Tech
InTheGarageMedia.com
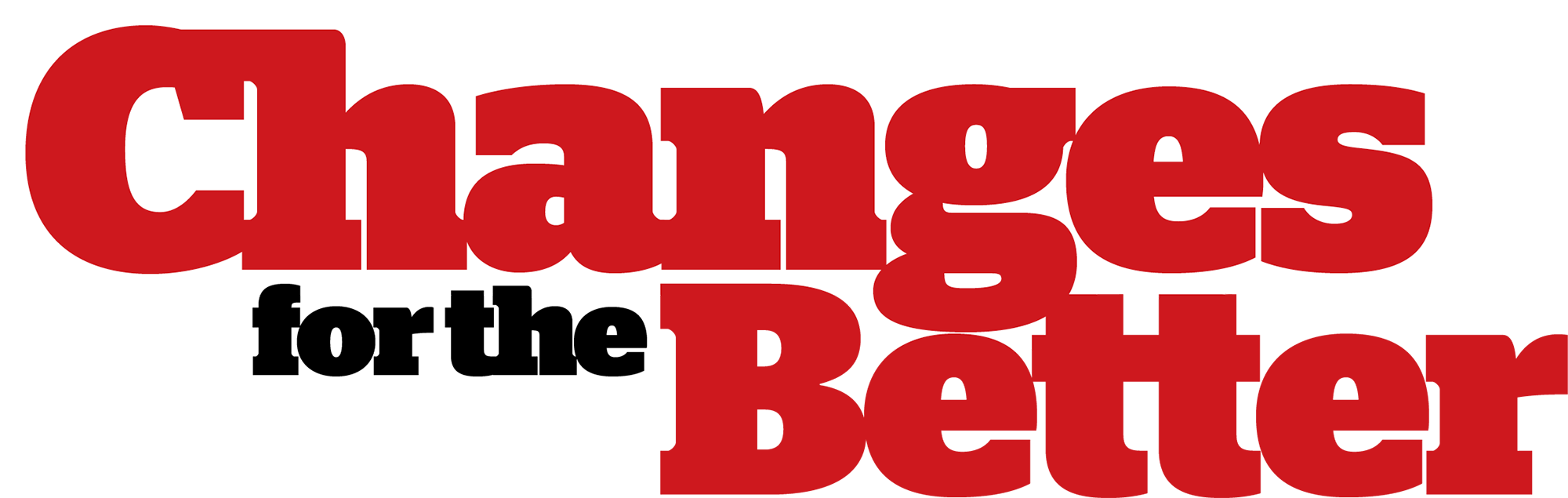

oe McGlynn is working on a very cool project: a chopped and sectioned ’56 Studebaker pickup inspired by the famous Rod & Custom Dream Truck. While he’s not building a clone, it does incorporate some major styling themes from that historic project.
McGlynn started this truck many years ago, but then “life got in the way” and his progress was halted for several years. After moving from California to Missouri and building his dream shop on his property, the truck project was finally revived.
Over the years, McGlynn’s tastes have become more sophisticated, so in Version 2.0 of this project, he decided to revise some of the initial work. The truck will feature a completely custom-built bed. He realized the rear wheels were a bit too wide for his design. Unfortunately, the four-link suspension outside the framerails prevented him from moving the wheels in as much as needed.
This required a complete redesign of the rear chassis and suspension, which McGlynn modeled in CAD. Having a digital model not only allowed him to fine-tune all the necessary dimensions, he could also examine the clearances in the “tight” areas and could send digital files out to have many of the components precisely laser cut. This was done by a company named SendCutSend, which saved an enormous amount of time in the fabrication process. It also allowed him to work to very precise tolerances.
McGlynn used a Narrowing Kit from Mittler Bros. to keep the axle bearings accurately aligned when he narrowed the rearend. This kit has sleeves that go in the bearing blocks in the third member and in the outer bearing housings. A precision-ground shaft fits through all these sleeves, precisely aligning the outer bearings before welding. It is essential to weld all of the brackets to the axle housing before installing the outer bearings since the welding on the brackets will distort the axle tubes.
Another product that proved quite helpful is the kit from Paul Horton’s Welder’s Series, which created the beautifully rounded corners where the rear crossmember connects to the framerails. This provides the same look as mandrel-bent tubing, but you can accomplish the task in your own garage.
As you look through the photos, you will appreciate many ways the latest technology can offer help for the homebuilder.
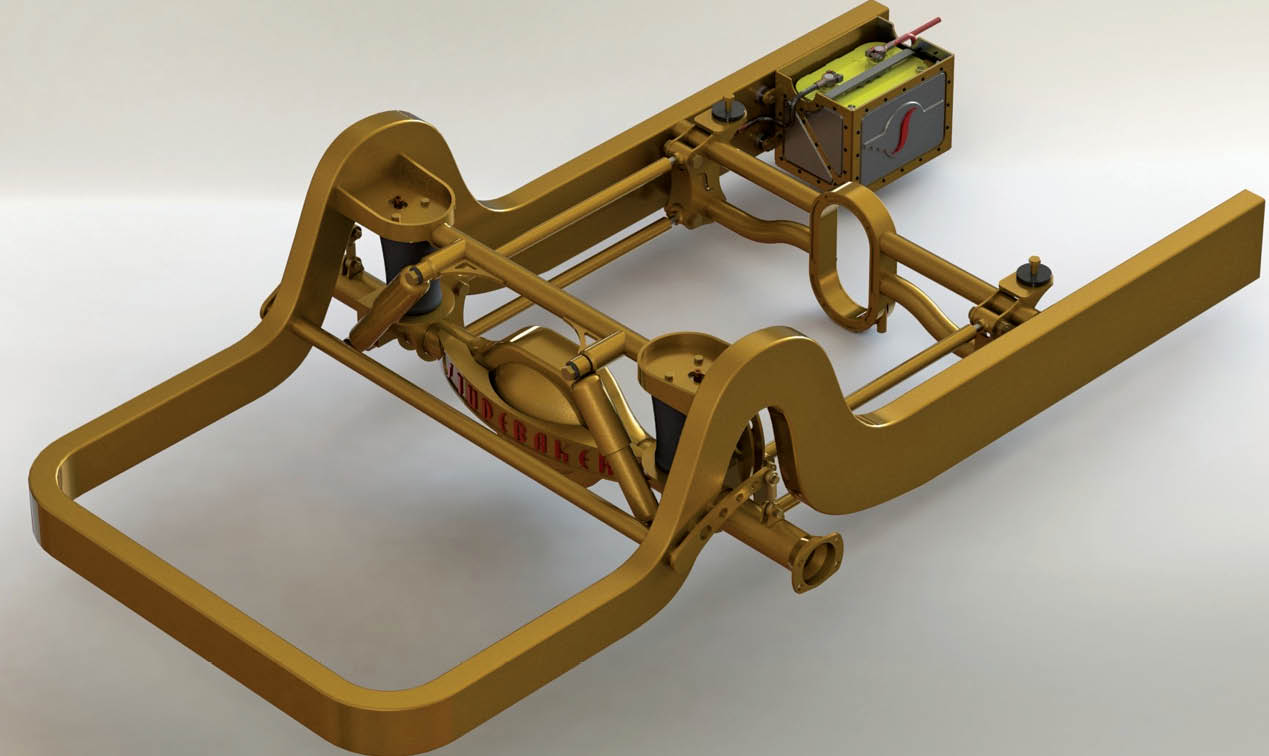
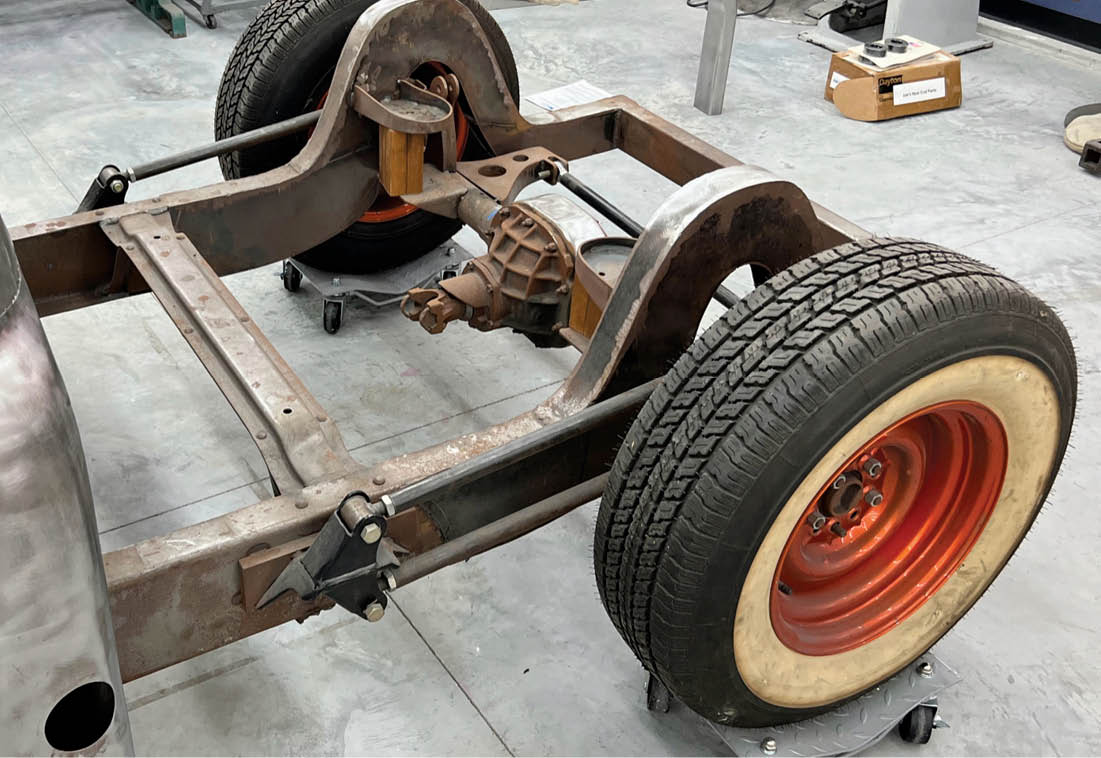
2. The rearend was originally set up with the four-link system outside the framerails. This prevented McGlynn from narrowing the rearend as much as he needed so changes were required.
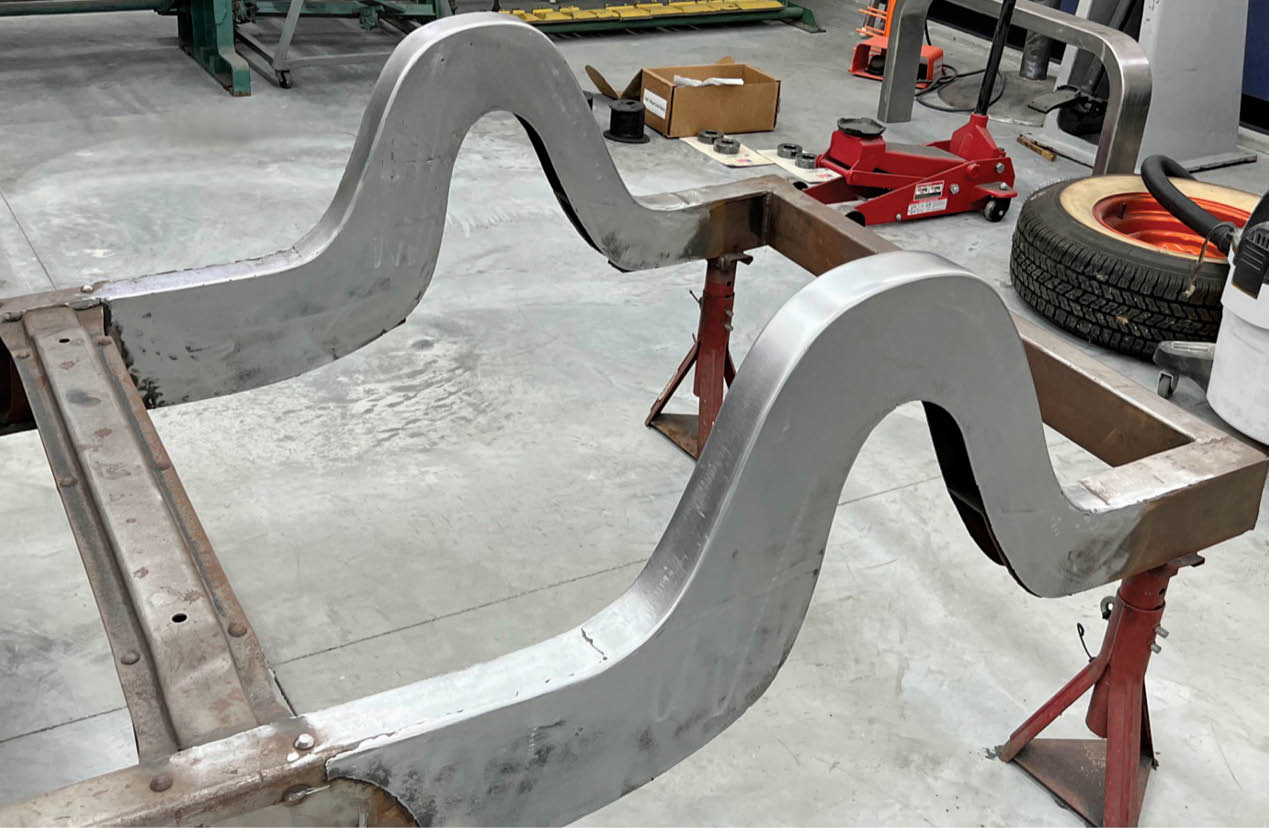
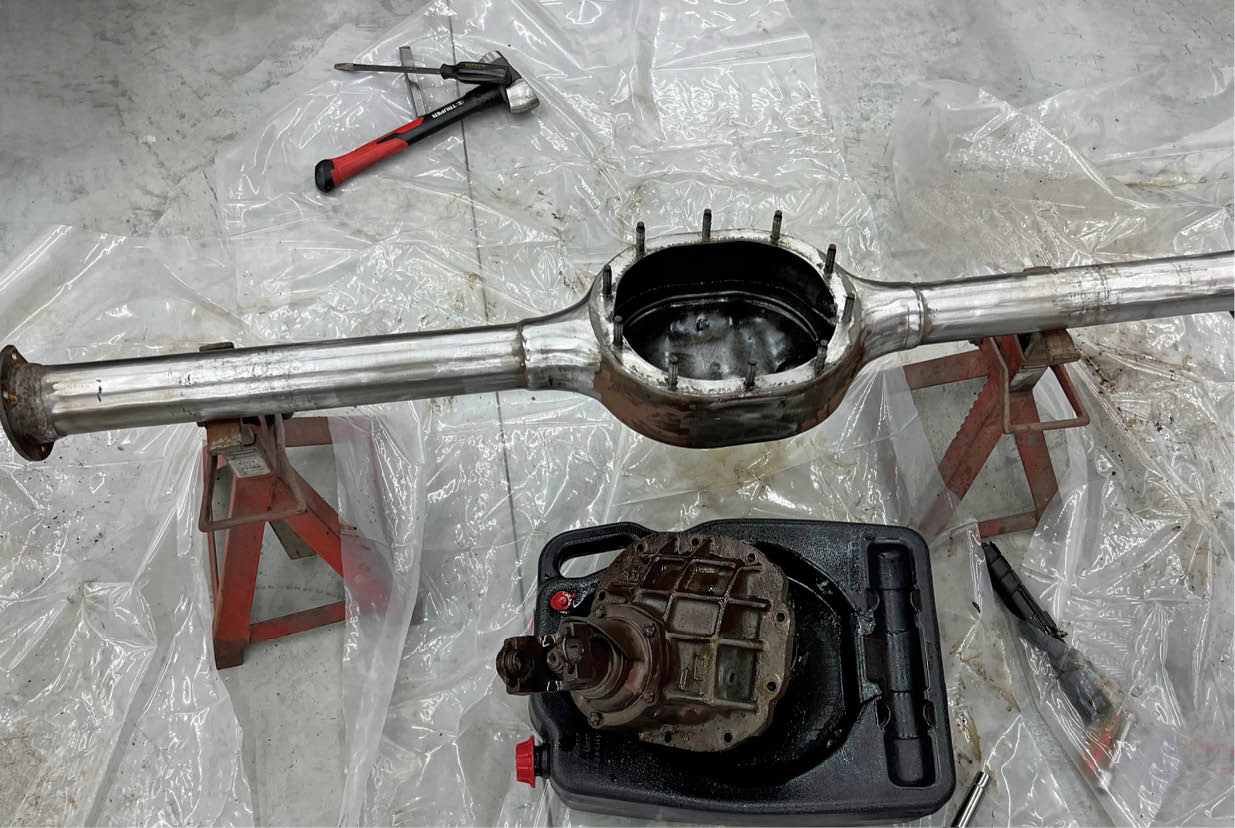
4. The rearend housing was stripped of all its brackets and cleaned in preparation for being narrowed the desired amount.
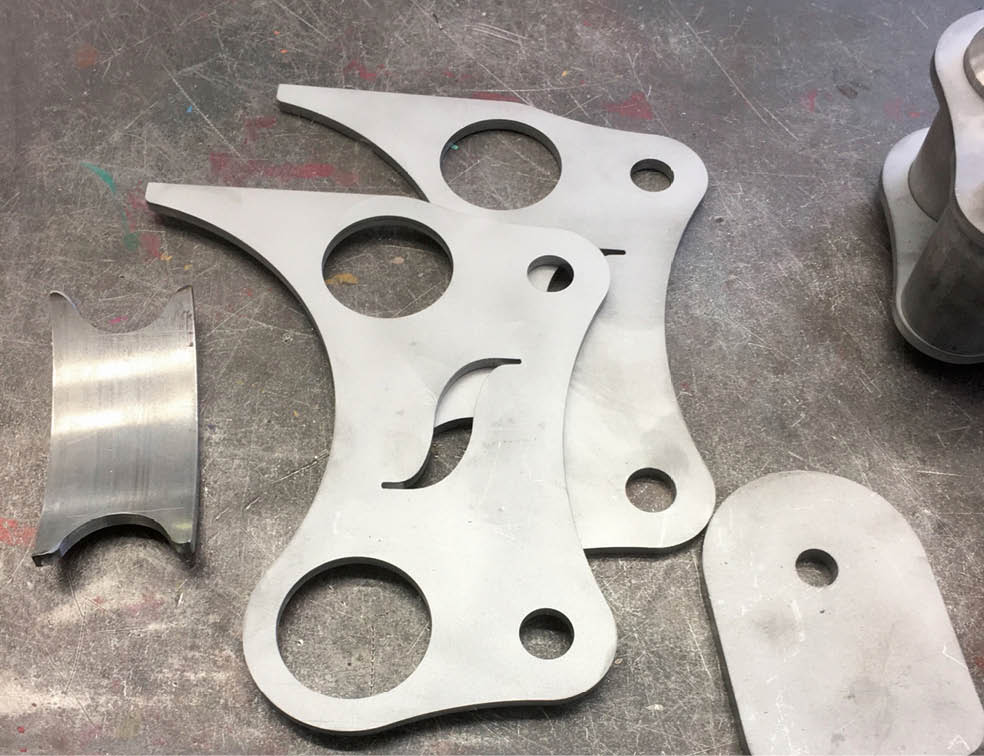
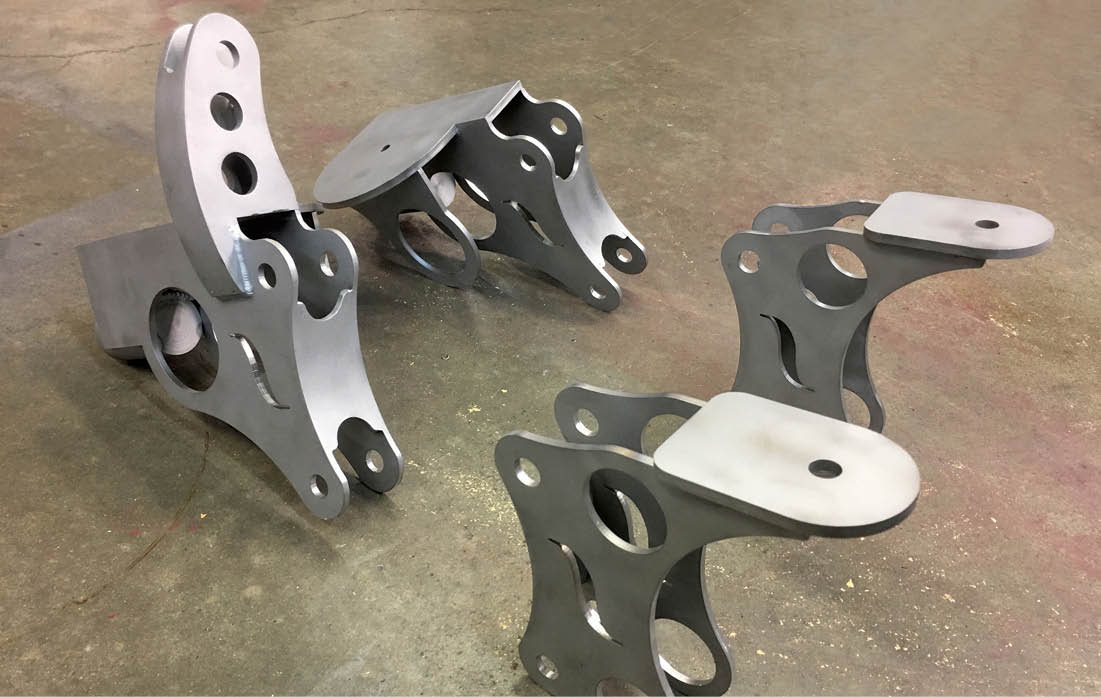
6. The laser-cut pieces were fitted together, checked for squareness, and welded into sub-assemblies.
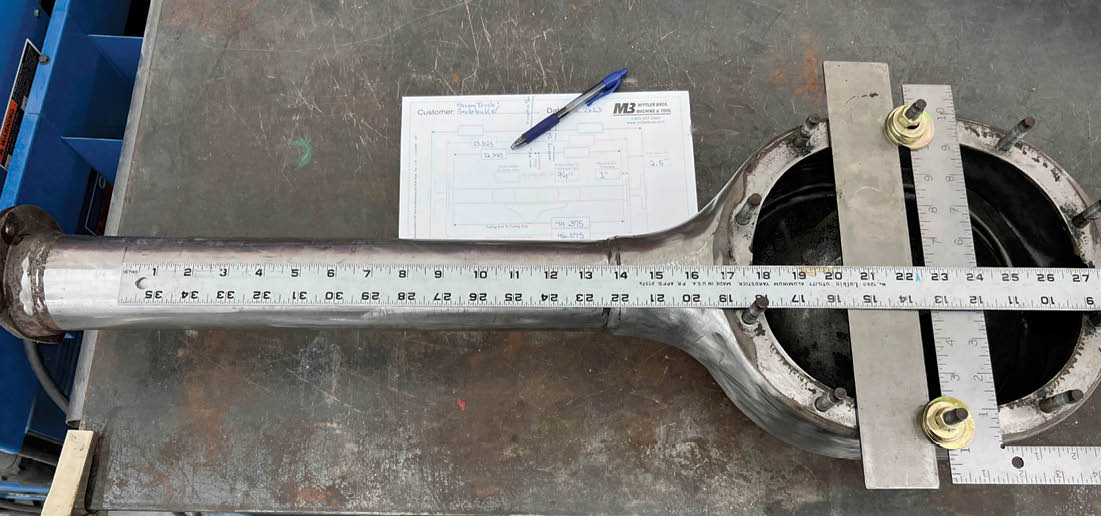
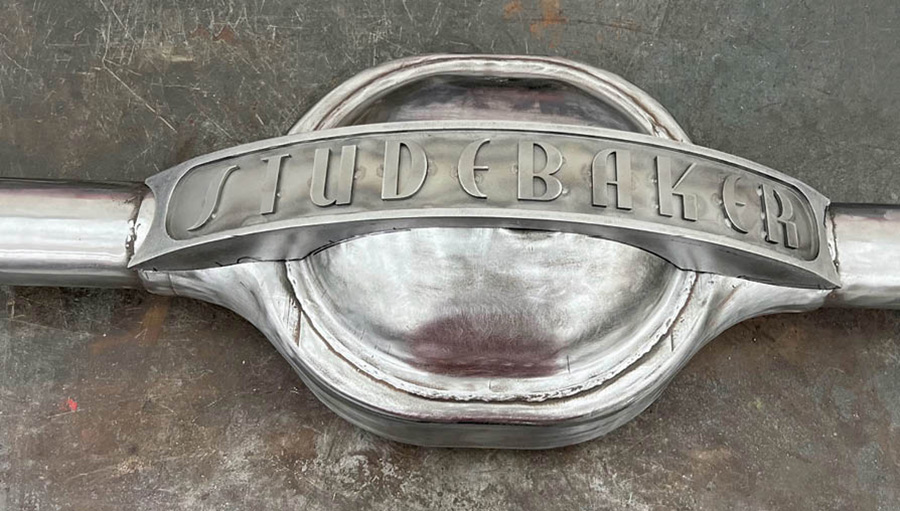
8. A brace featuring the Studebaker logo was designed for the rear of the axle housing. Again, all the parts were CAD designed and laser cut, saving many hours of fabrication time.
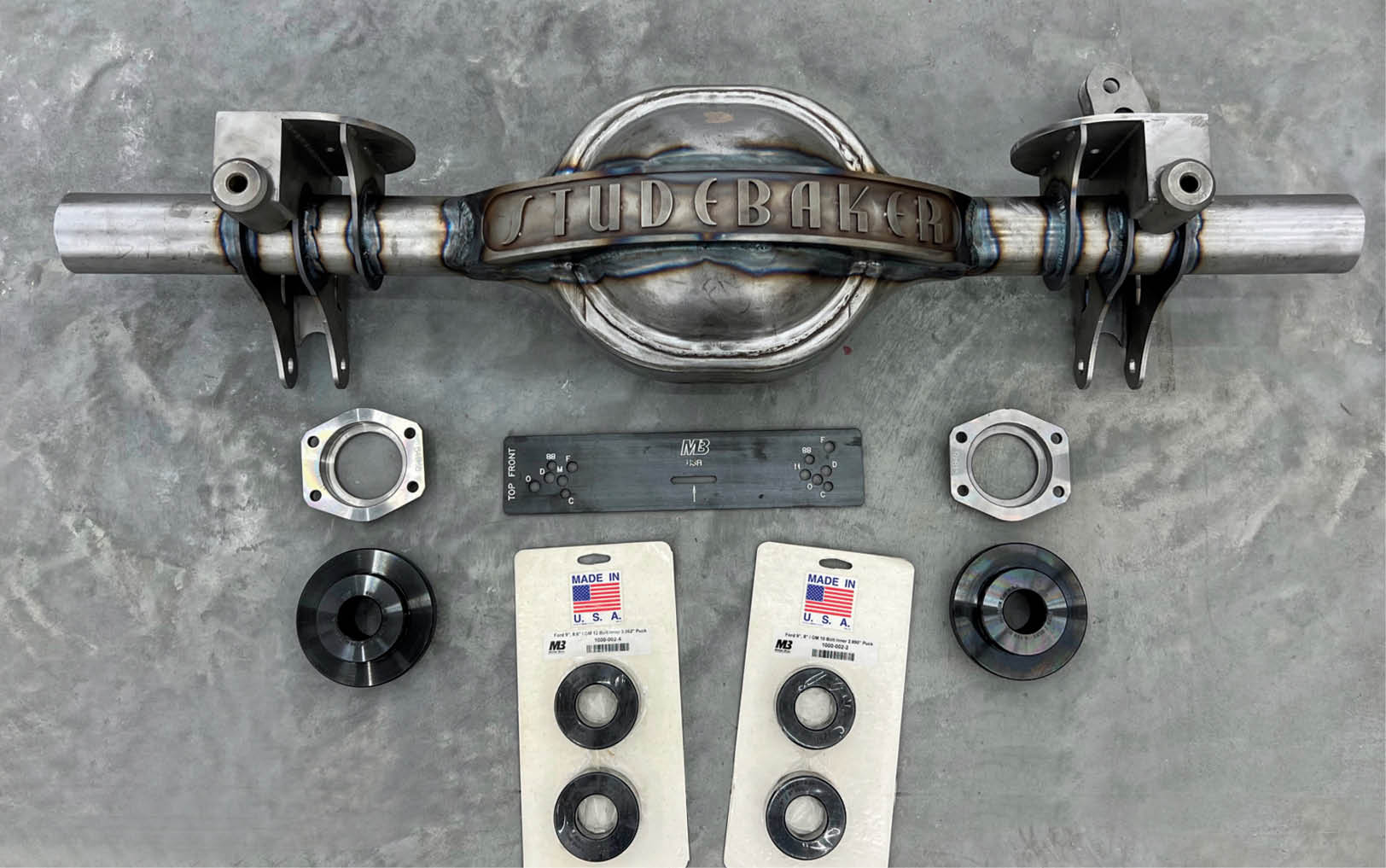
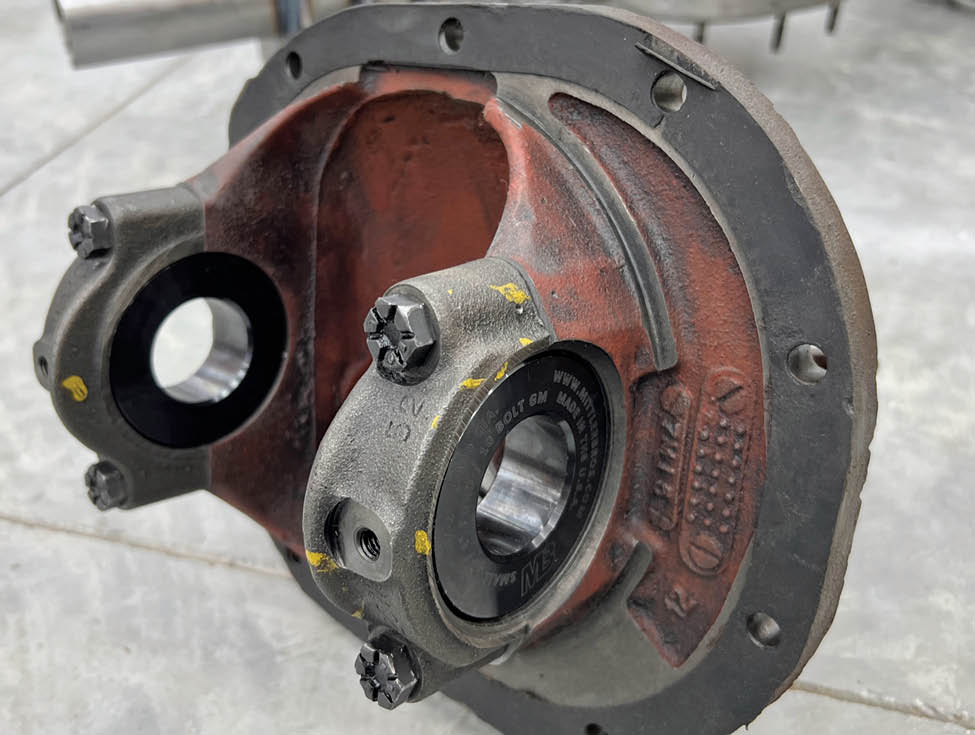
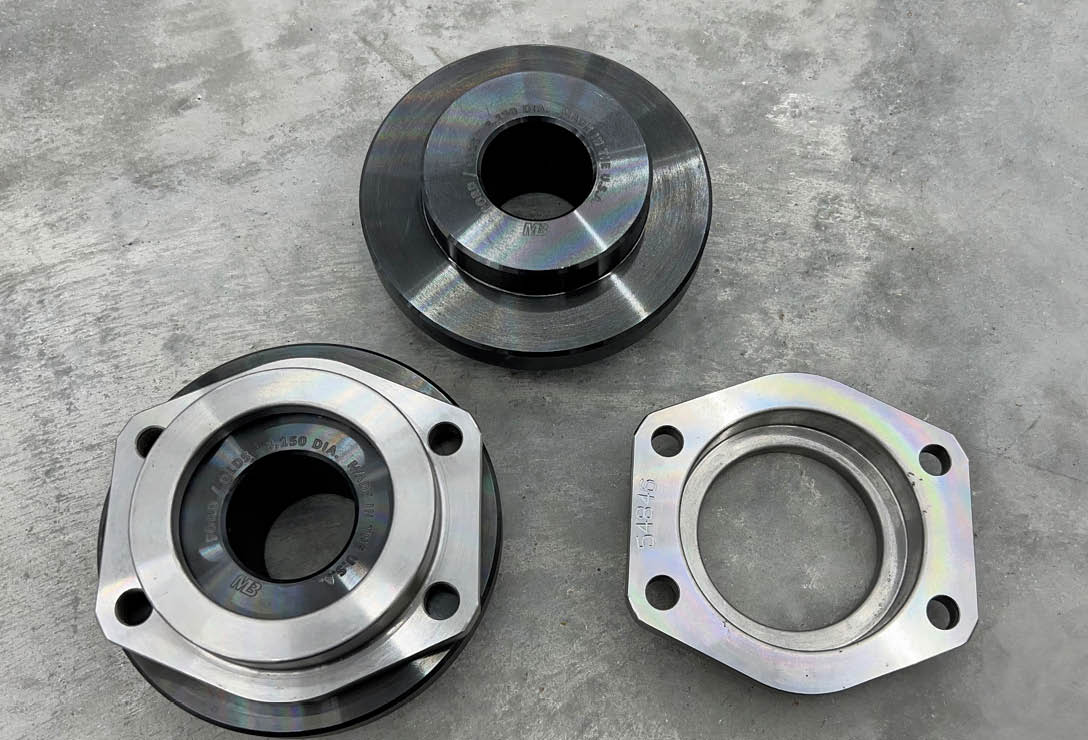
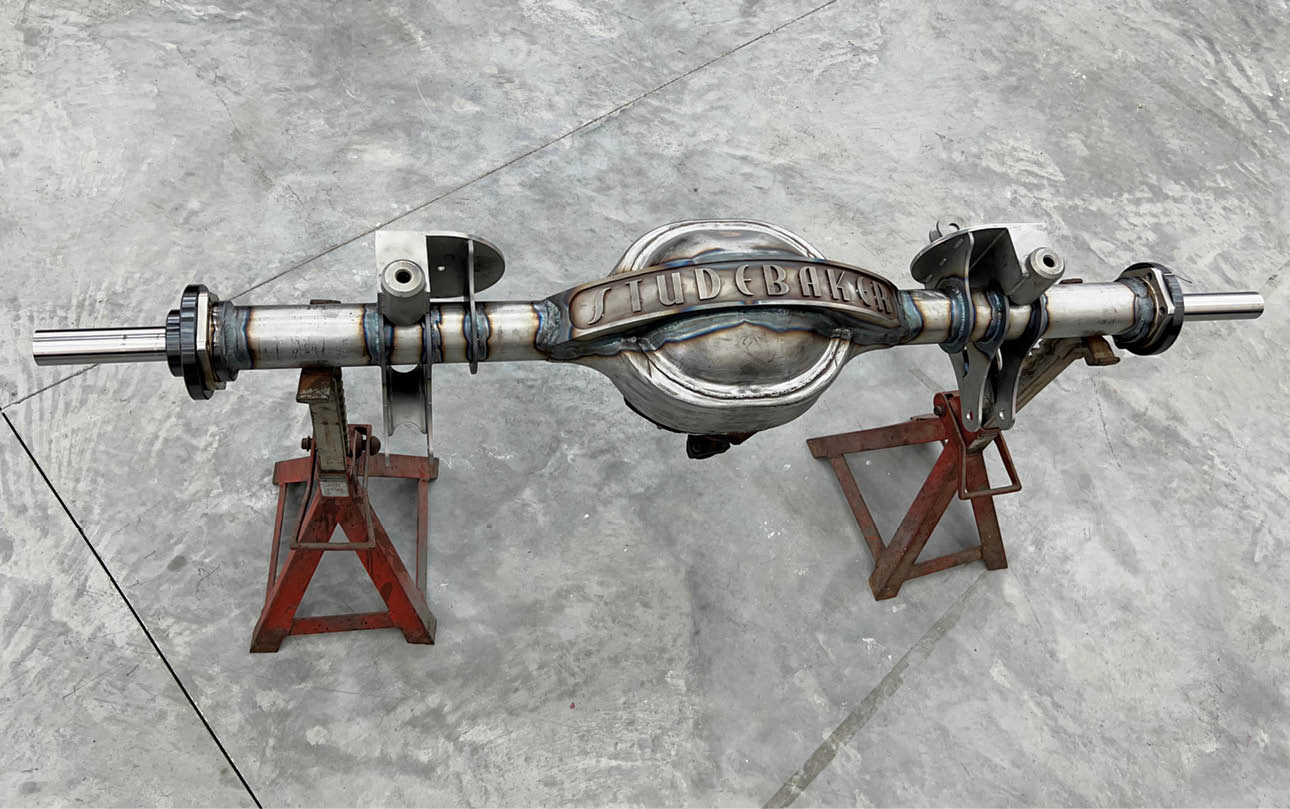
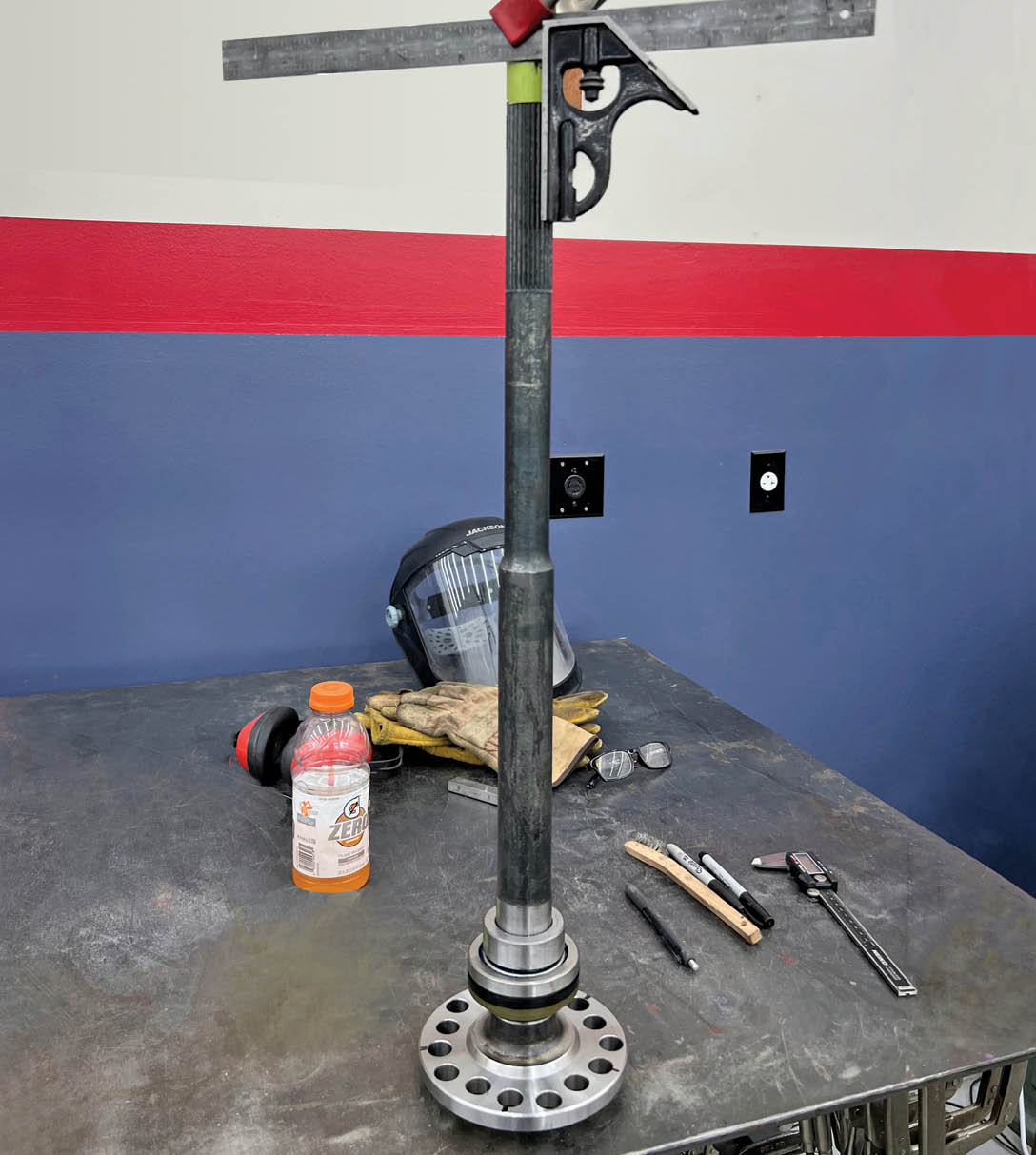
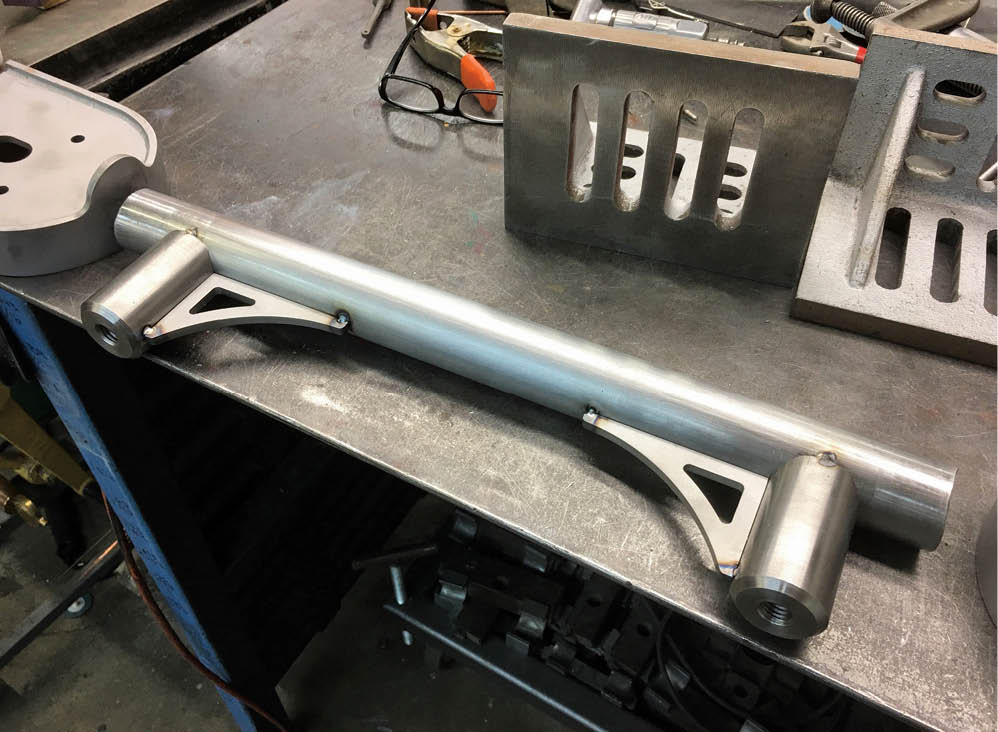
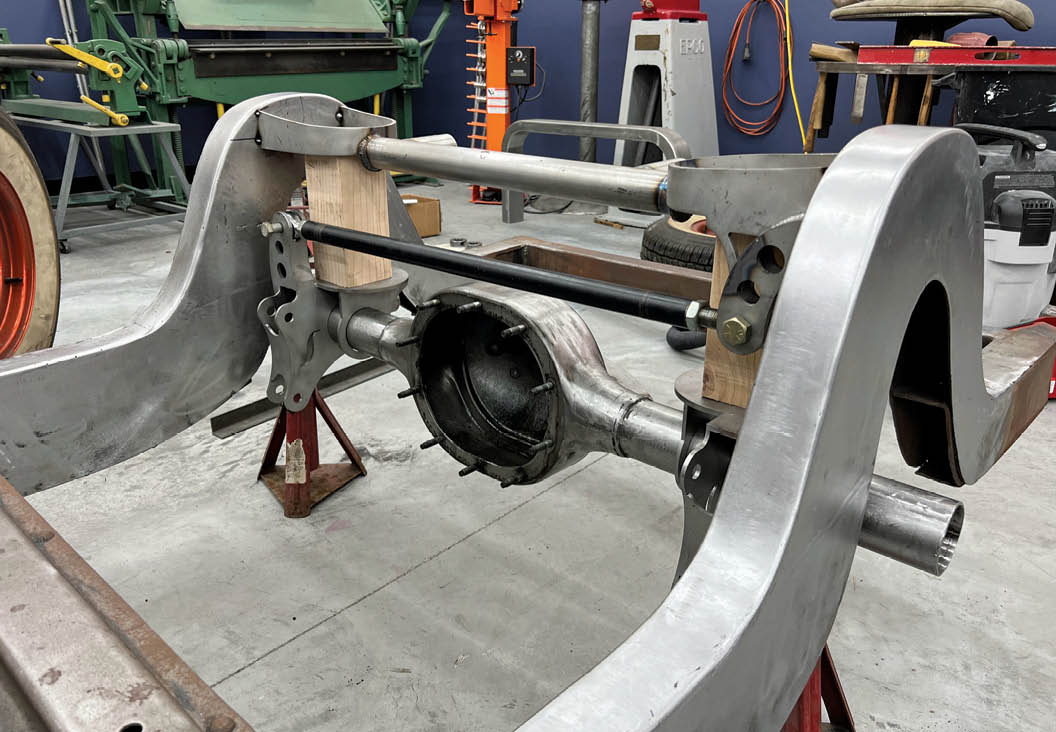
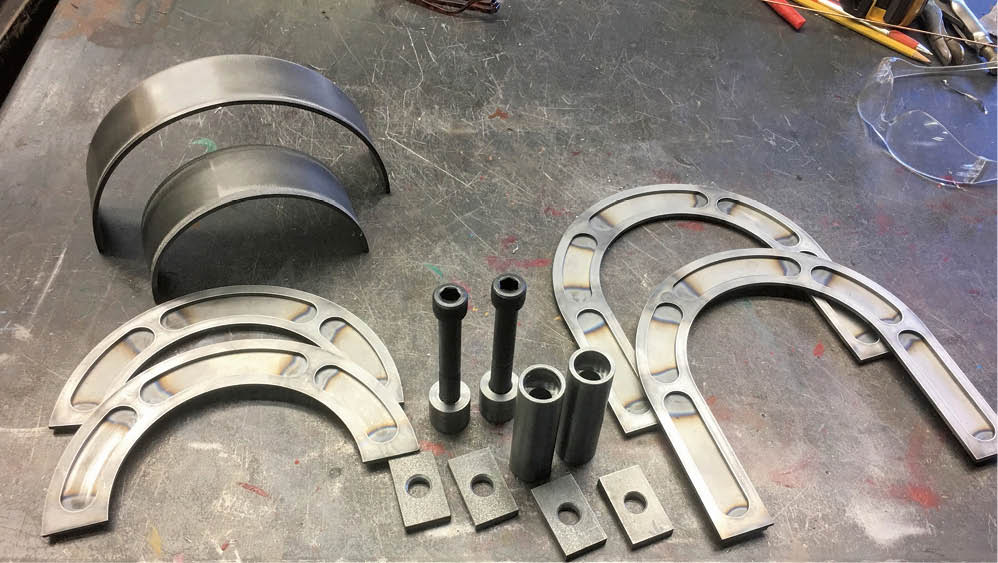
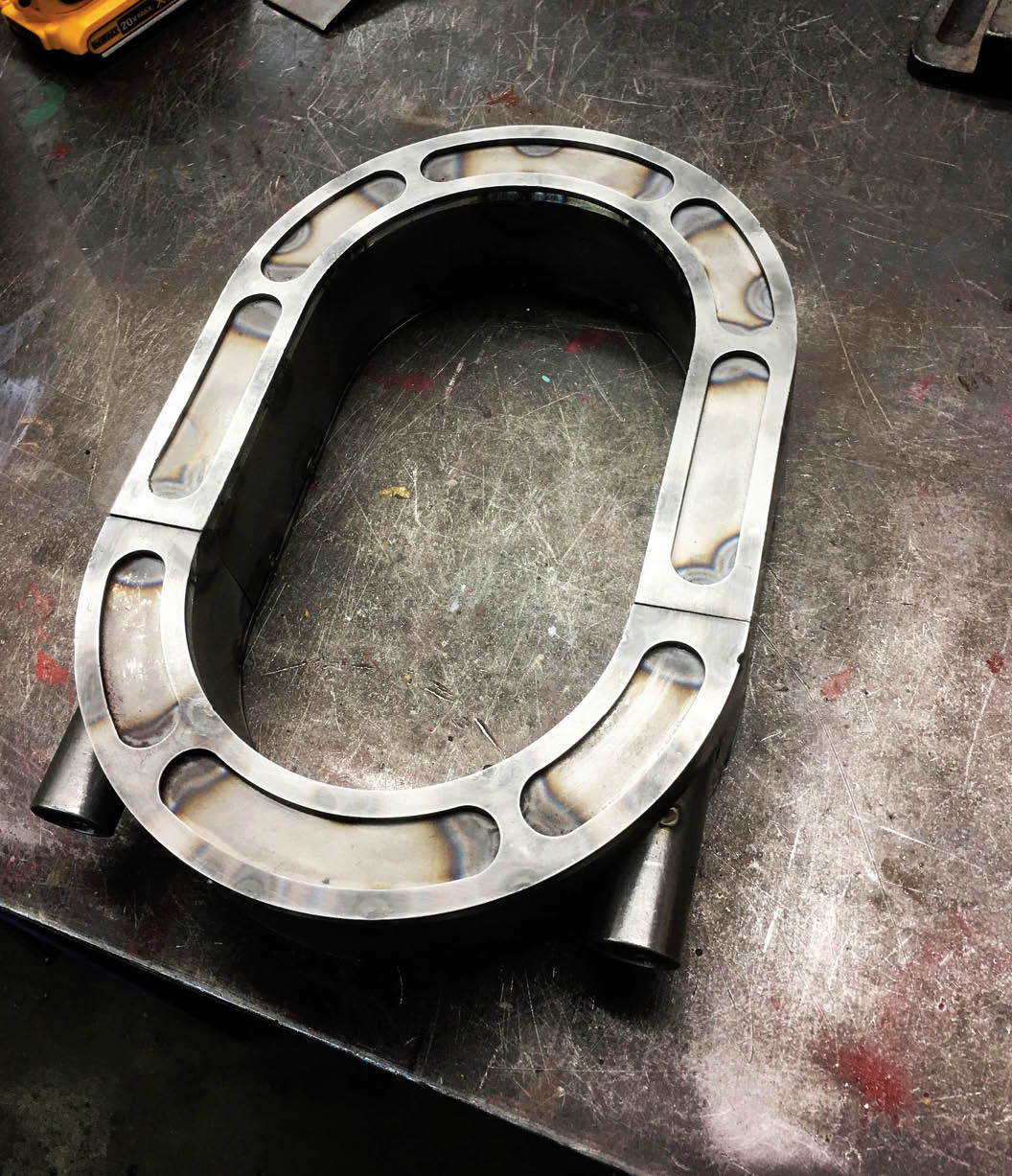
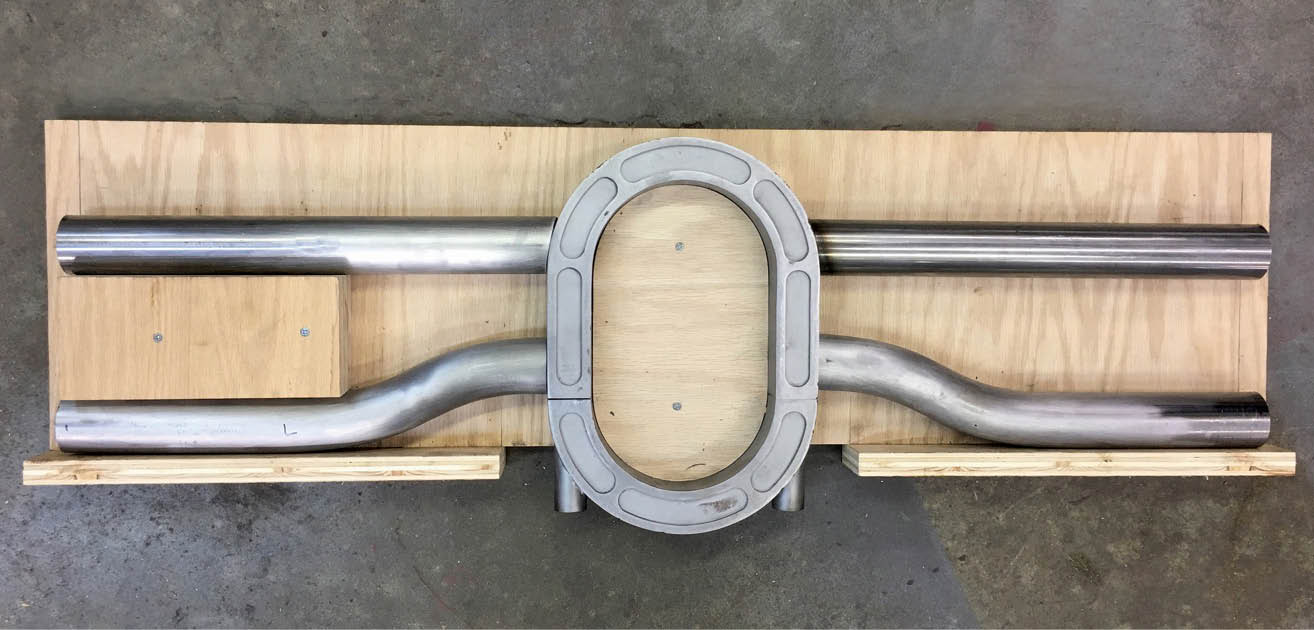
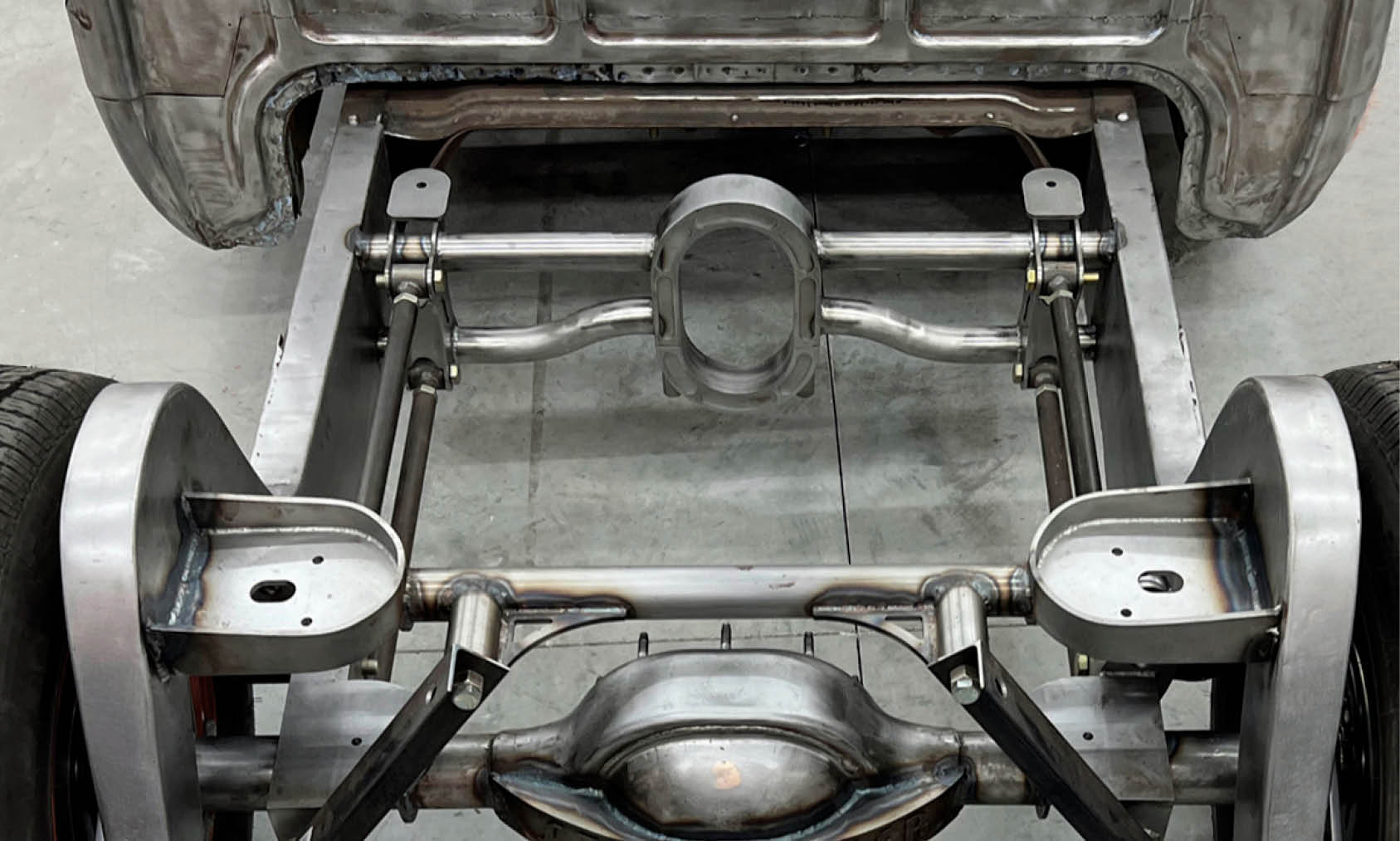
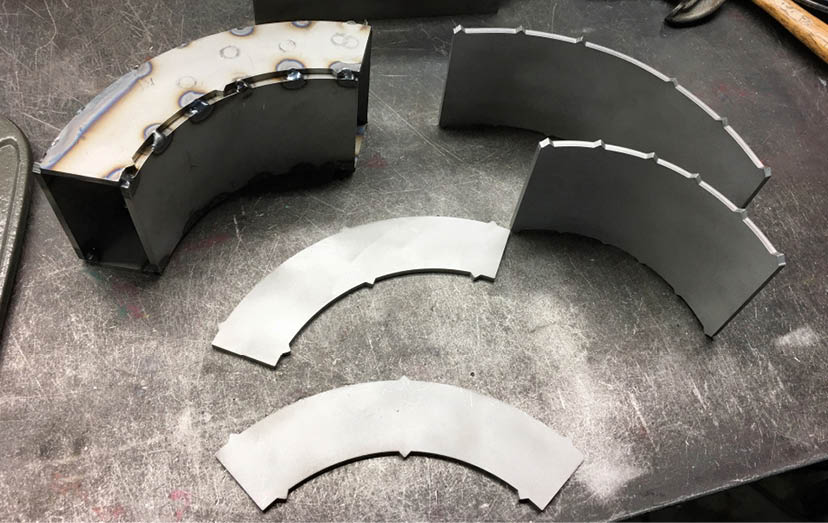
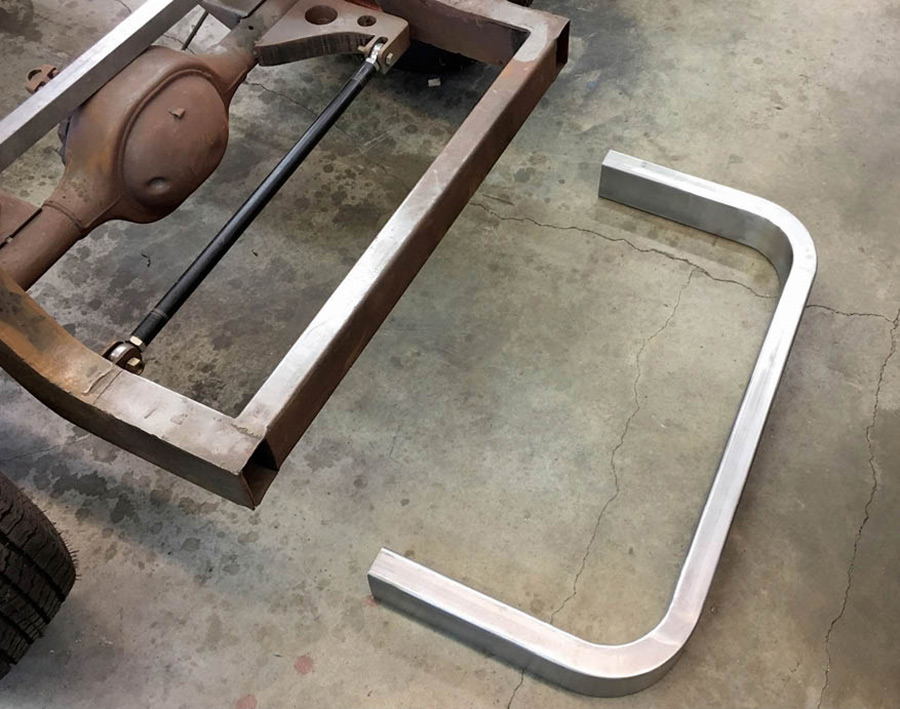
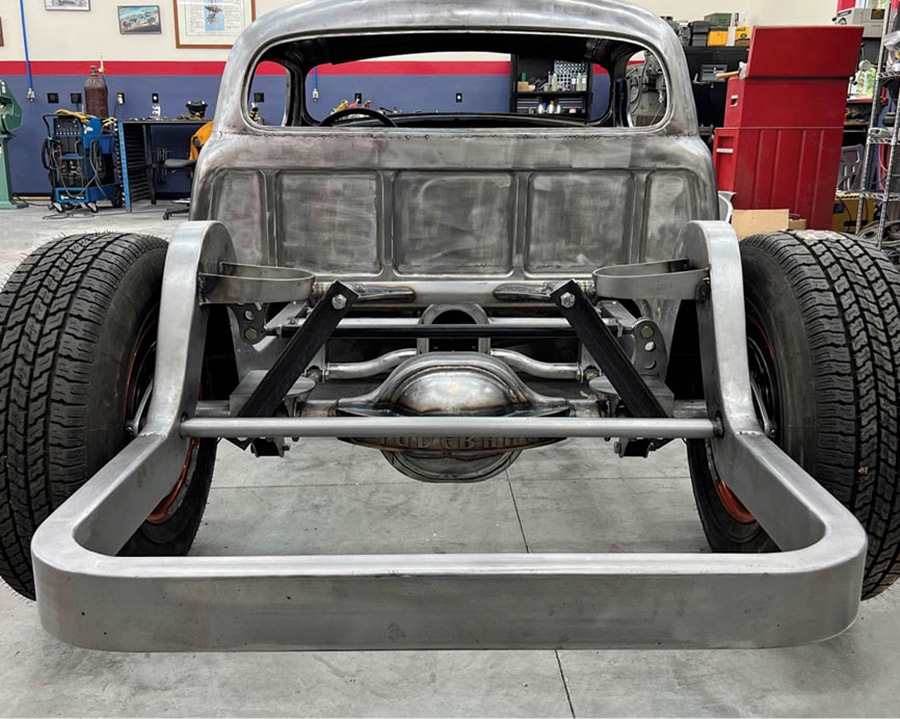
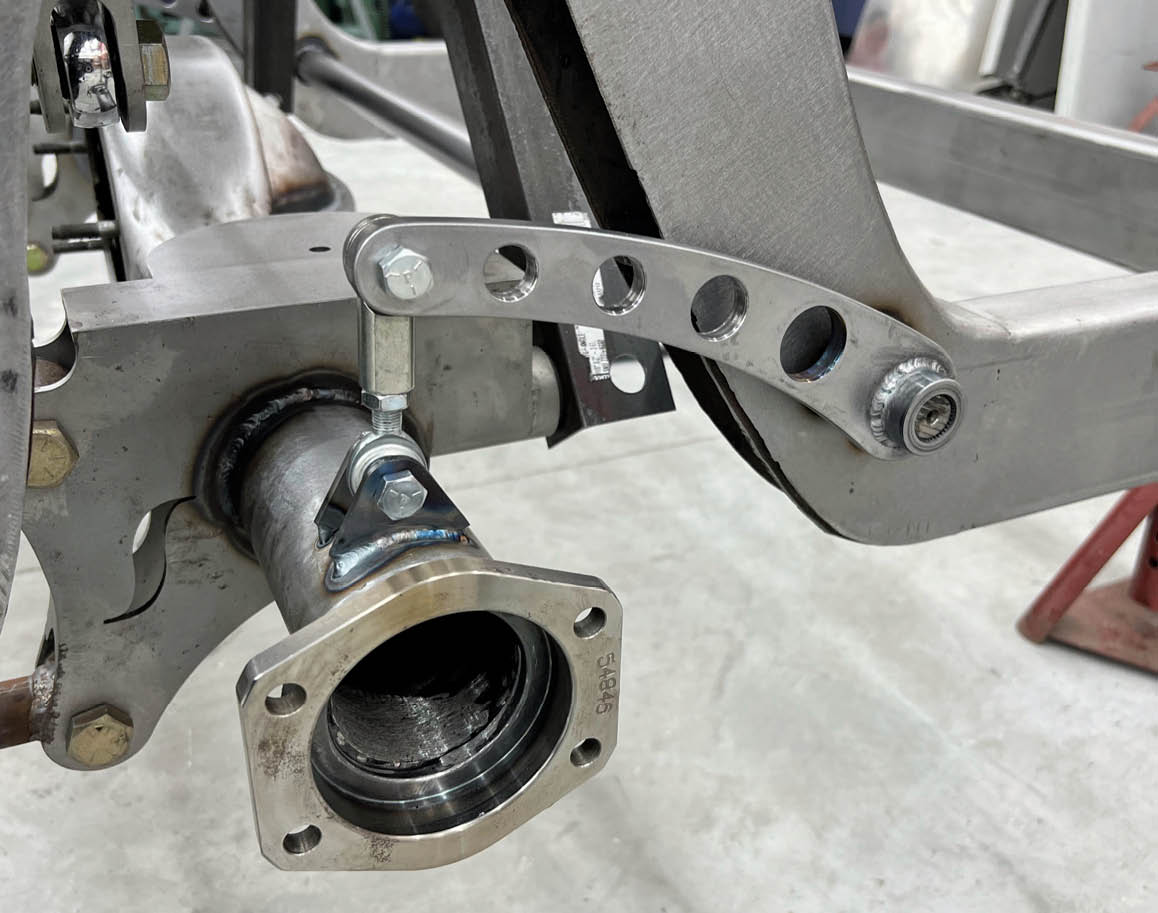
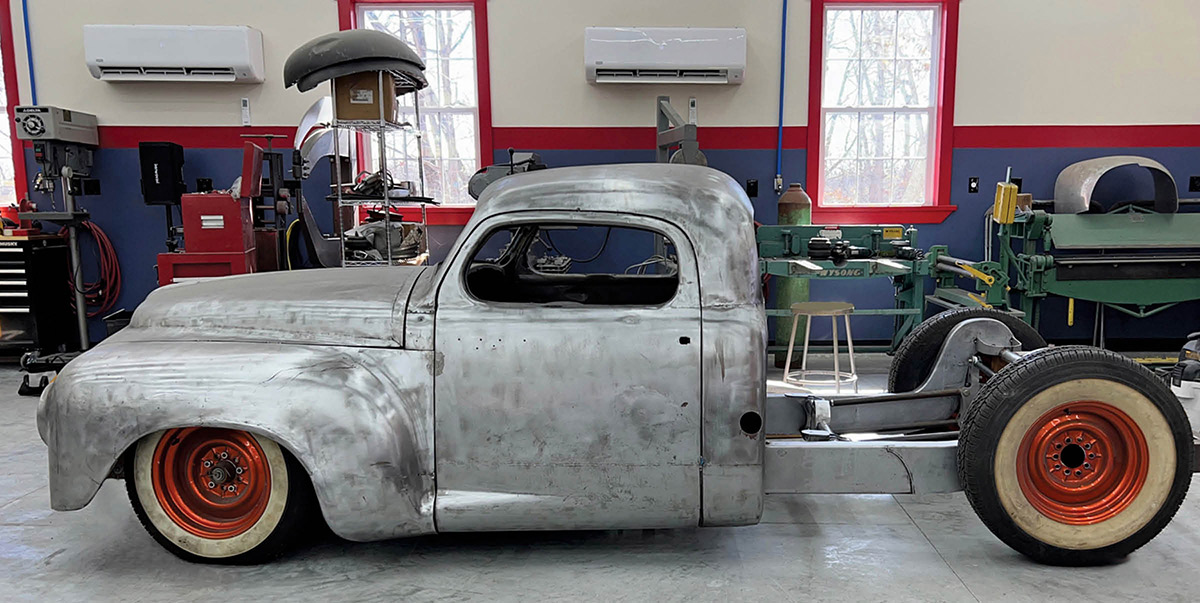
