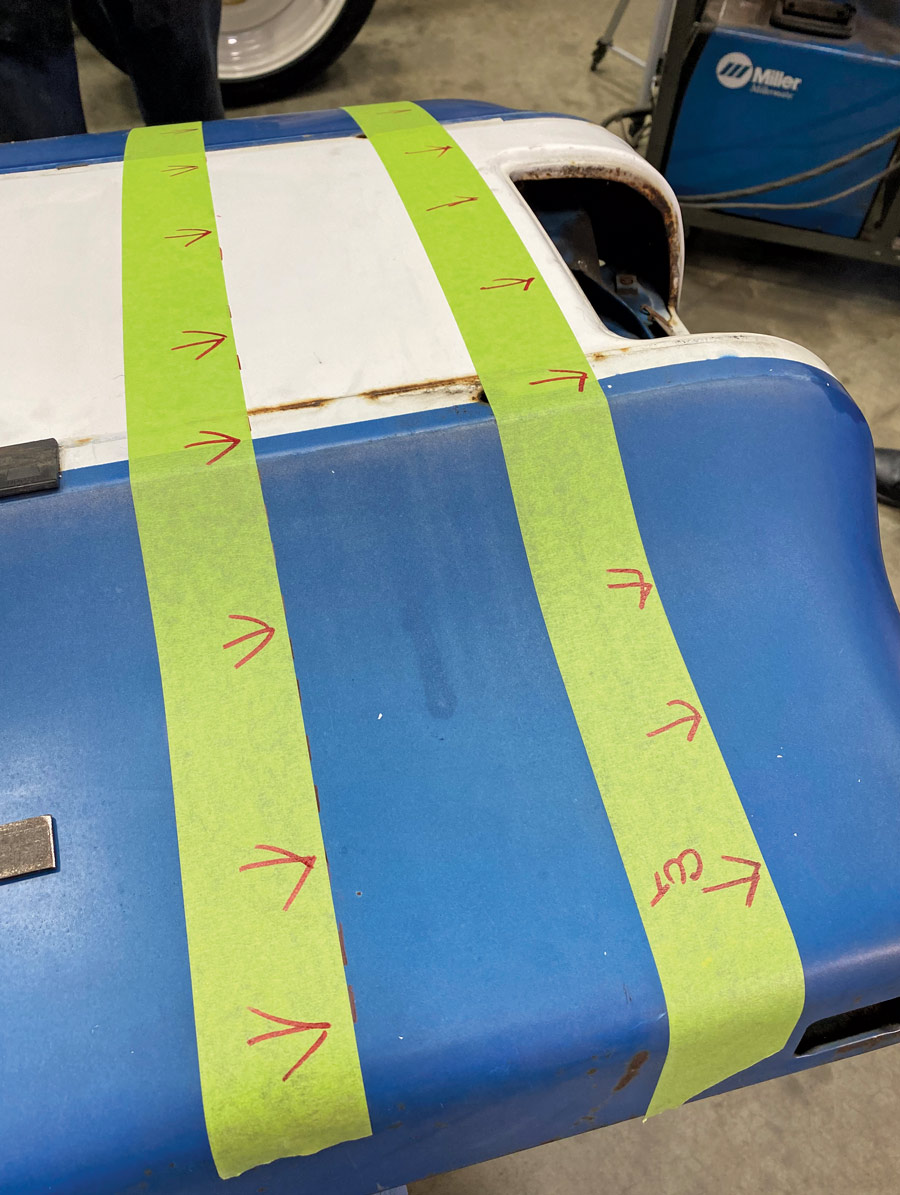
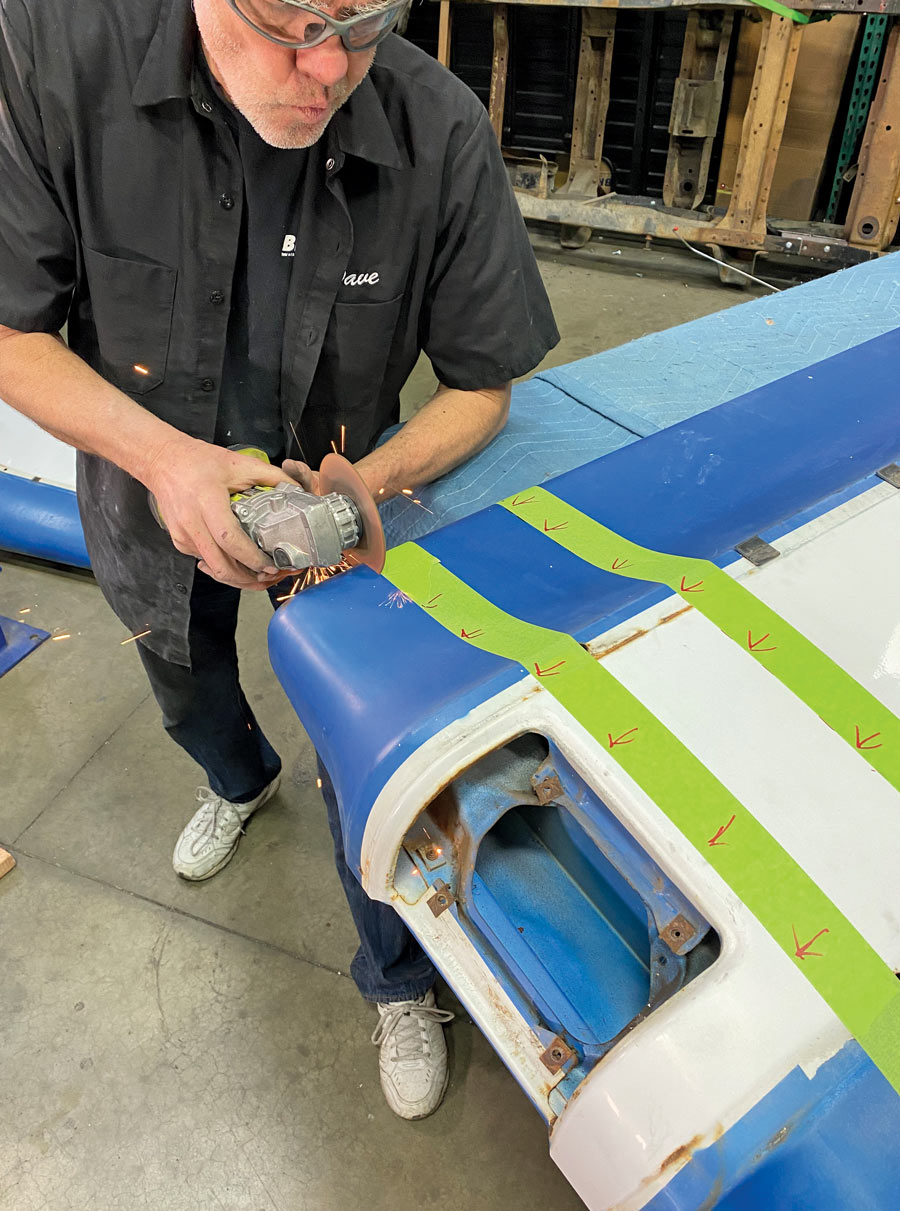
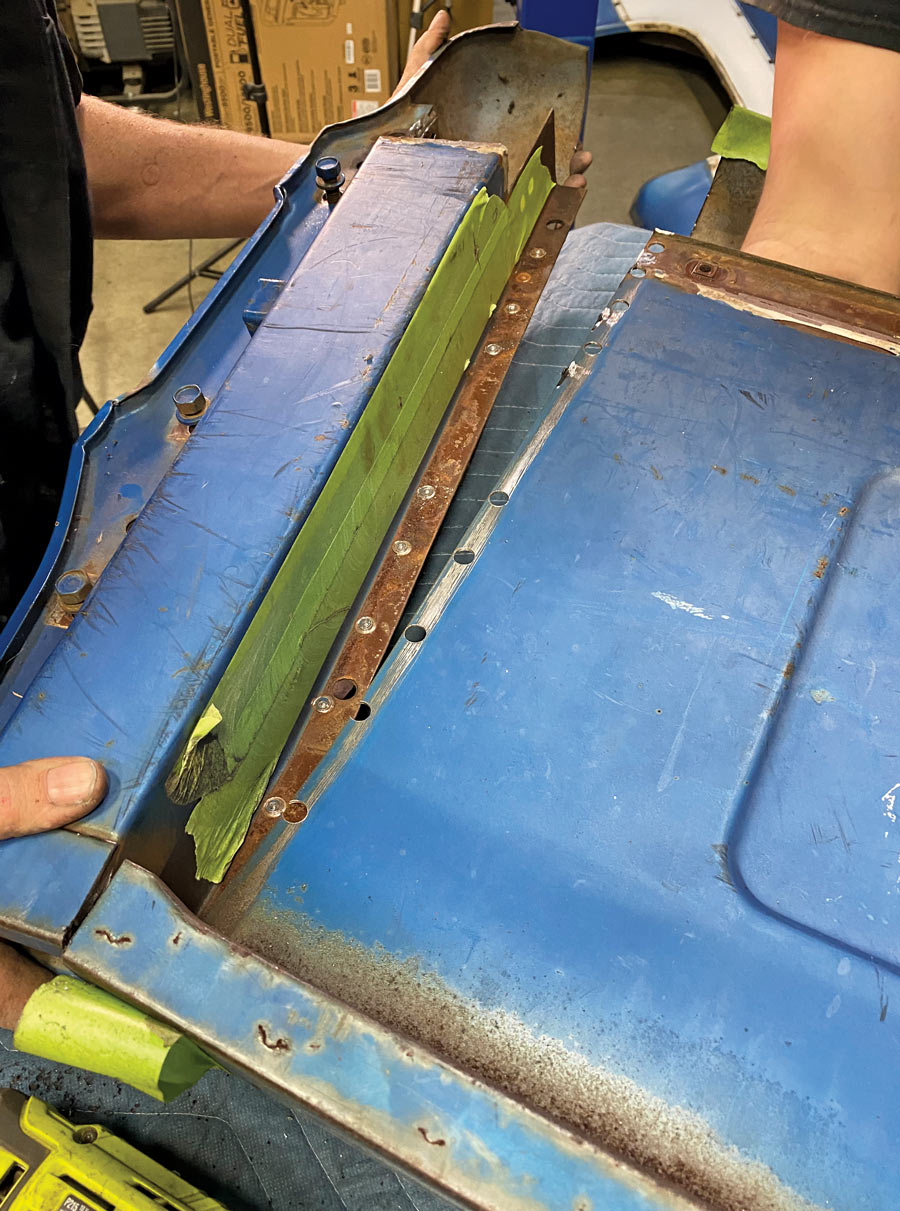
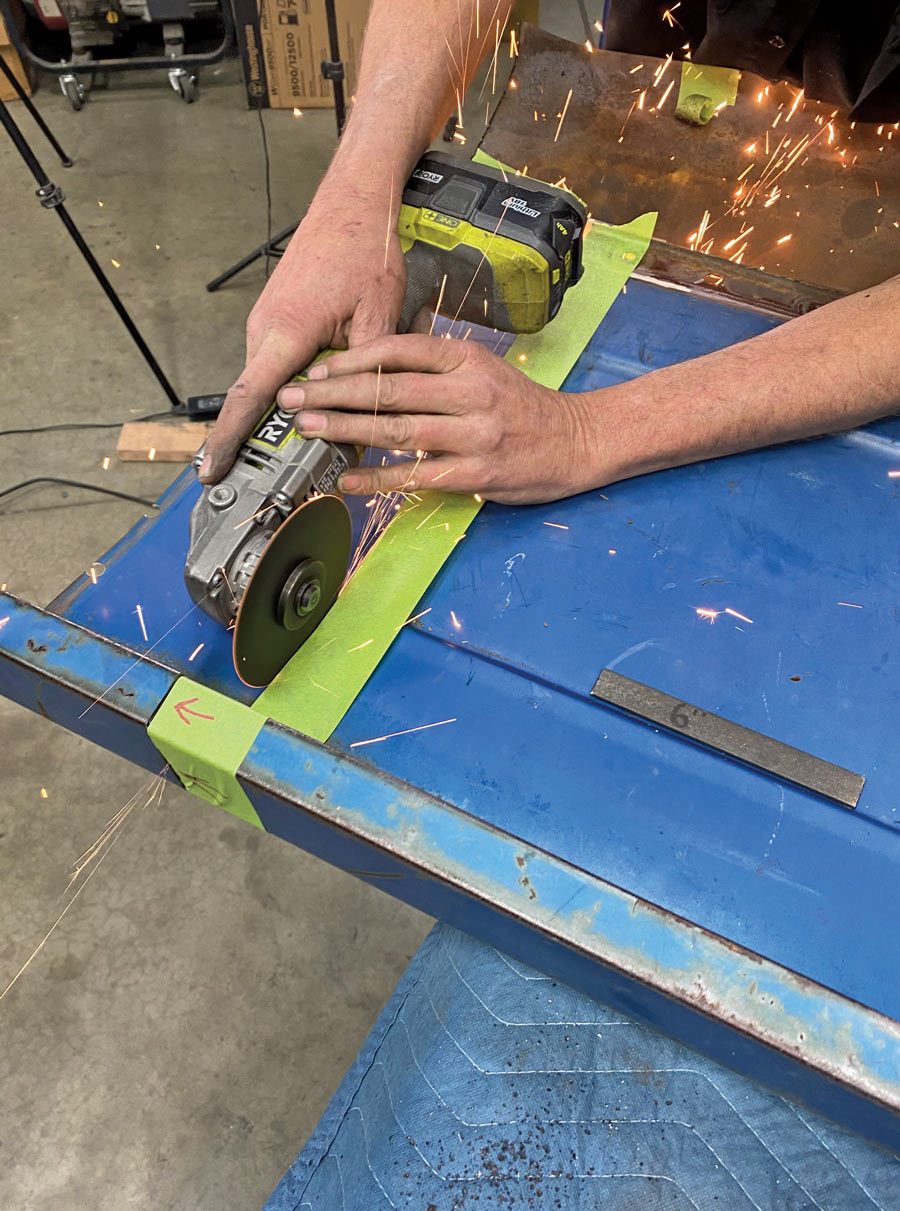
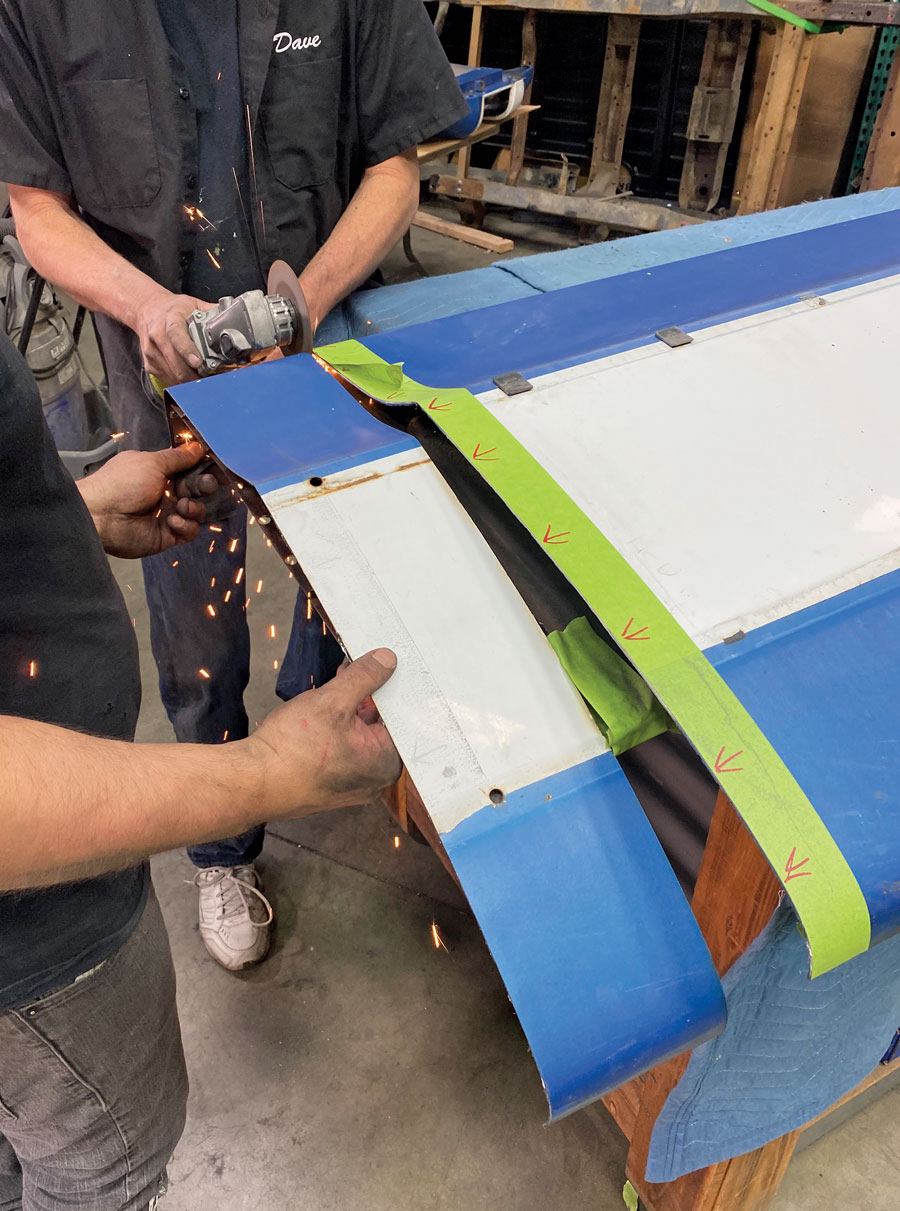
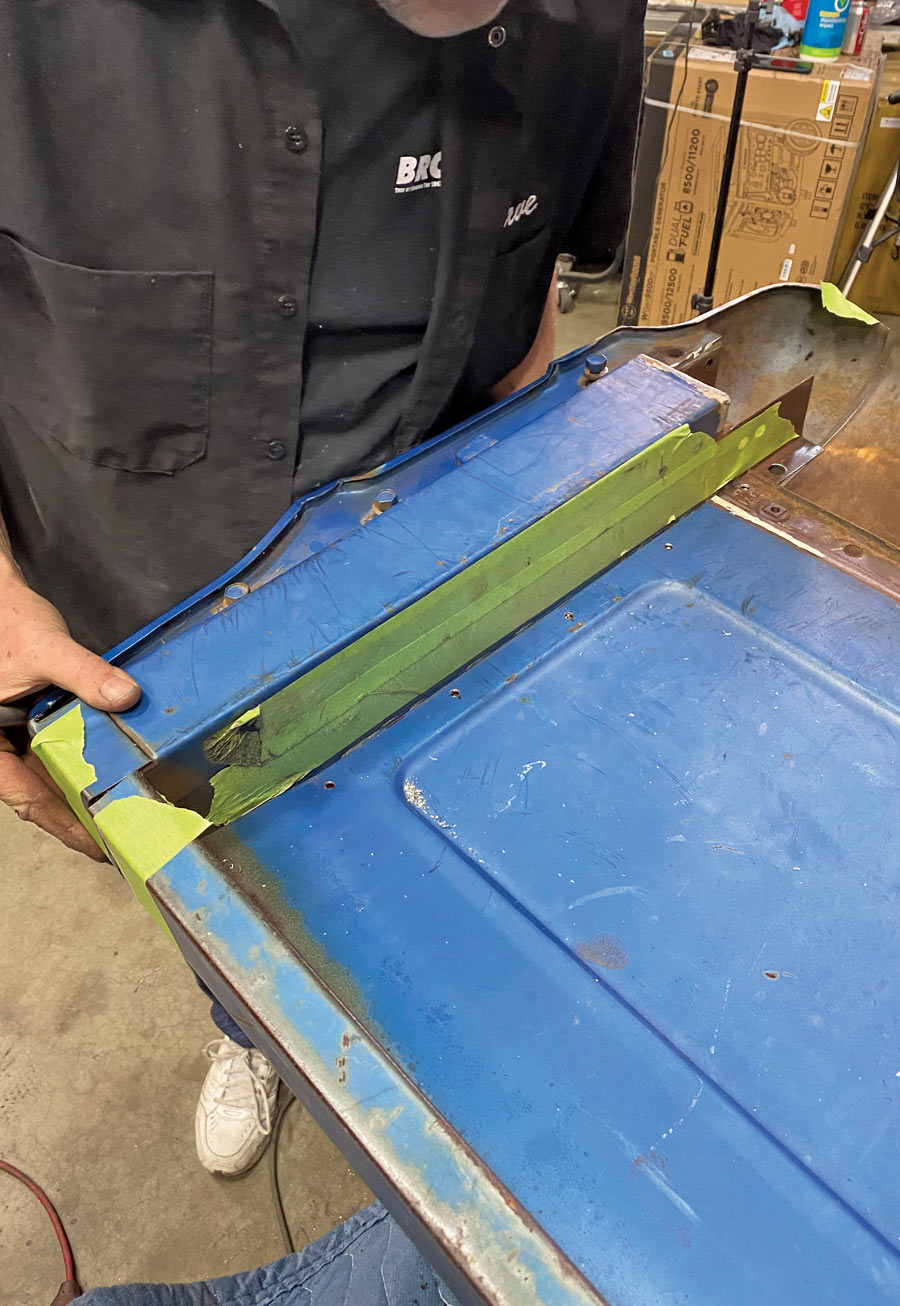
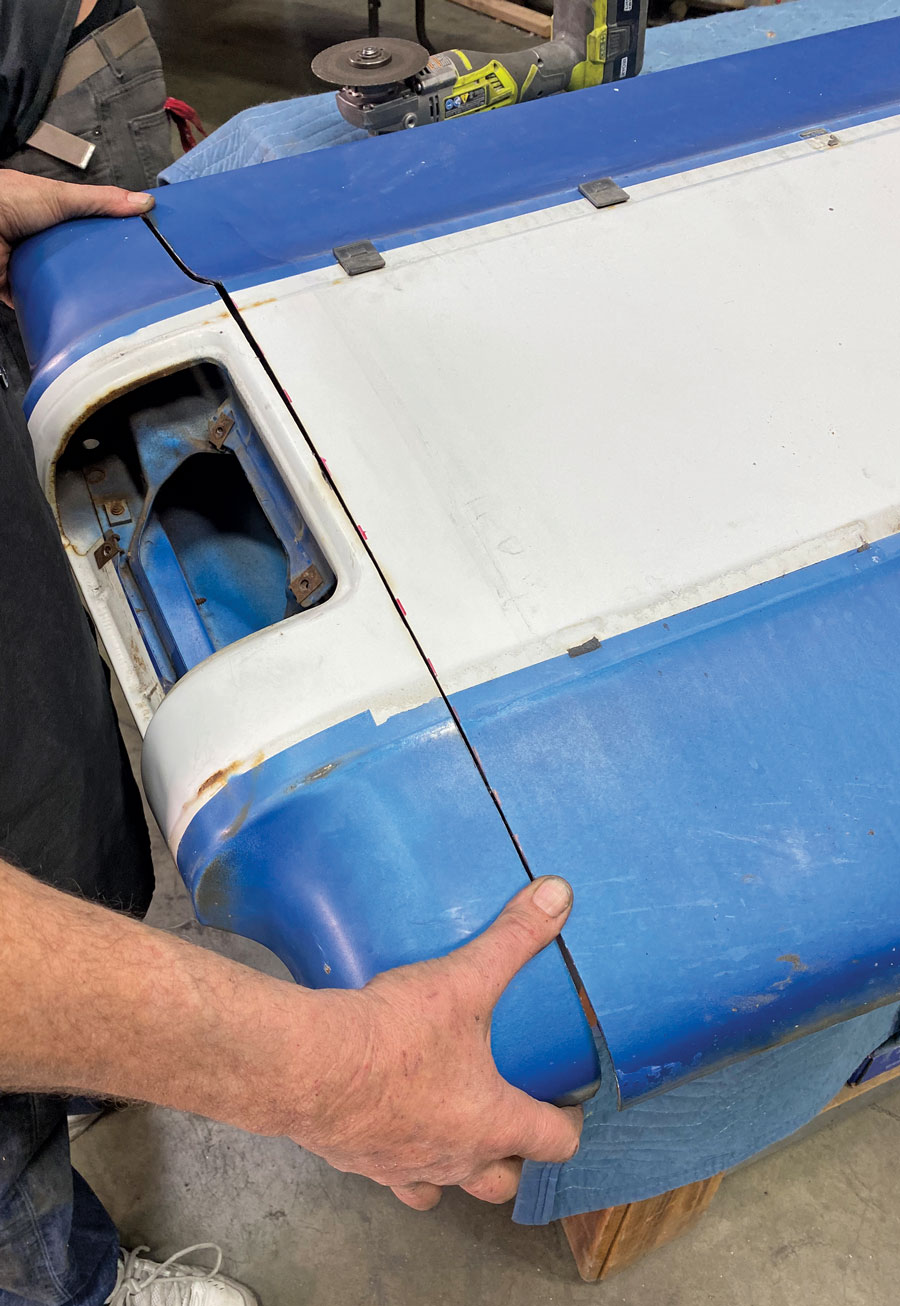
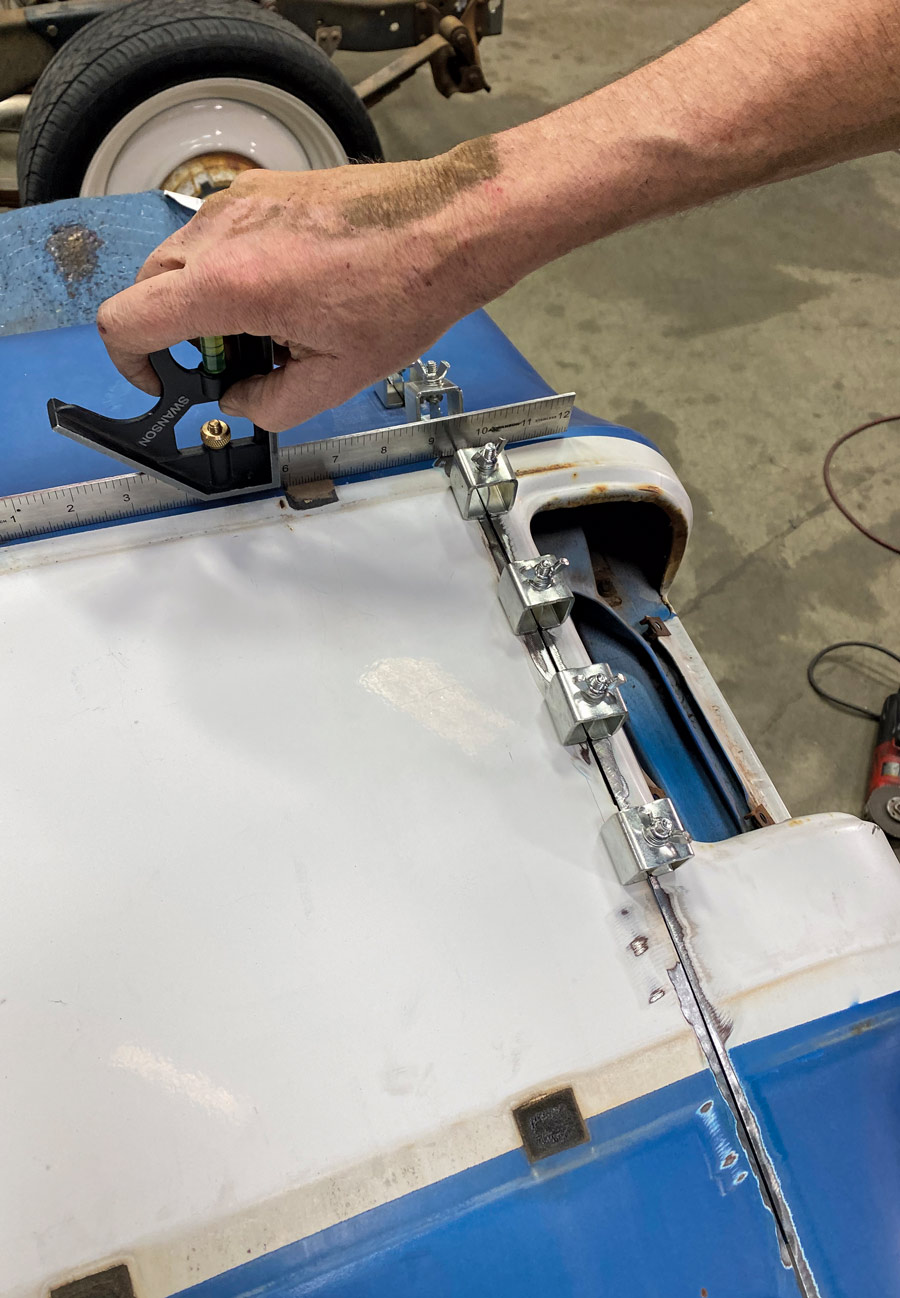
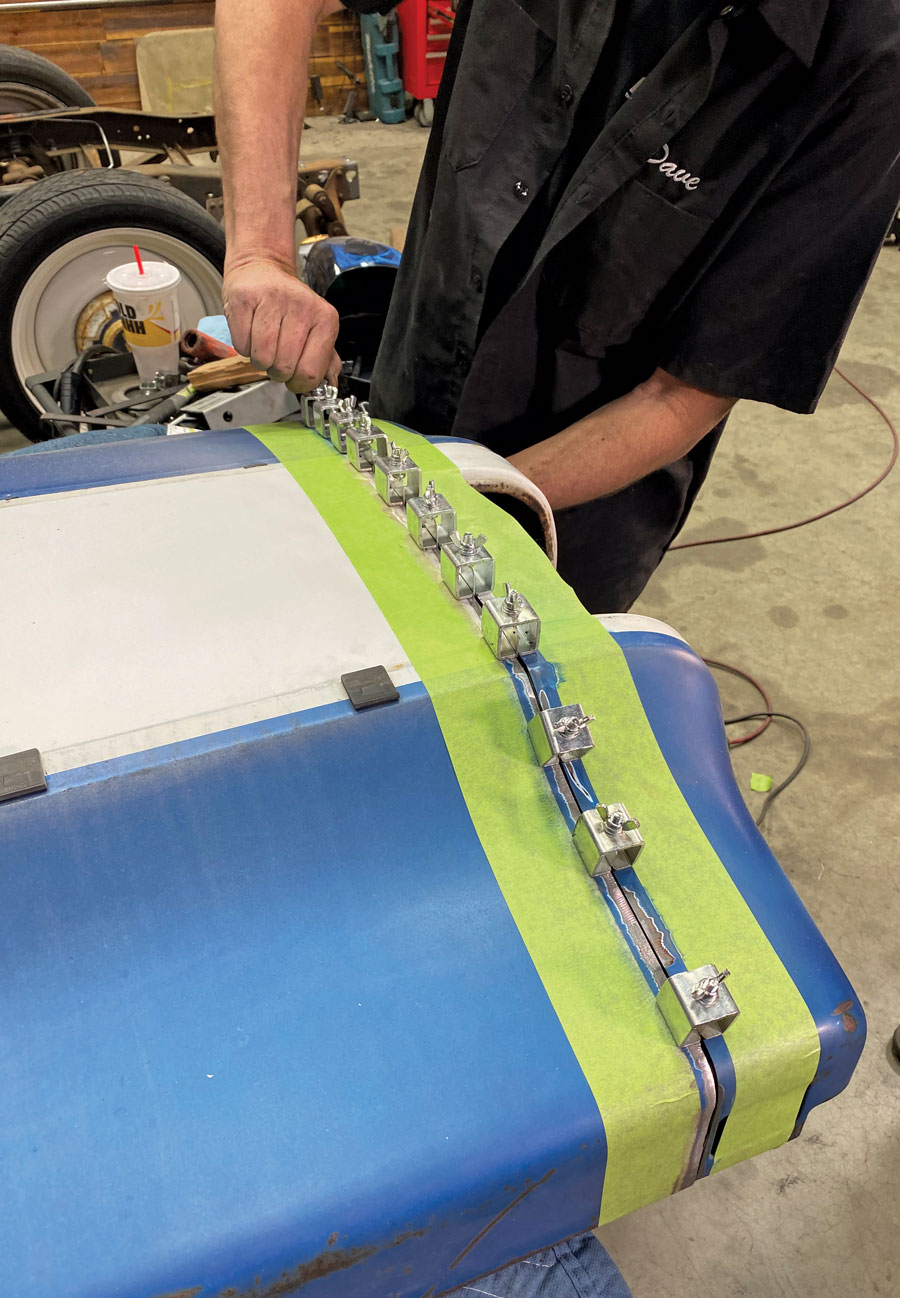
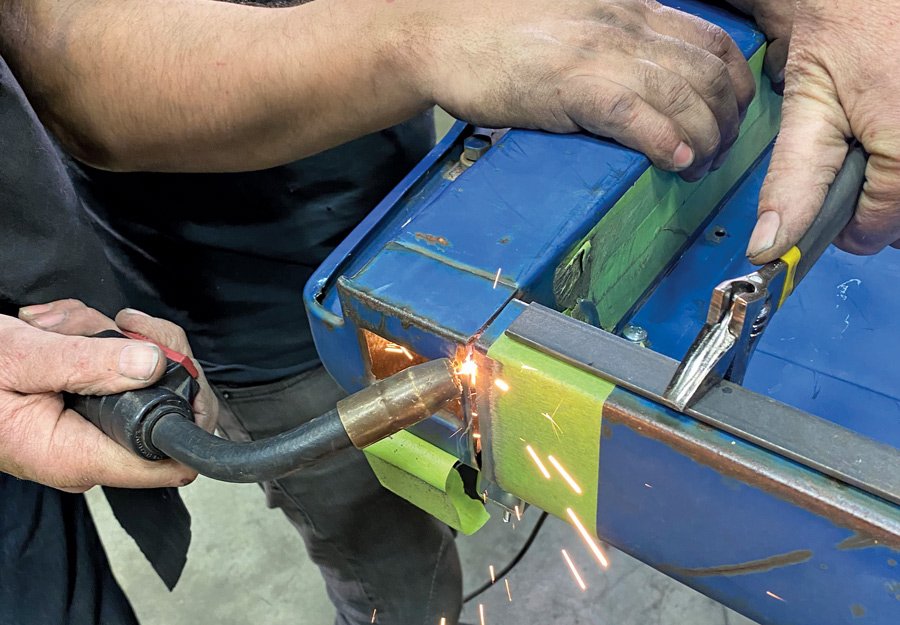
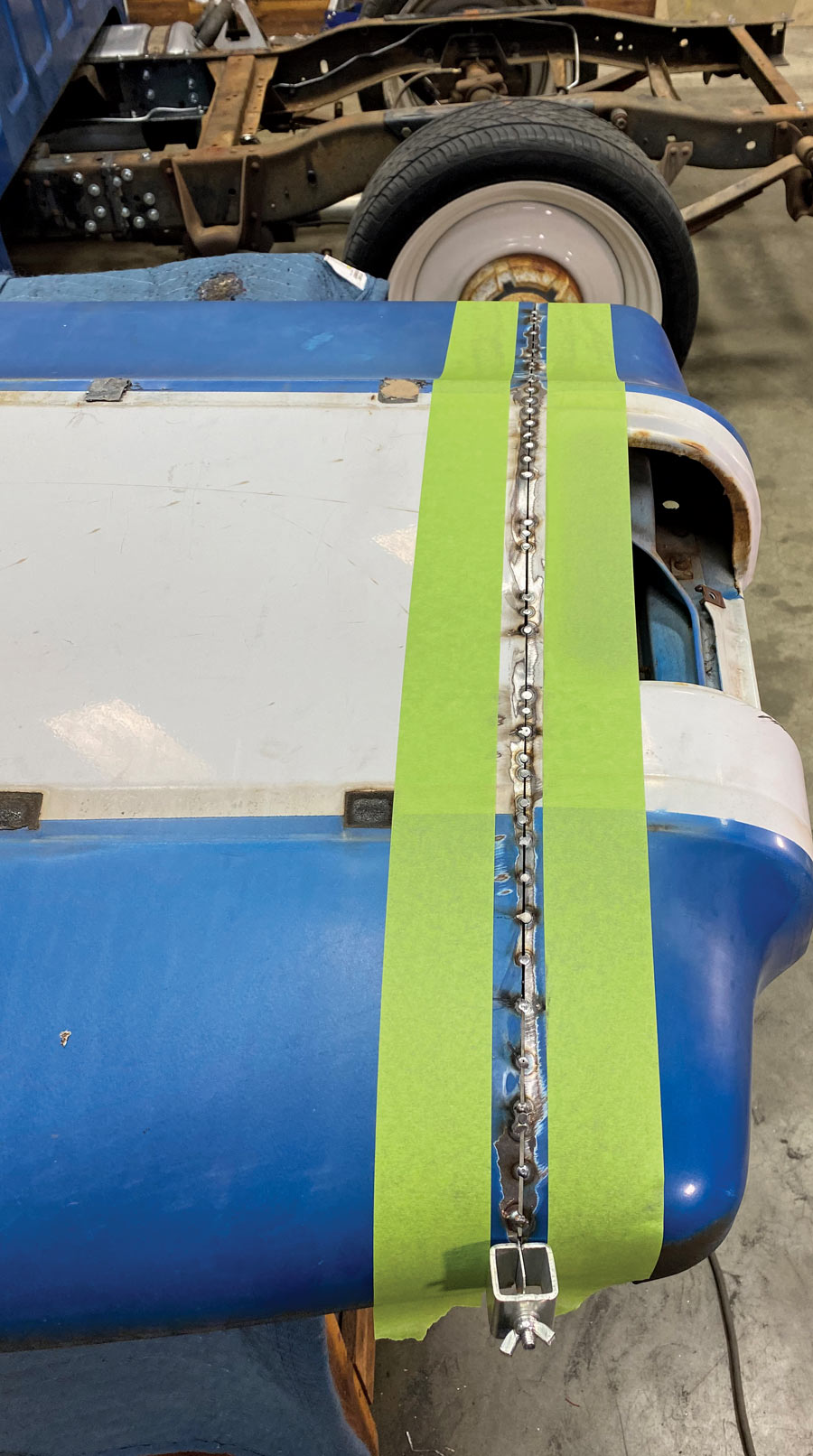
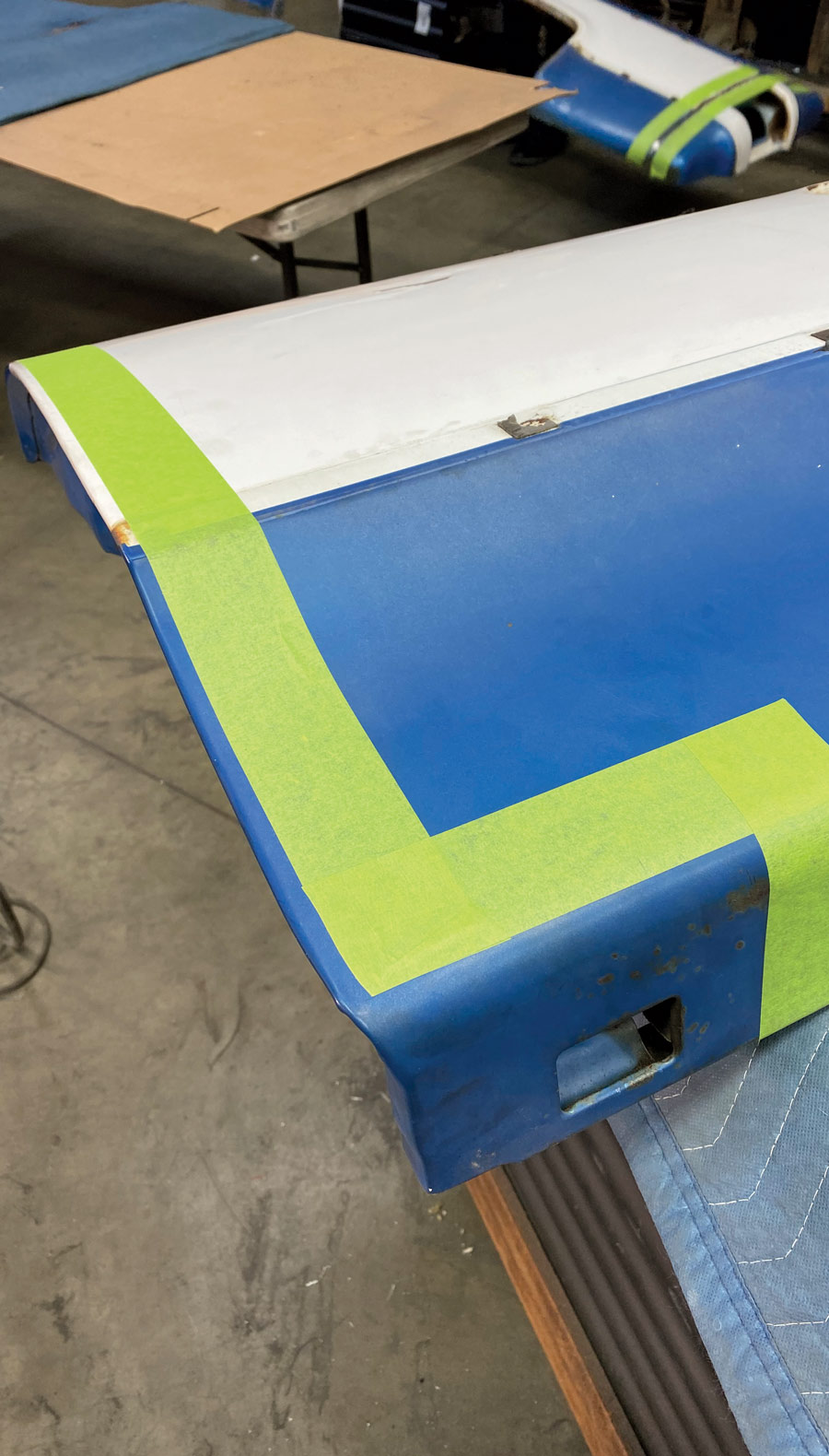
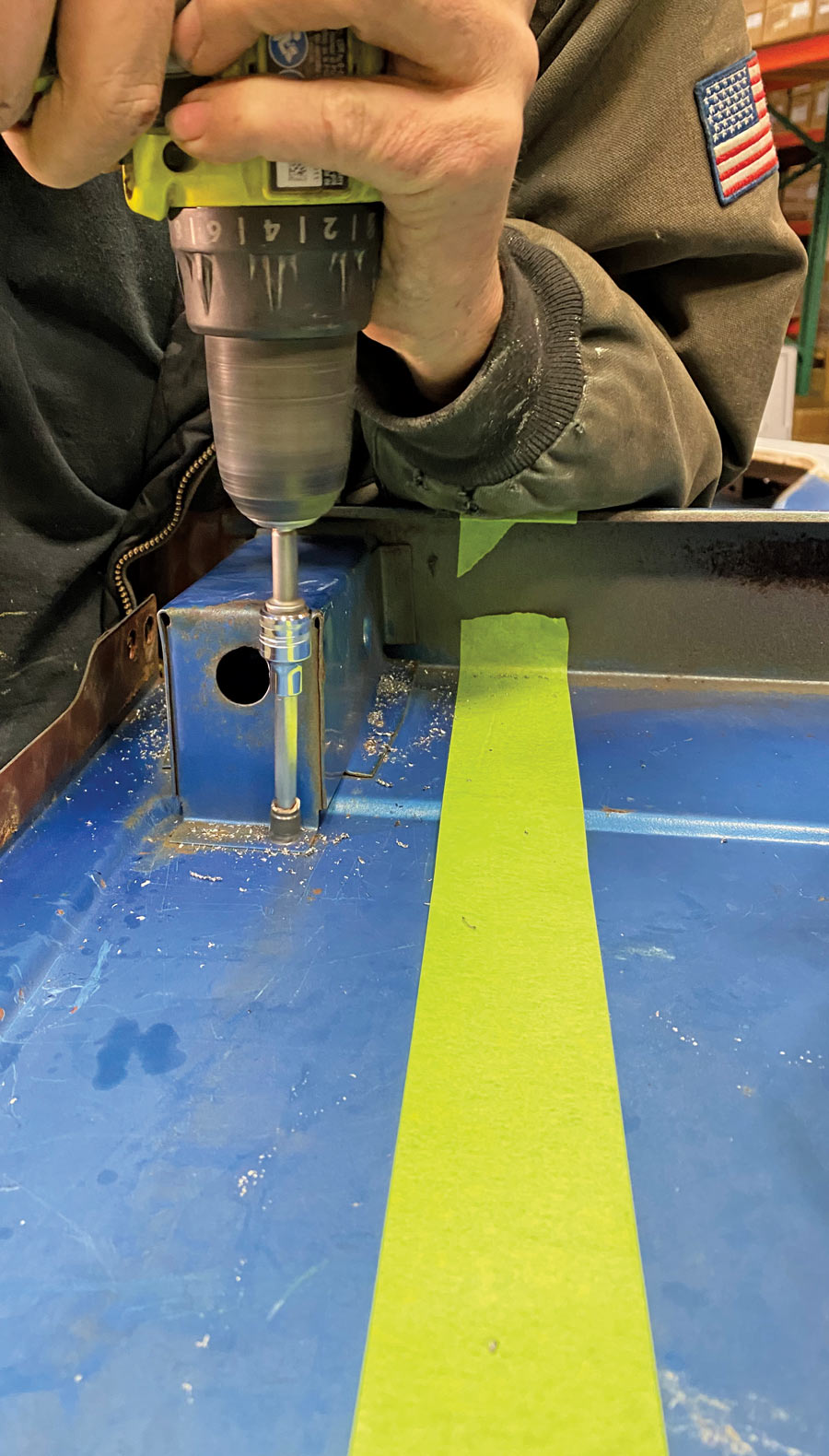
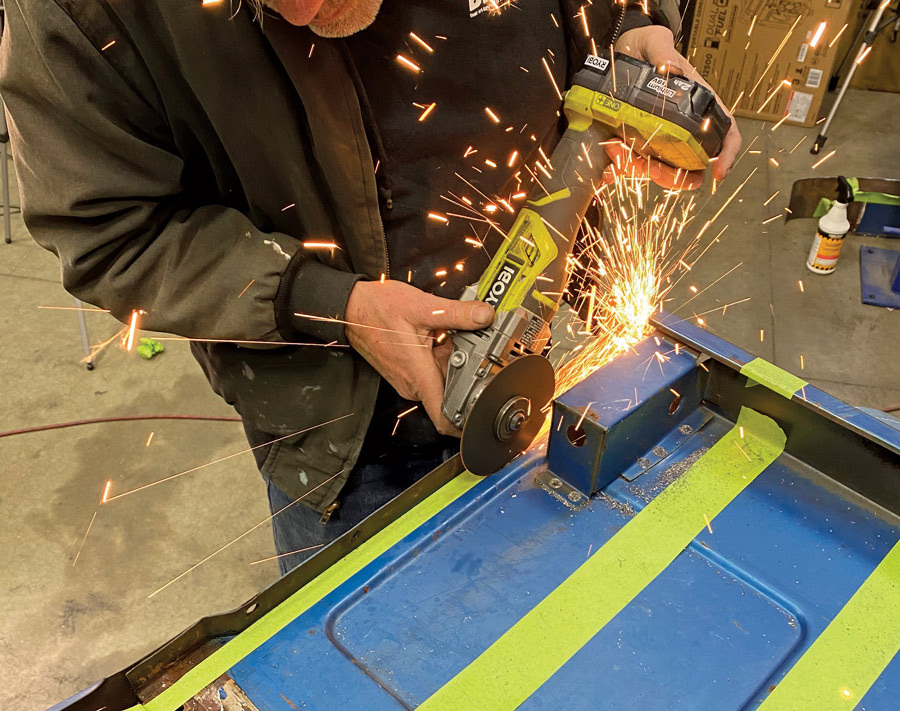
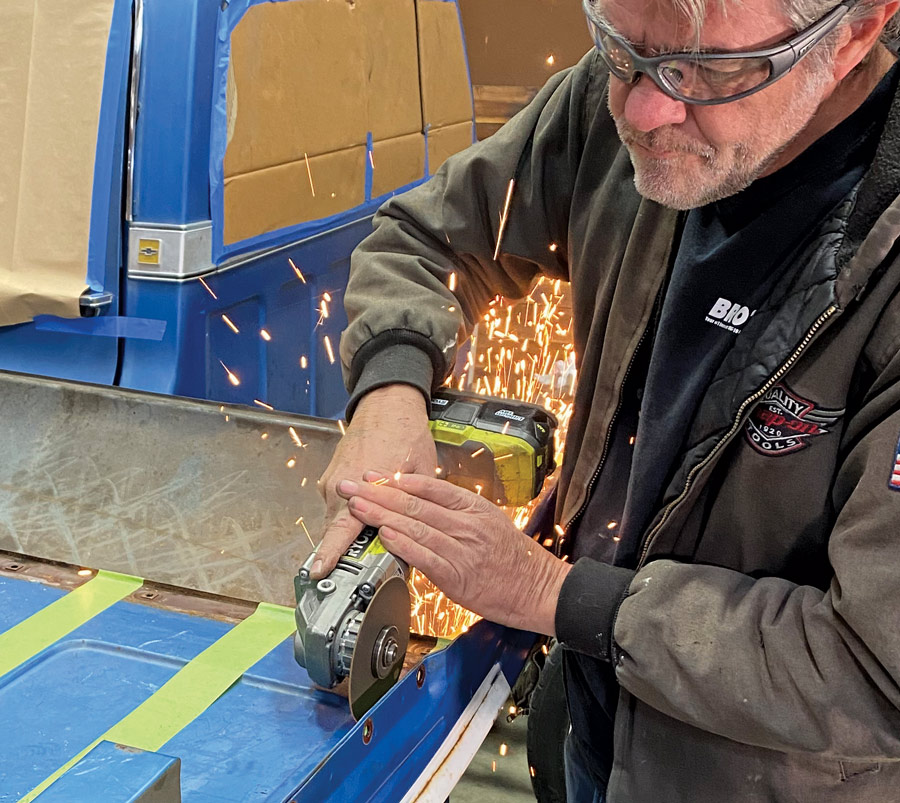
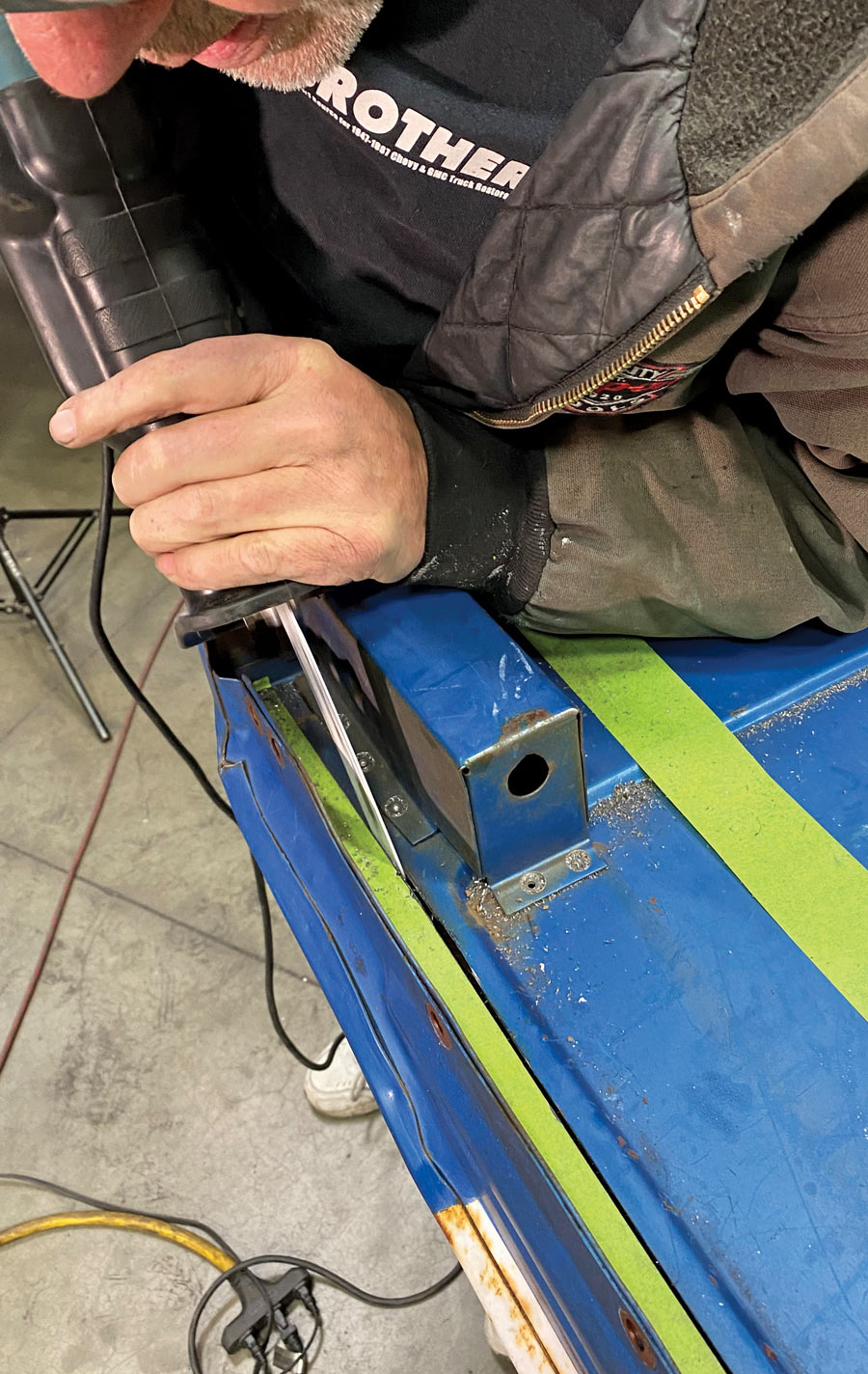
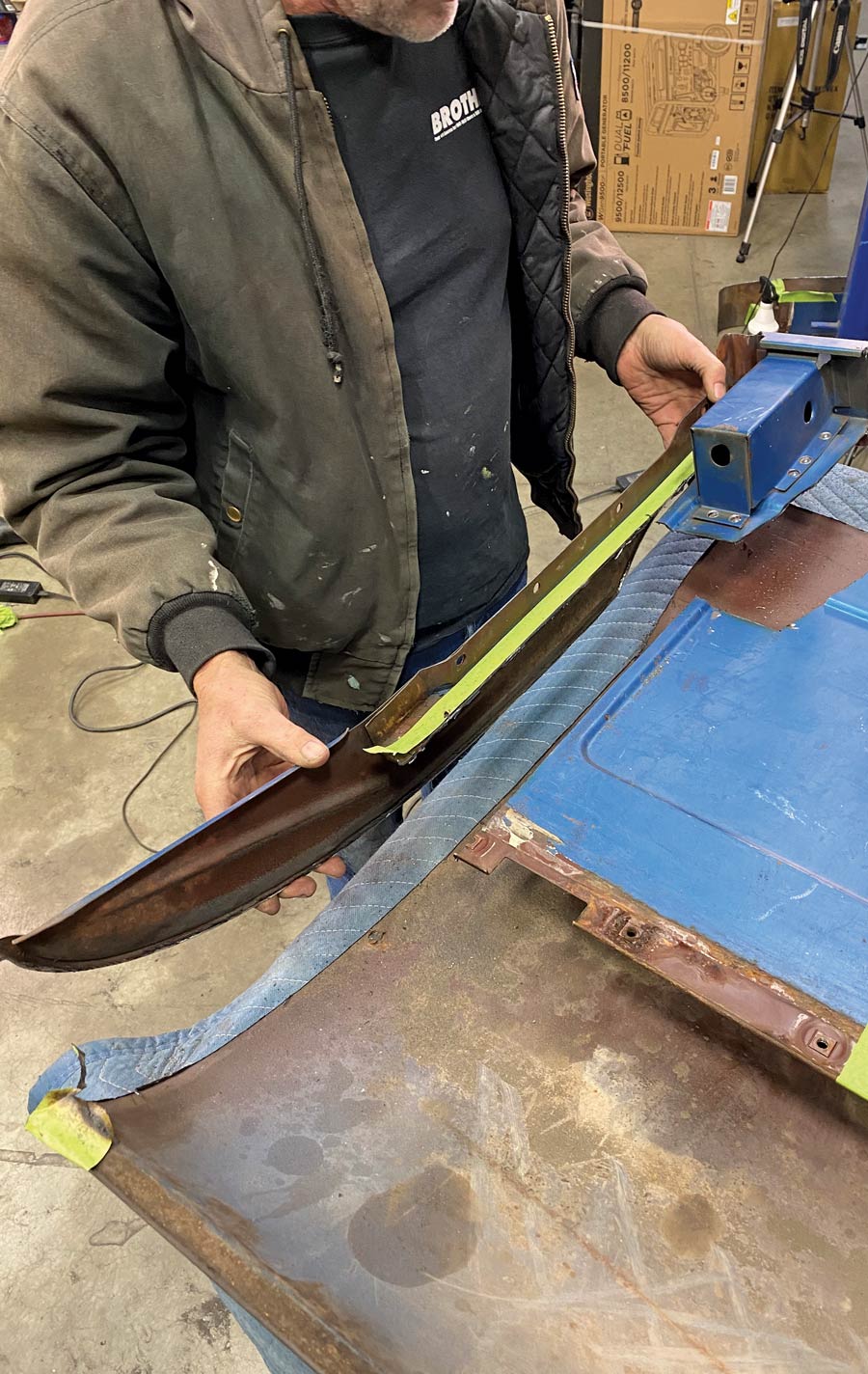
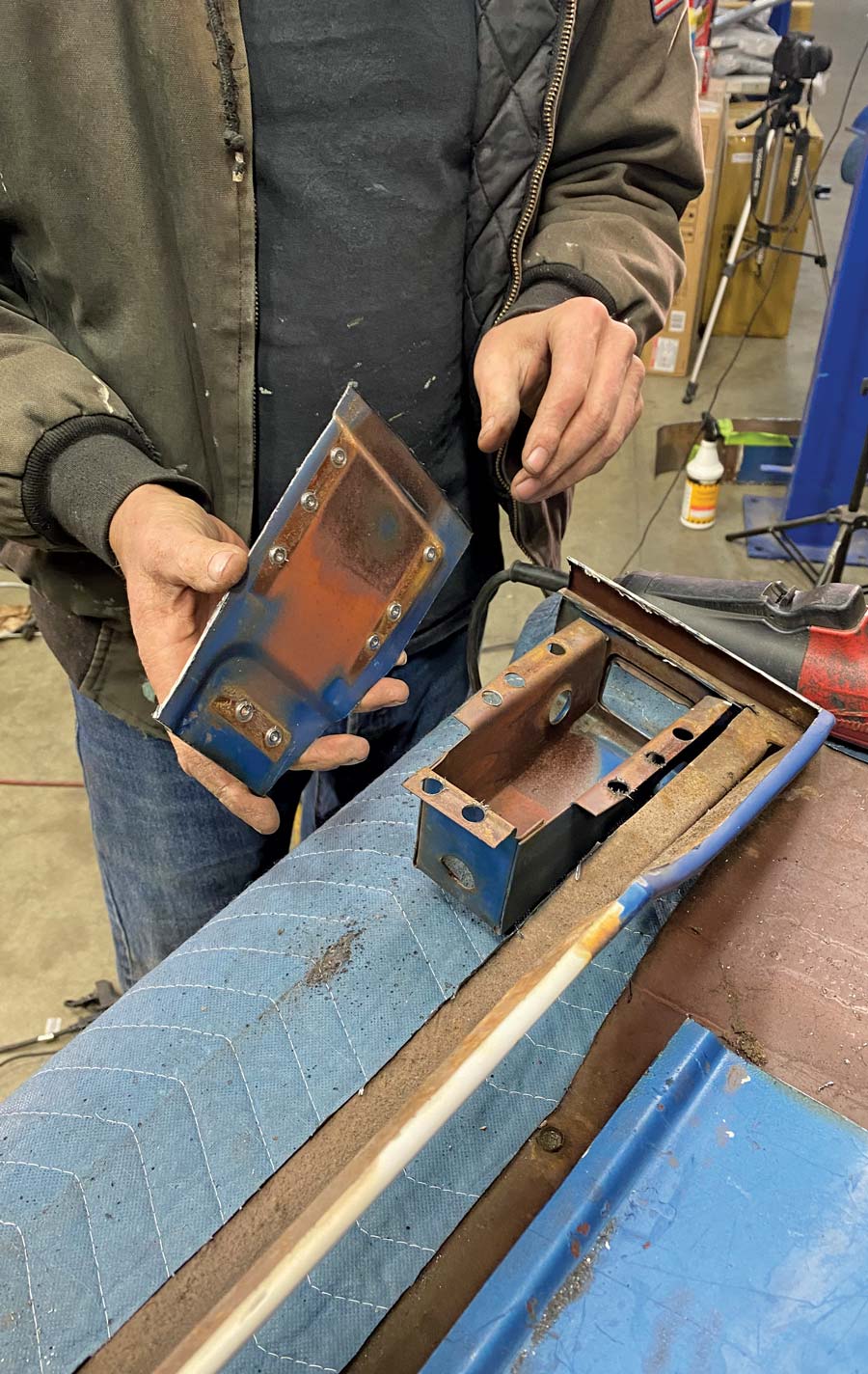
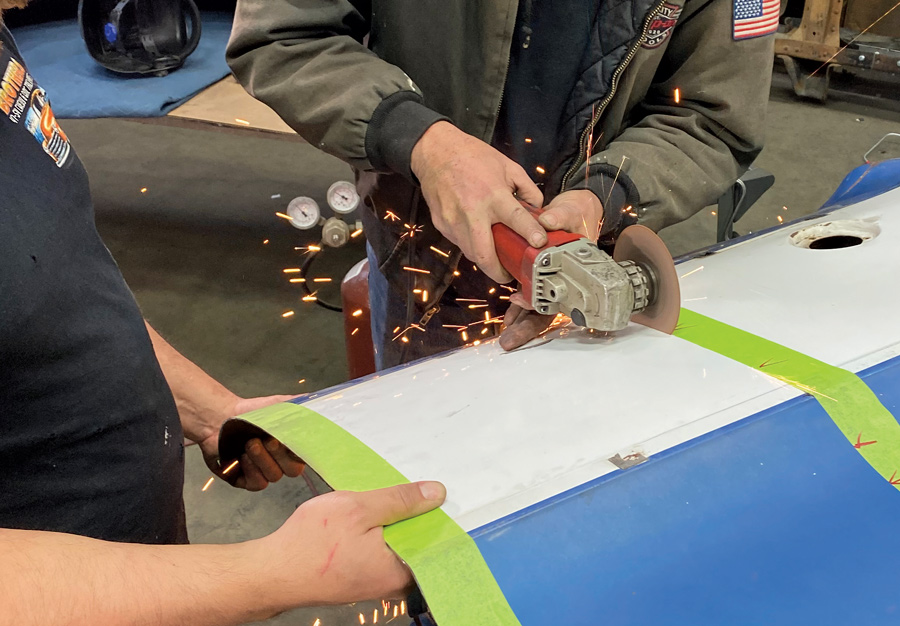
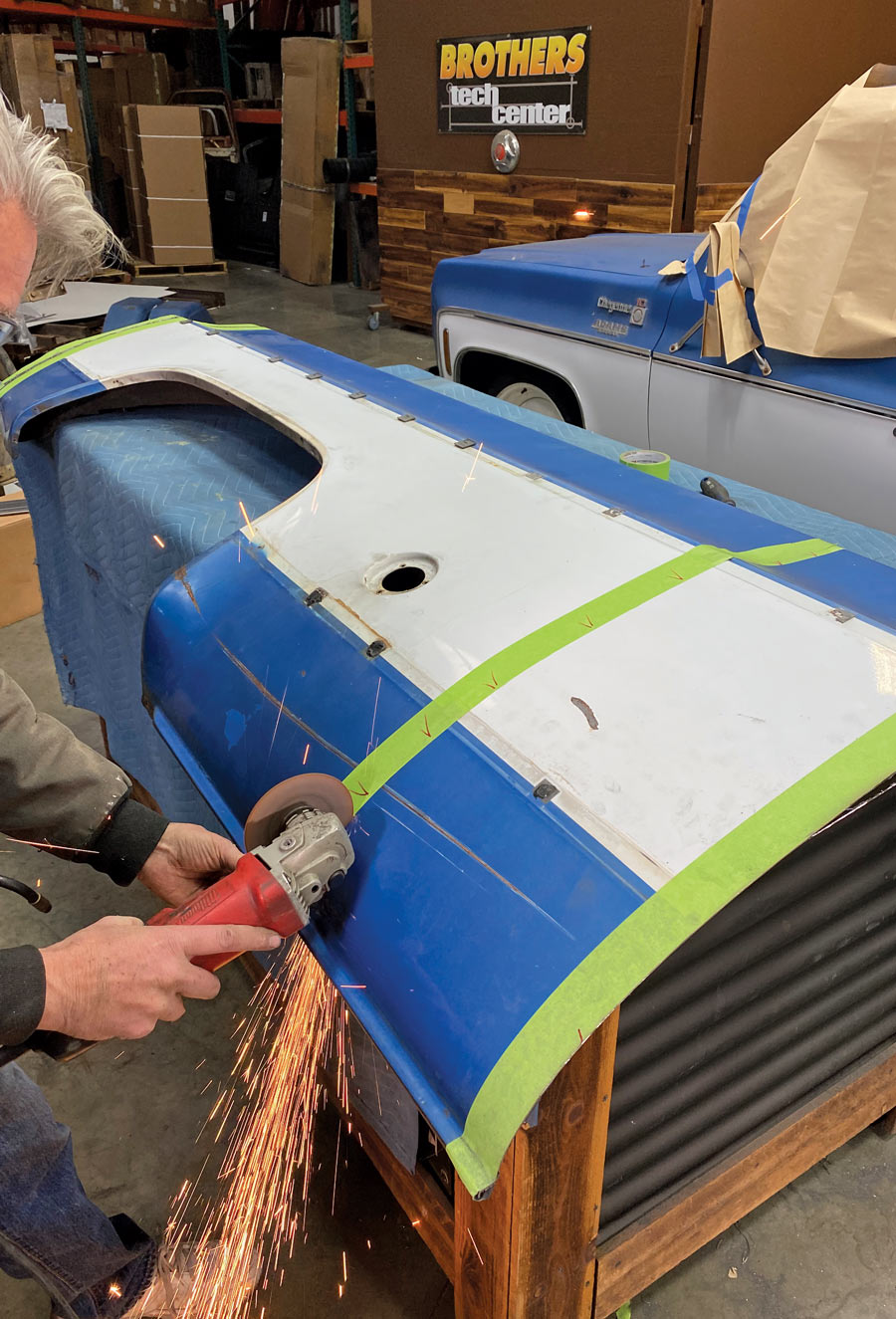
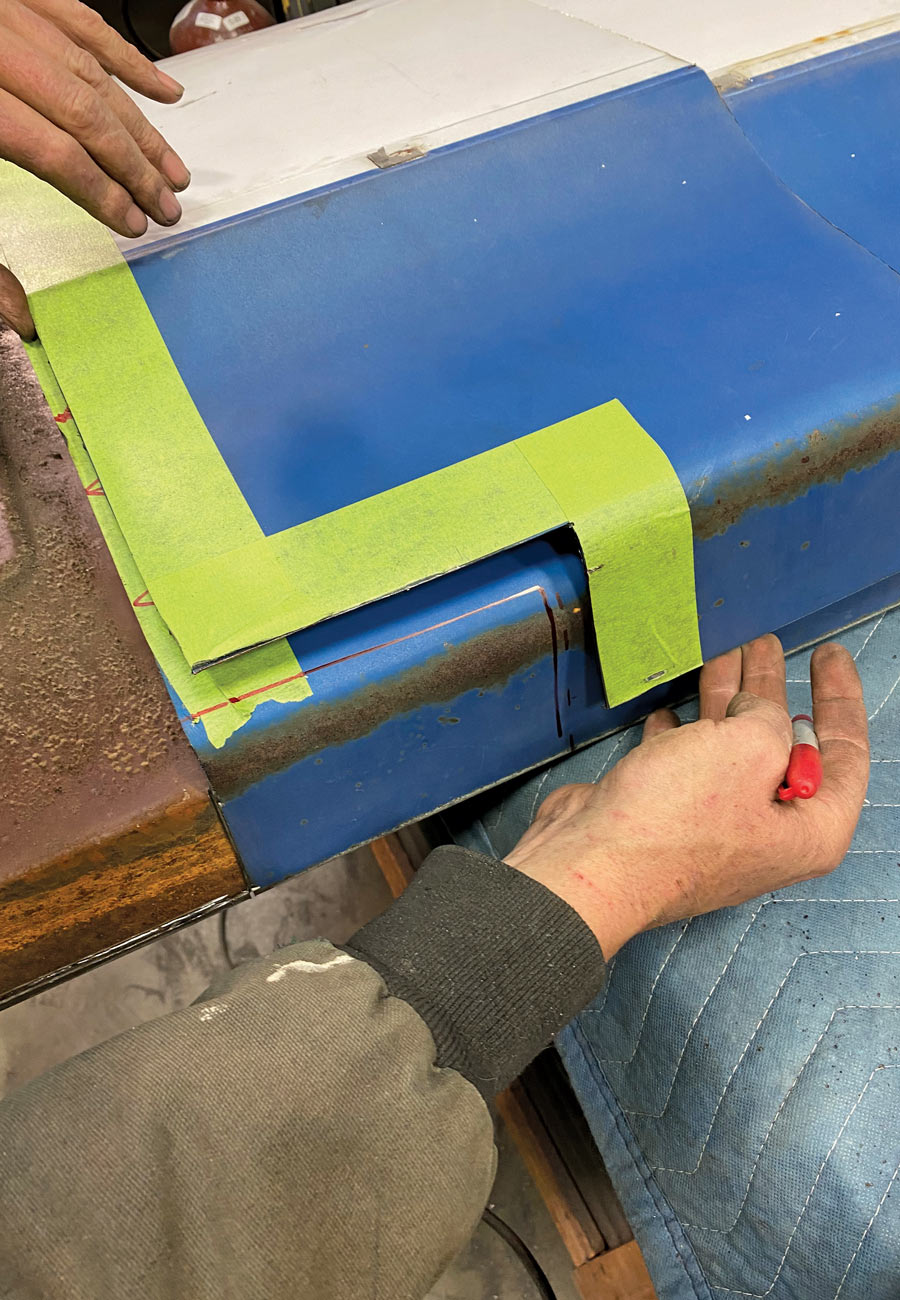
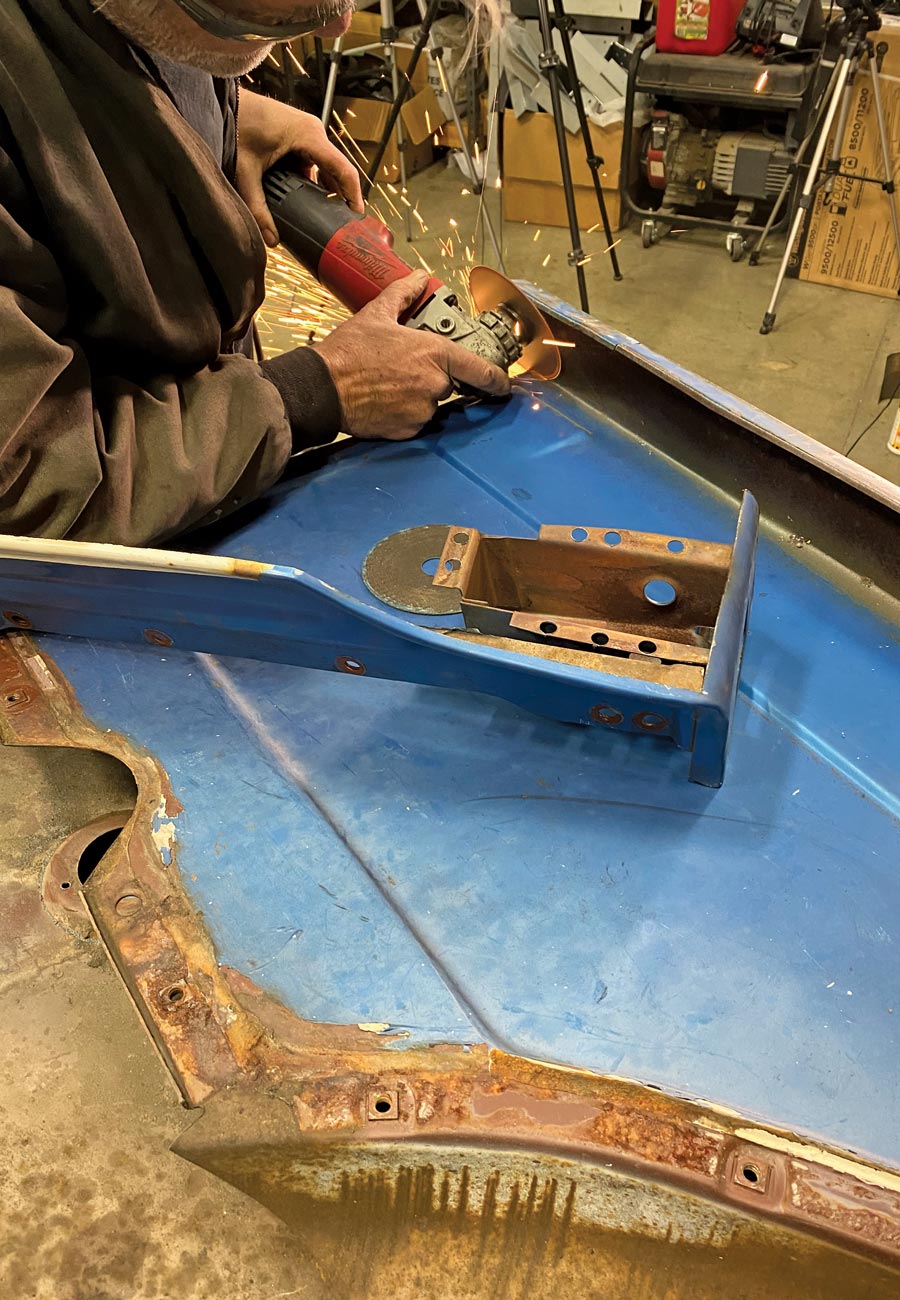
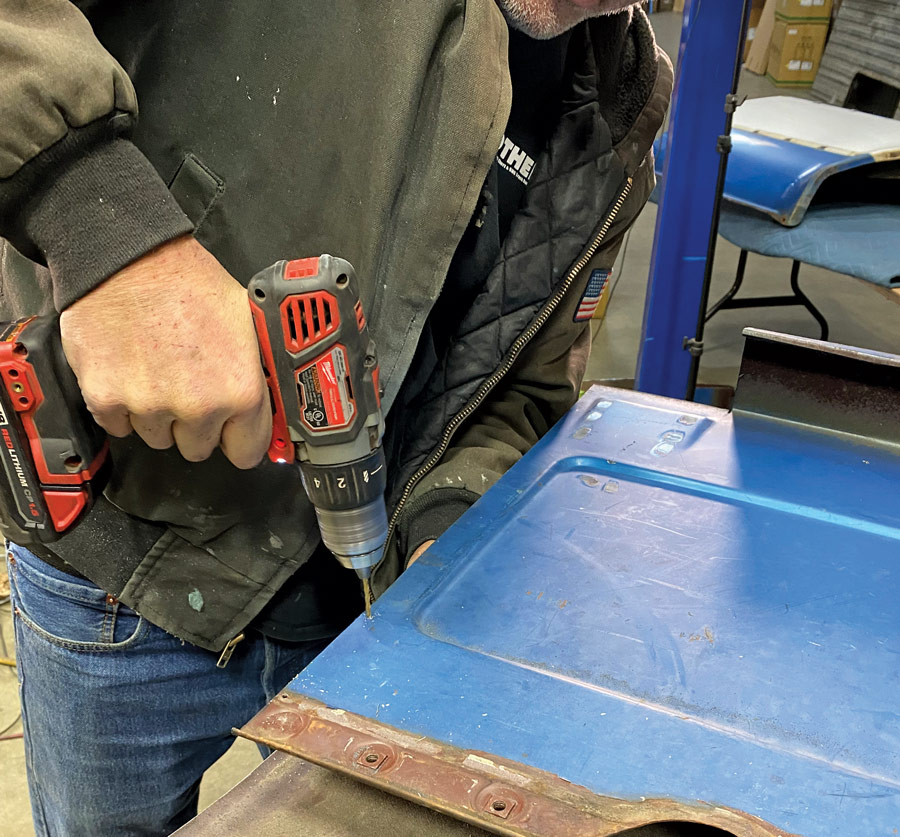
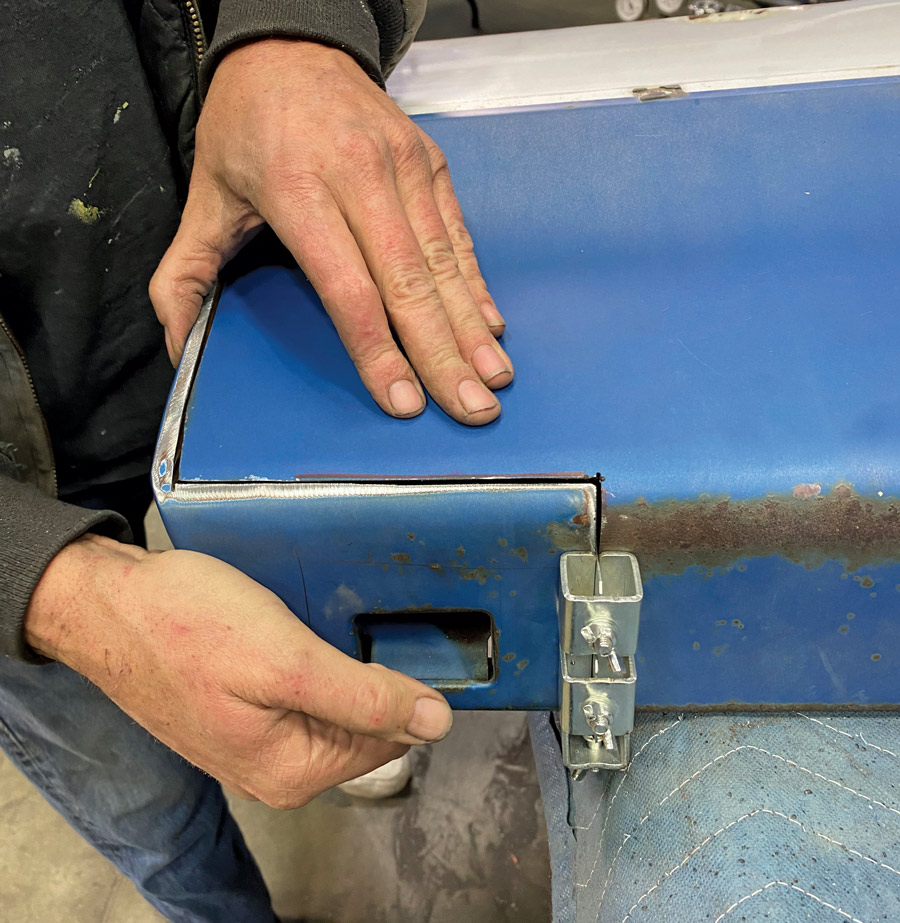
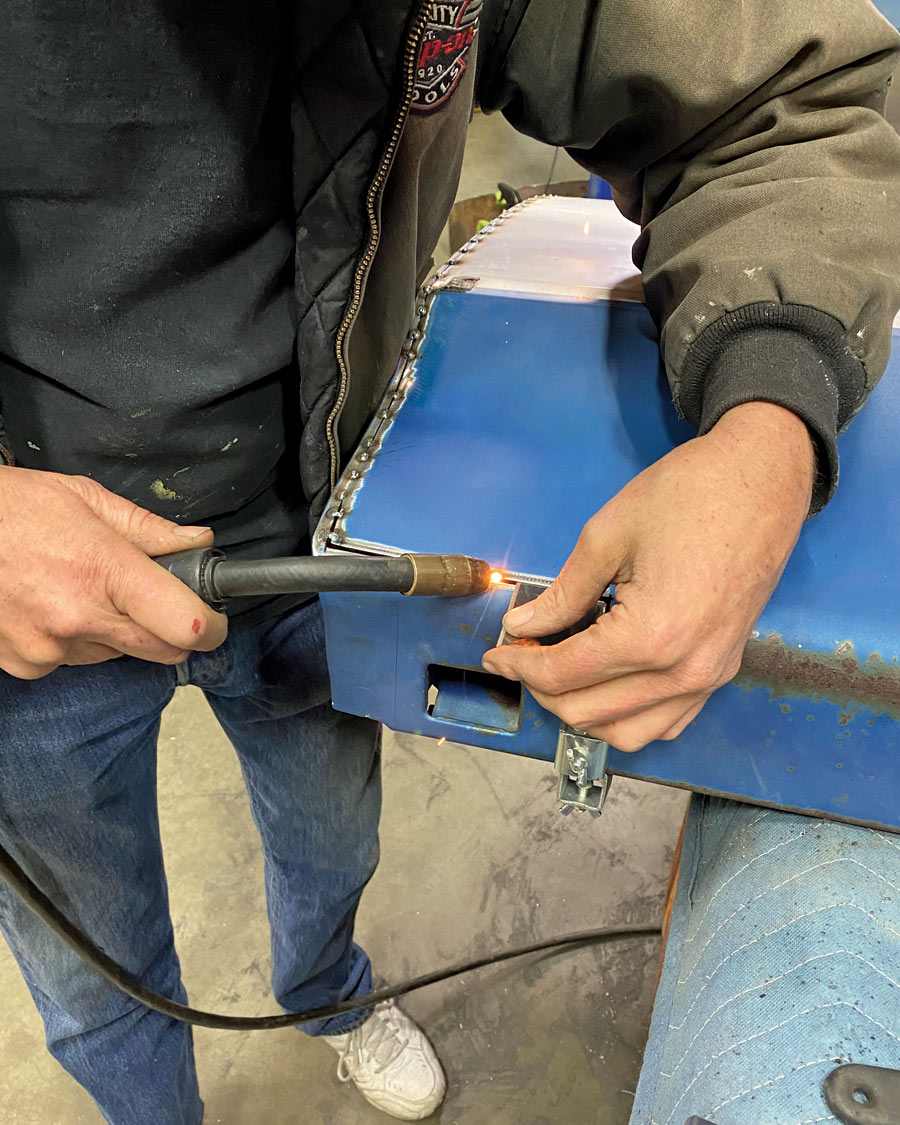
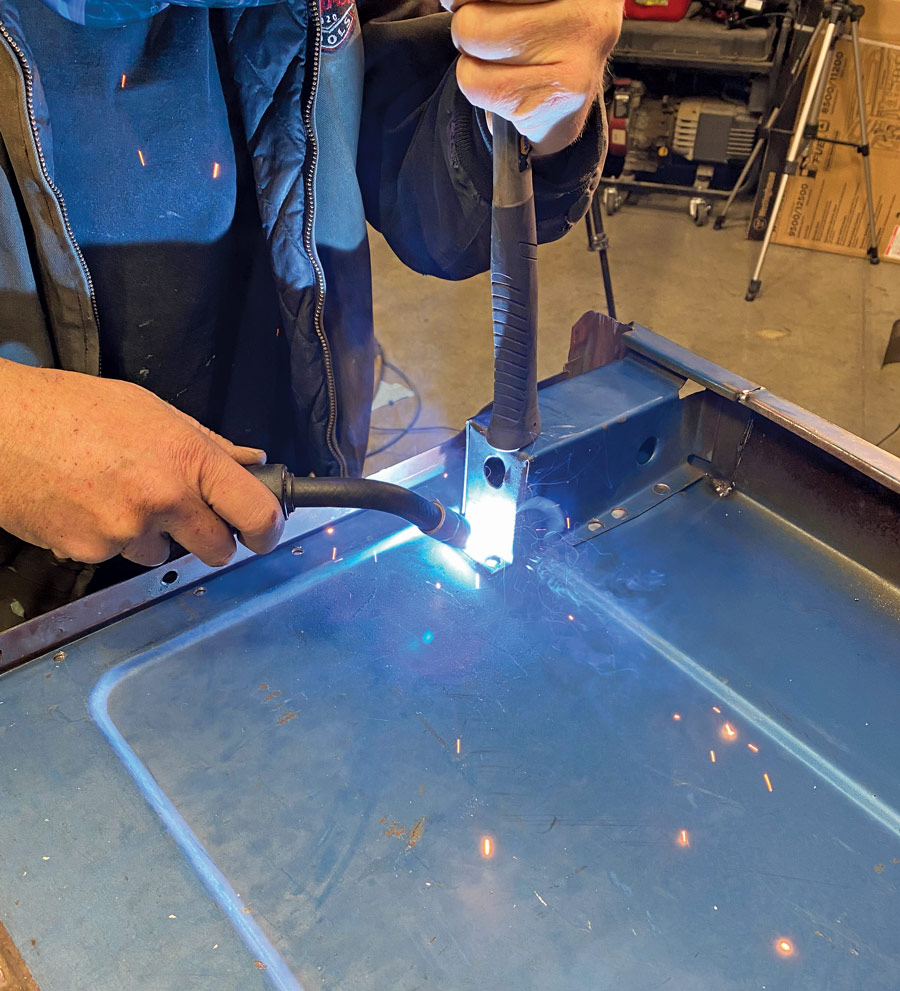
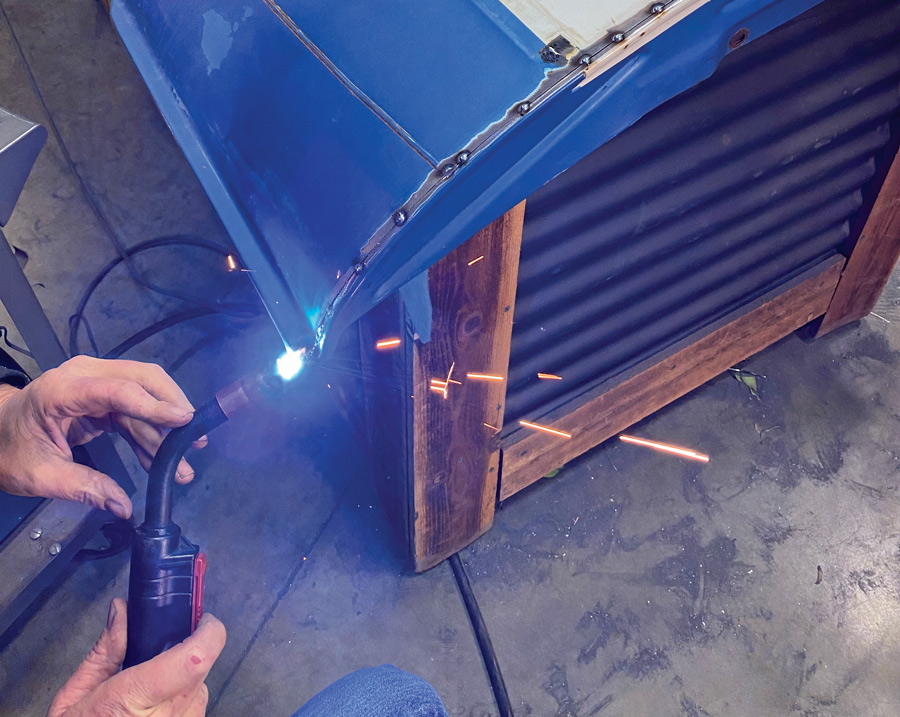
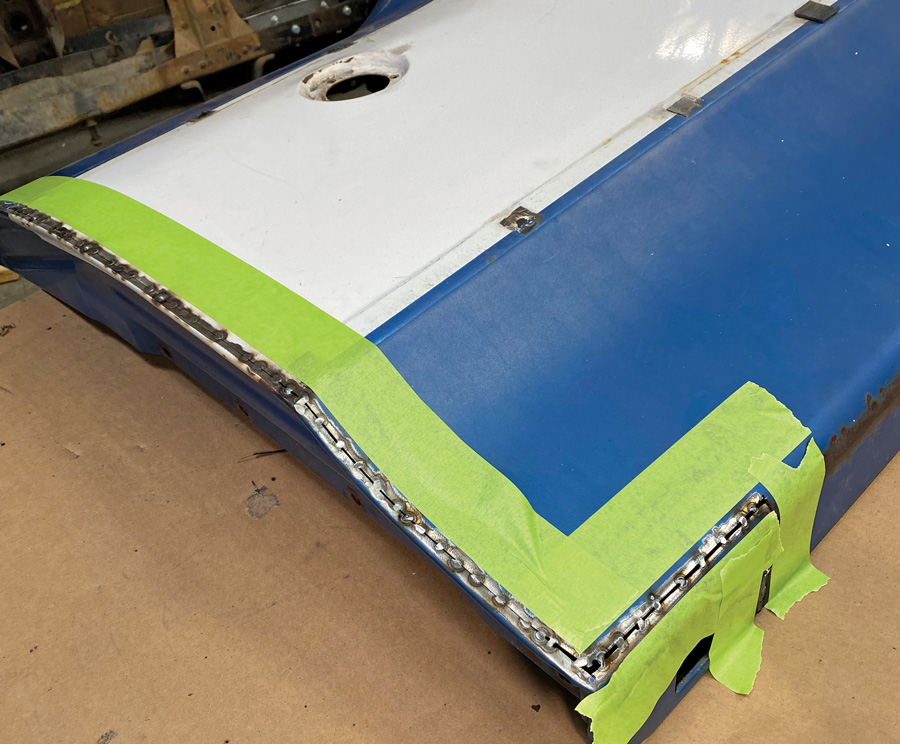
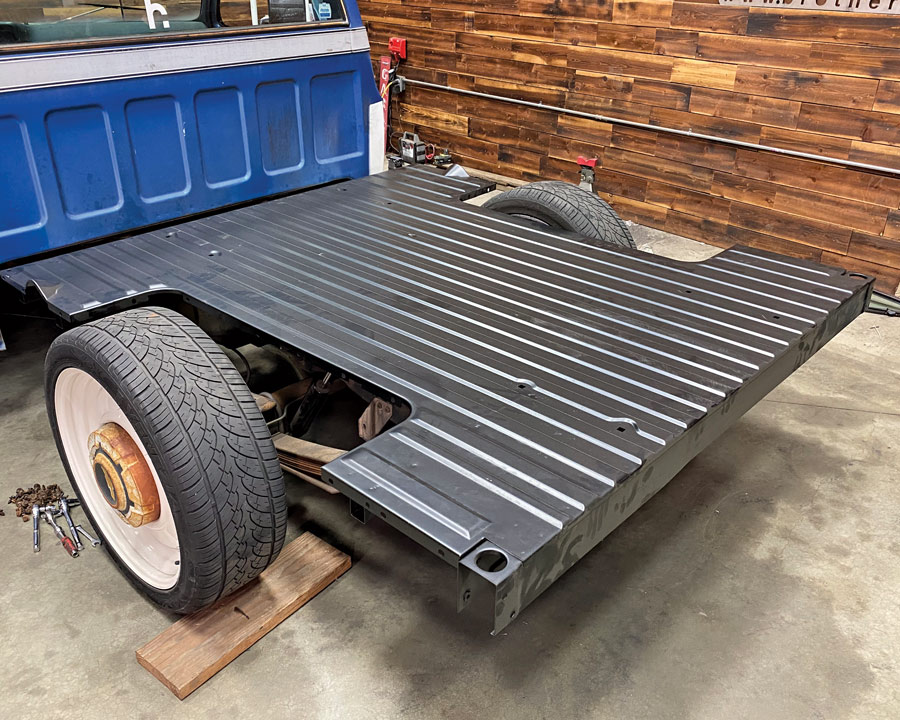
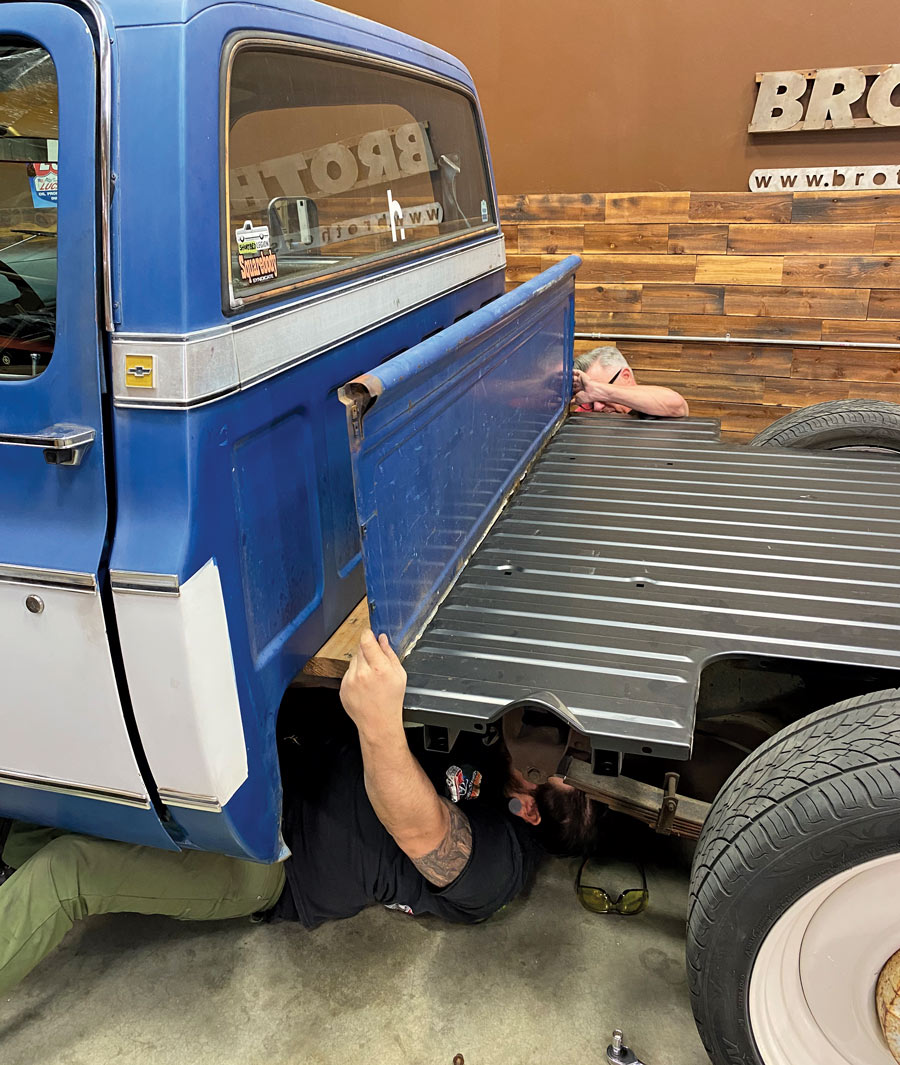
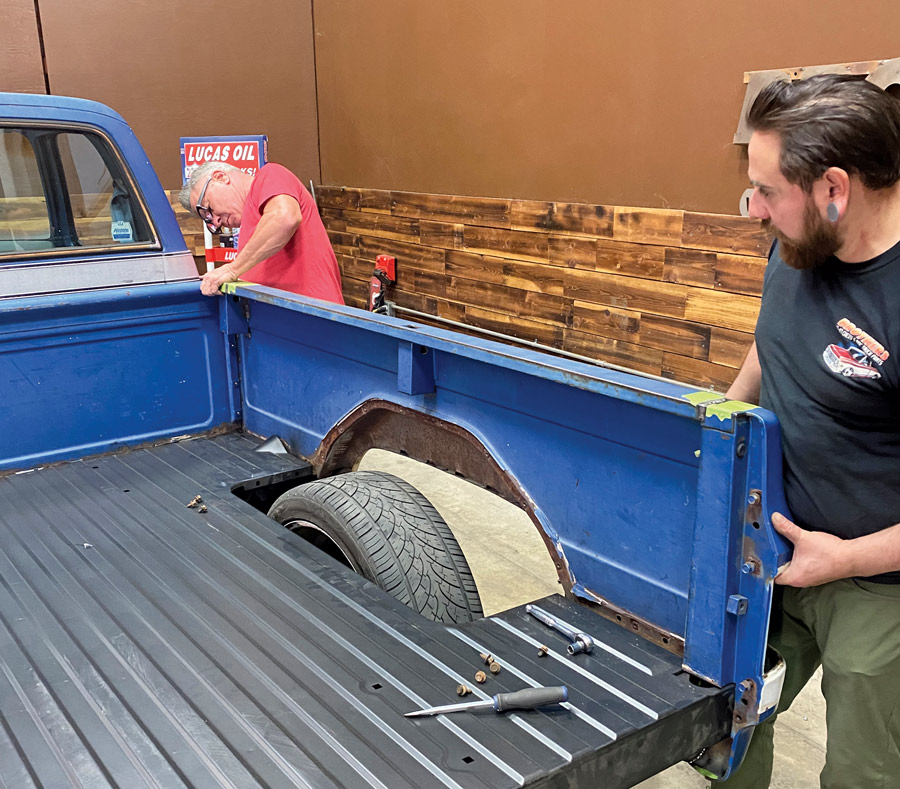
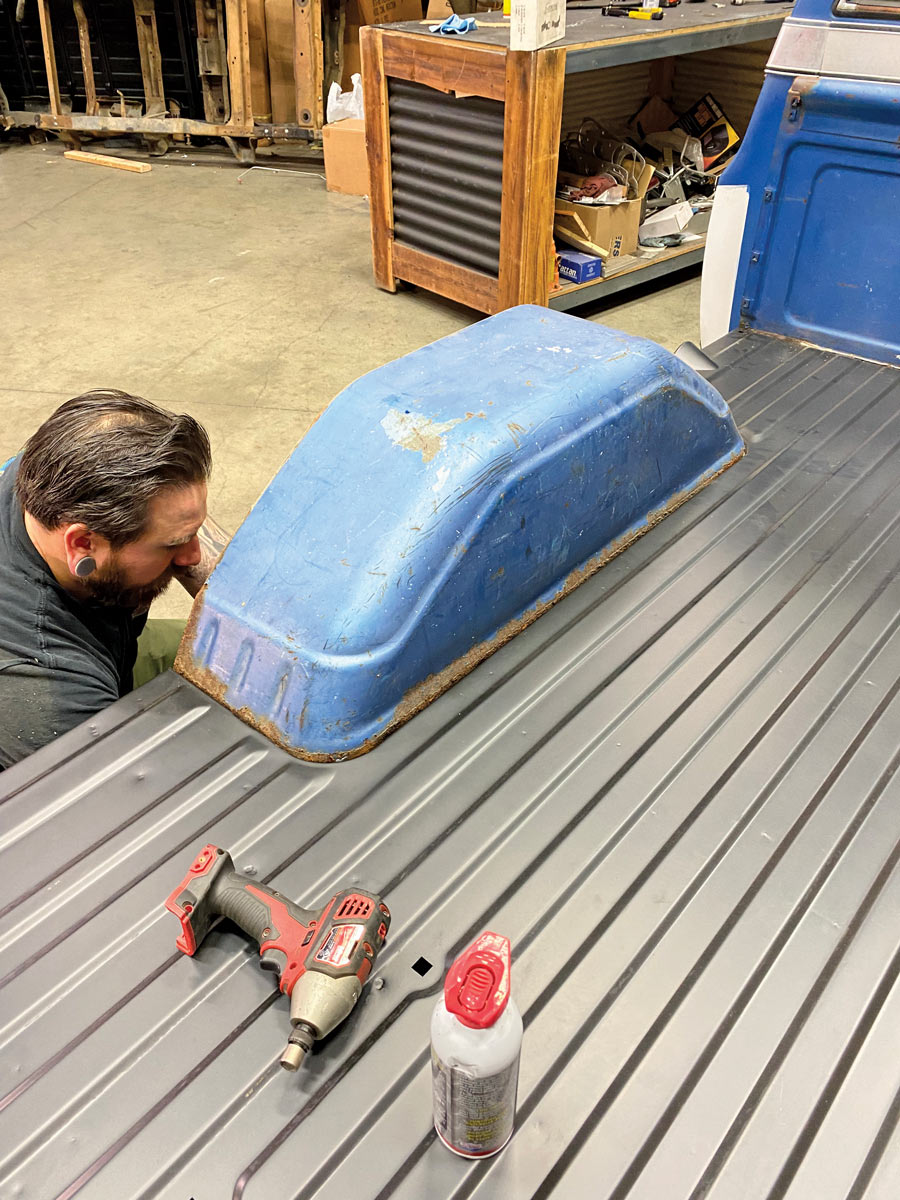
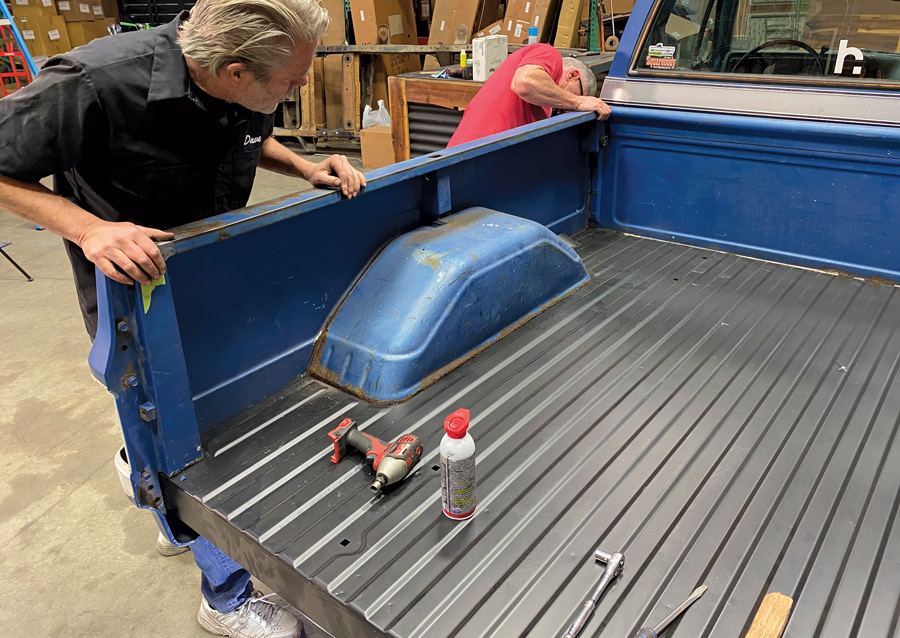
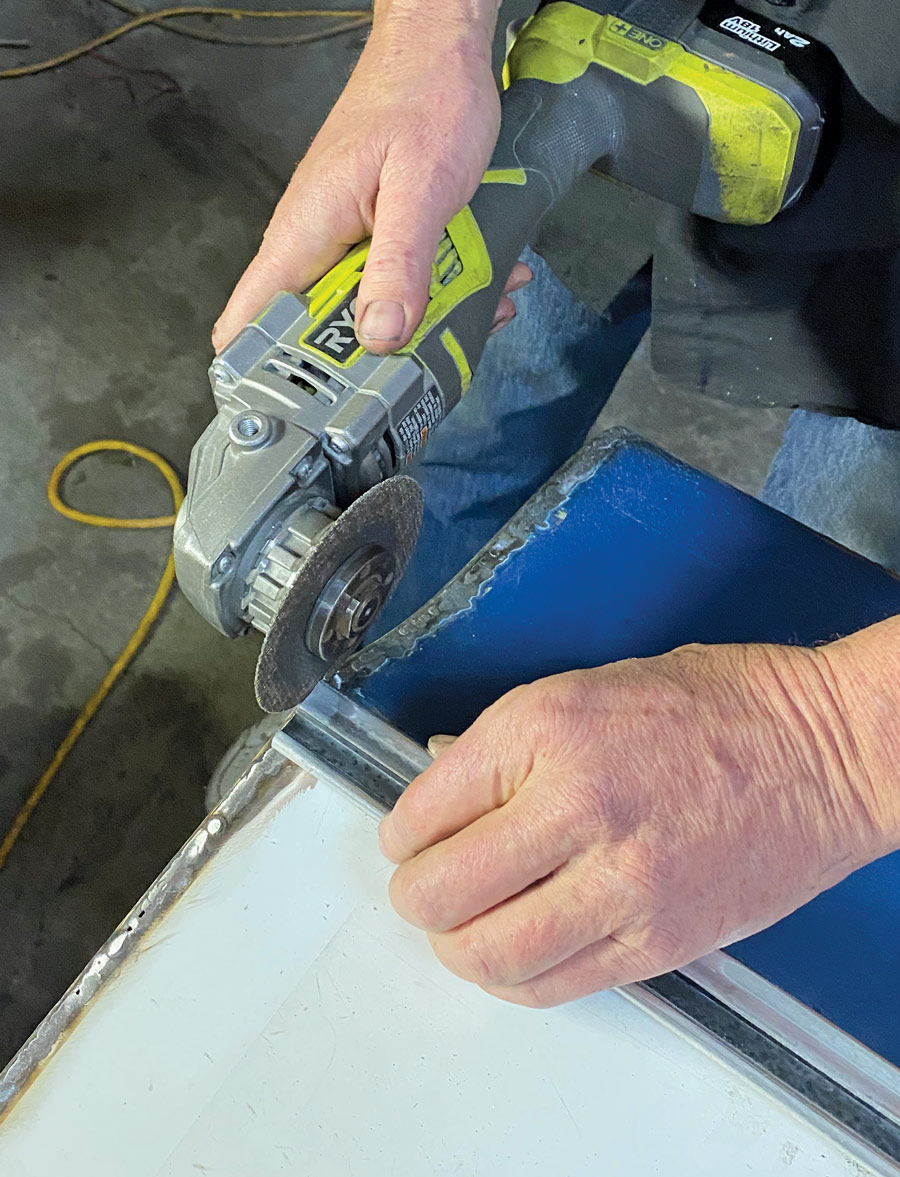
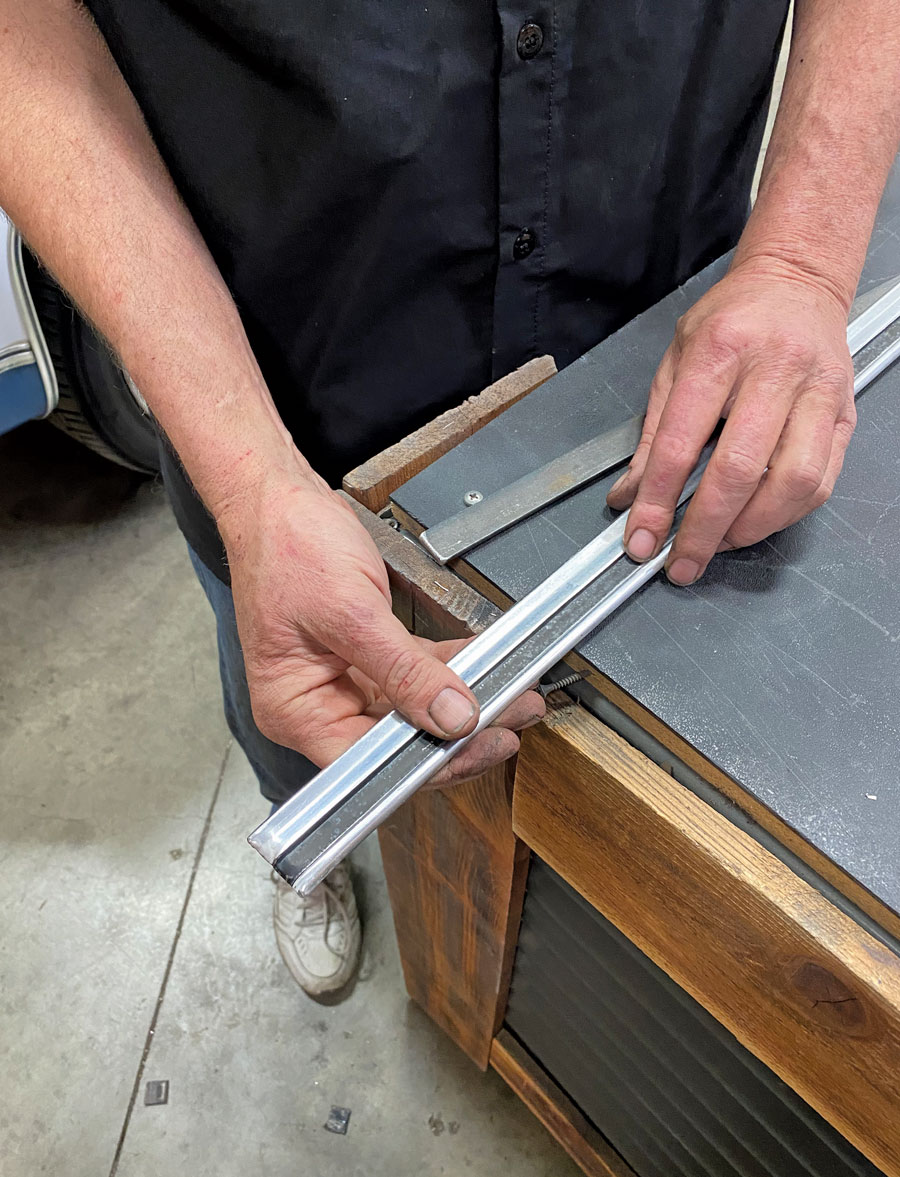
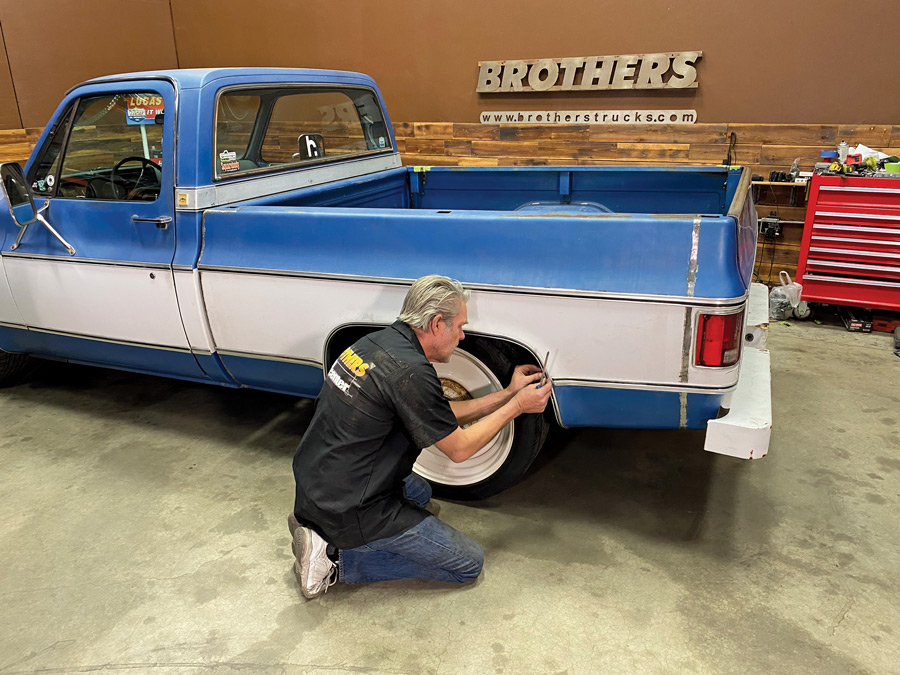
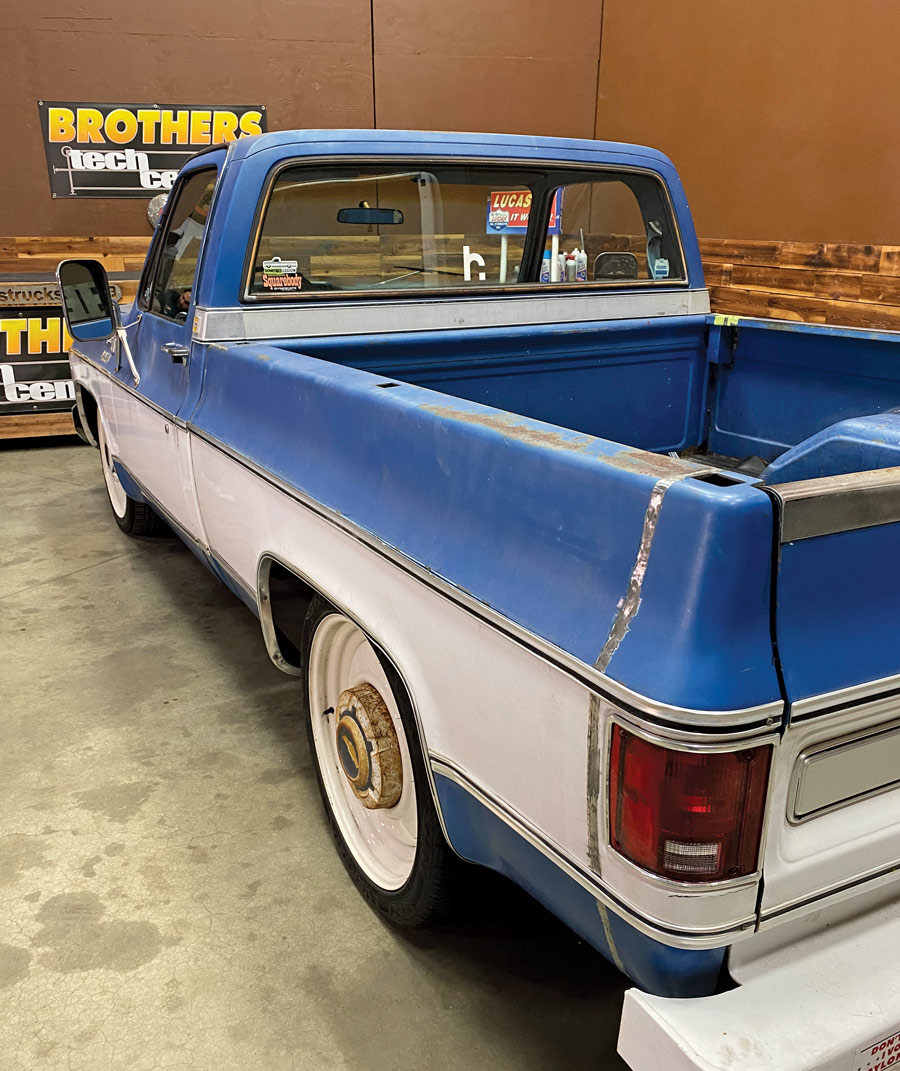
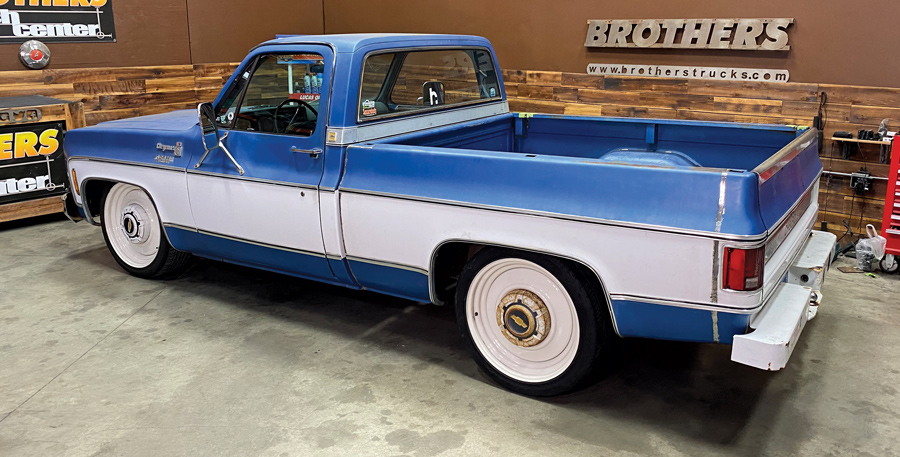
