


I-Beams for IFS

n 1948 Ford introduced their first generation of 1/2-ton pickups, the F-1. They were revolutionary in so far as they were no longer based on passenger car frames and suspension components like all Ford’s light-duty trucks that had come before. The second generation of the F-series trucks were produced from 1953-56. This series of trucks had been redesigned once again, the 1/2-ton versions were now identified as F-100s and 3/4-ton trucks were now F-250s. The third generation of Ford pickups from 1957-60 were treated to another face-lift. While several updates had been made to the chassis at this point, the same basic design could be traced back to the ’48 F-1; at both ends were solid axles with parallel semielliptic leaf springs—simple but effective.
The fourth generation of the F-series trucks were produced from 1961-66. Up to this point annual sheetmetal and trim changes were made for a fresh look, but the chassis remained much the same as those that had come before, that is until a big change was made midway in 1965. A completely new chassis was introduced that included Ford’s infamous twin I-beam front suspension. This layout used two I-beam axles, each anchored to the frame on one side of the frame with the wheel on the opposite side of the truck. The idea was the long individual axles would allow each wheel to act independently while maintaining the strength of a conventional single I-beam.
For the fifth generation of the F-series, from 1967-72, and the sixth generation, from 1973-79, there were styling changes and improvements in interior comfort but the twin I-beam front suspension remained in play. And to a great degree that suspension system is why ’65-79 Ford pickups have often been overlooked by early truck aficionados. Despite the fact that these pickups are good looking, the twin I-beam configuration was not one of Ford’s better ideas. These front ends had very little caster, so a common complaint was poor straight line stability and wandering on rough roads as a result of the camber change as the wheels moved up and down at the end of the individual axles. These front ends were also known to be hard on tires and could lay waste to a pair of shock absorbers in short order.
Although the Mustang II was forgettable, the front suspension will always be regarded as the best feature of those cars. The Mustang II had a surprisingly stout front end with bigger wheel bearings than the Chevy Nova clip swaps that were once popular. The ball joint and tie-rod end studs are the same size used on fullsize Fords and the front mount rack-and-pinion steering that makes room for virtually any engine. Given all that and the fact that it is easily adaptable to a variety of applications, it’s hard to find fault with a Mustang II suspension system.
CPP has gone to great lengths to make installing their IFS kit easy. Once the stock Ford axles, spring brackets, and crossmember are removed, CPP’s Mustang II crossmember and upper control arm brackets bolt in place, with no welding required. By using factory holes locating the new crossmember and upper control arm brackets is foolproof—and only six additional holes have to be drilled to complete the installation.
Along with the beautifully crafted main crossmember and control arm brackets the CPP kit includes a new manual or power rack-and-pinion steering gear, stock or dropped spindles, new coil springs and shocks, 11.75-inch disc brake package, black powdercoated tubular control arms, 3/4-inch sway bar with billet mounts, and all the required hardware. Also available with this kit are CPP’s unique FitRite adjustable engine mounts to suit a variety of Ford engines as well as Chevy LS and LT V-8s. For those who want to run larger wheels, bigger brakes, and suspension adjustment capabilities, CPP offers a number of upgrades to the basic IFS kit that include Corvette-style spindles and hubs, 13-inch brake kit, and coilover springs and shocks. Additionally, this spindle and brake combination comes with spacers that allow the tread width to be reduced by 1/4 or 1/2 inch per side.
Ford pickups with twin I-beam suspension are often overlooked by classic truck enthusiasts because front suspension modifications have been seen as difficult to accomplish satisfactorily, but that has changed. CPP’s bolt-in Mustang II front suspension kit is the quick-and-easy way to swap those twin I-beams for IFS and gain the benefits of a smoother ride, better handling with the road feel of rack-and-pinion steering, along with the cool look a lowered ride height provides. There’s even more to come—CPP has more upgrades for fans of Ford’s iconic F-series trucks that we will reveal soon.
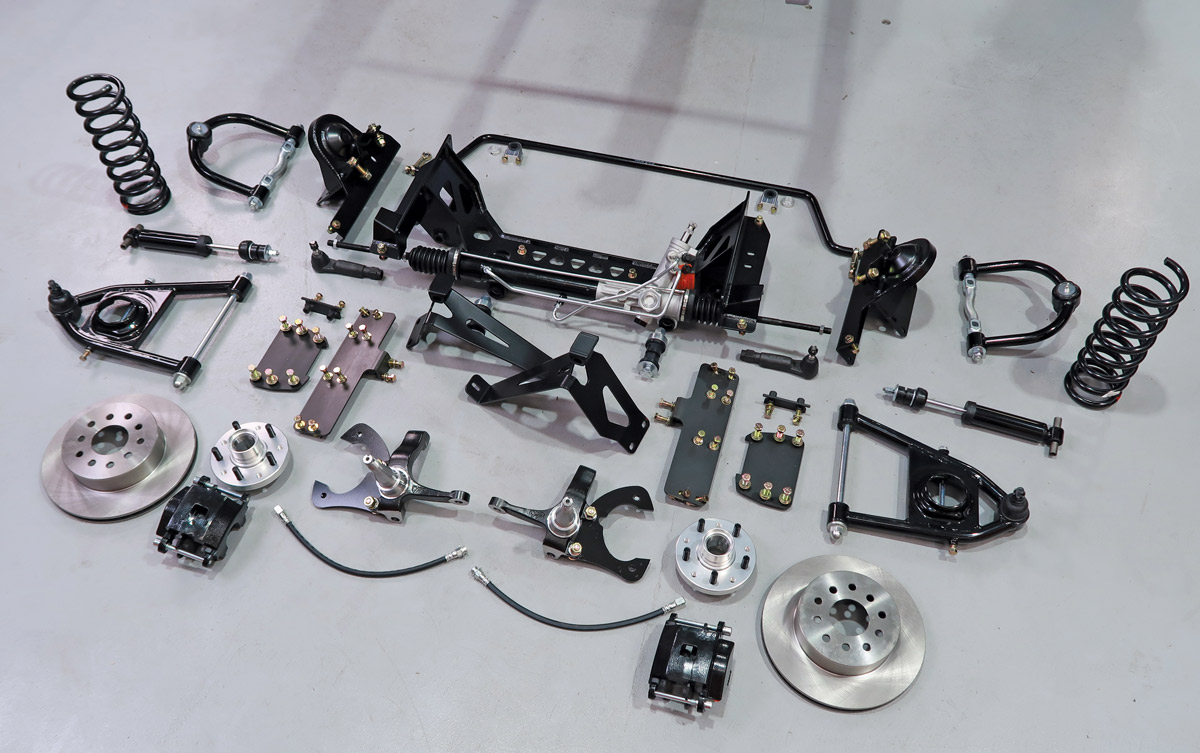
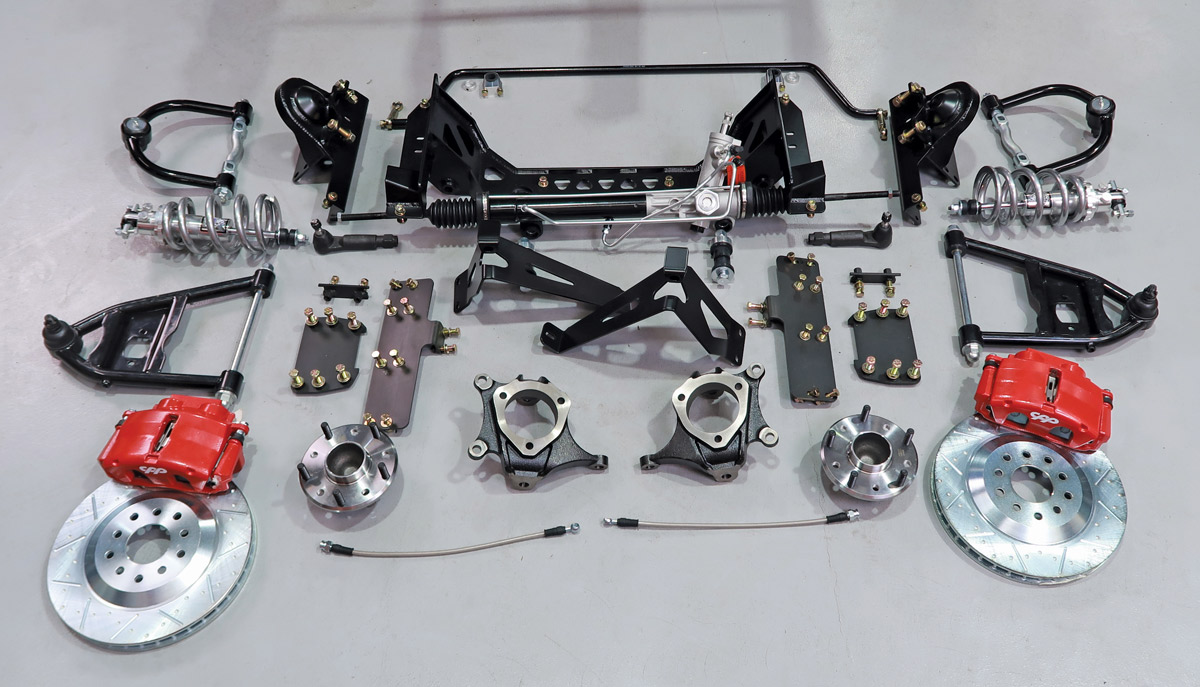
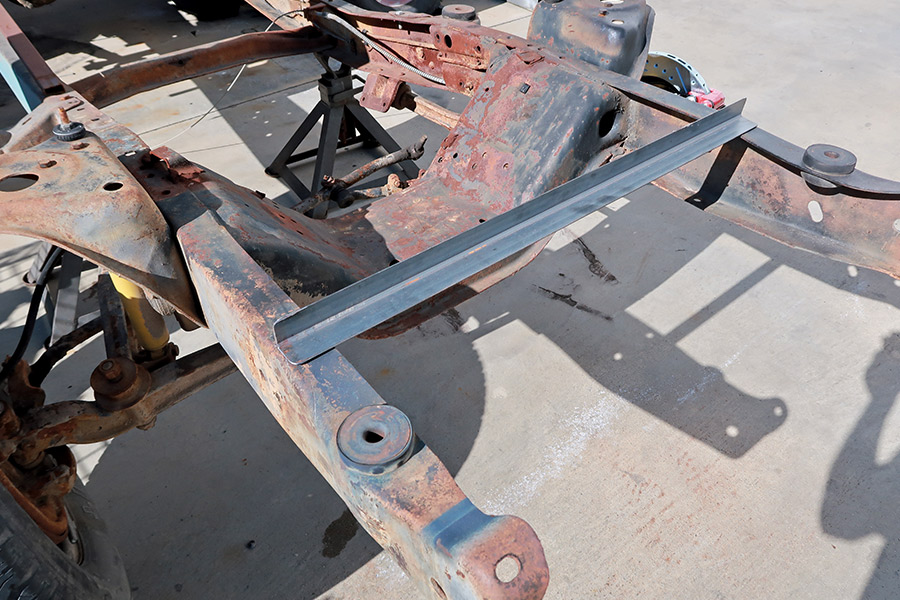
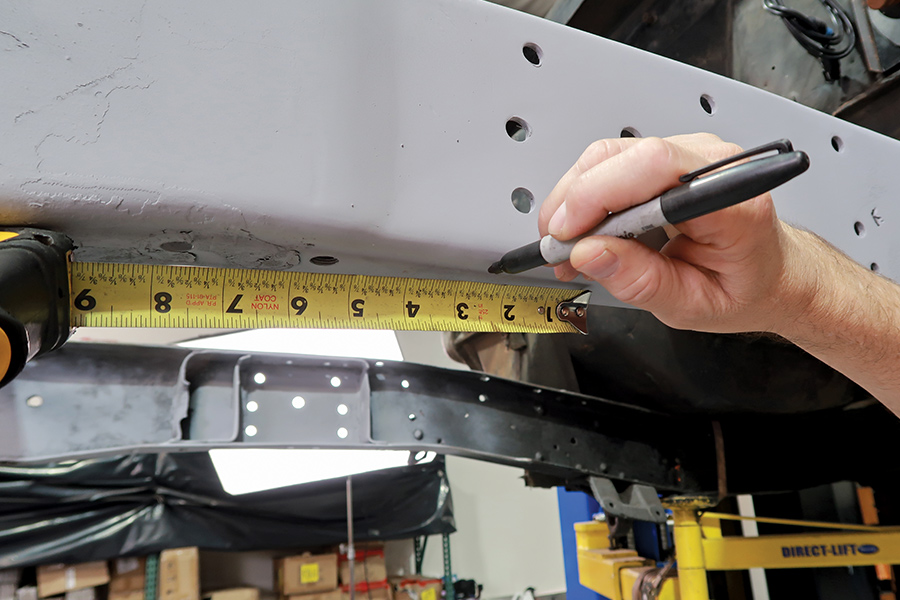

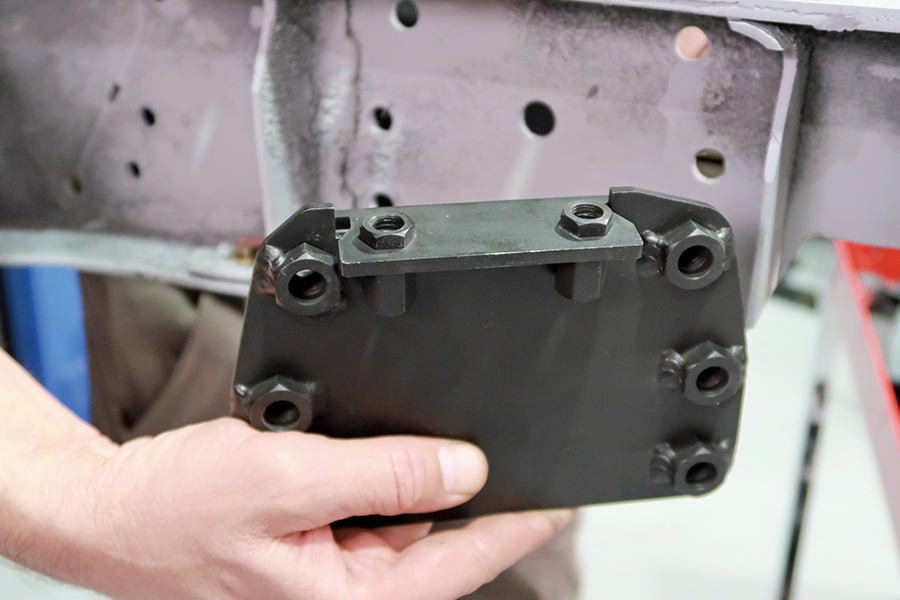

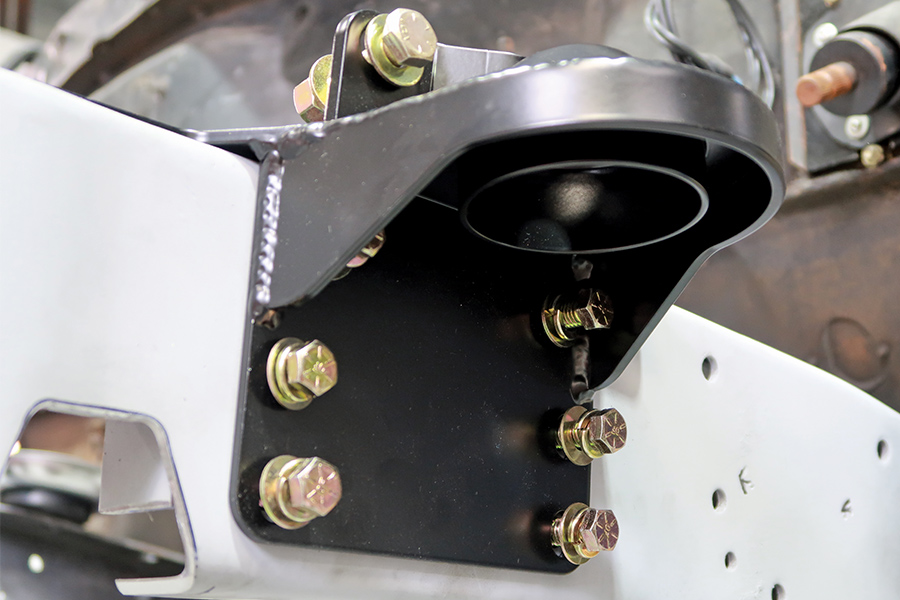
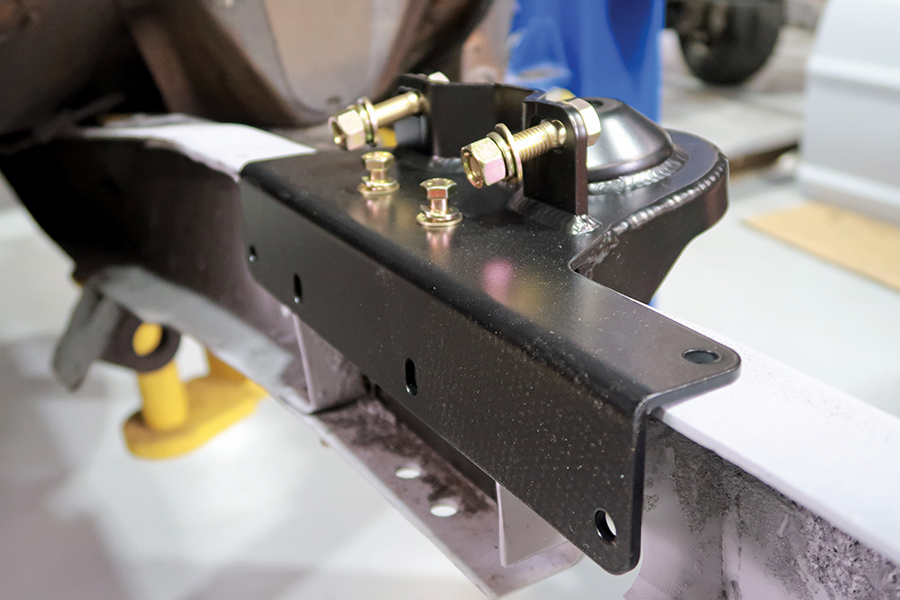


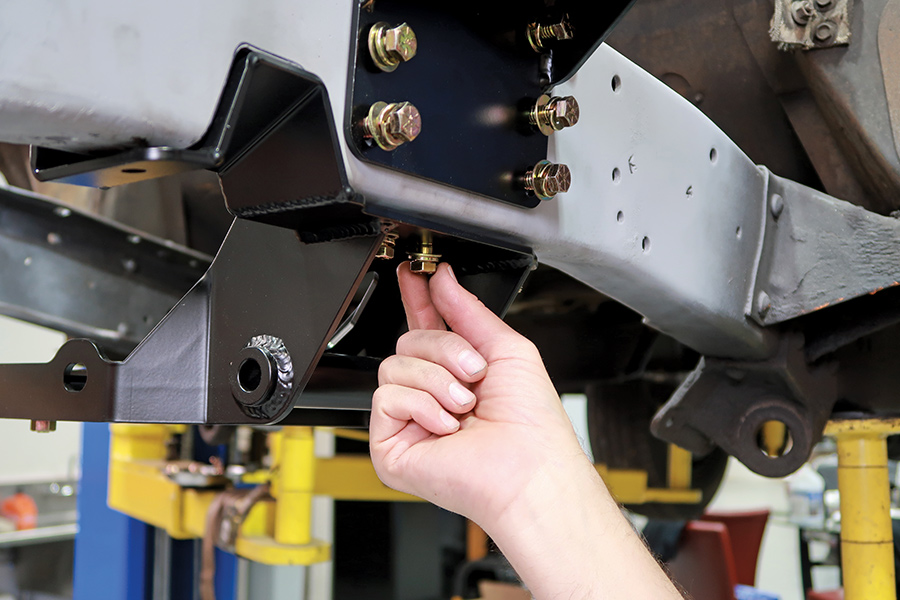
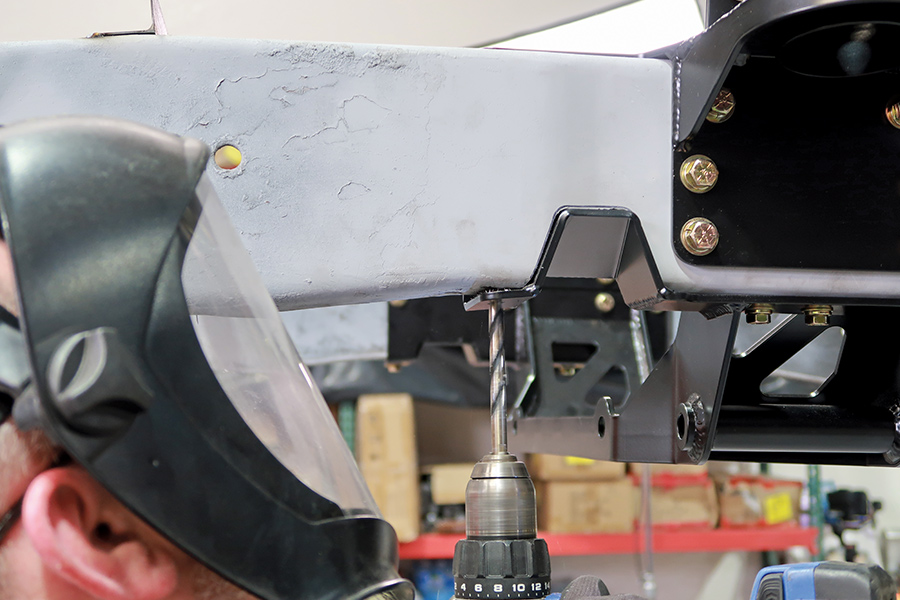




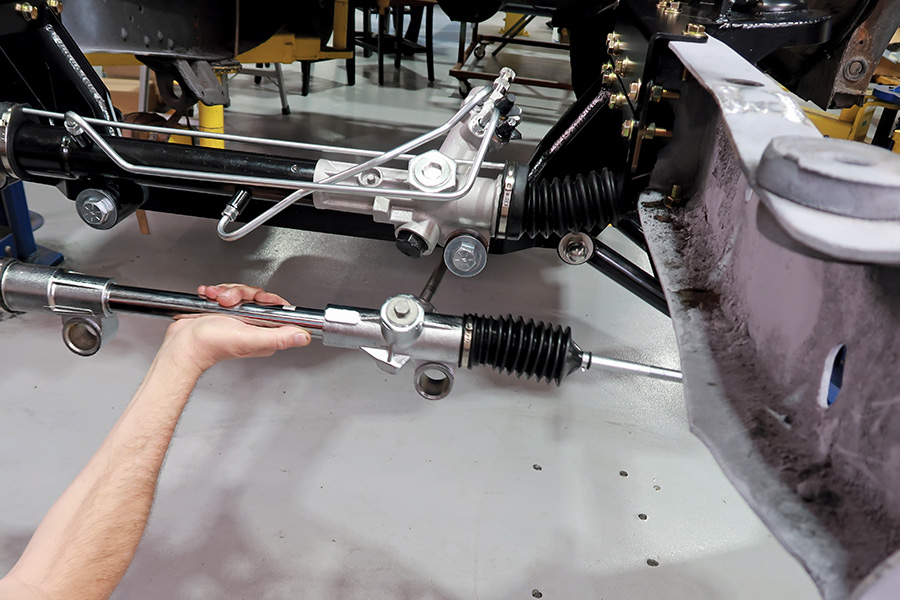

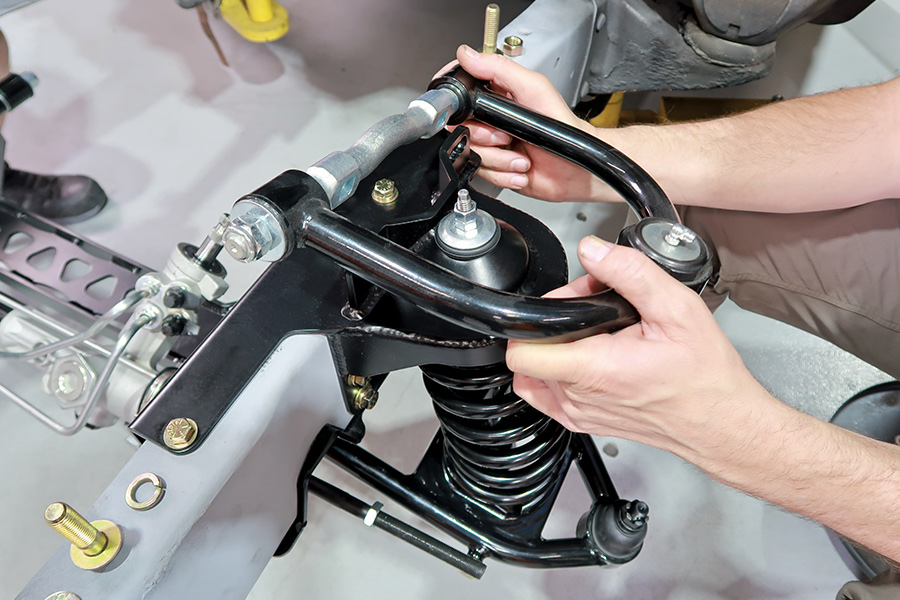





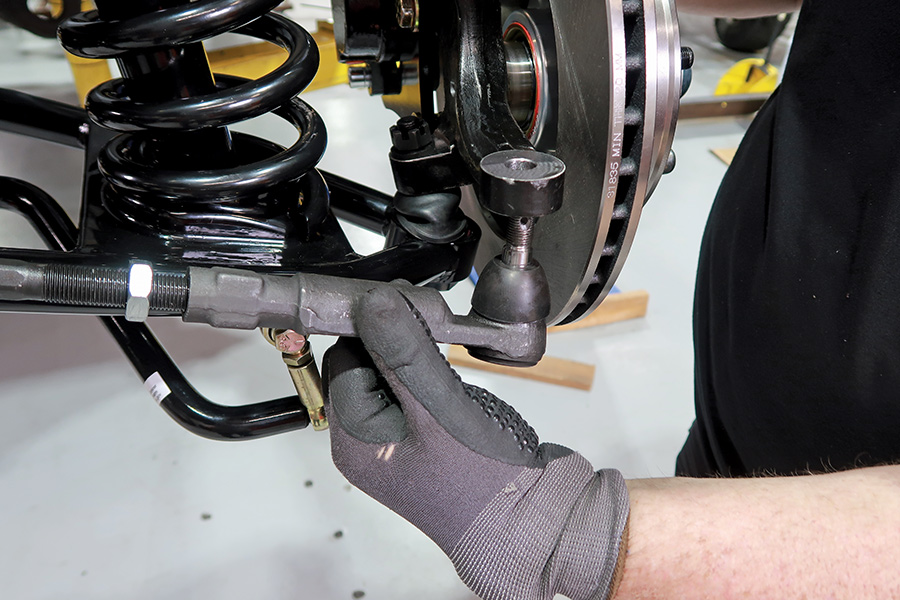
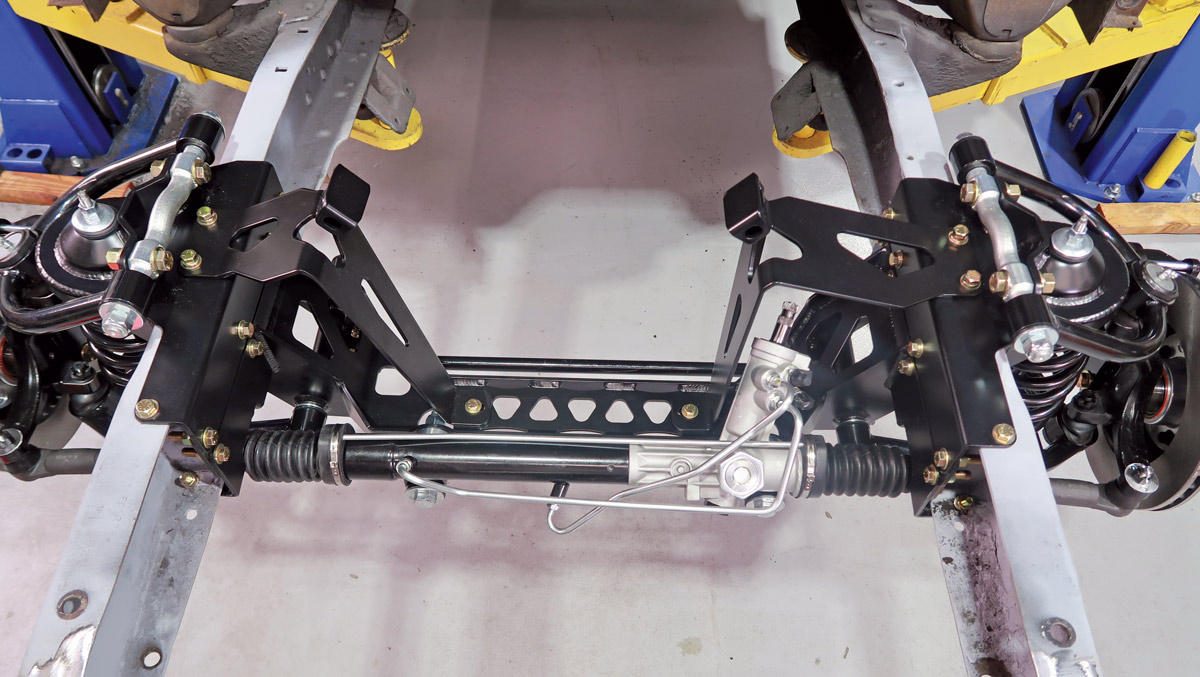
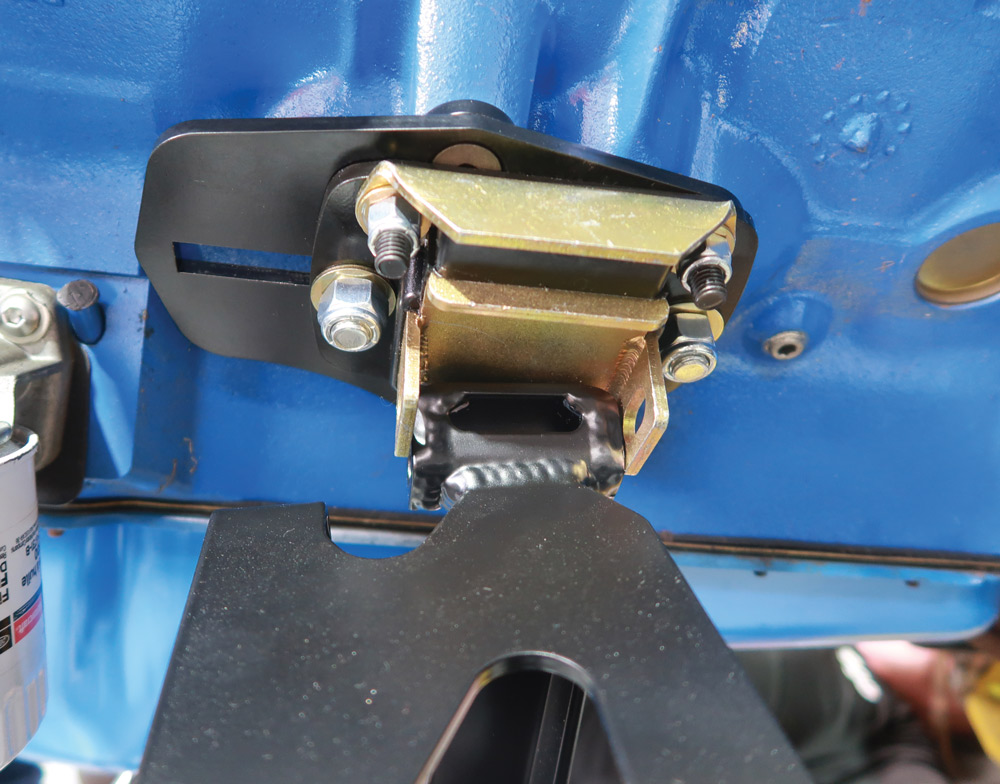
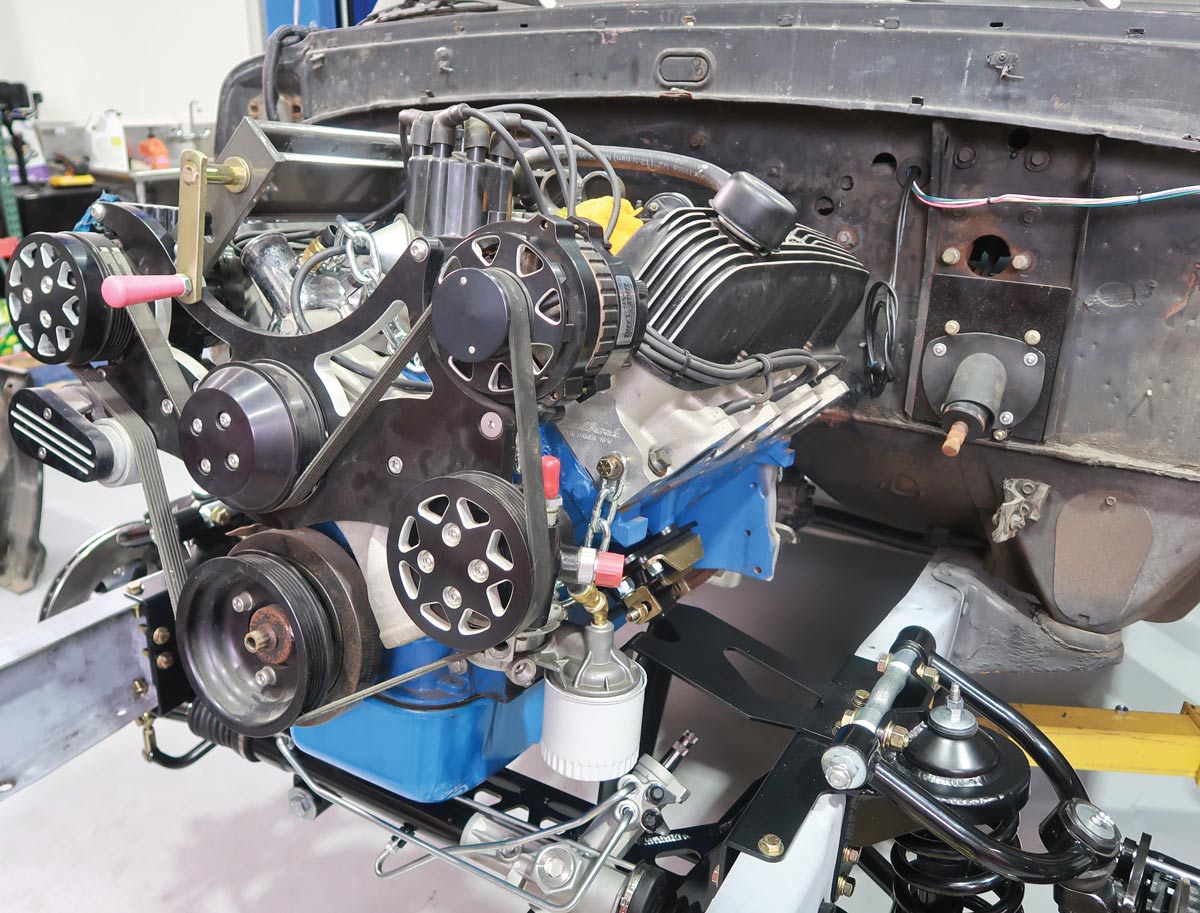
