


his saga started not long after our good friend, Paul Willis, announced he had unequivocally finished his last project truck. Shortly thereafter Willis brought home a 1954 Ford F-100 that he claimed would really be his last project.
Like many trucks its age, this latest acquisition had undergone several modifications—the most notable being the once-popular installation of a Volare transverse torsion bar front suspension. This swap included a failed attempt at adding a rack-and-pinion steering gear of unknown origin and a pair of crudely fashioned motor mounts. It all had to go.
As was often done with such installations, the bottom lips of the Ford’s framerails were cut away, then the complete Mopar crossmember was welded in place. That meant to install a more suitable independent front suspension system the Volare crossmember would have to be cut out, after which the framerails would require major repairs.
When it comes to selecting a replacement IFS for the Ford there are a variety of kits to choose from, but one of the most intriguing is Speedway Motors’ G-Comp Universal front suspension system. Not another version of the Pinto/Mustang II design that’s been done over and over, the G-Comp Pro Touring style frontend is a complete assembly based on a subframe made from 2×3-inch, 0.120-inch wall tubing. Available in 56-, 58-, 60-, and 62-inch track widths, 56- and 58-inch versions are 29.75 inches wide at the outside of the framerails, while the 60- and 62-inch versions are 33.75 inches at the outside of the rails.
The G-Comp suspension comes with Speedway’s exclusive G-Comp uprights that use Corvette-style cartridge spindles. Engineered for optimum handling and vastly improved control, the G-Comp’s suspension geometry provides optimized camber gain for better handling and no bumpsteer. To provide the ultimate in suspension tuning options camber adjustments are made with shim plates and caster changes are made with inserts in the upper cross shafts—both are more secure than the slotted adjustment holes often found in Mustang II kits. Also included in the G-Comp IFS kits are a power rack-and-pinion steering and a 1¼ inch od splined sway bar (coilovers are sold separately).
The G-Comp front suspension is designed to use C6 Corvette-style brakes, such as the Wilwood PN 835-1408921 with 13-inch rotors and Superlite 6R six-piston calipers. Another option is Speedway’s Economy disc brake kit (PN 3502001) that uses their own GM metric-style calipers and Pro-Lite brake rotors. It will work with 15-inch steel wheels and 16-inch and larger aftermarket wheels.
With the Volare frontend removed, we simply cut off the damaged portion of the Ford’s frame then slipped the Speedway subframe inside the remaining portion of the ’rails. With the subframe in place it was thoroughly welded to the original frame and then the areas where the two were joined were boxed. In our case the only additional modifications were to add portions of rectangular tubing to the front of the subframe to provide mounts for the stock bumper.
Speedway’s G-Comp suspension is the ideal update for the front suspension under almost any classic truck. For us it fixed our fouled up frame and provided our F-100 with a truly state-of-the-art suspension system—we call that a win on both counts.
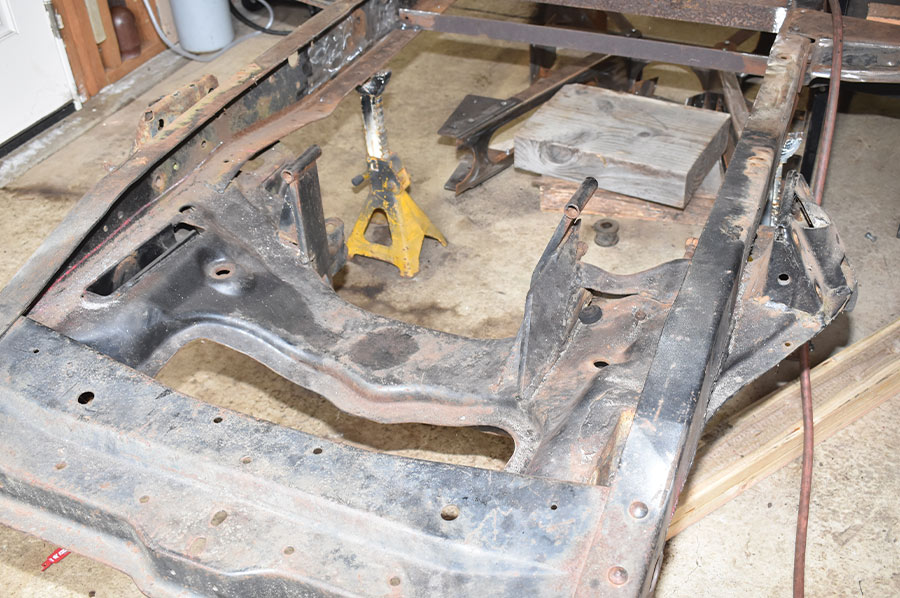
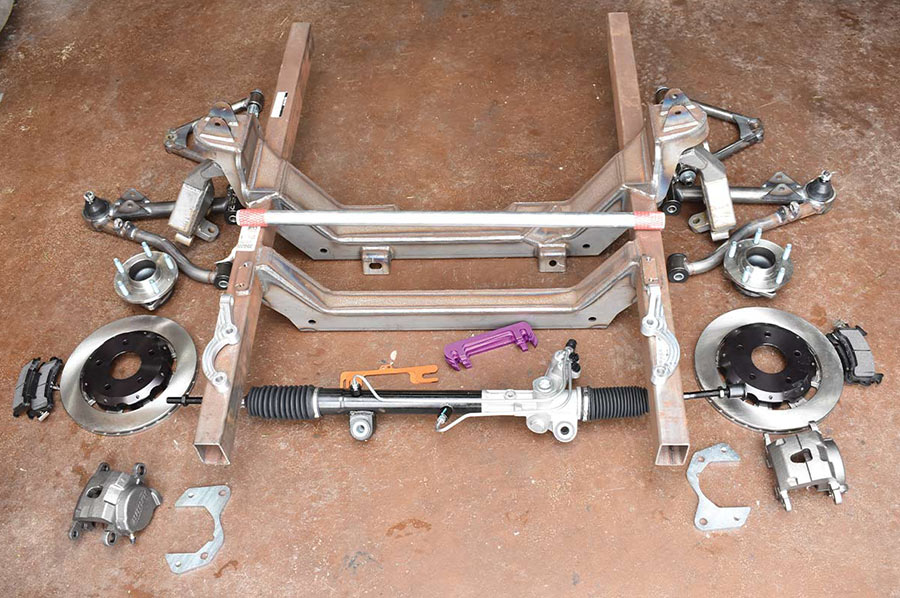
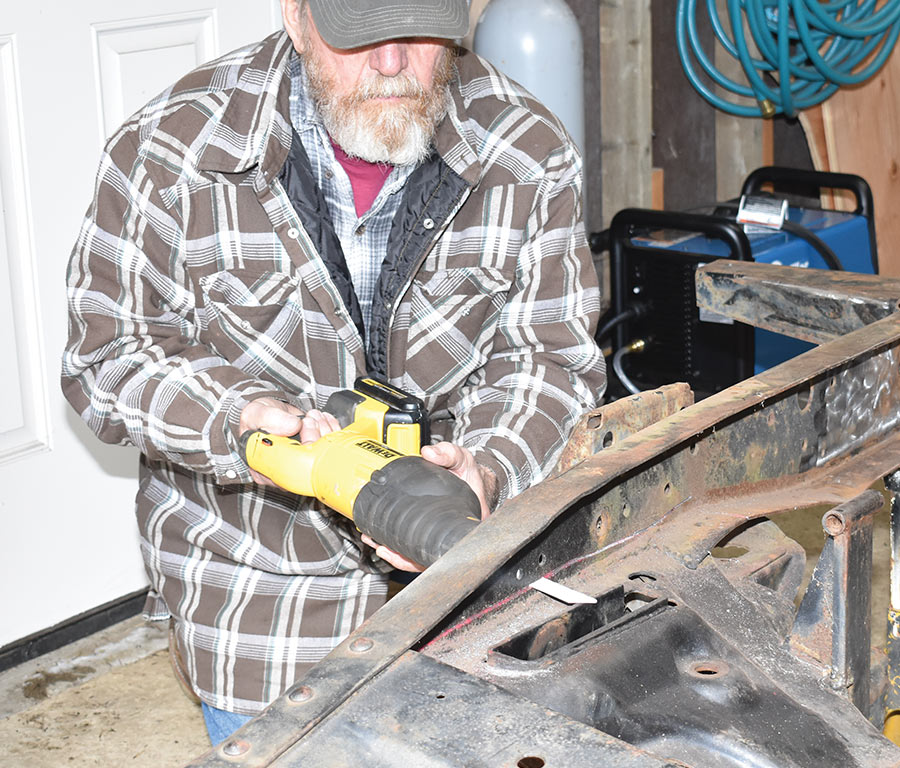
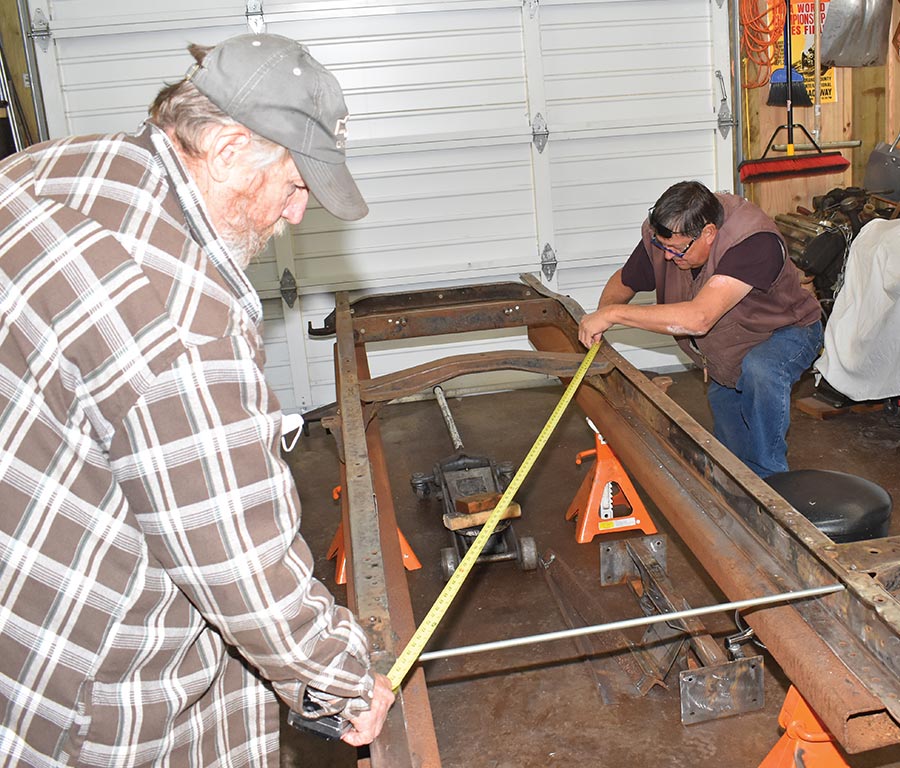
4. With the frame resting on leveled lengths of heavy steel tubing, a pair of Pauls (Willis on the left and Wilson on the right) measured it diagonally from several points. Satisfied the frame was “square,” it was clamped to the tubing that acted as a makeshift jig.
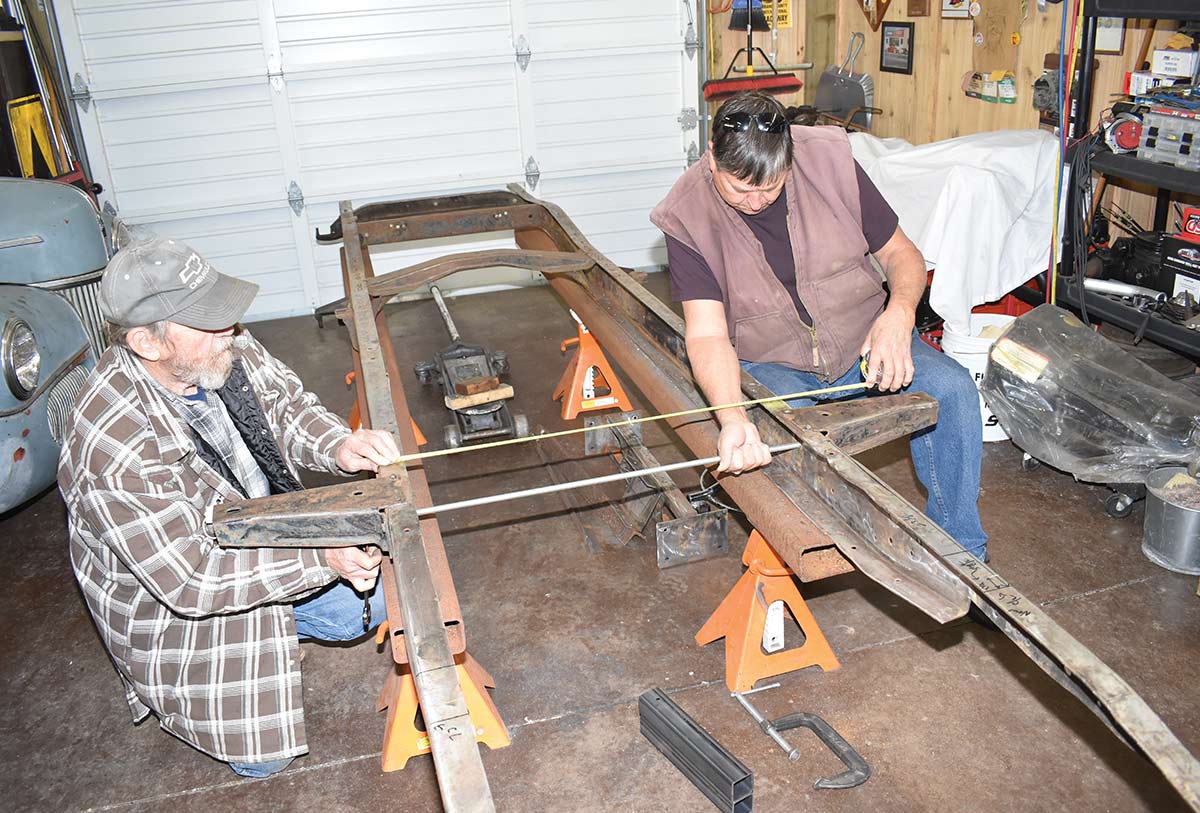
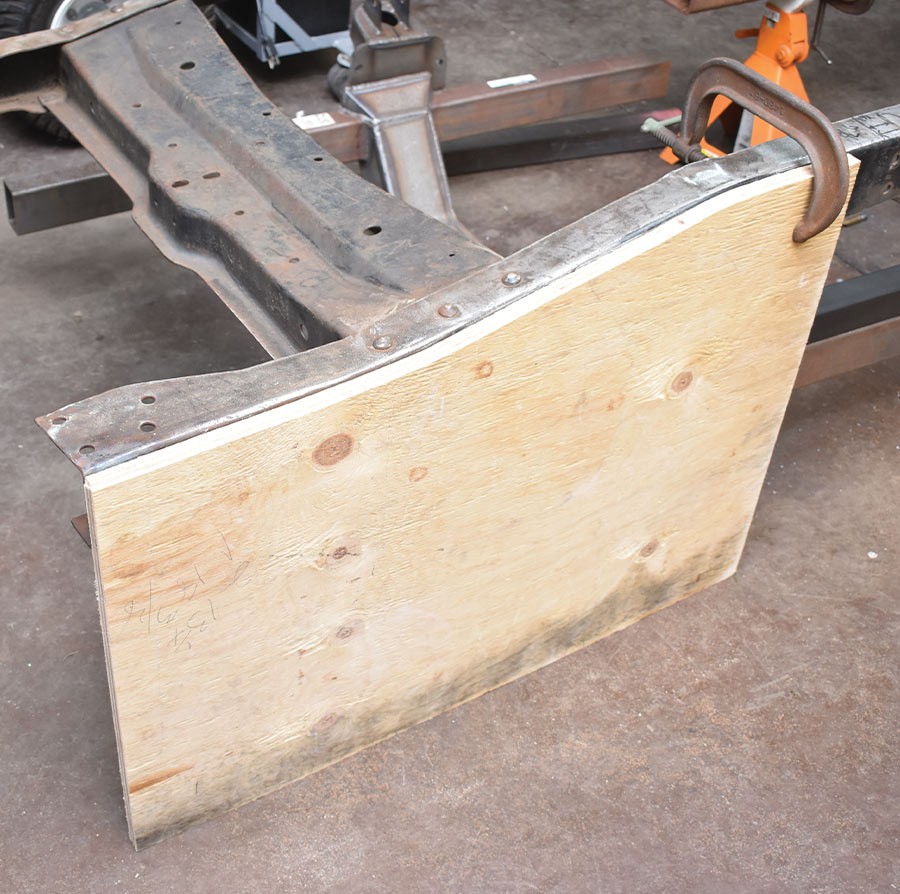
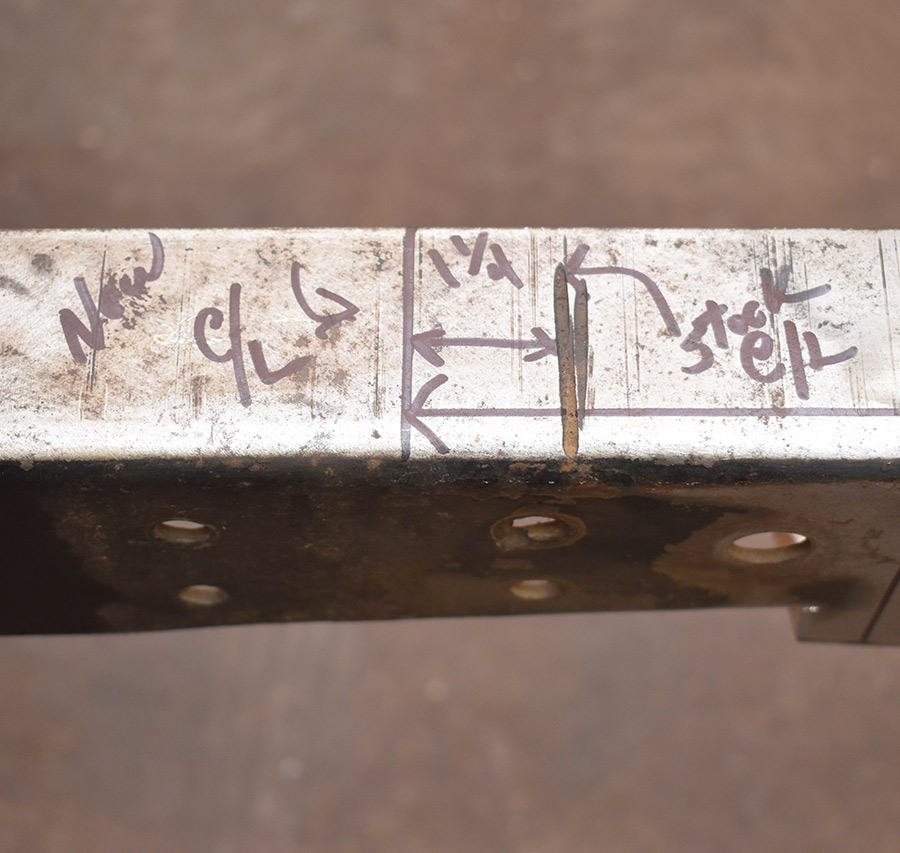
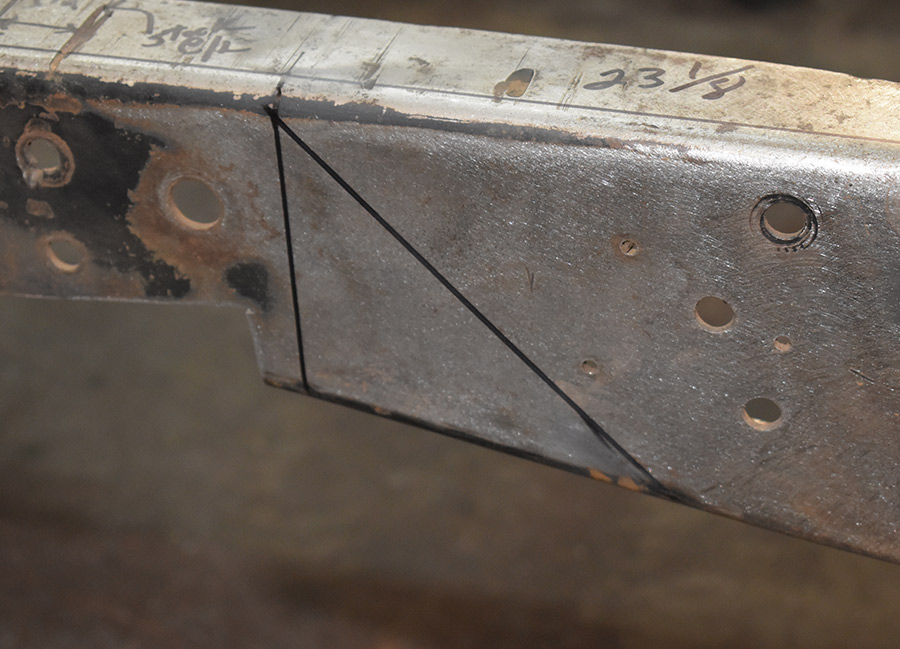
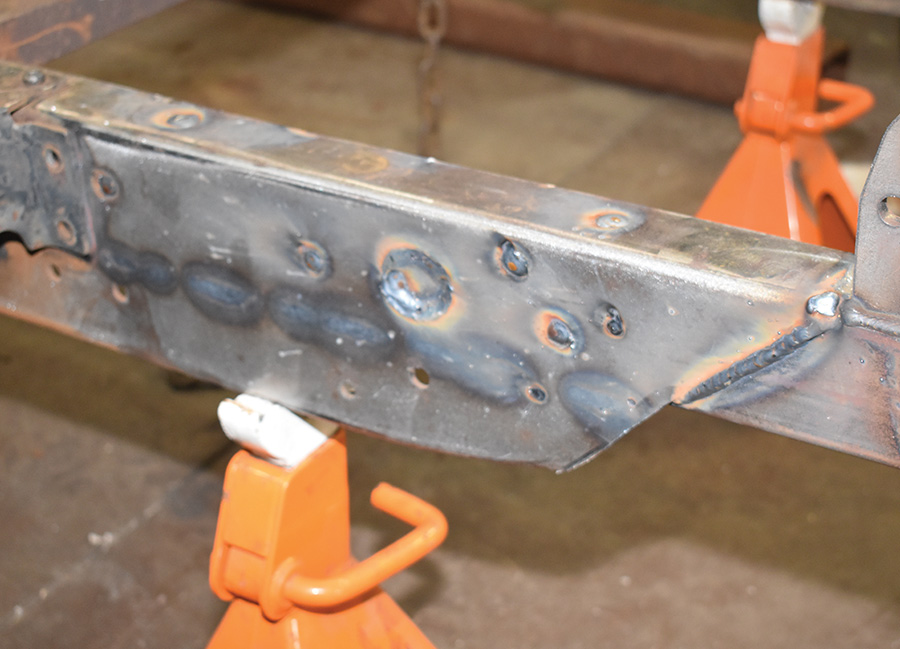
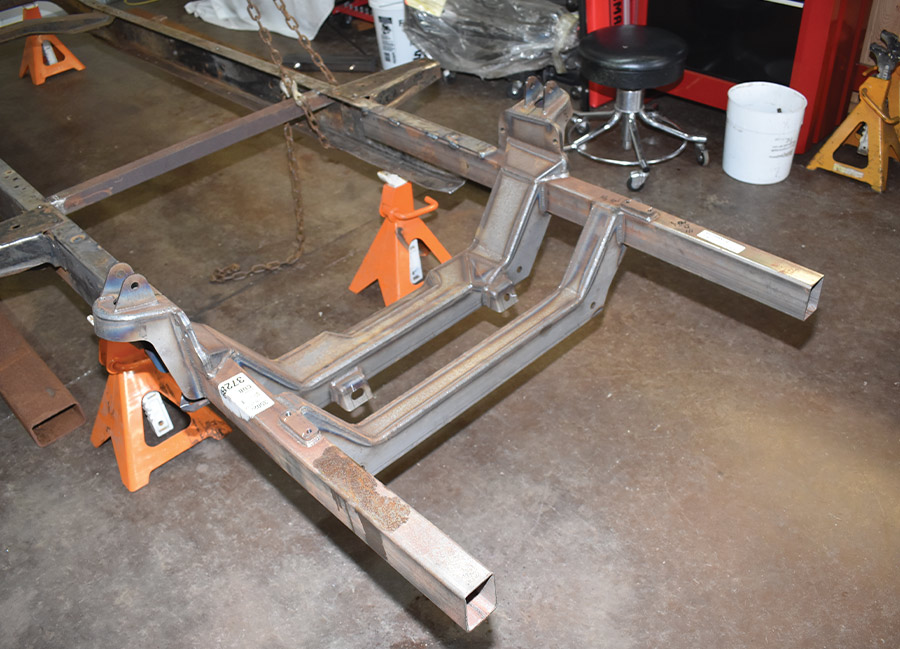
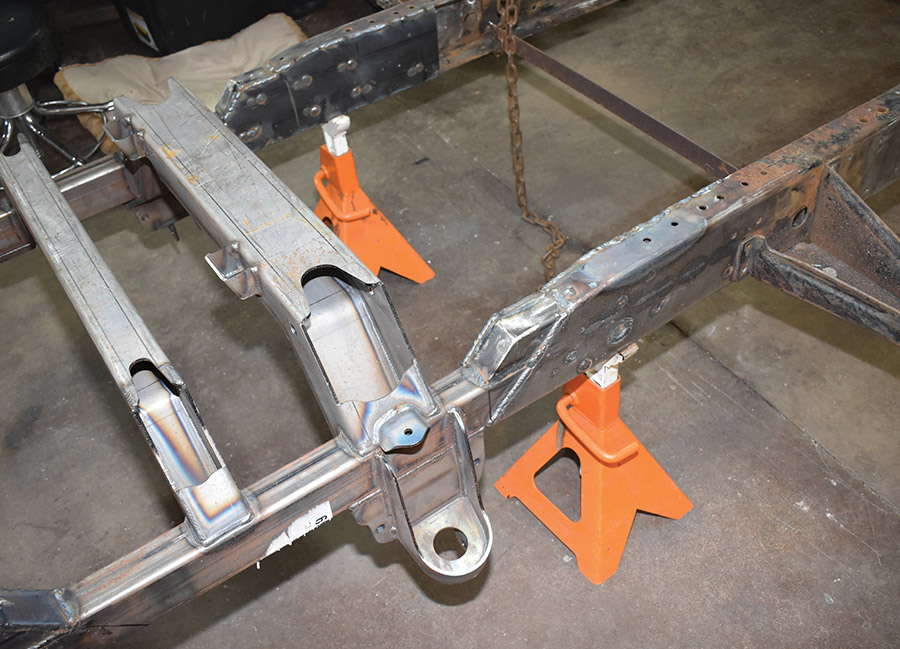
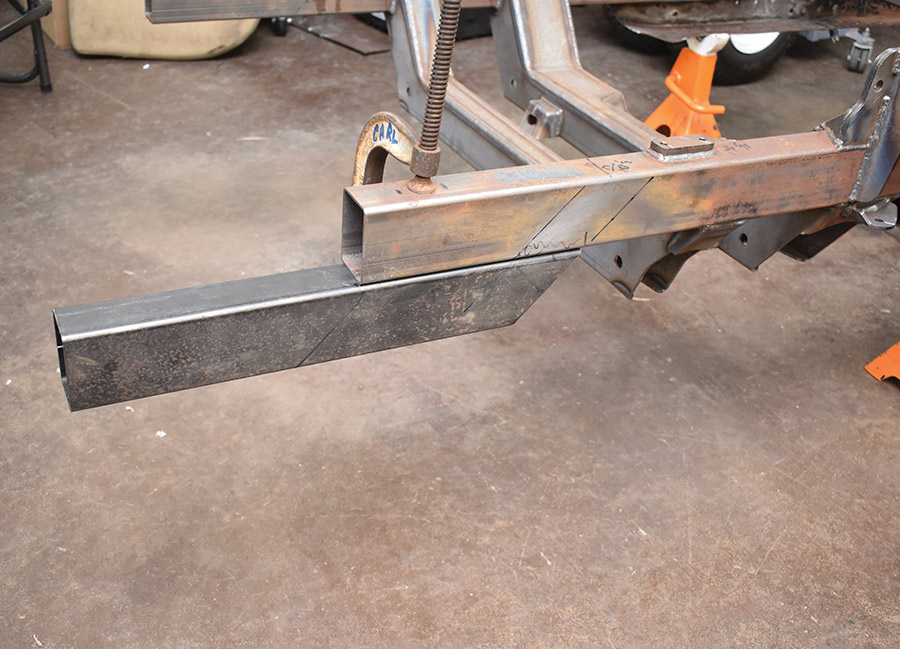
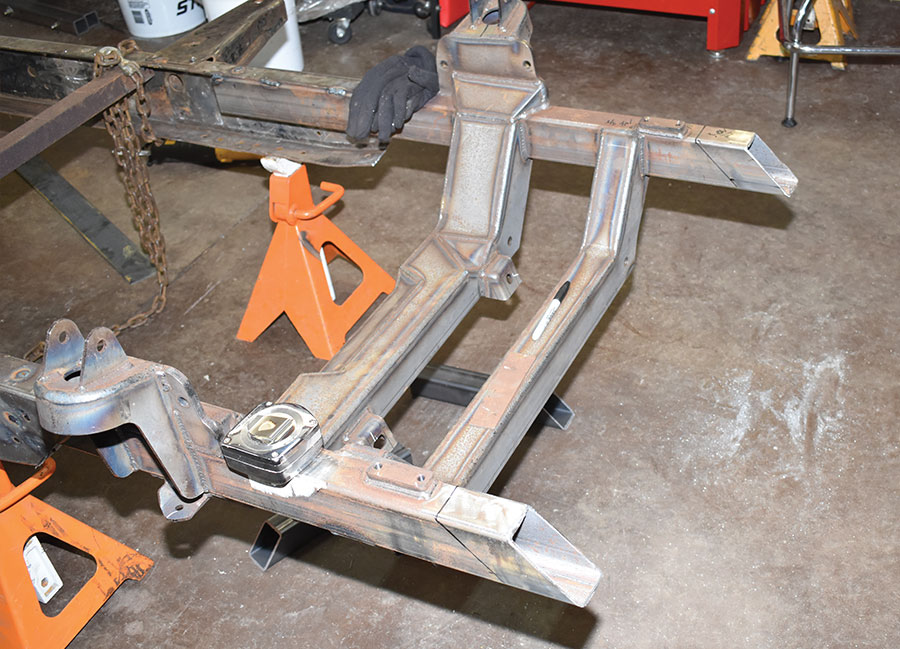
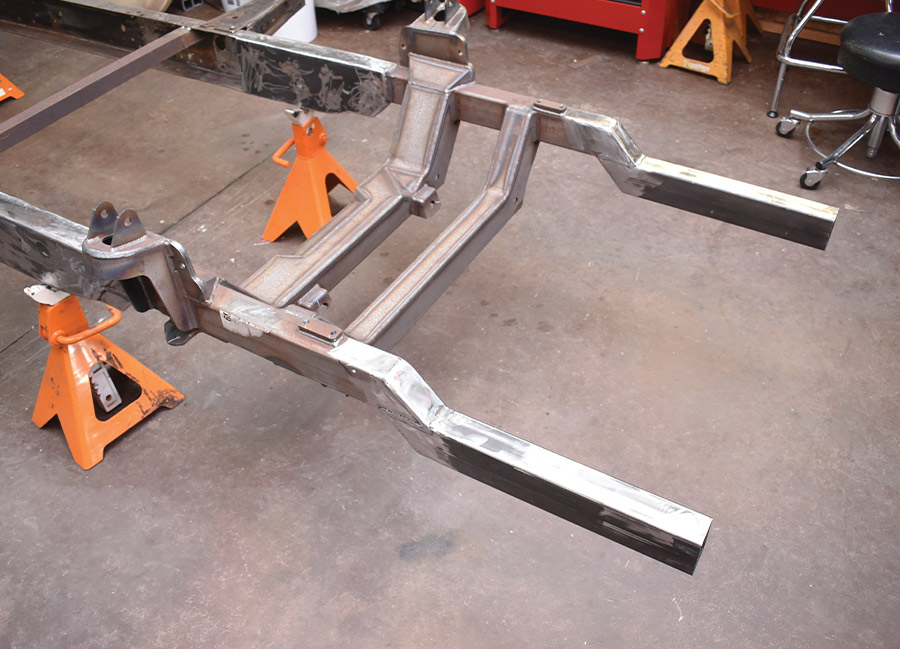
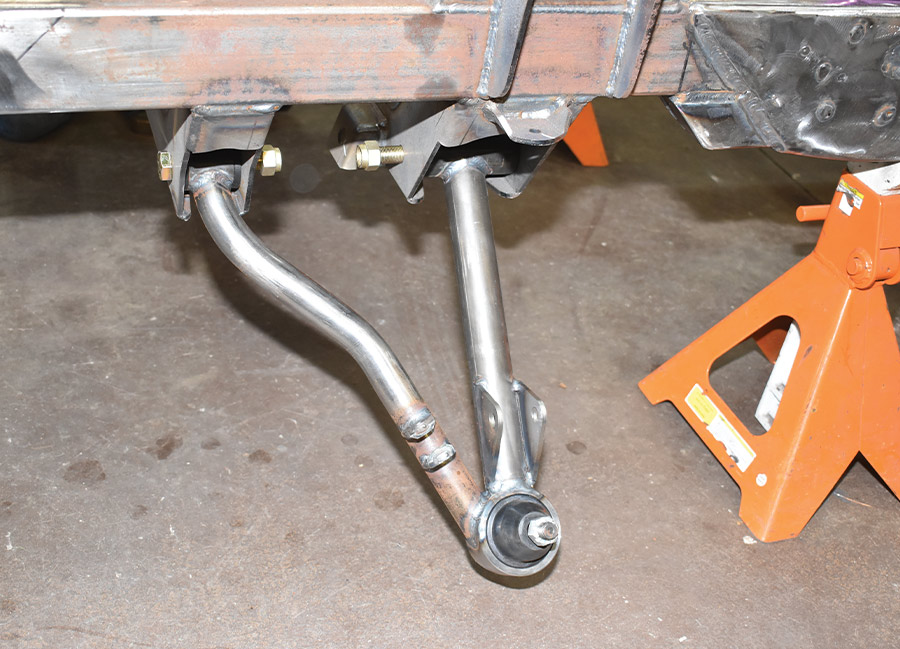
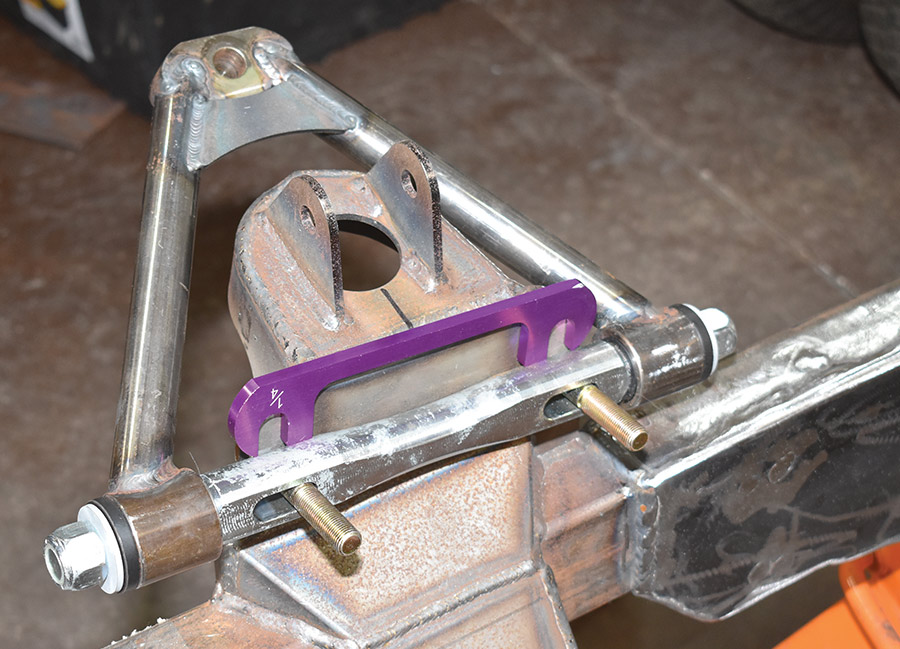
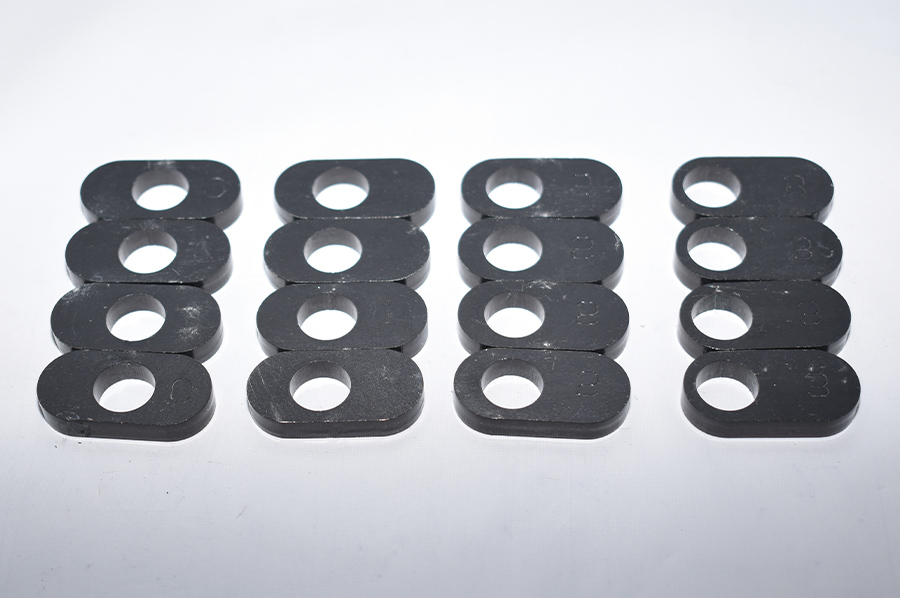
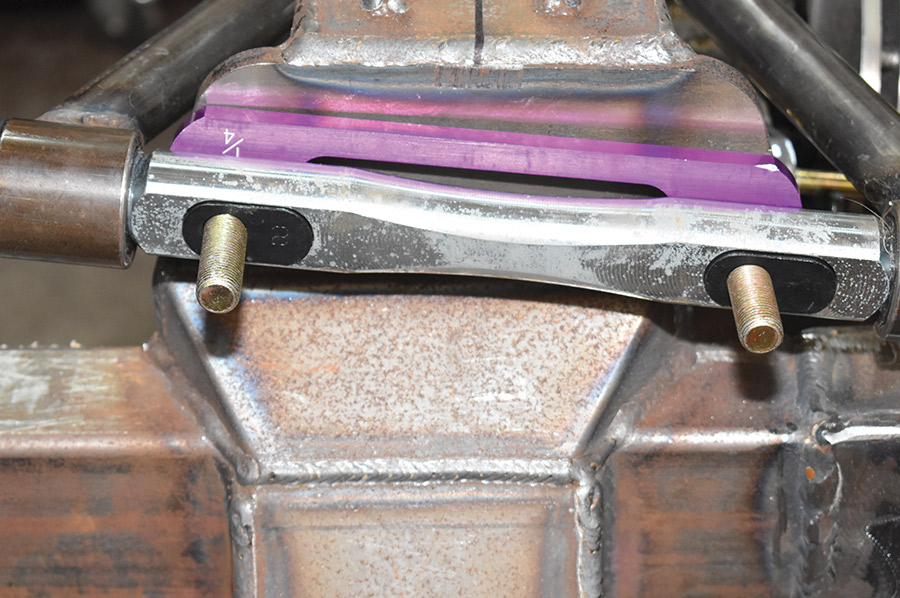
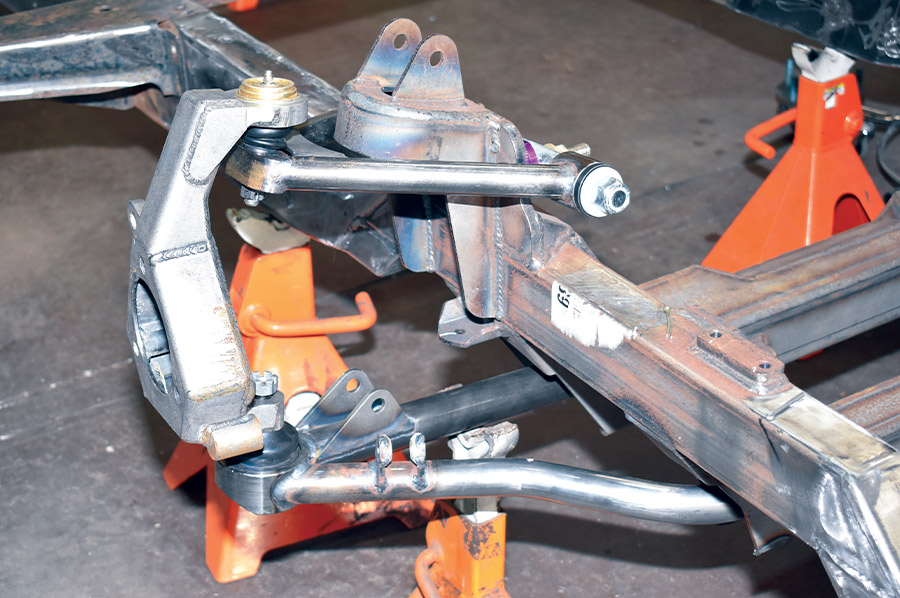
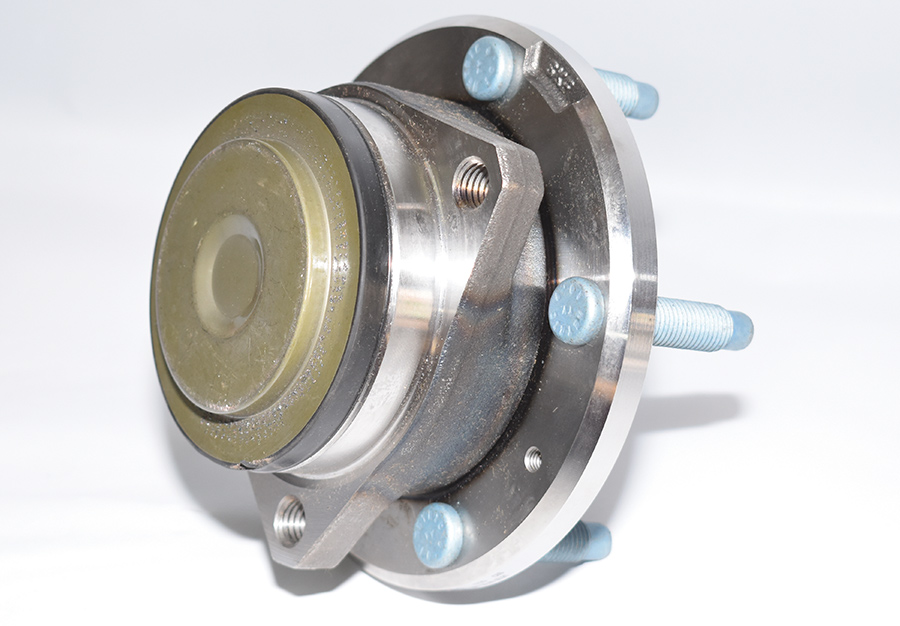
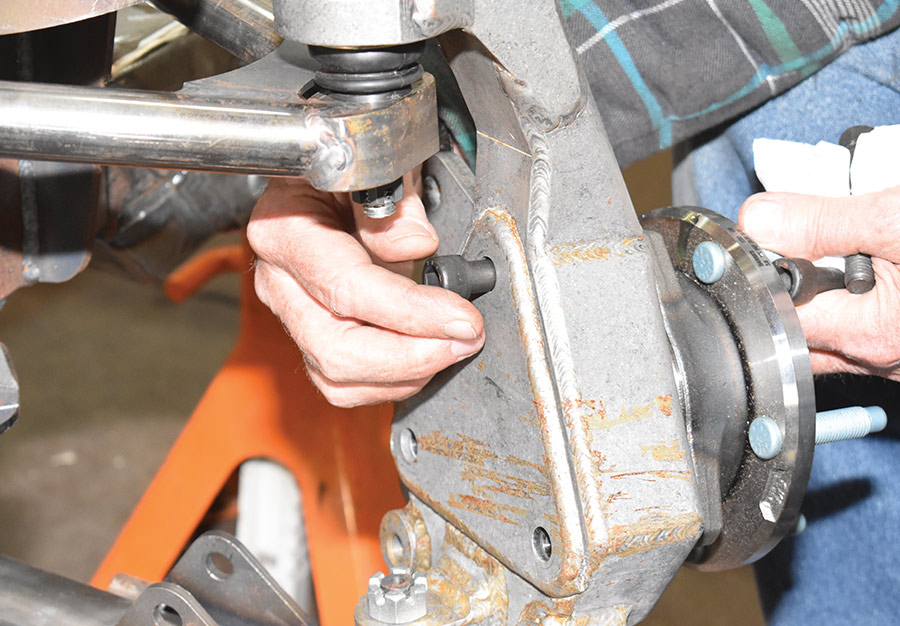
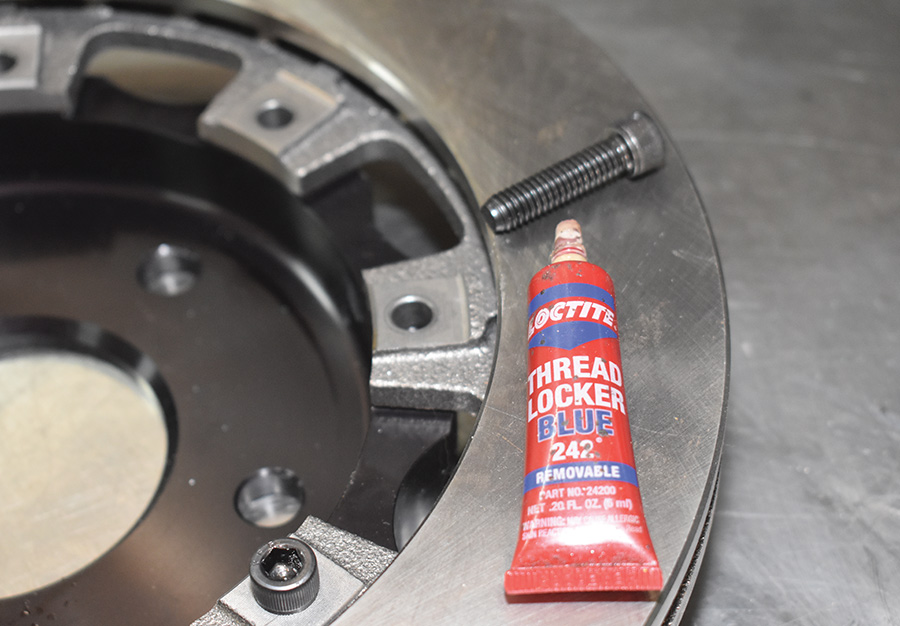
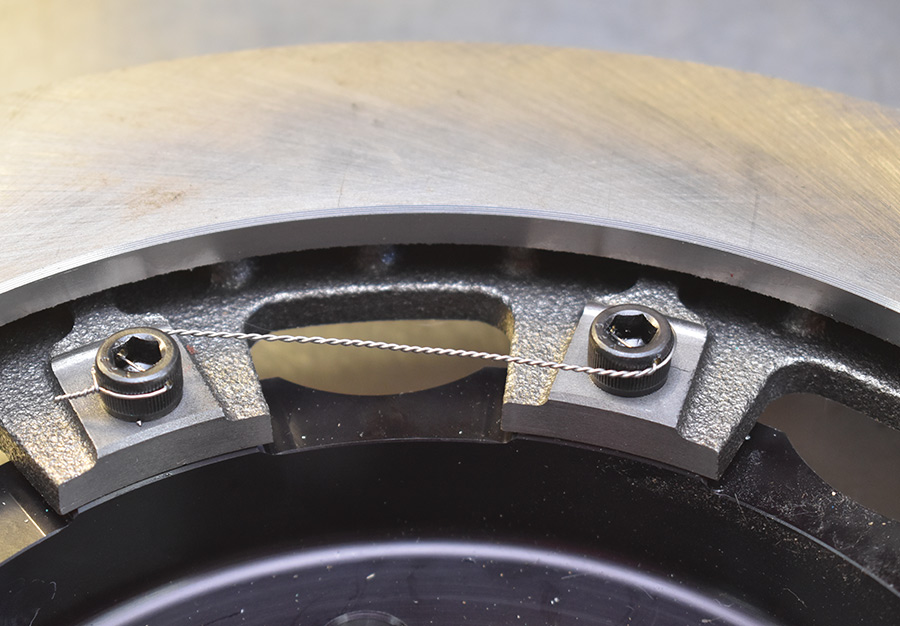
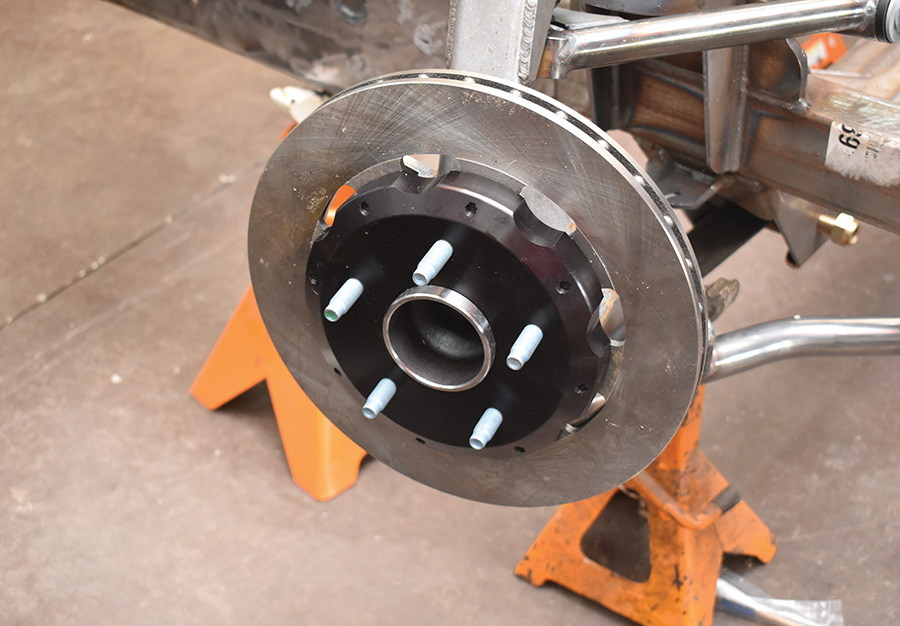
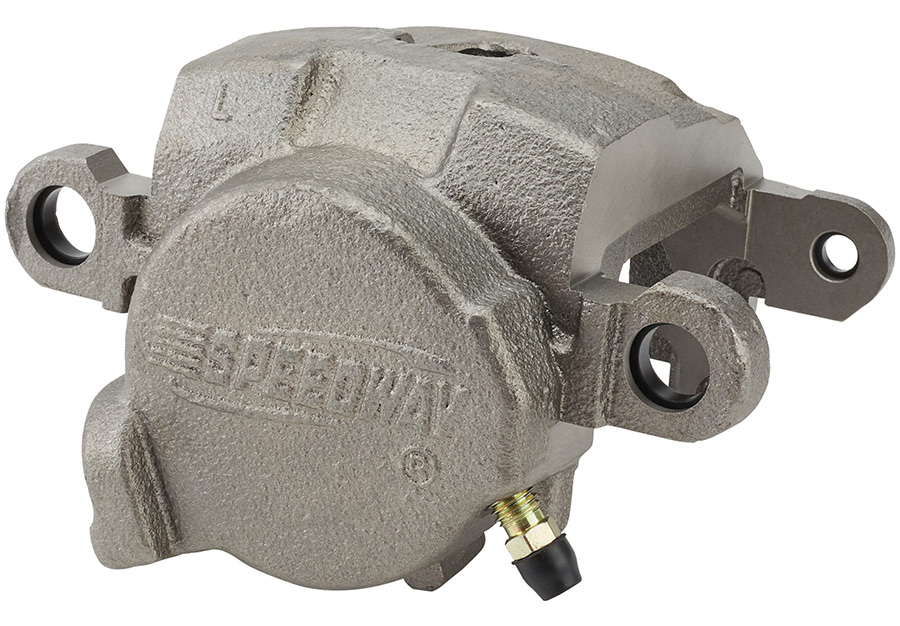
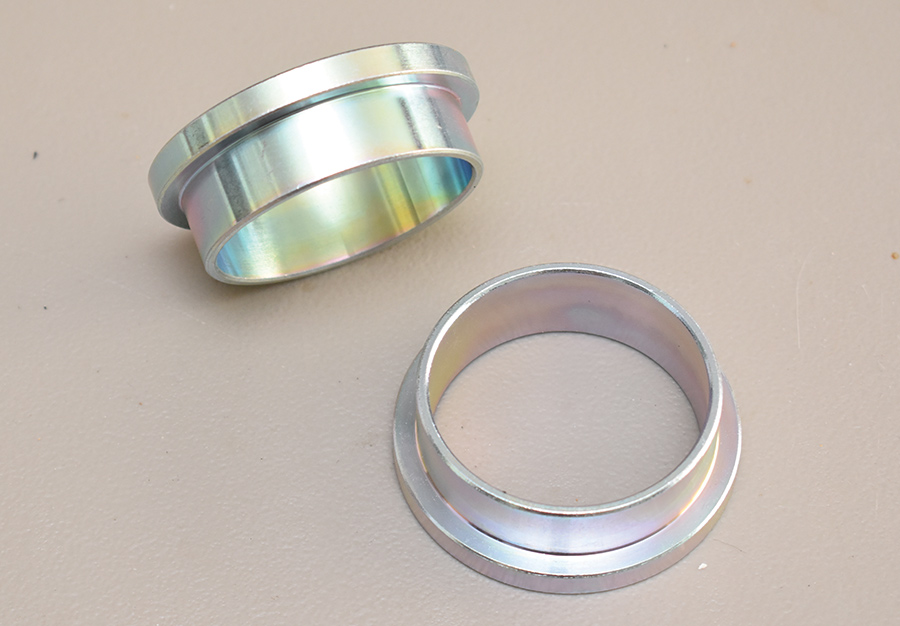
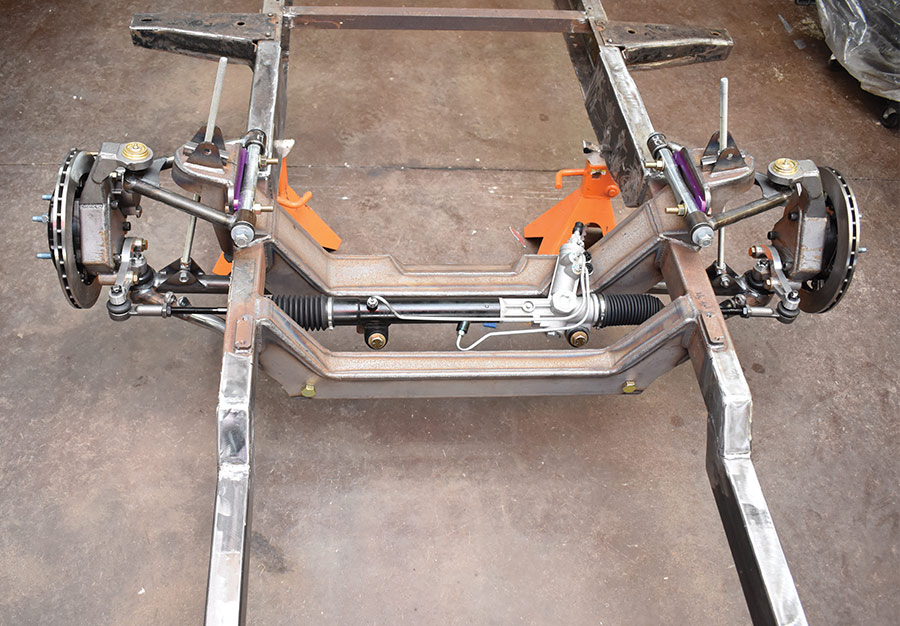
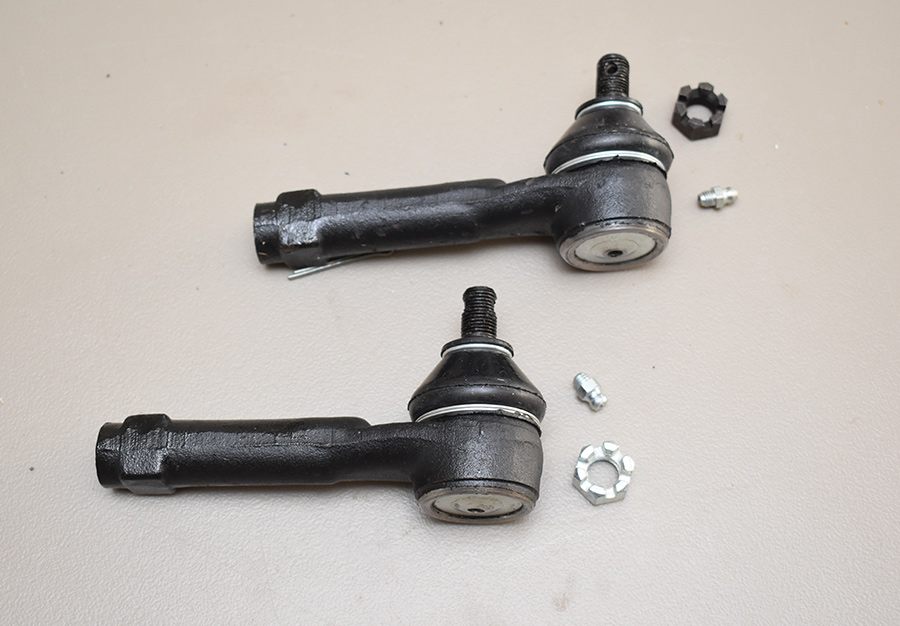
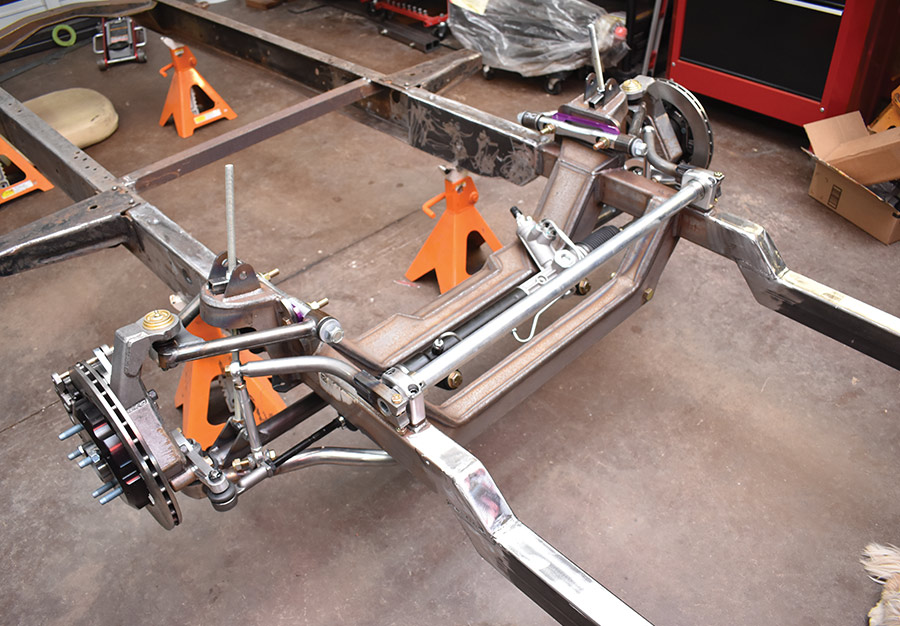
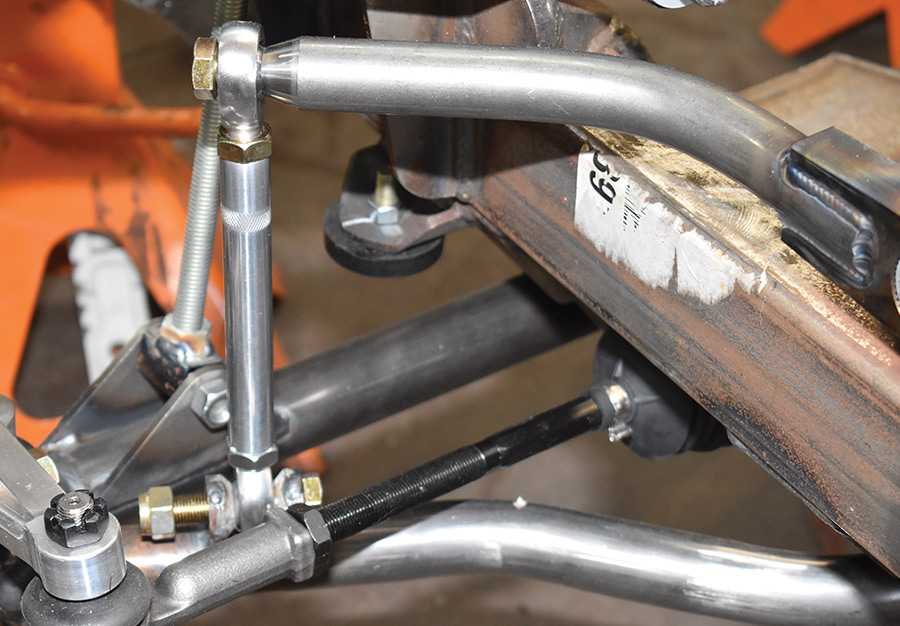
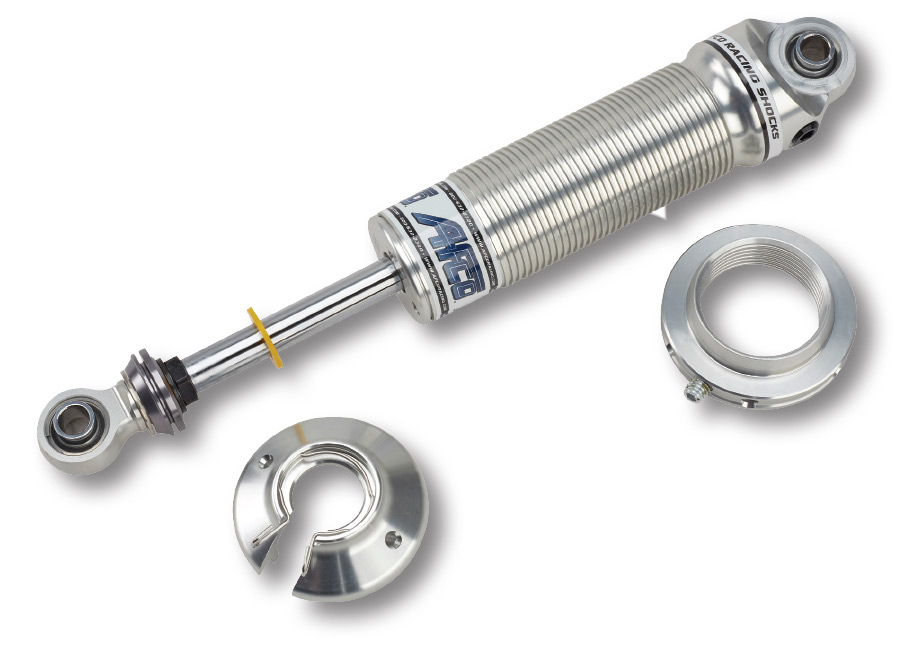
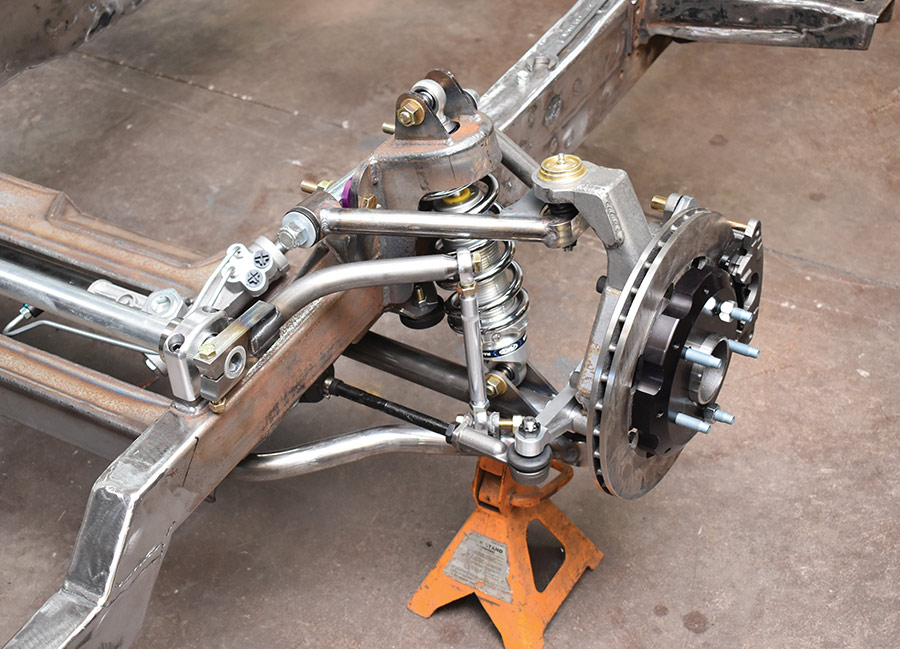
