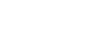

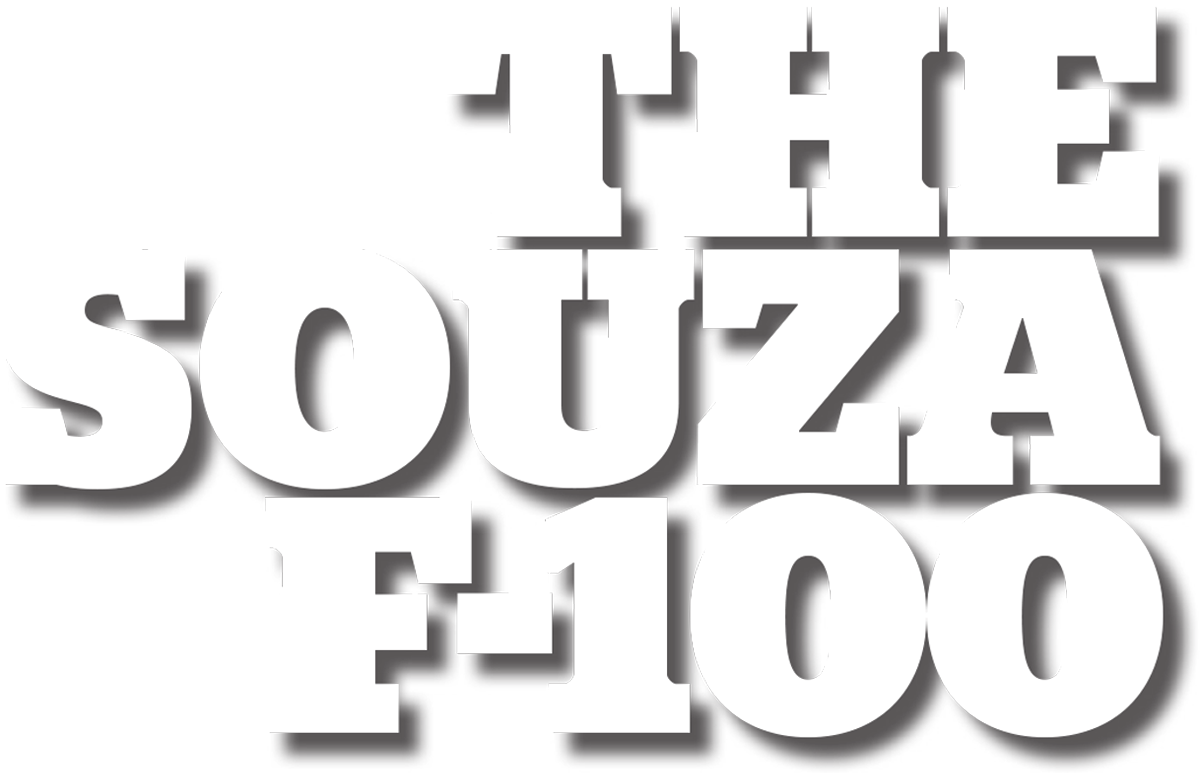
1. Every project needs a foundation, and this heavily modified (with an Art Morrison mandrel-bent IRS back-end) TCI chassis will definitely be up to the task.


ary George, who runs Gary’s Rods & Restorations in Northern California, has a long history of building outstanding vehicles. He was recently approached by Jason Souza to build a showstopping ’56 Ford F-100. This will be a “no-holds-barred” project, but they want the truck to have an elegant and refined character rather than going for shock value. Look for future articles that will include sectioning the cowl and the hood, moving the wheelwell openings in the front fenders, and scratchbuilding a new bed that matches the shape of the cab.
McIntyre also built an outstanding exhaust system and included a custom-fitted set of headers that feed into the Vibrant Performance mufflers and then into gorgeous 2×4-inch oval stainless tailpipes that gracefully snake through the confines of the frame.
The engine is a Ford Boss 572, fitted with Jon Kaase stack injectors and accessories, backed by a Hughes Performance–built 4L85E transmission.
To start the project, George had all the sheetmetal panels stripped and powdercoated. This ensures that all the nooks and crannies are protected from rusting, inside and out, and will provide a stable foundation for the extensive body modifications to come.
Emilio Belmonte is George’s sheetmetal expert. After the chassis work was completed one of his first tasks was to make a new firewall and floor for the cab. He used chip board to mock up the firewall, getting a close fit to the bellhousing but allowing adequate room for the powerful engine to flex on its mounts. There will be raised panels formed on the firewall, inner fender panels, and inner bed panels to provide stiffness and style. Belmonte uses a Pullmax machine to form these panels, as you’ll see in the photos.
Once the design and patterns for the new firewall were completed, the original firewall was removed. This provided the perfect opportunity to install bracing for the Kugel Komponents pedal system, and to get the pedals and master cylinder properly located and mounted. This job is so much easier with the firewall out of the way.
The photos will show the “intimate details” of how this work was done, and you can look for more articles on each of the major body modifications to come. Hang on for the ride–not only will this be an outstanding truck, it could very well give you some ideas for your personal projects!
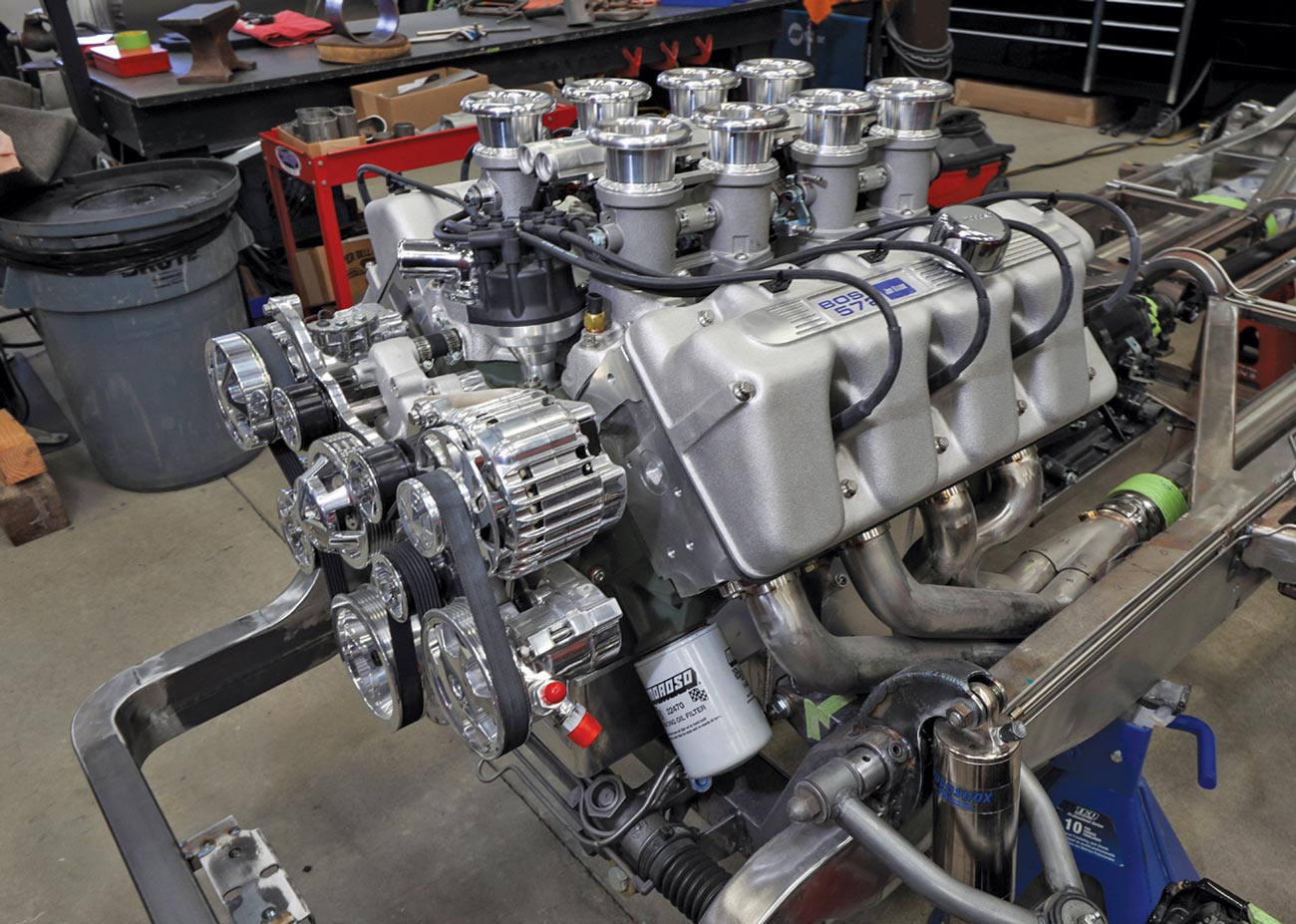
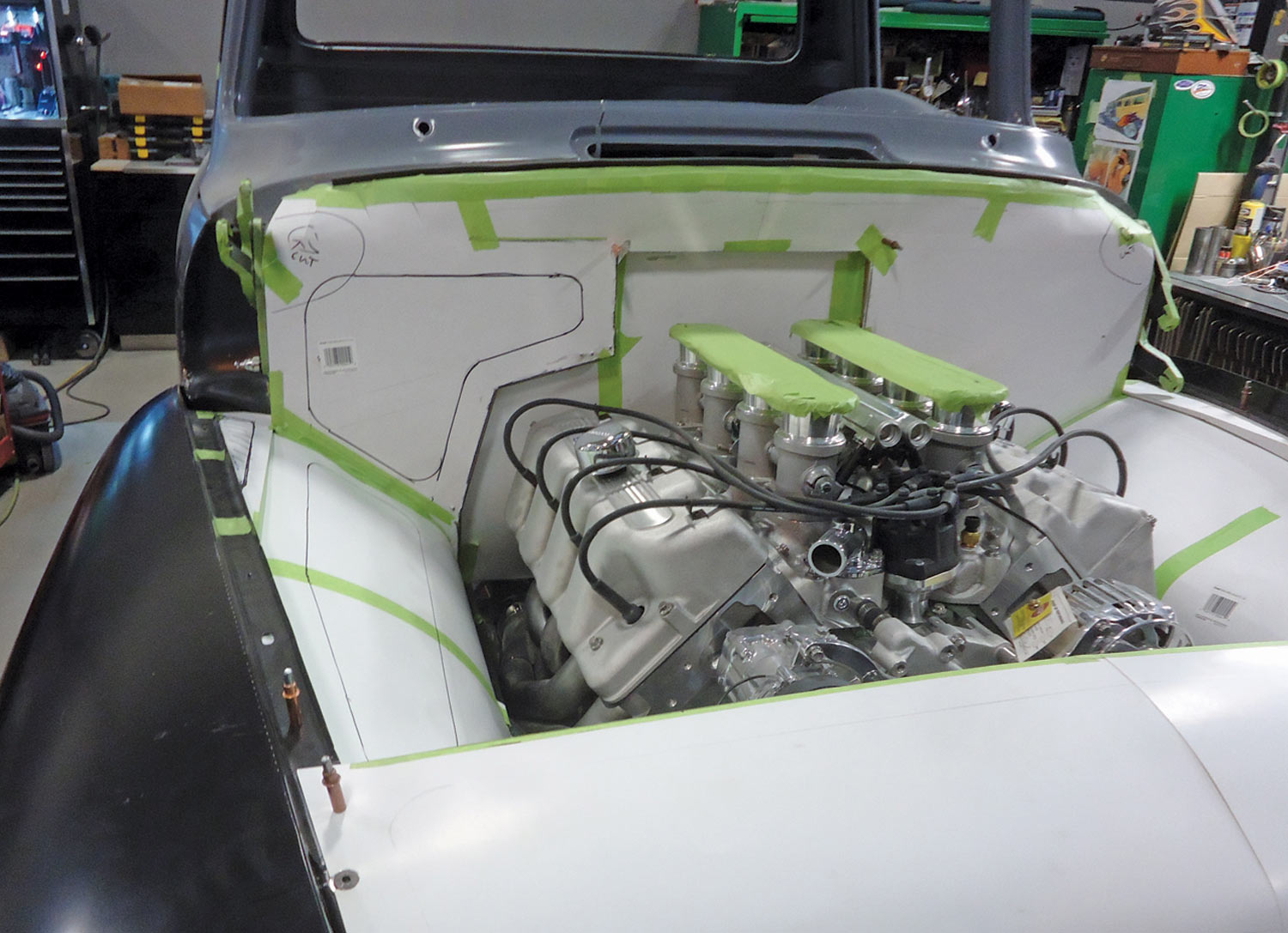
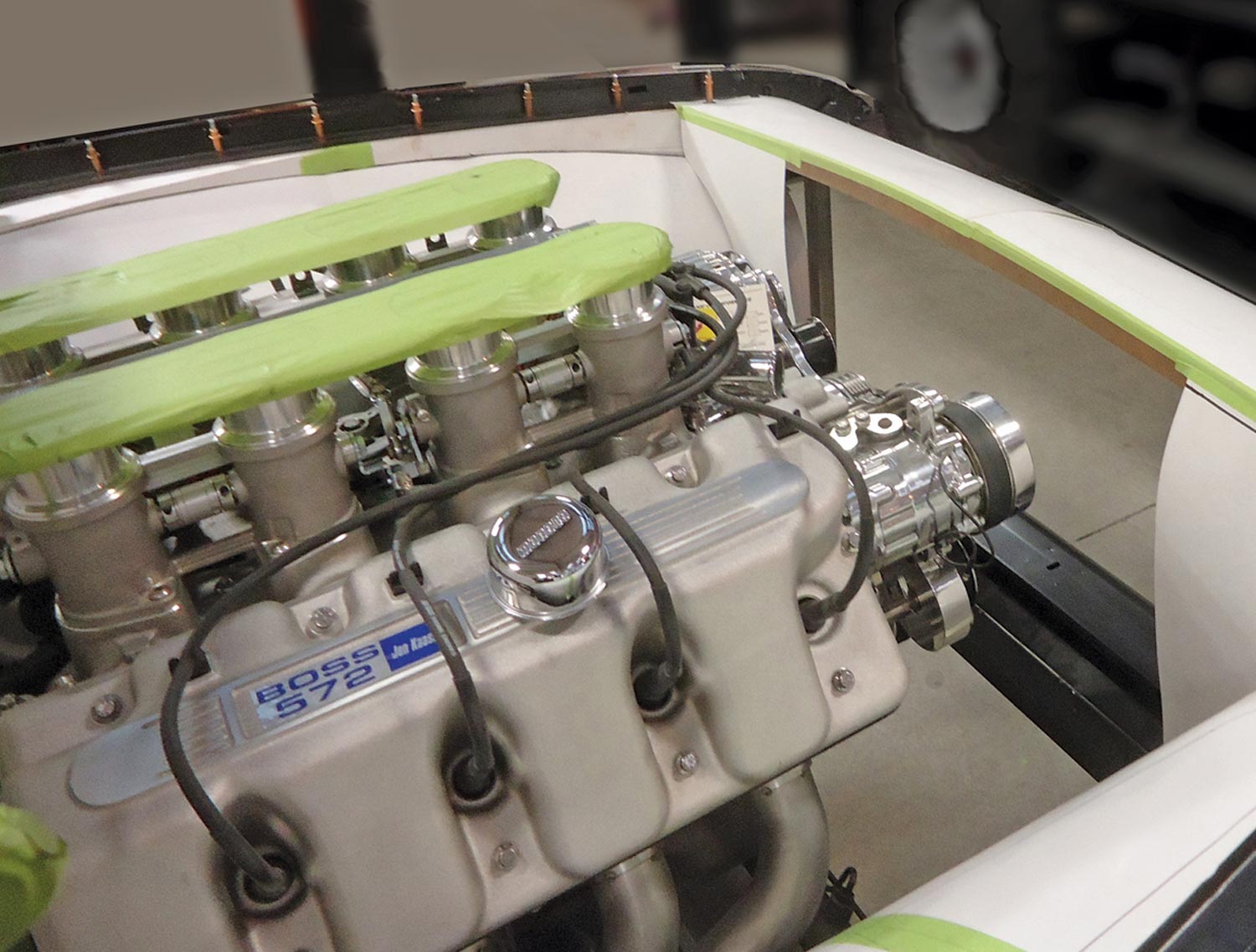
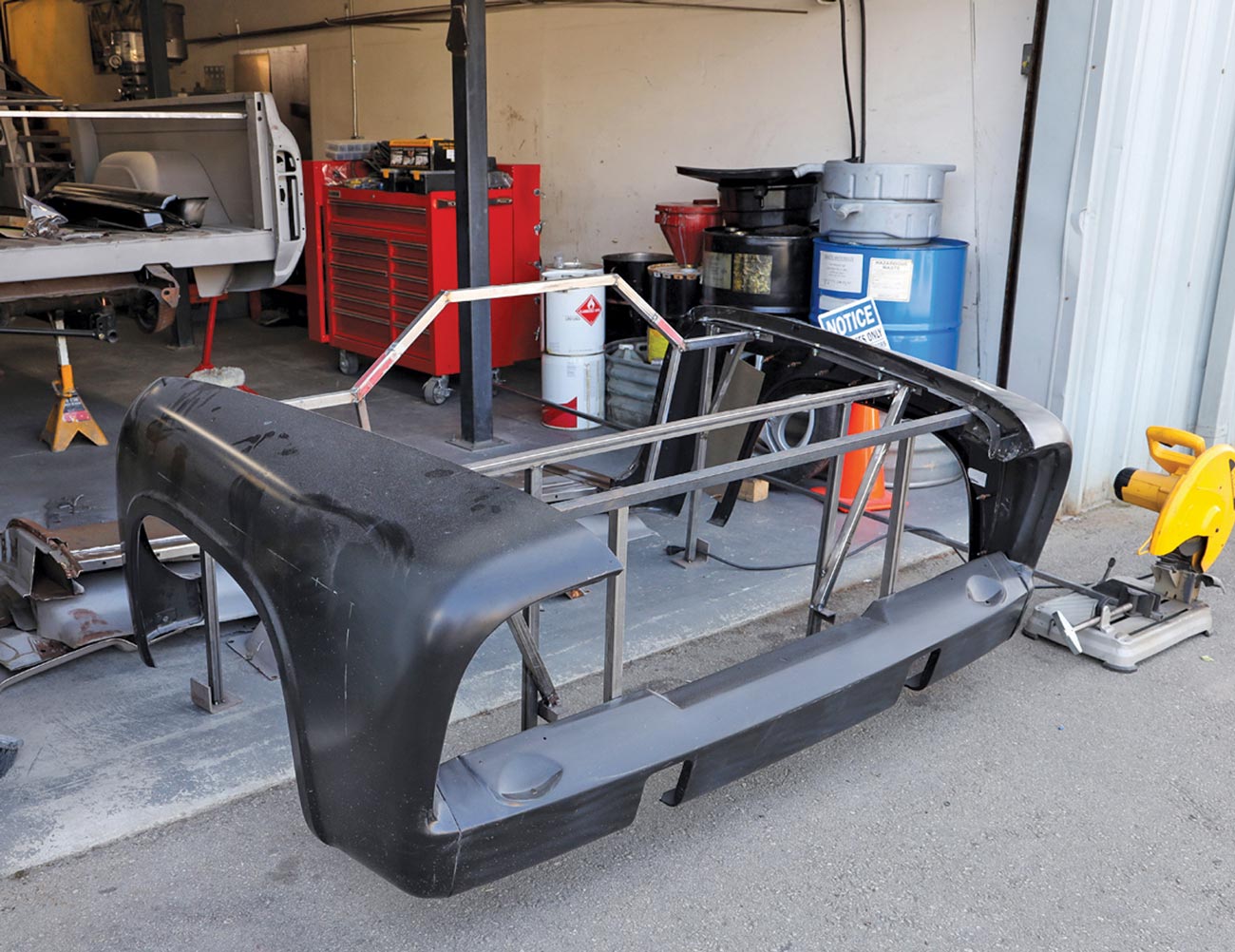
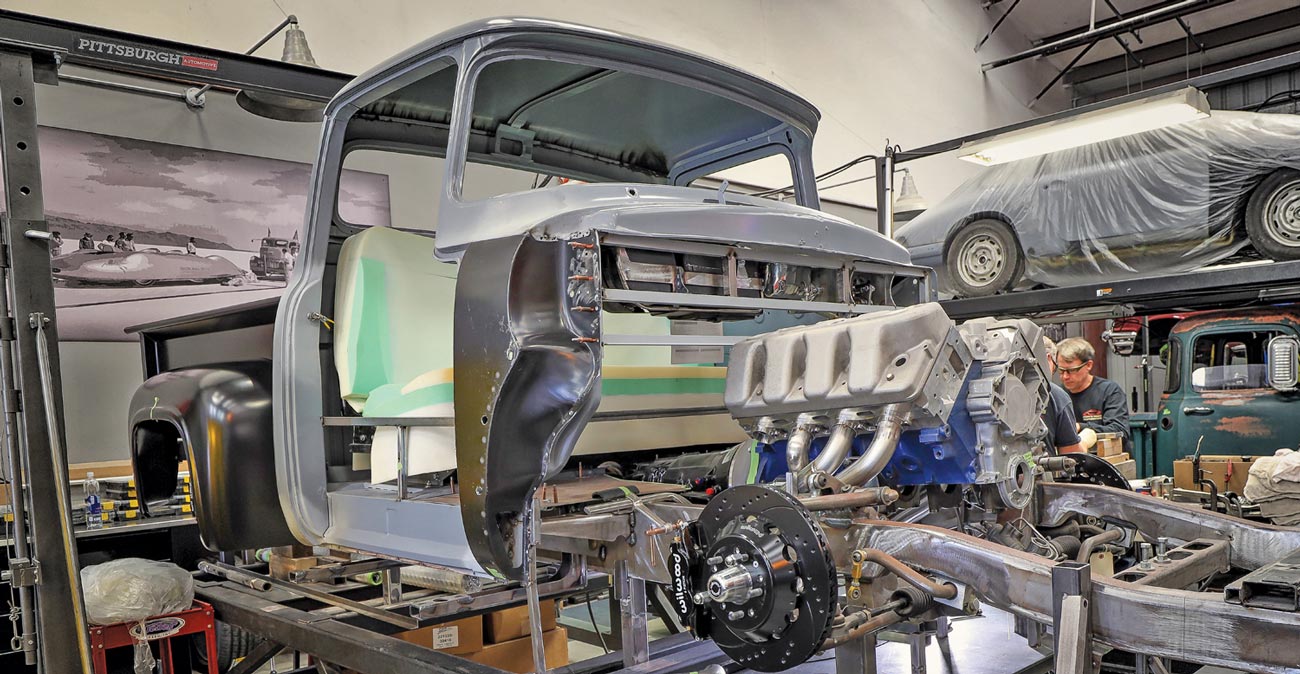
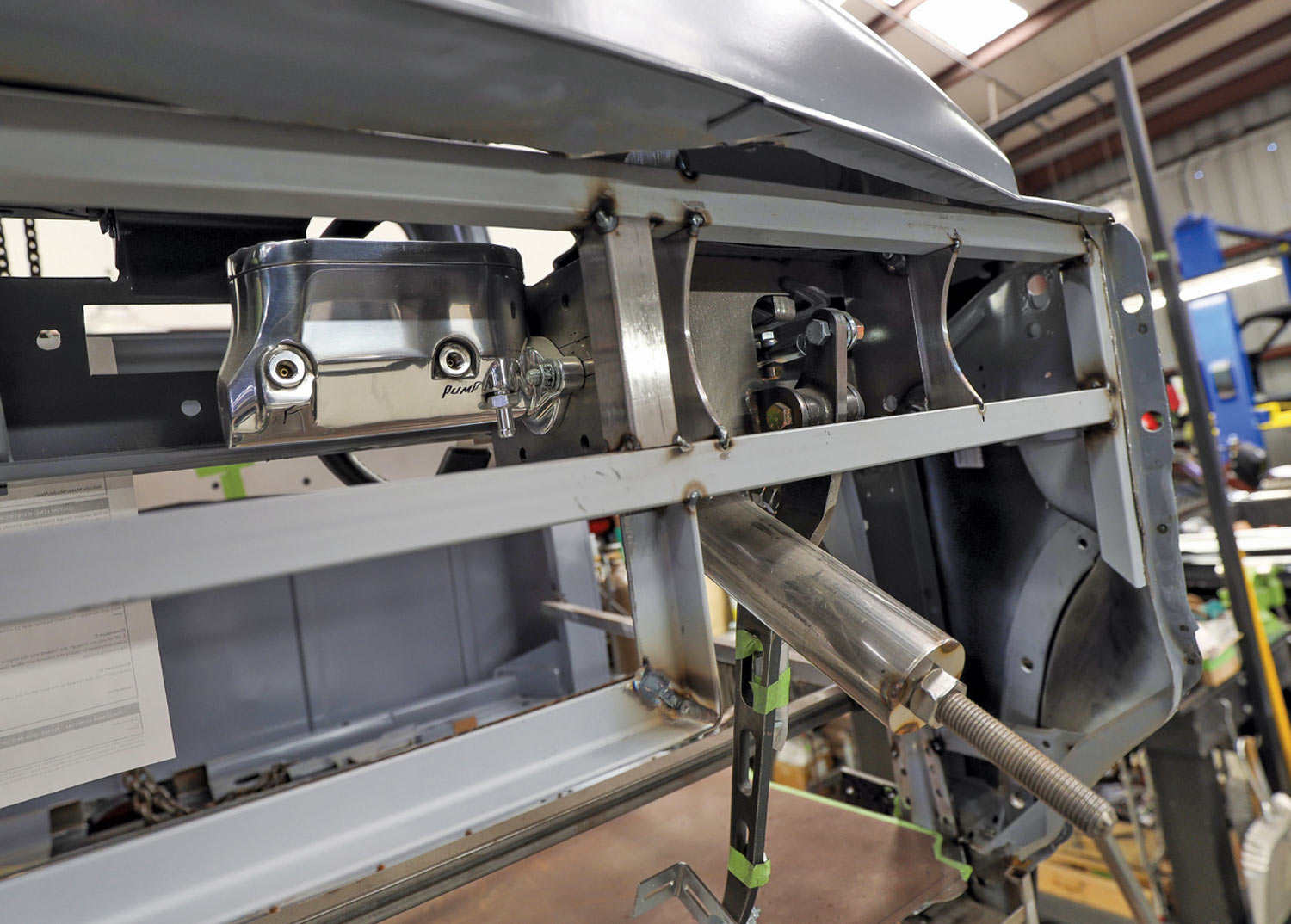
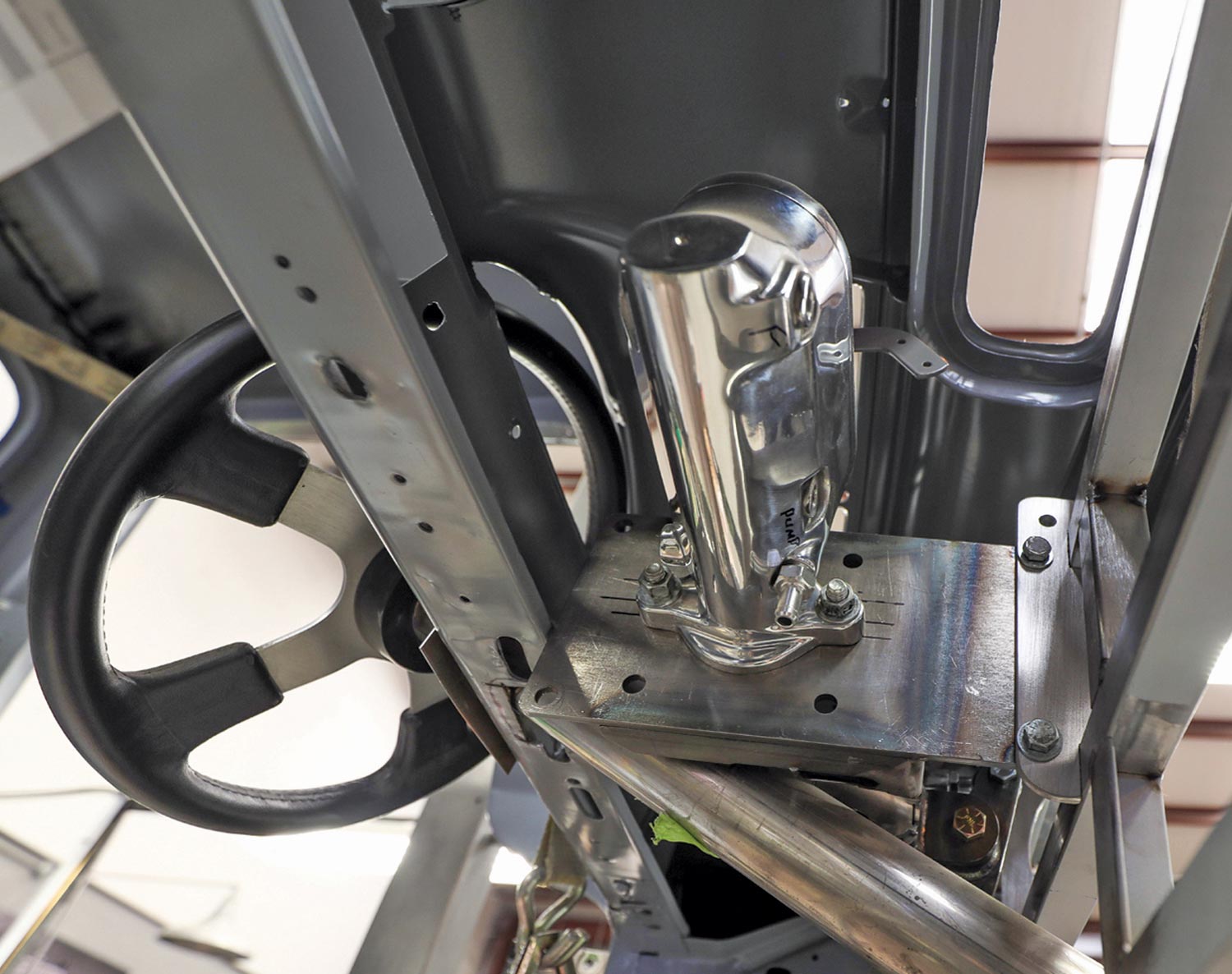
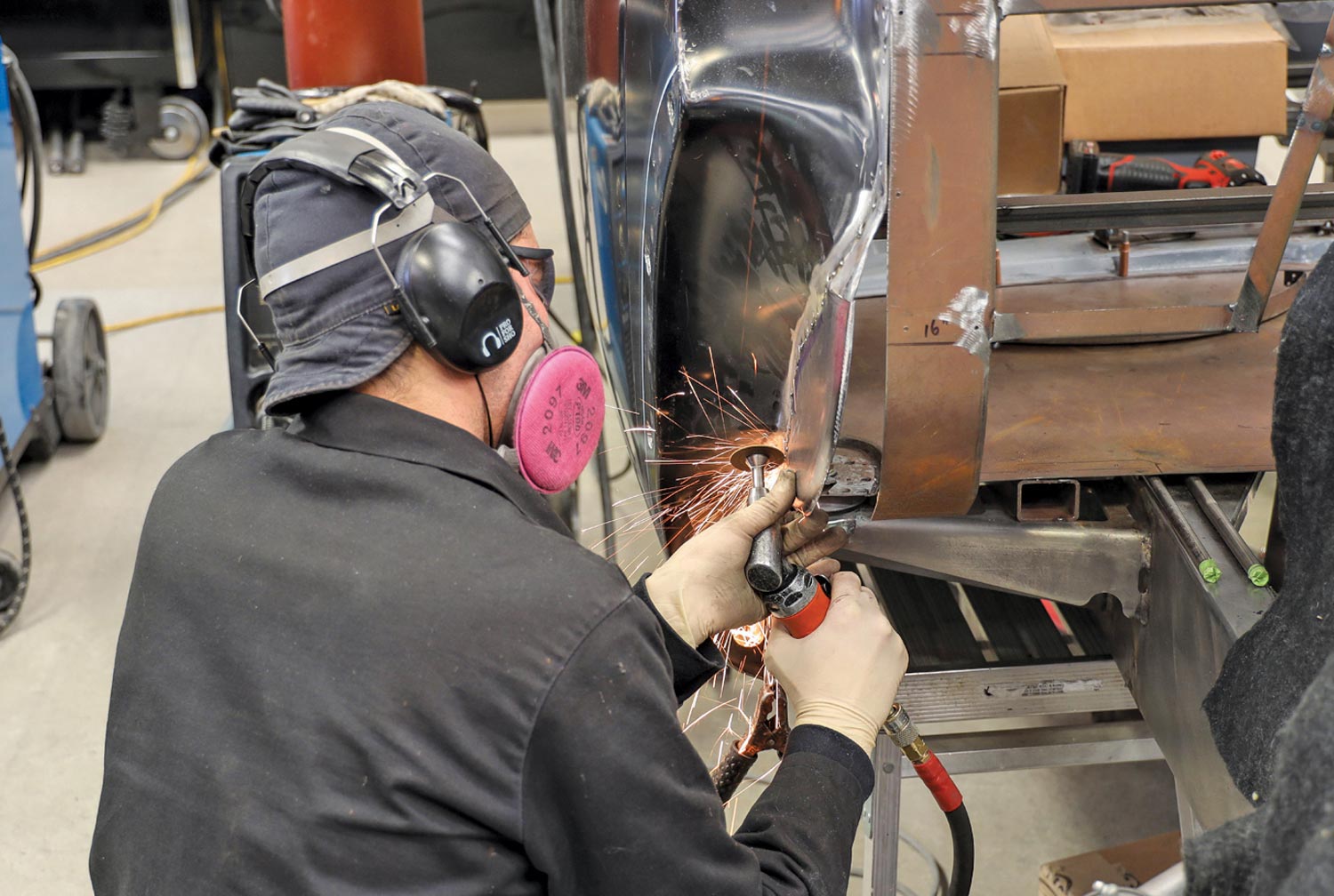
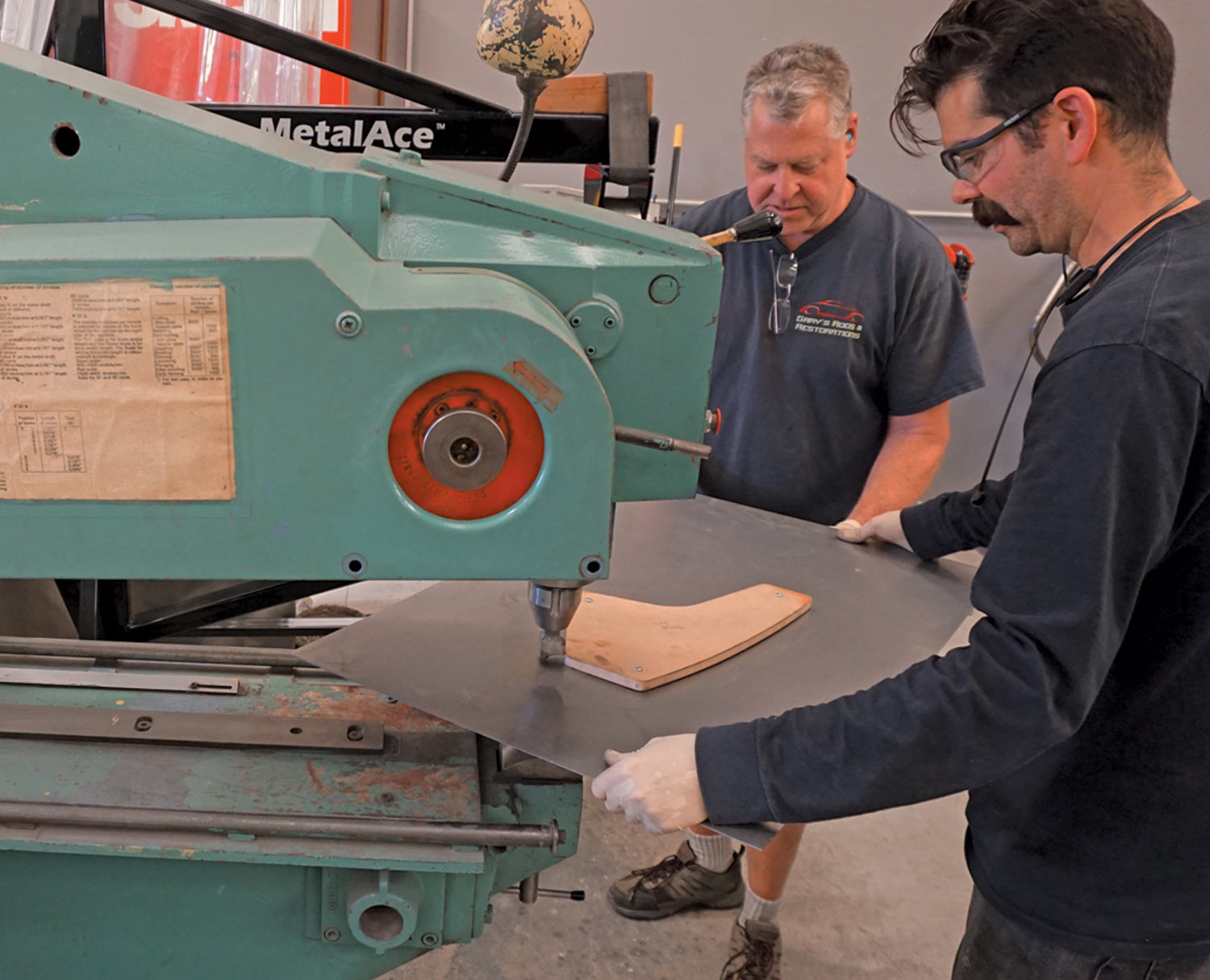
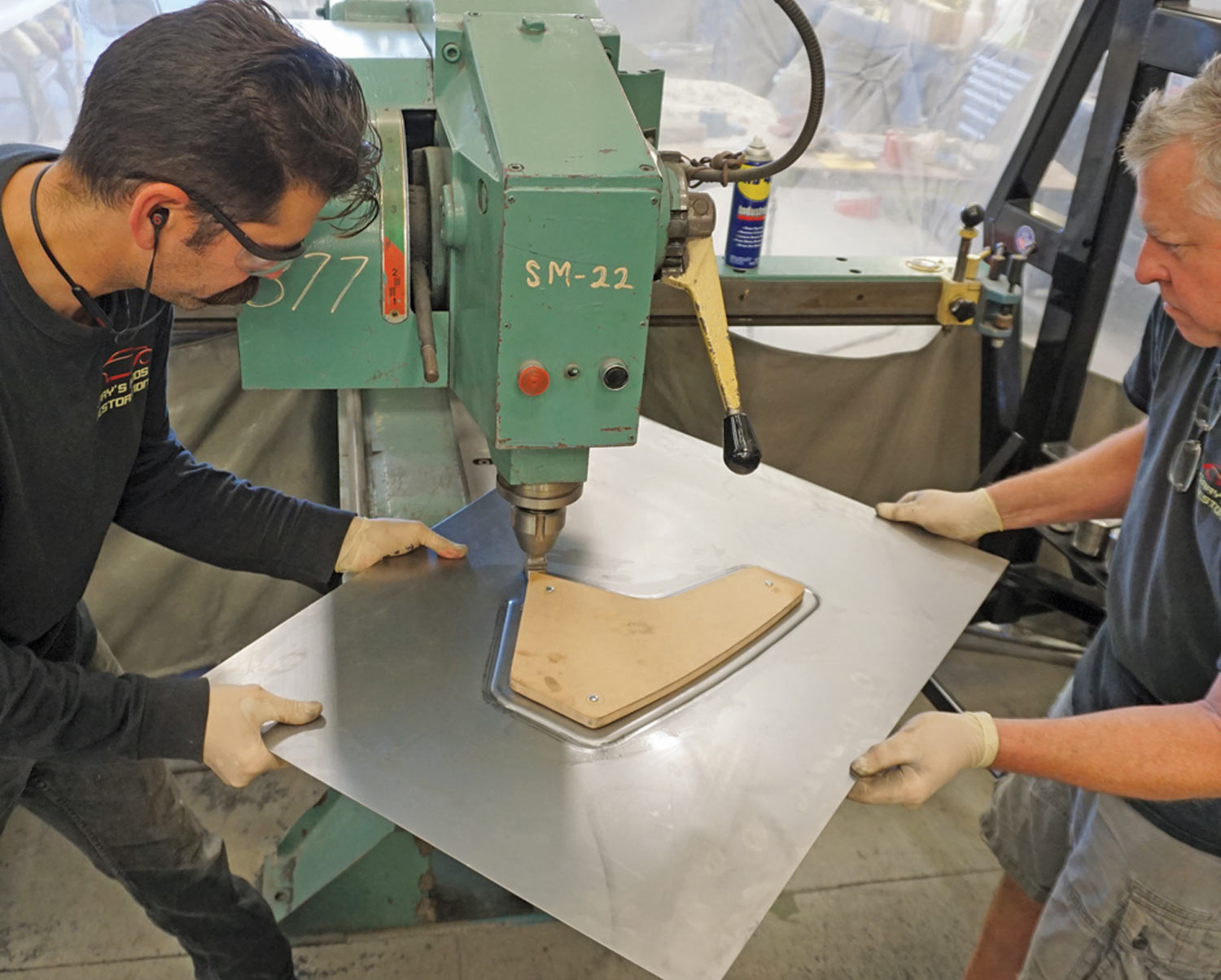
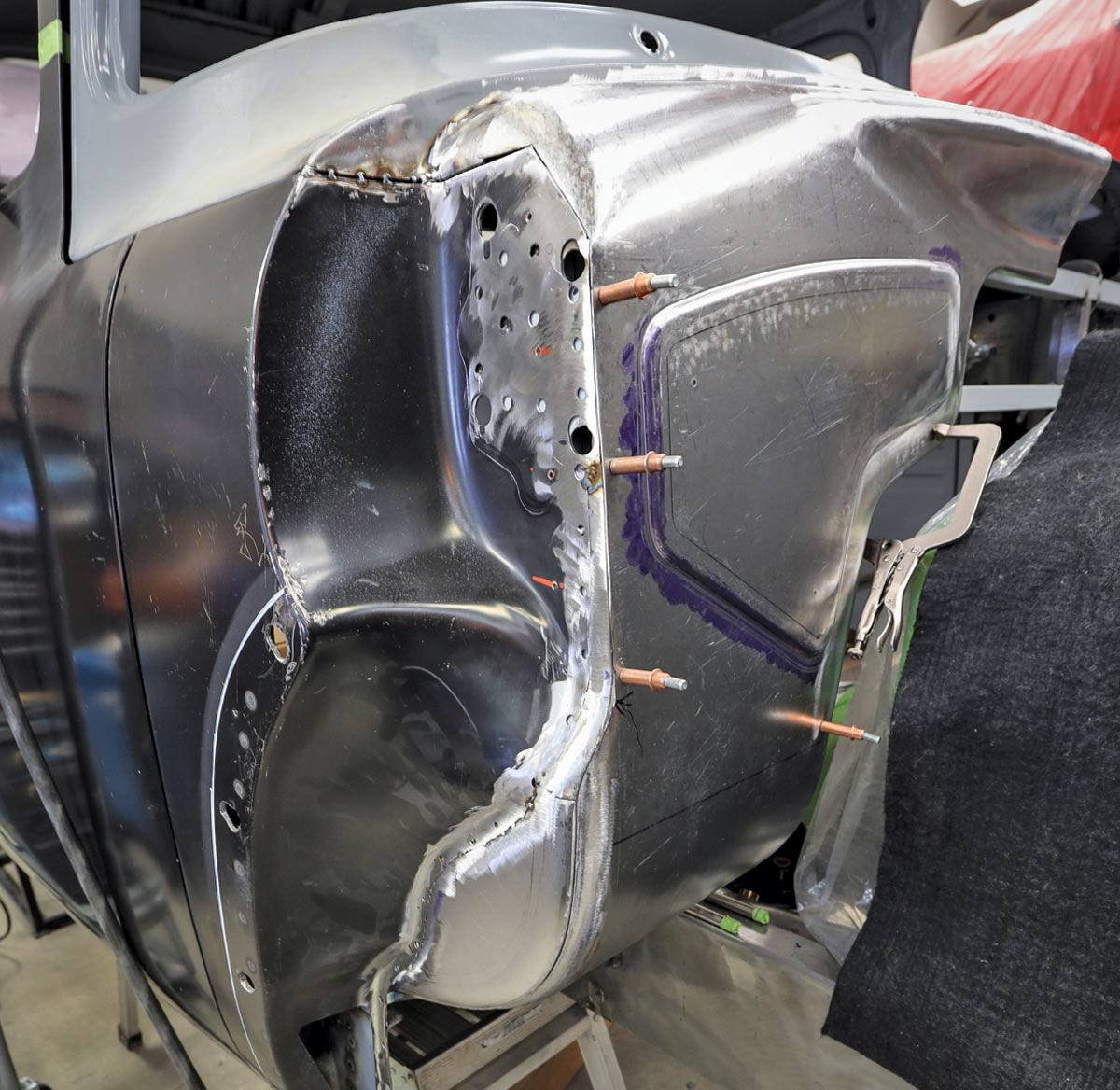
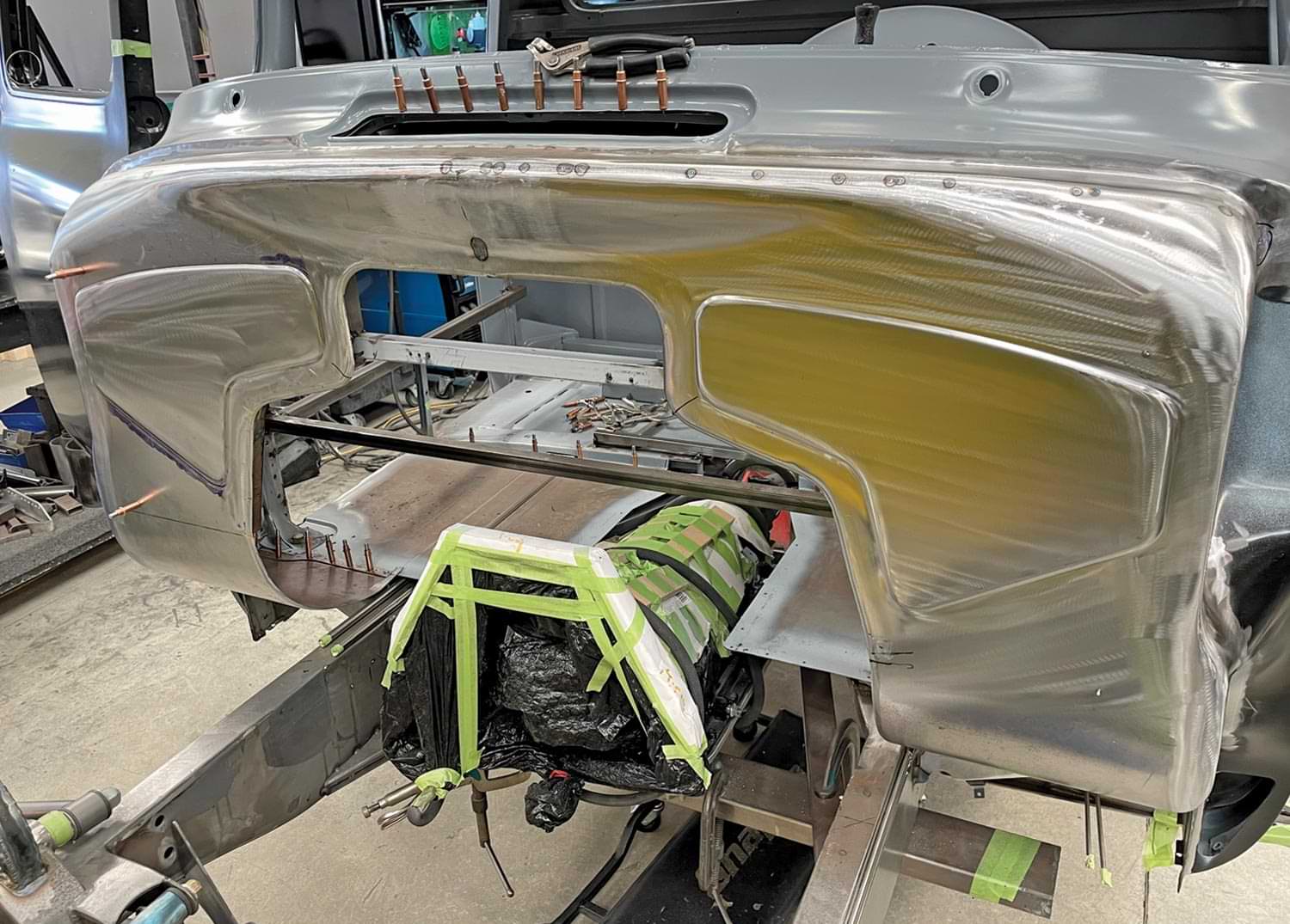
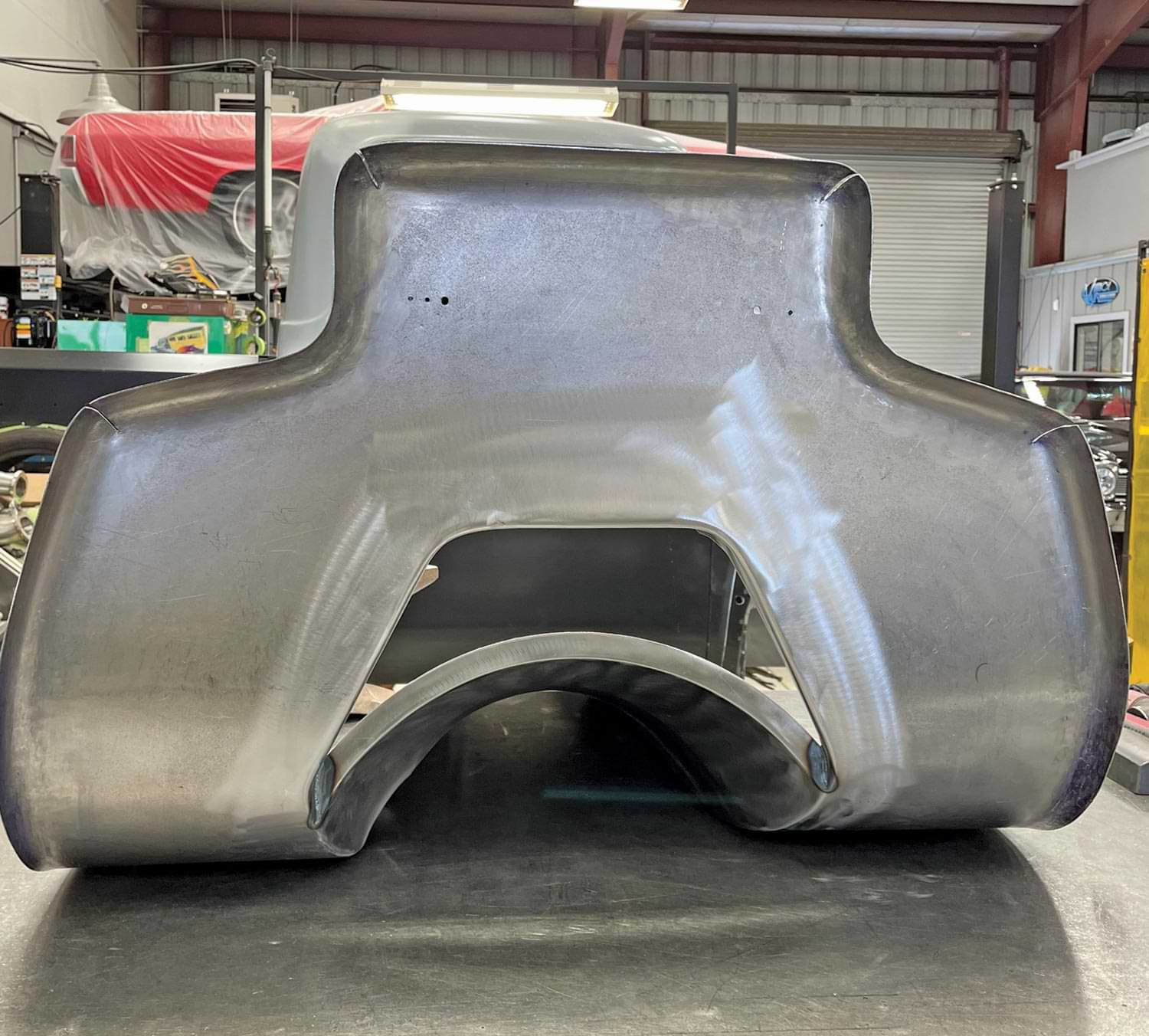
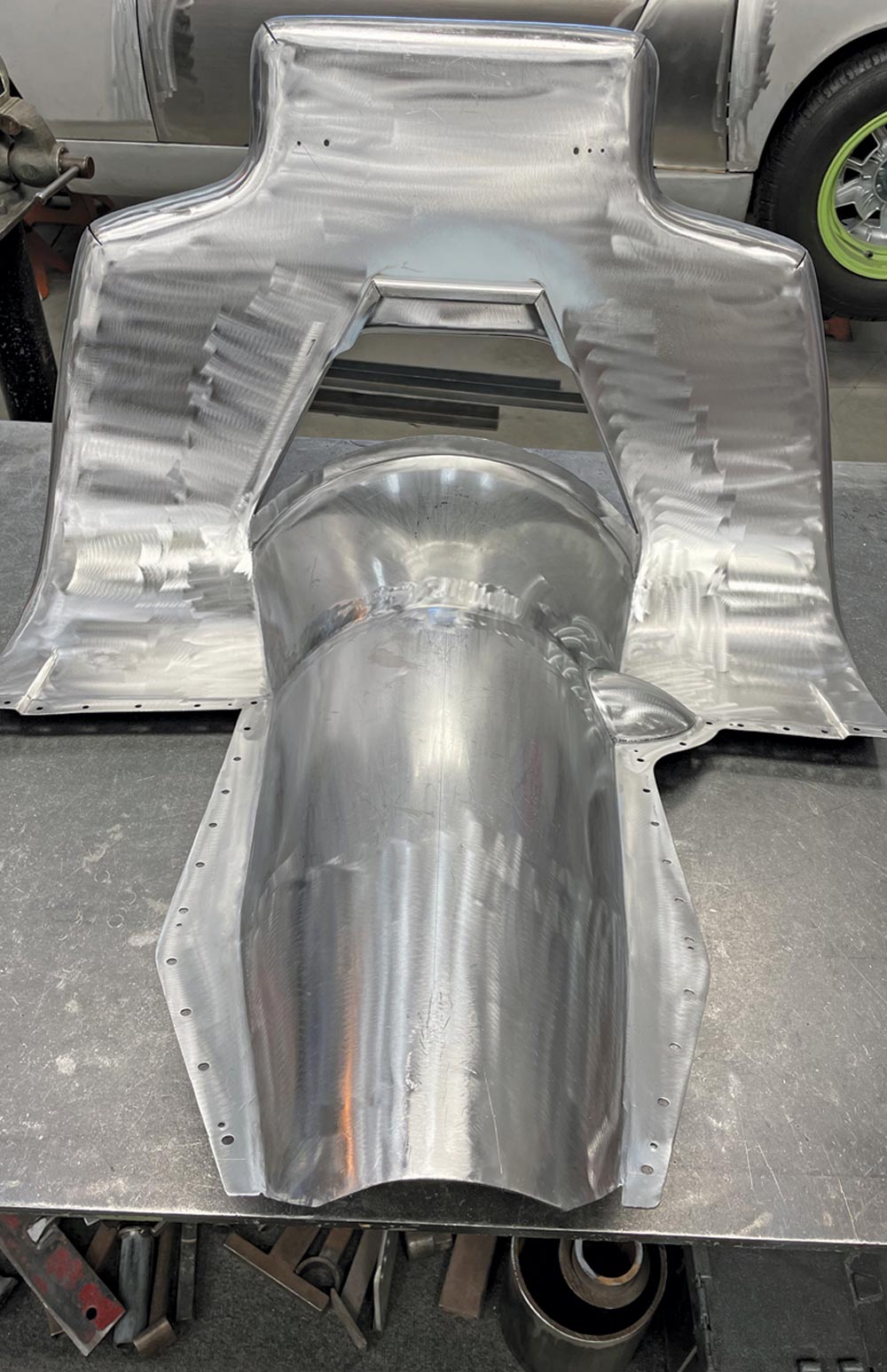
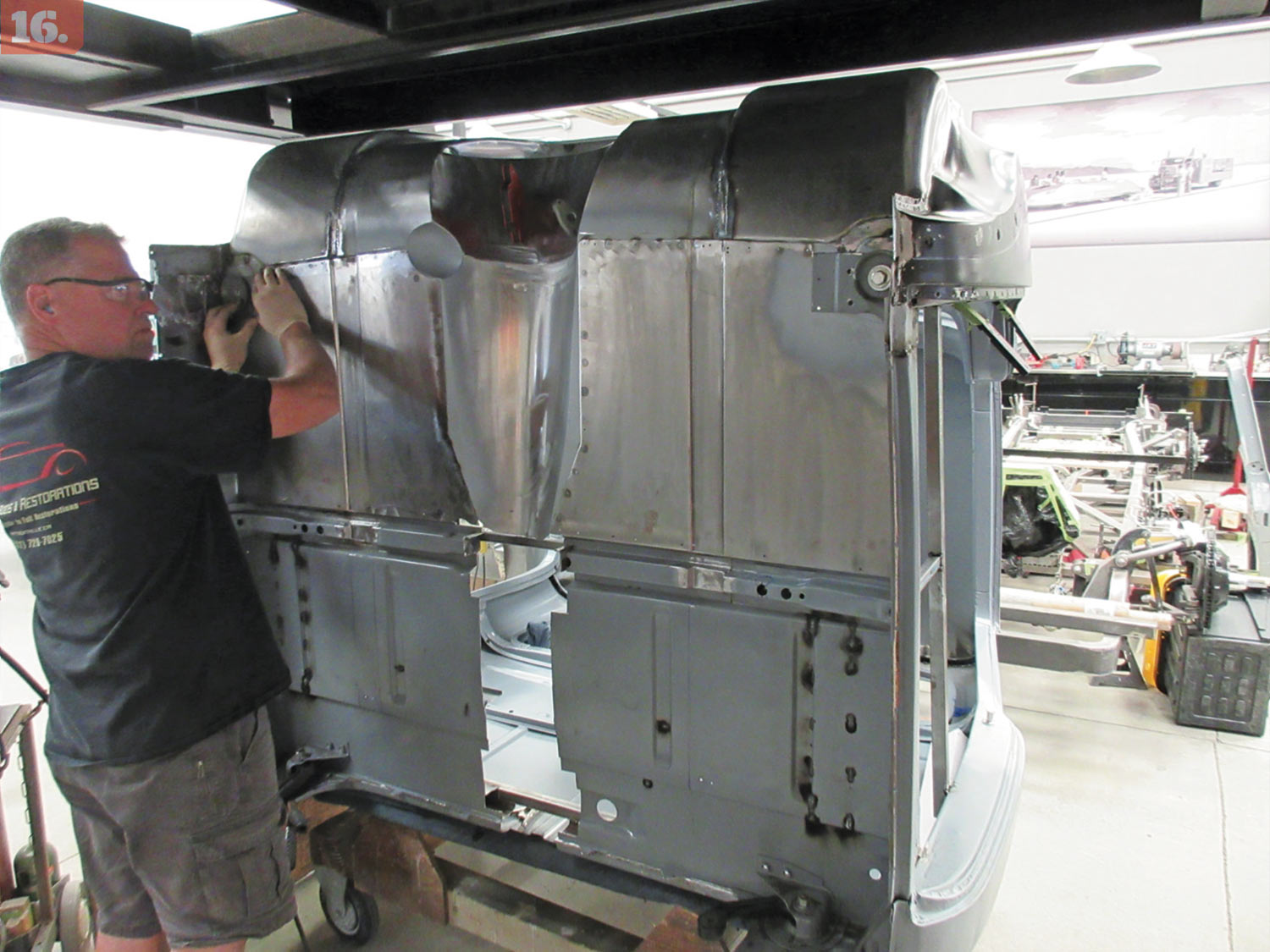
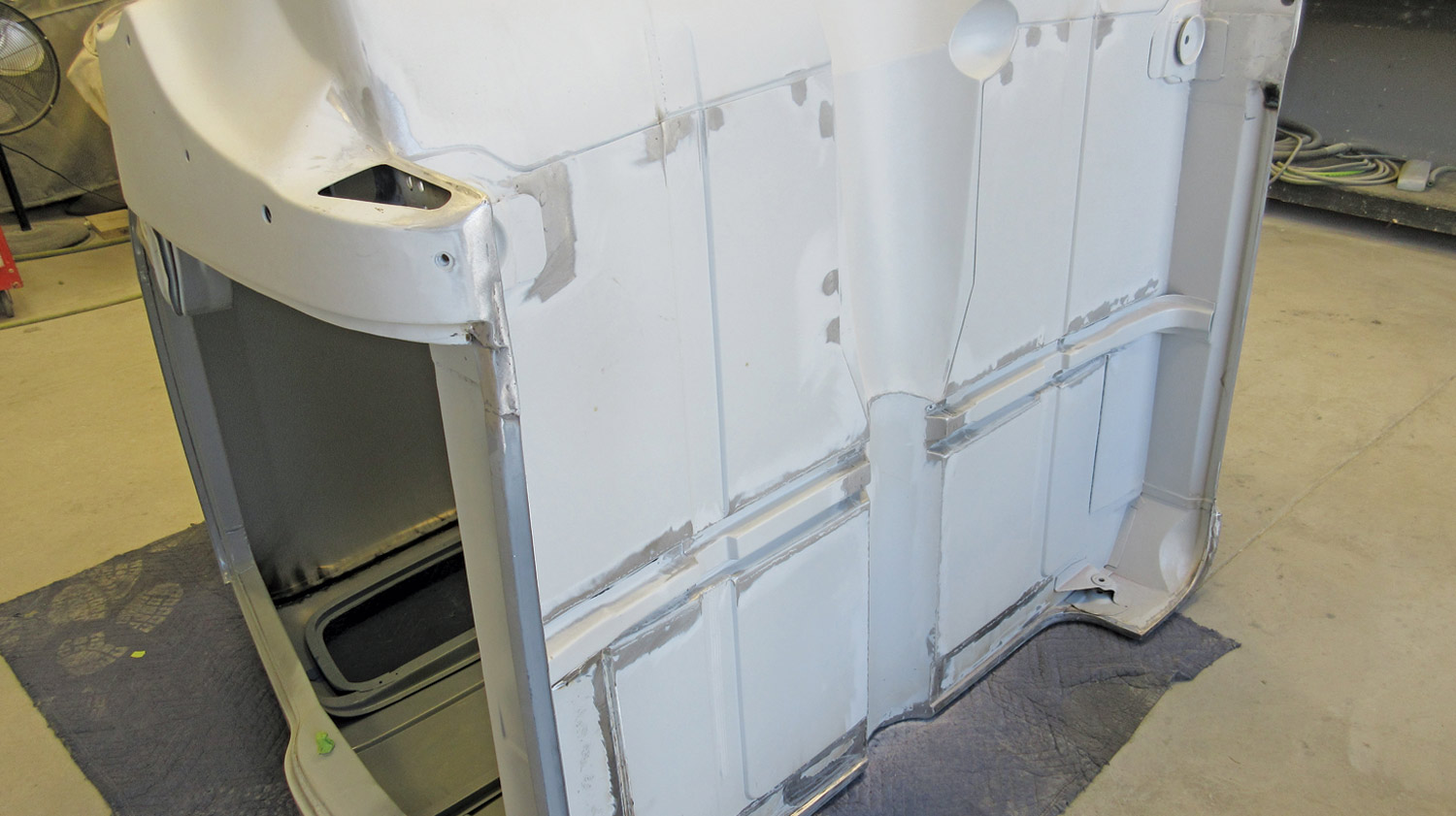
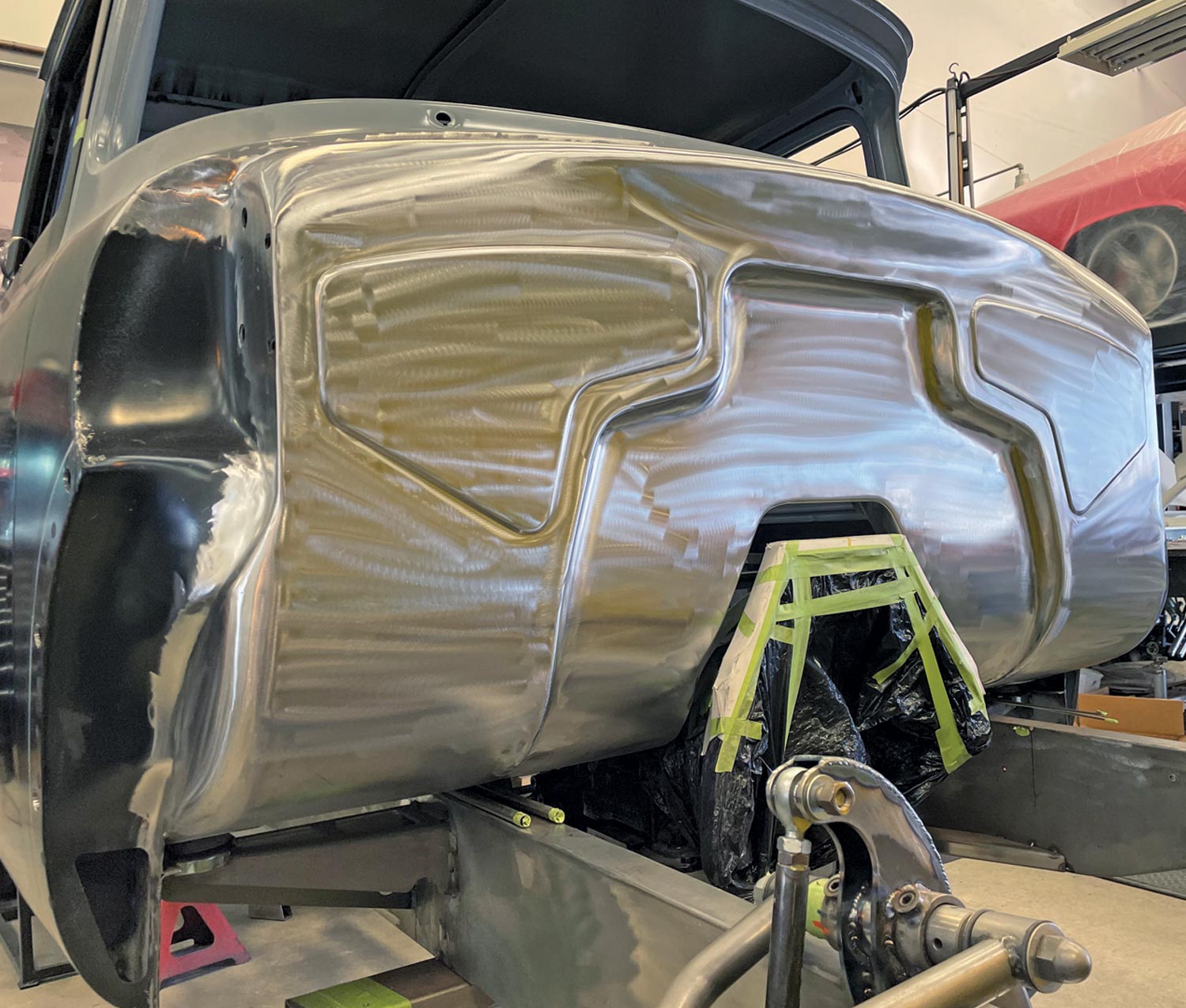
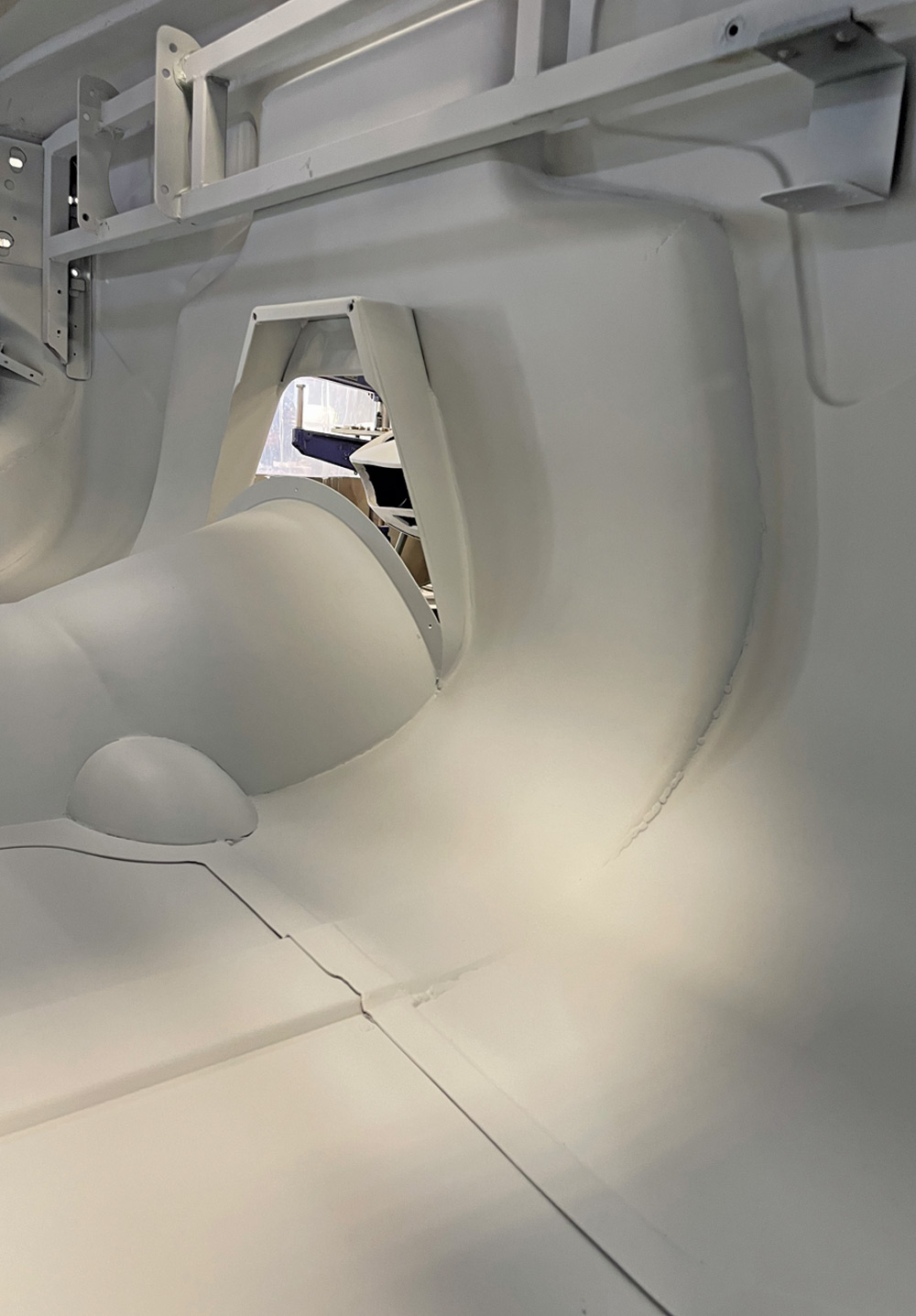
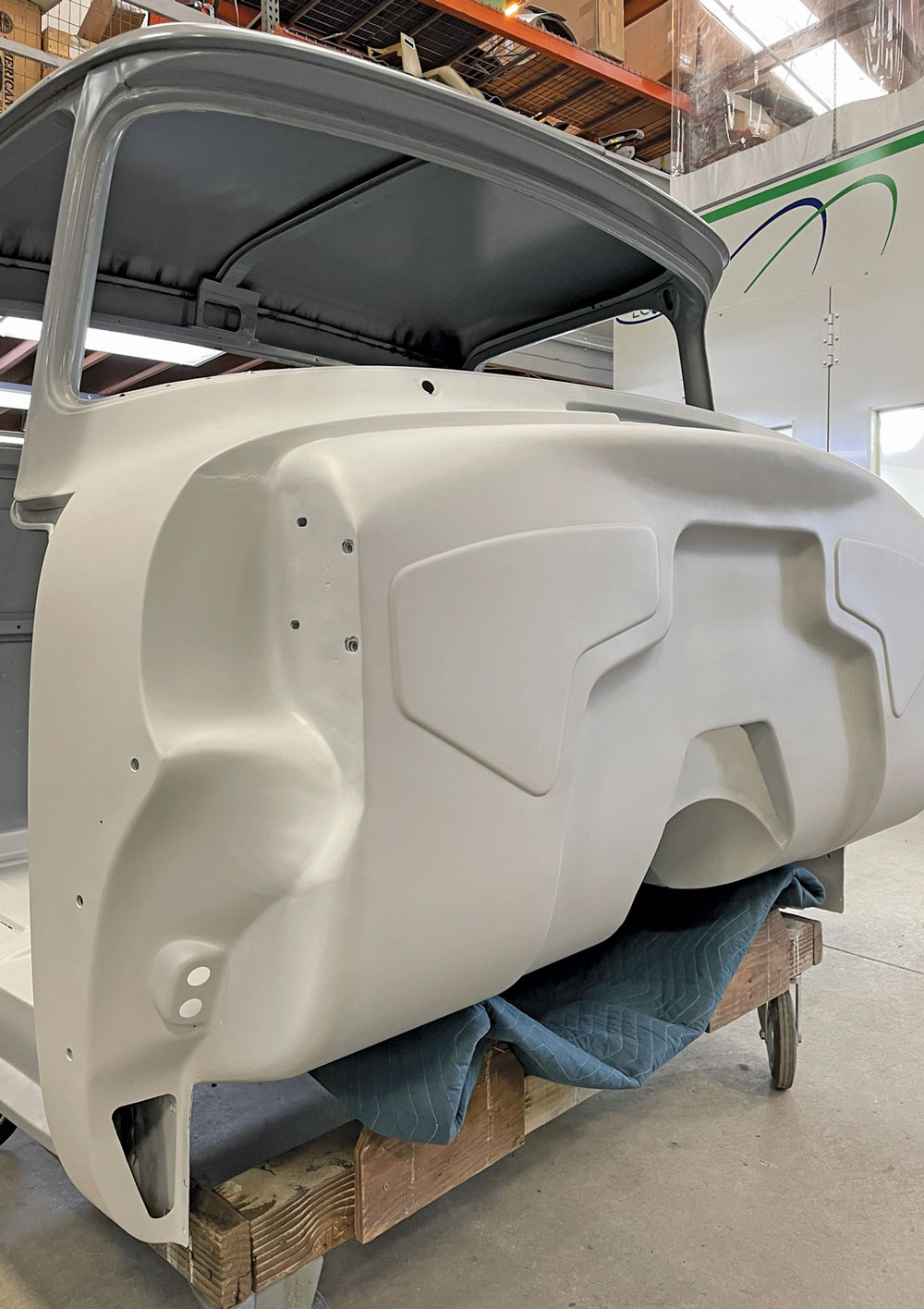
20. Here’s the face of the finished firewall. It will provide a perfect backdrop for the powerful engine.
