



uring the course of most any classic truck build, sooner or later we’re going to do something twice. Double-checking ourselves can certainly lower the risk, but wouldn’t that also be doing something twice? If it is, it should be OK here since double-checking a hood-to-cowl gap goes a bit quicker than repainting a hood and cowl.
For an earlier issue, we did a little tech story that dealt with hidden damage. The inspiration came with the discovery of depressions in our project ’55 Chevy second-series cowl. Being optically challenged, I didn’t see it—and I must not have felt it before installing brand-new Brothers hood hinges right over the damage.
With the covered-up problem, mock-up alignment for the hood and surrounding panels was a struggle. We just couldn’t get our hood-to-cowl gap right without a box of shims. Our shop manual says: “If necessary, add shims between hood and hinge.” It says nothing about adding shims in other places. In order to achieve a factory-suggested 3/16 gap that still might later eat paint, we had to add shims at the lower hinge-to-cowl bolts, too.
Once we’d finally convinced ourselves that our shimmed-up hood-to-cowl relationship was as good as it would get, the mocked-up truck was disassembled for finish bodywork and paint. When the bare cab reassumed its position upon its rolling cab cart, one of us (the one with better vision) noticed two small dents in the cowl. Being right where hood hinges go, the dents caused snugged hinges to point slightly downward. So, that’s why so many shims!
As it sits today, the truck’s cab, doors, and frontend panels are all in first-round primer. The straightened-up cowl looks about right now, and we know the difference will effect hood hinge operation as well as our hard-earned hood-to-cowl gap.
When it’s time for final assembly, we’ll expect less trouble from the hood, hinges, and cowl. The trouble is now one of us (the one with the wilder imagination) is focused on the repaired-original hood’s rearward edge. Toward the center stretch of its lazy arch that edge looks a little flat to me.
Thinking back, we’ve been dealing with collision damage throughout our ongoing build. Years ago when the wrecked truck came to us, the original hood hinges were pretty wadded up. We don’t rightly recall if the hood’s rearward edge was catching on the cowl, but since the collision was a front-ender, it’s quite likely that it was.
At the time of this typewriting we haven’t actually seen the results of our earlier cowl repair. Instinct says we’ll see improvement and maybe we can toss some shims. So, what about the hood’s questionable rearward edge? When we see the hood adjusted, we’ll know what to do. If fine-tuning is necessary, we’ll be ready.
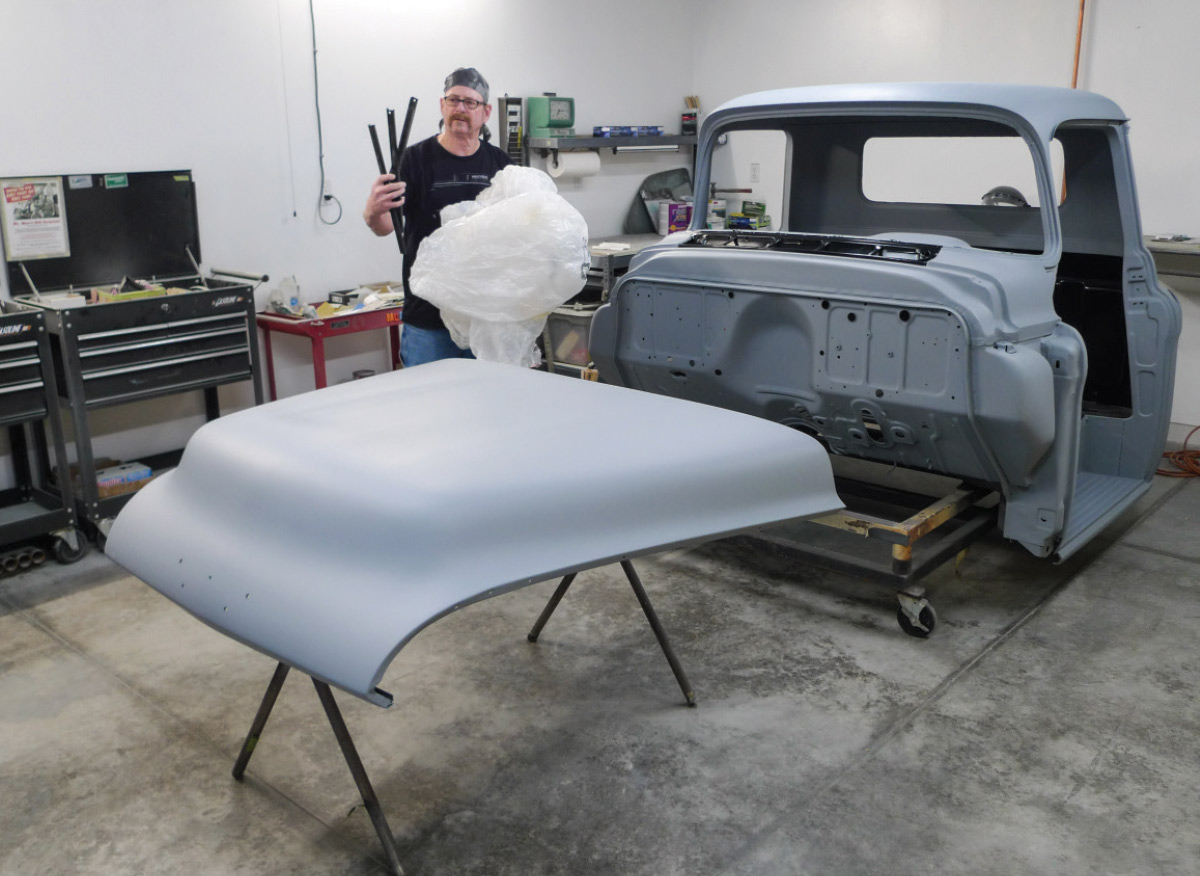
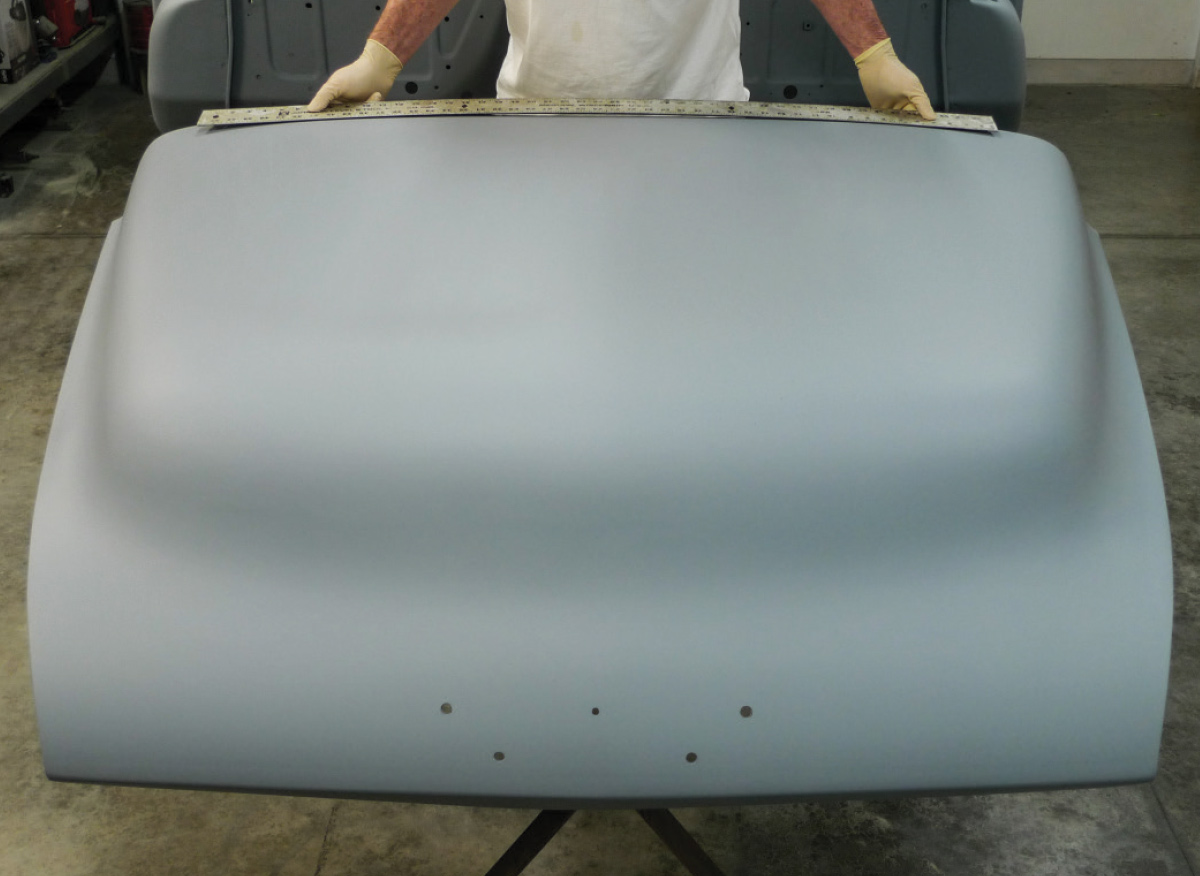
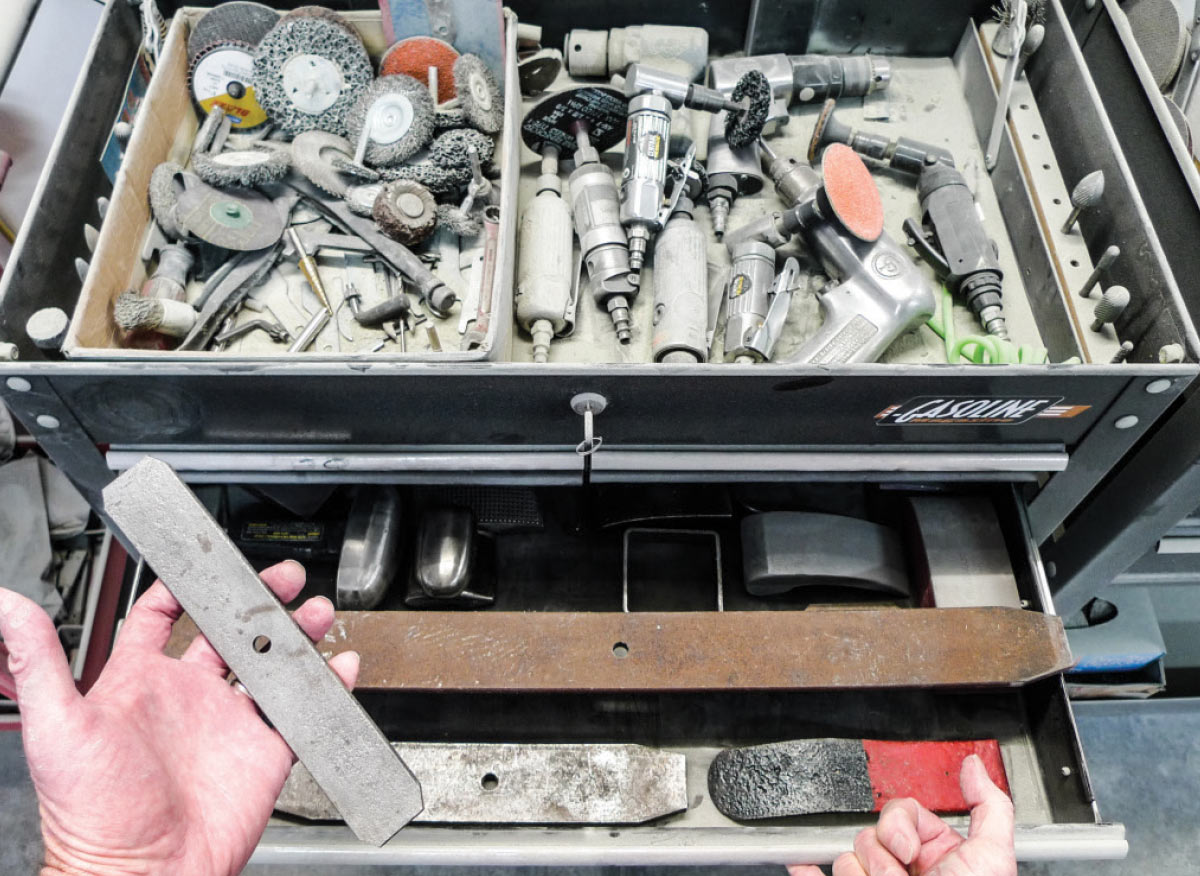
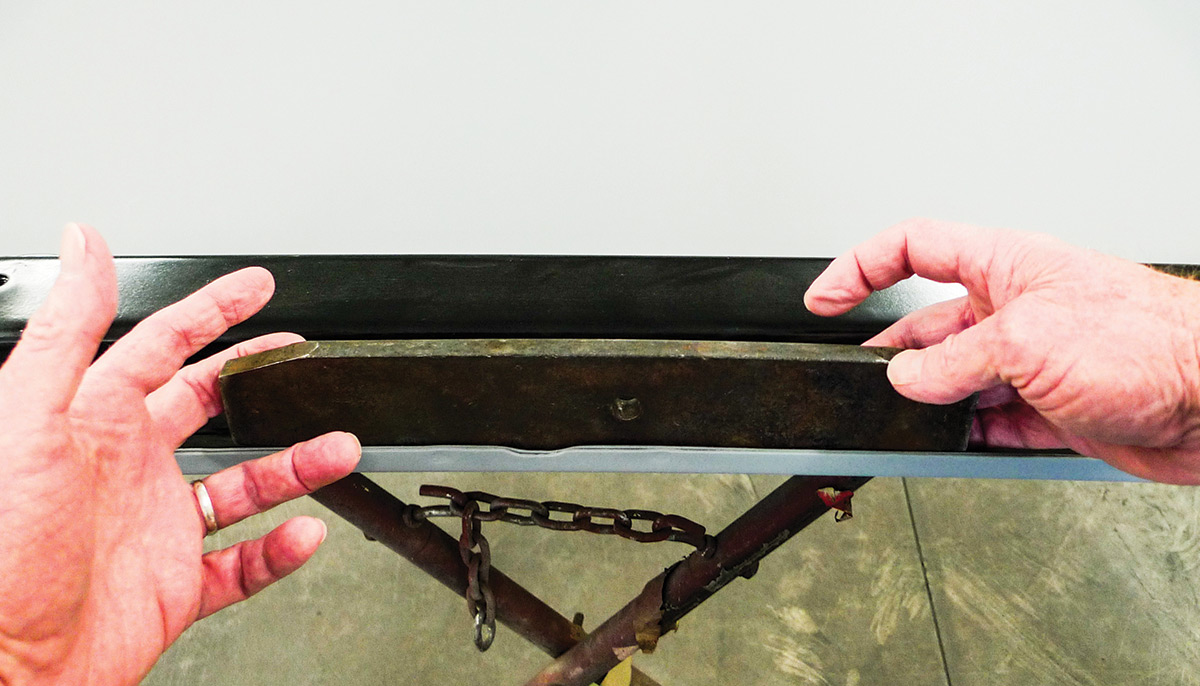
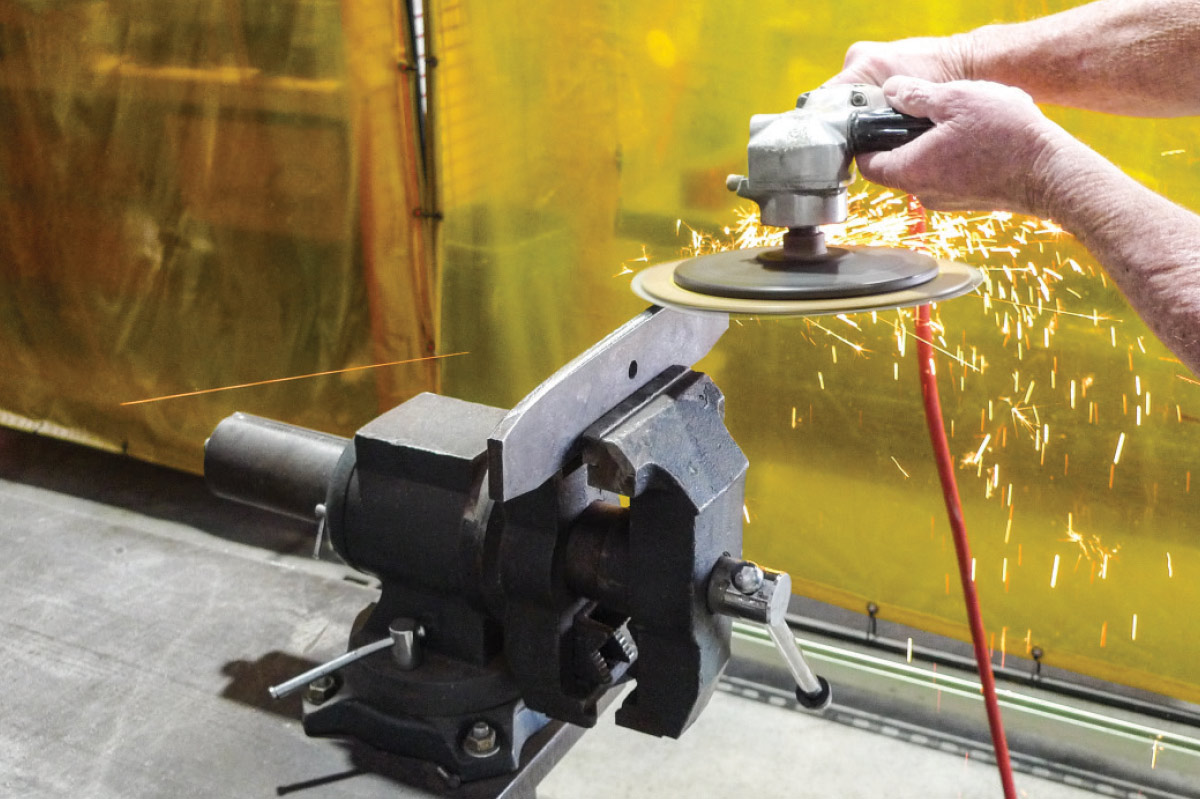
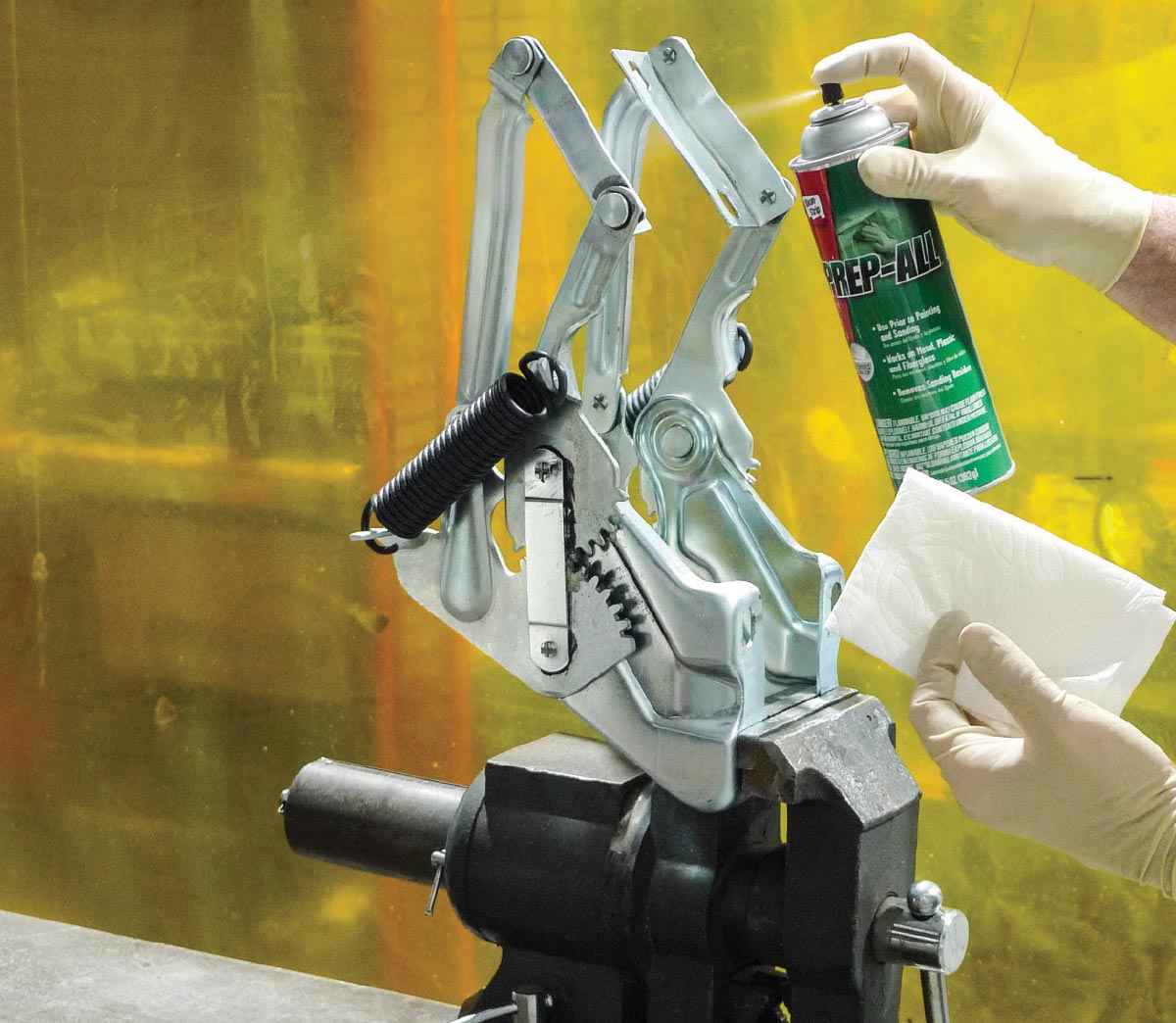
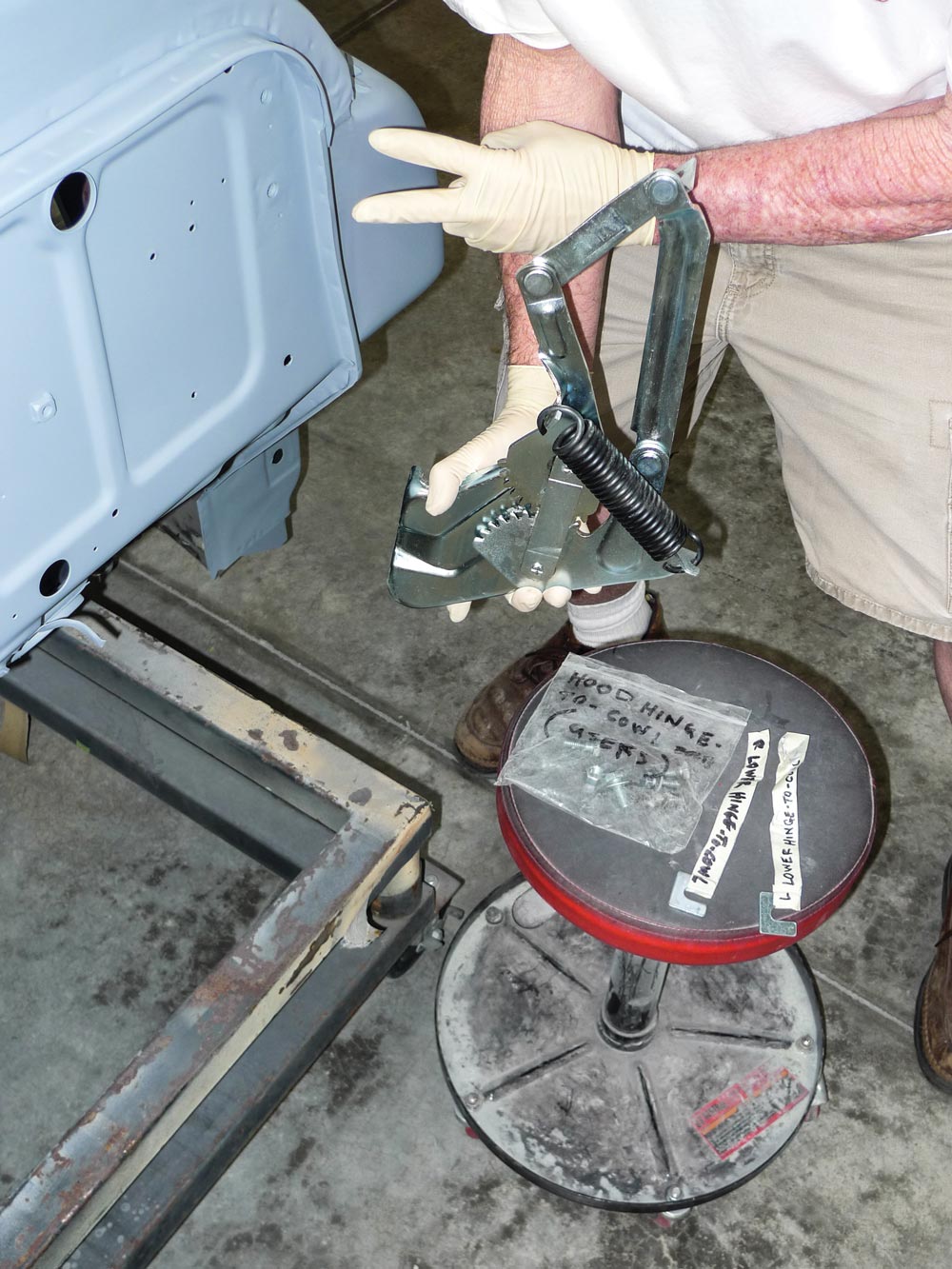
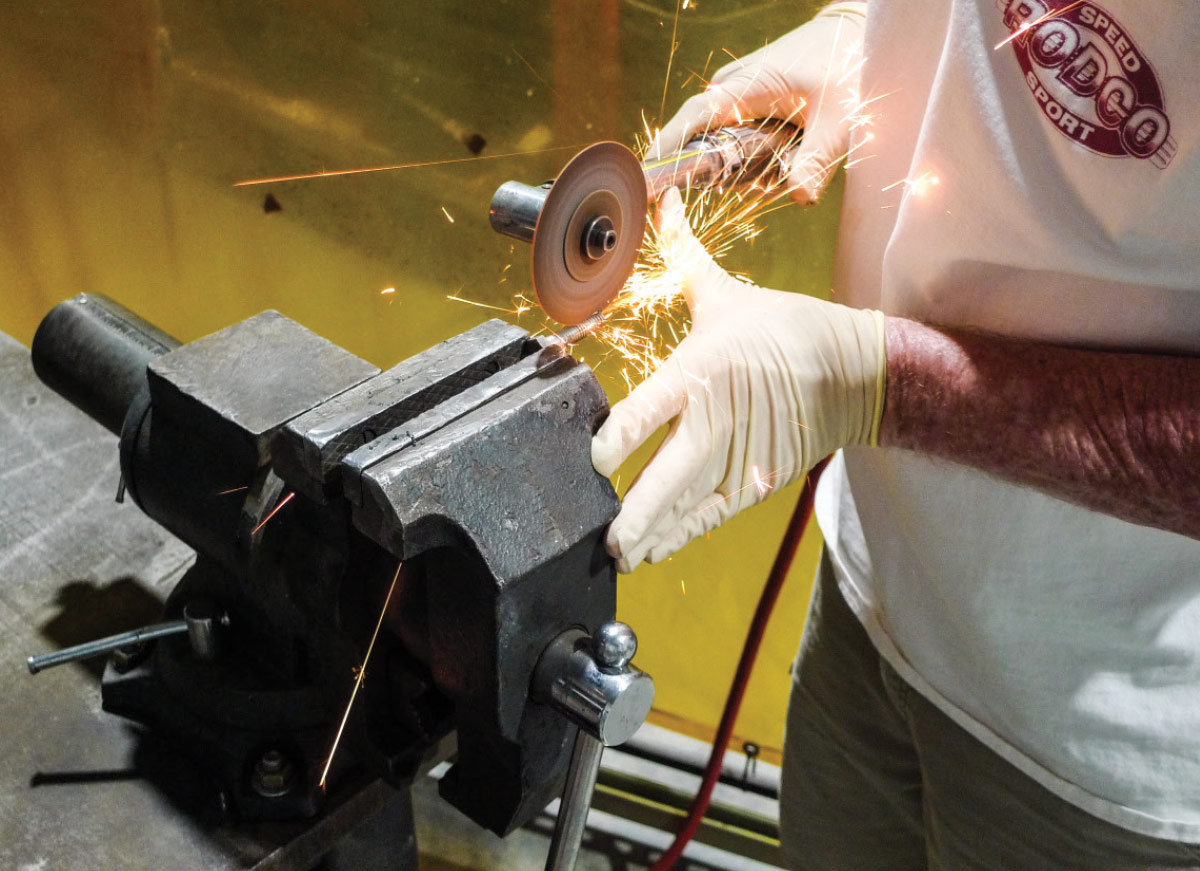
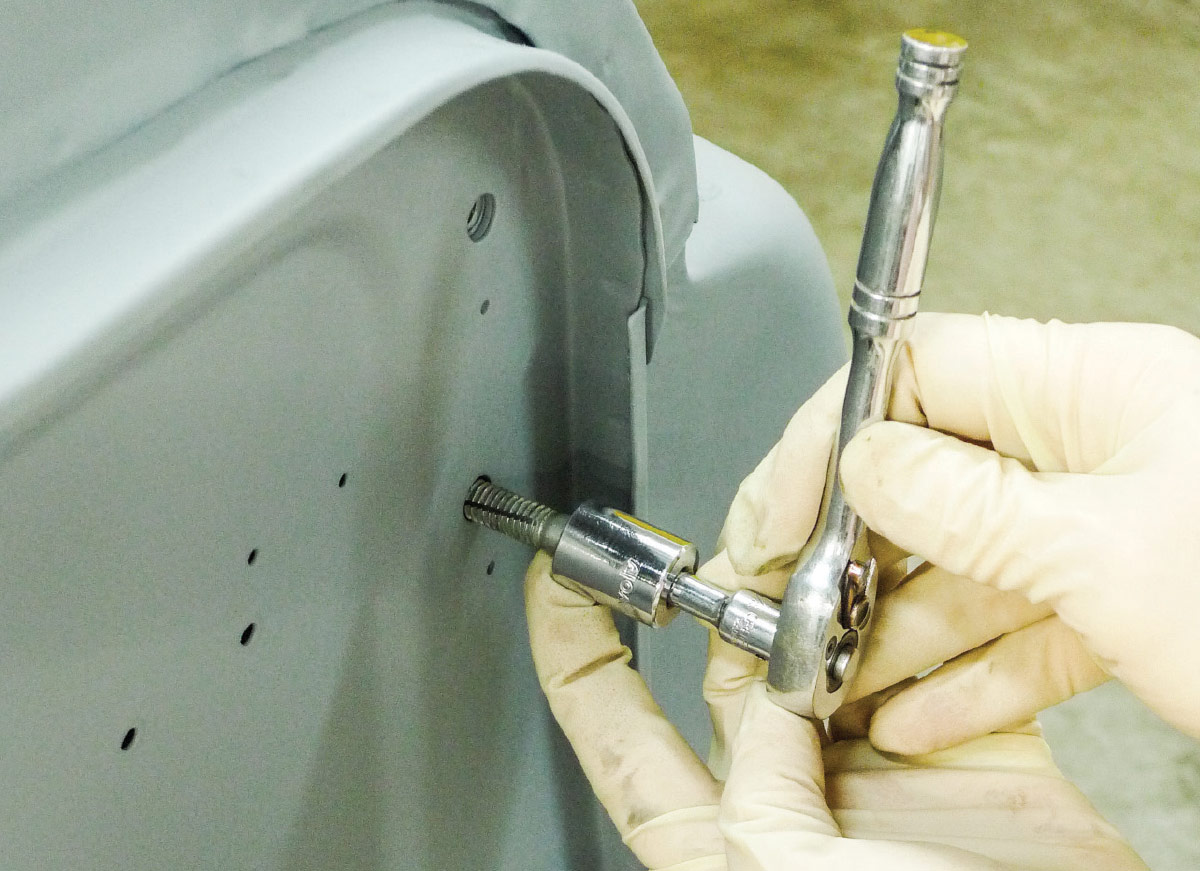
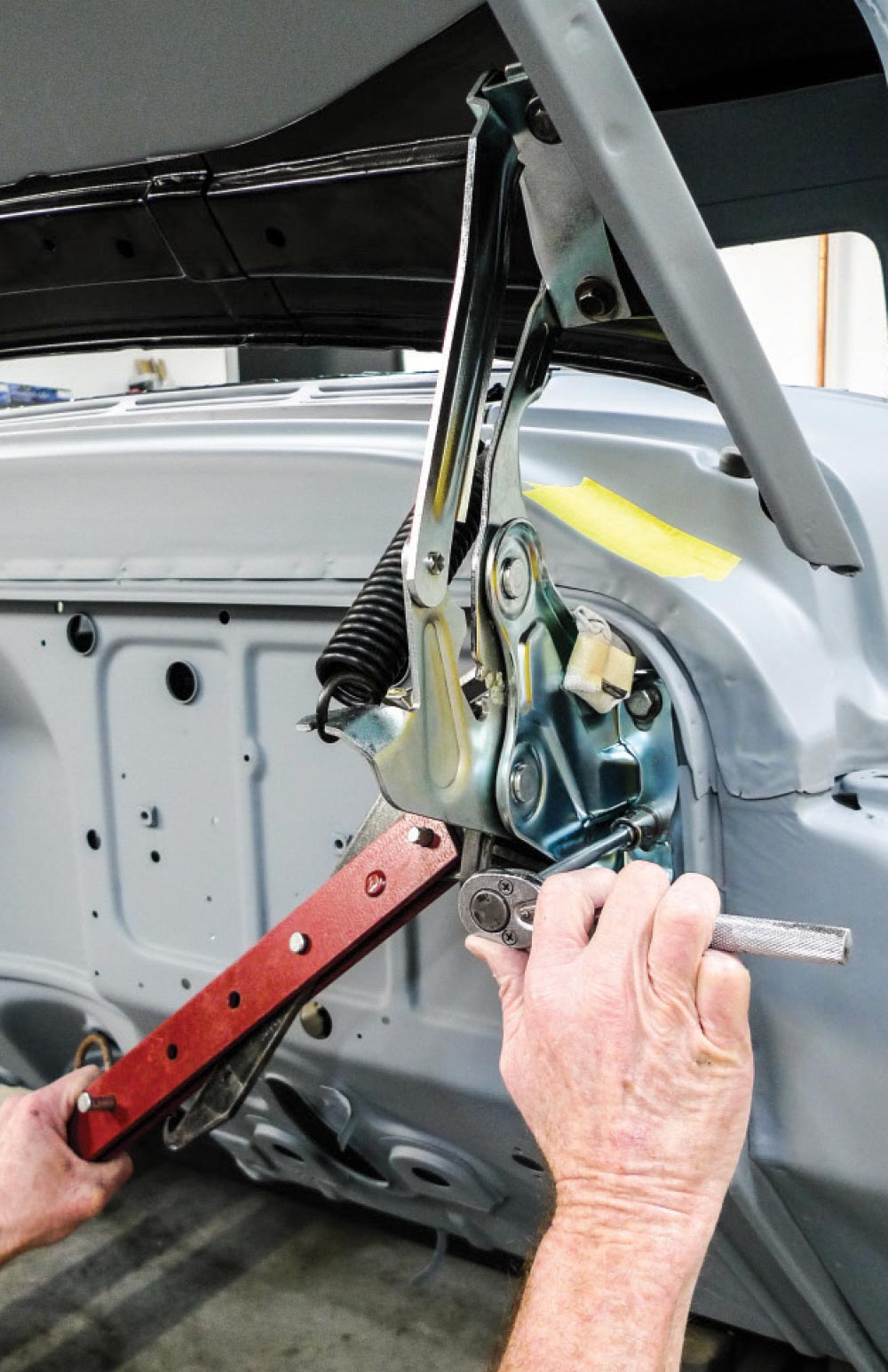
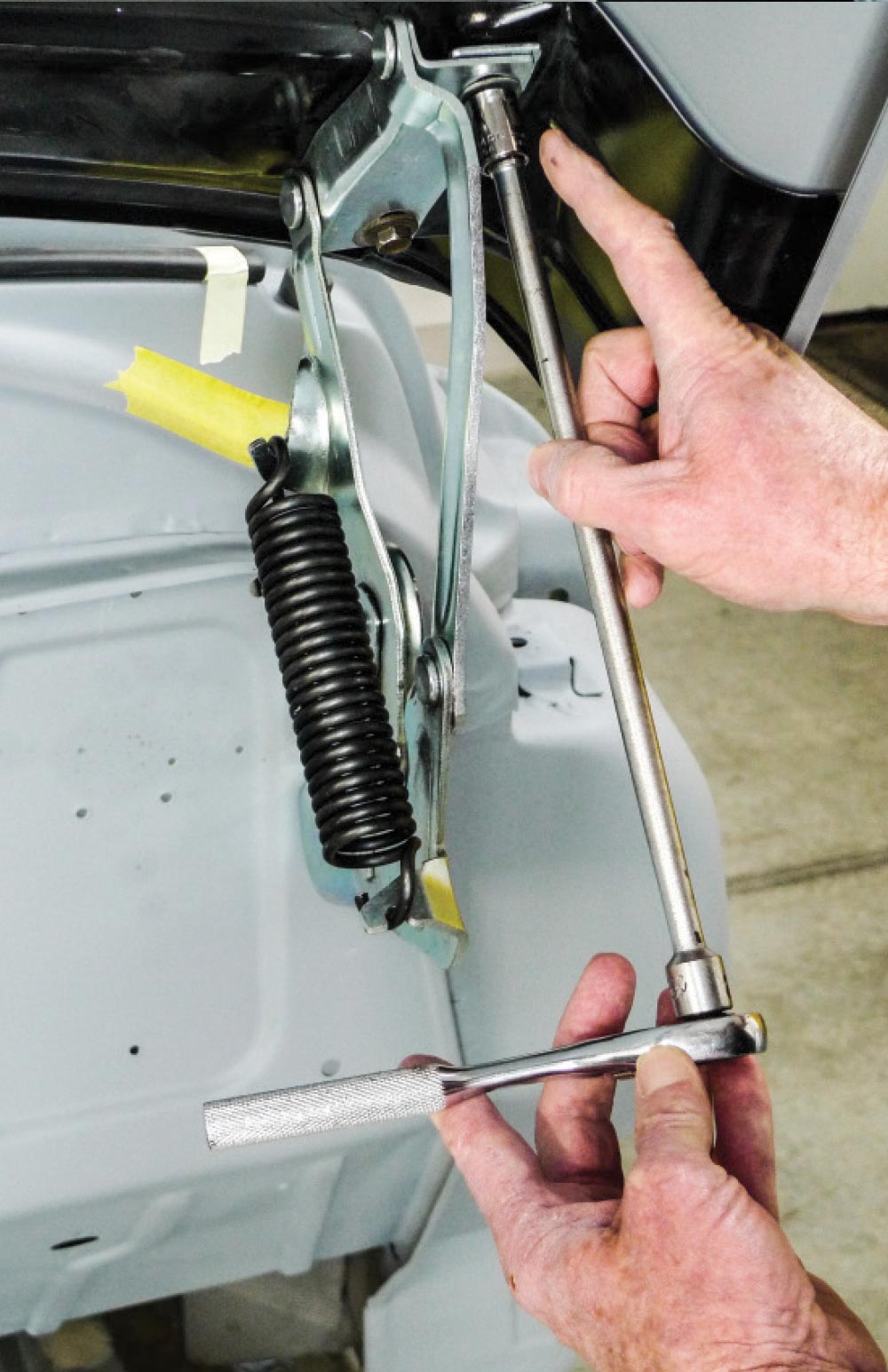
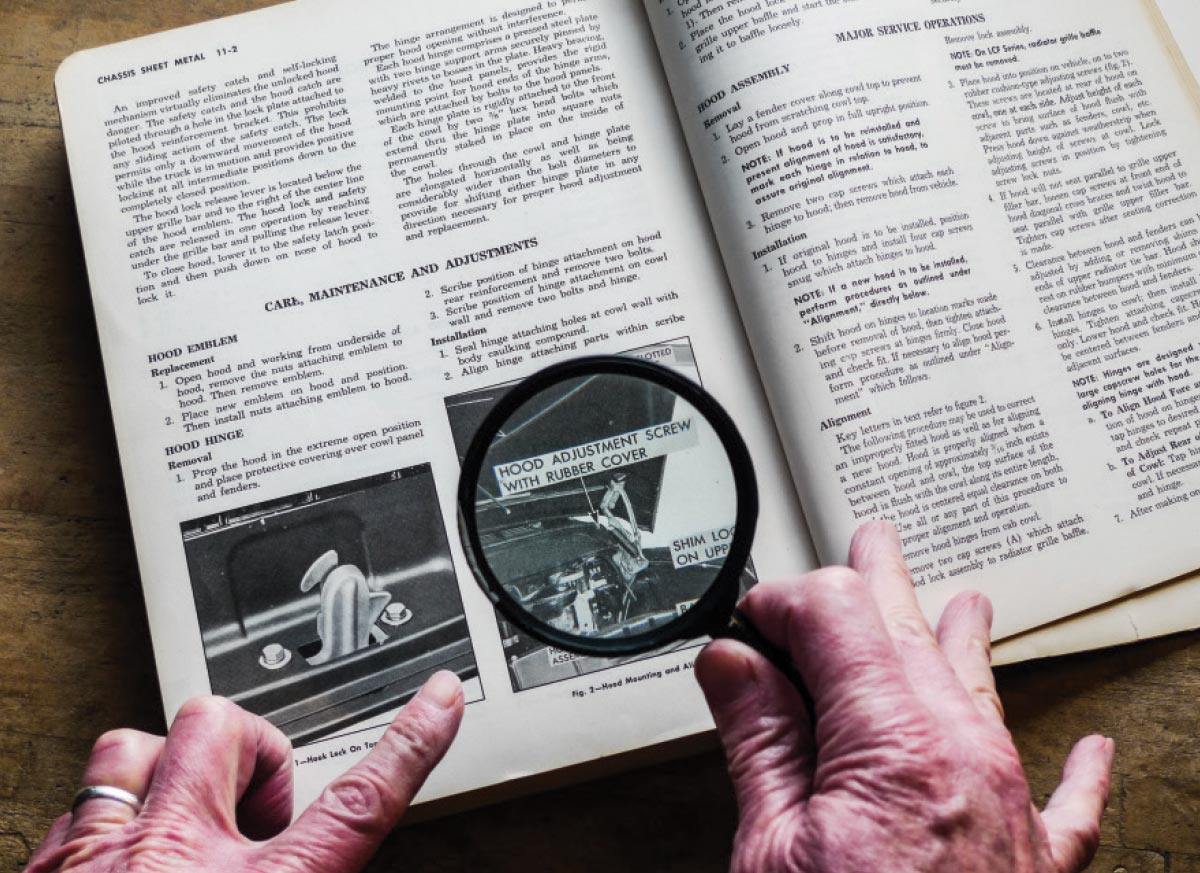
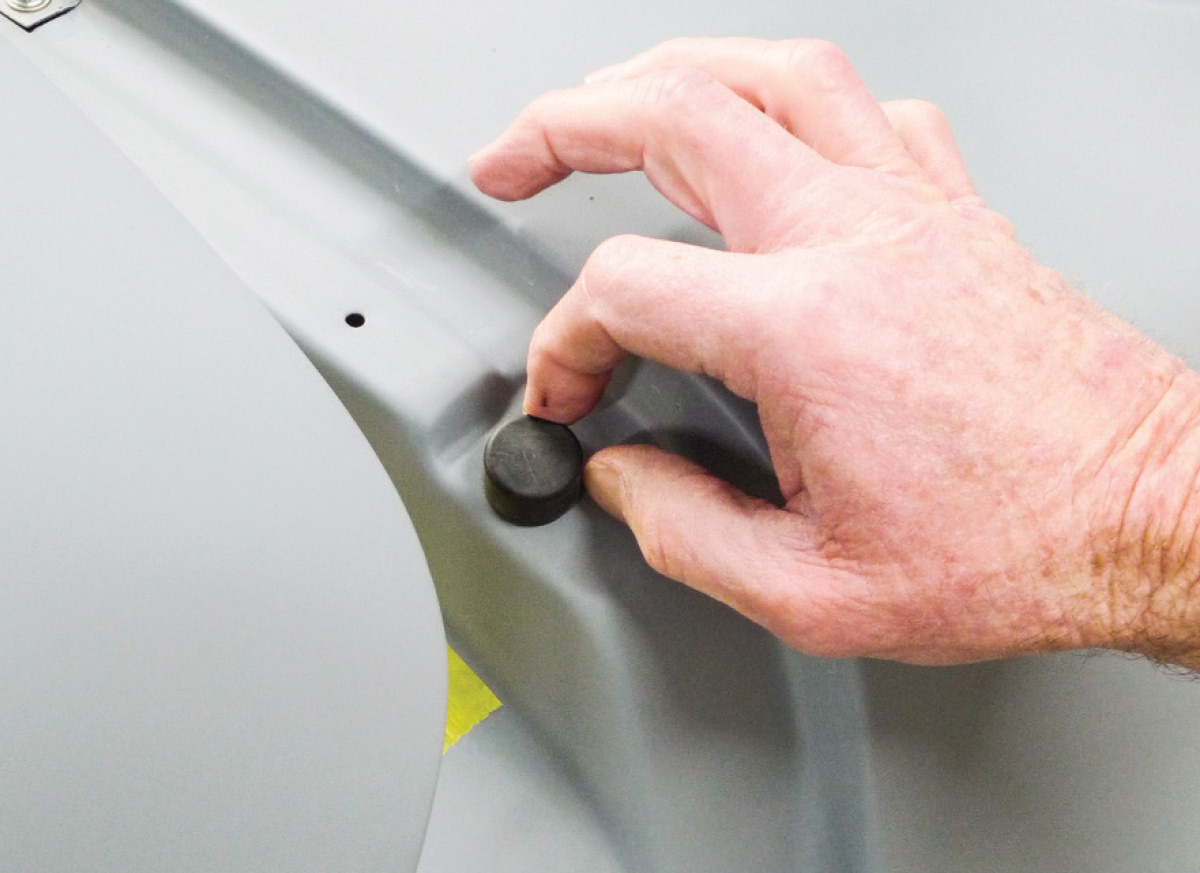
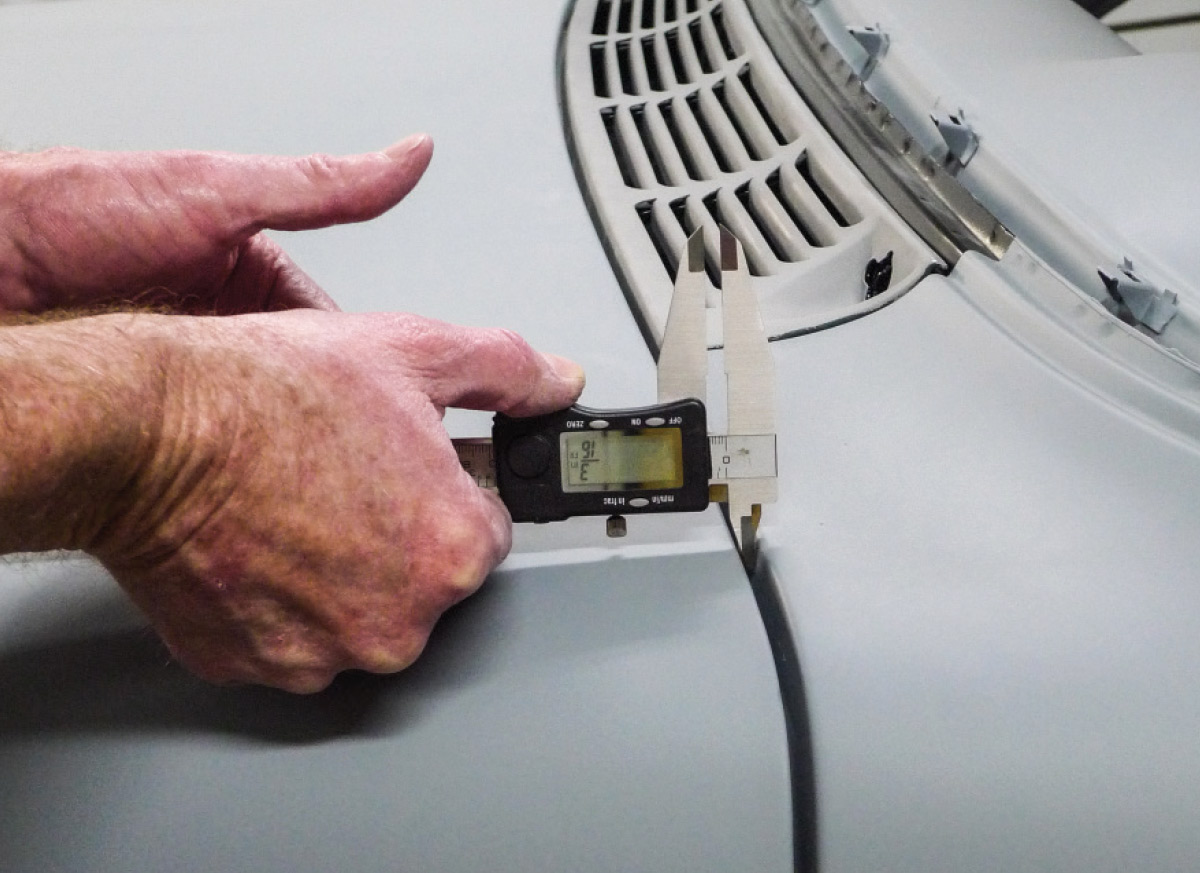
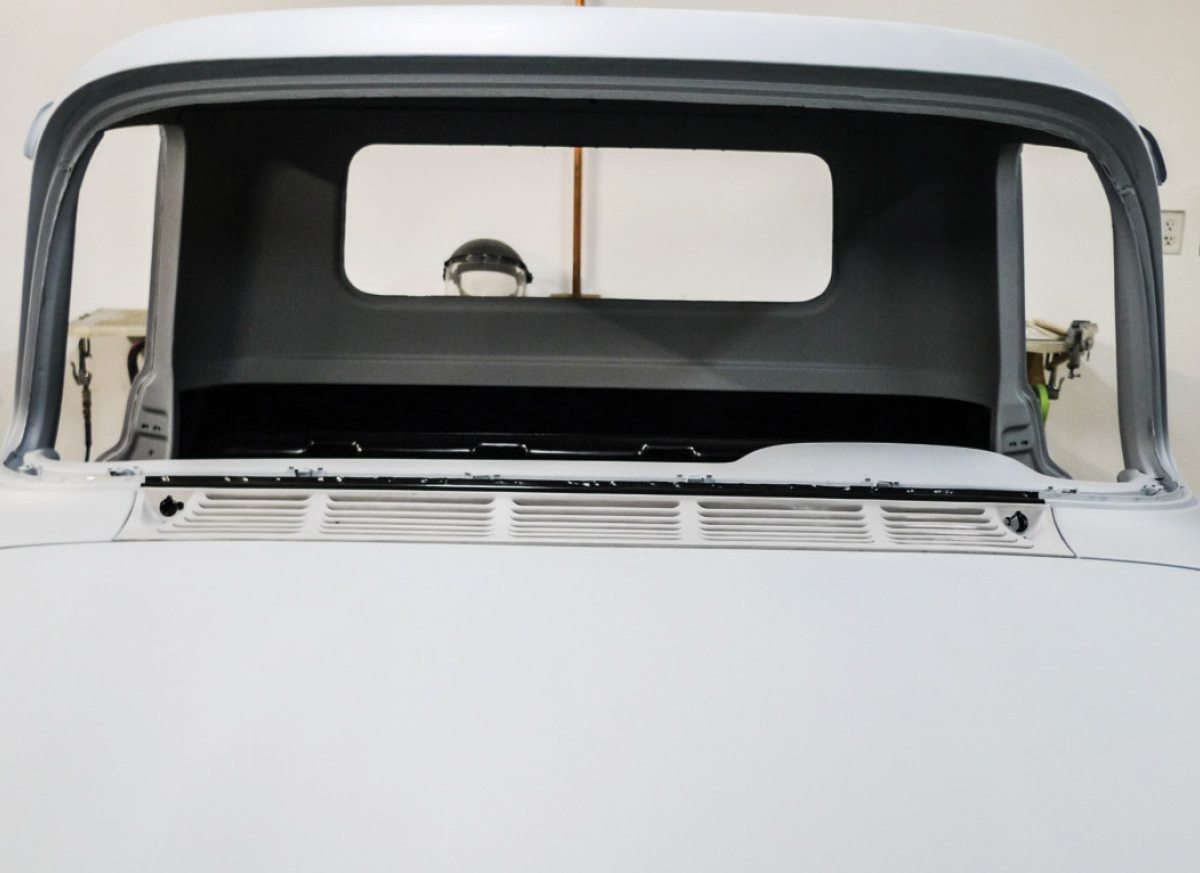
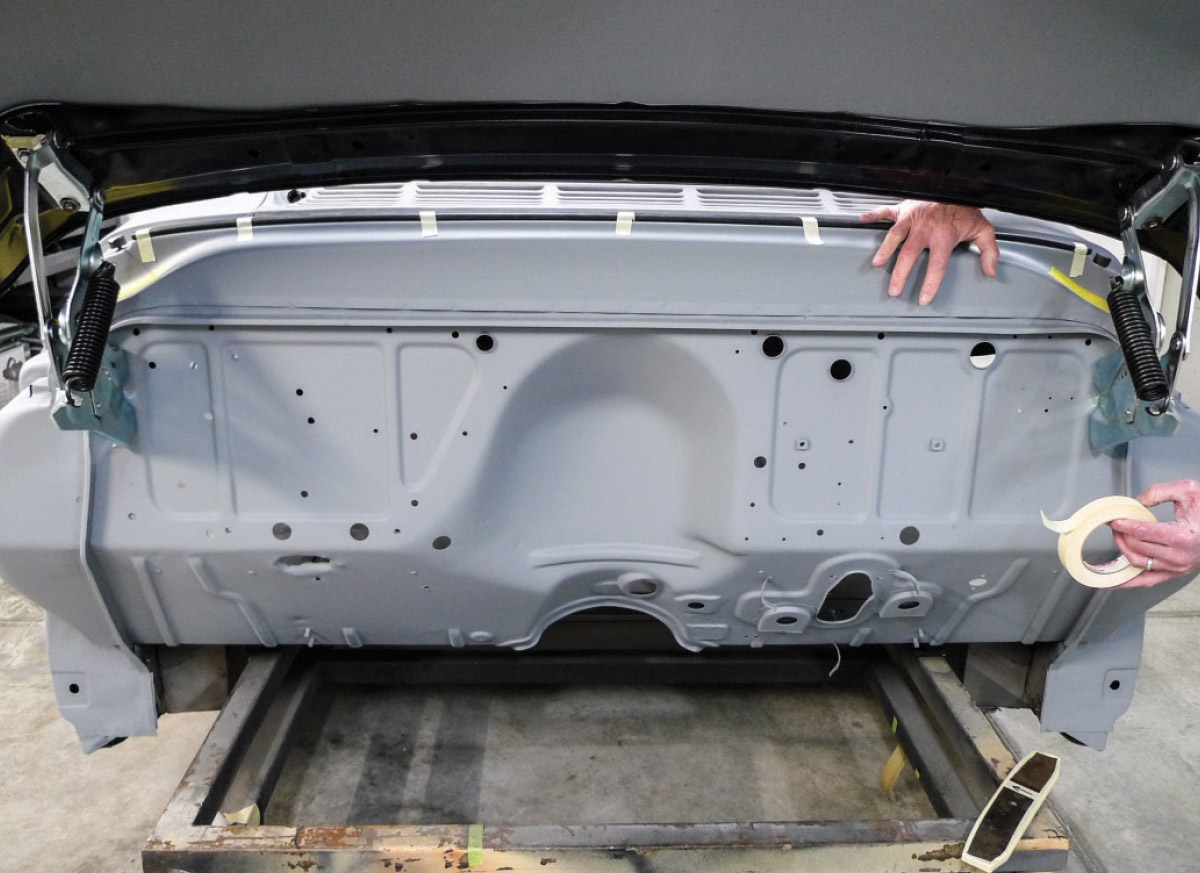
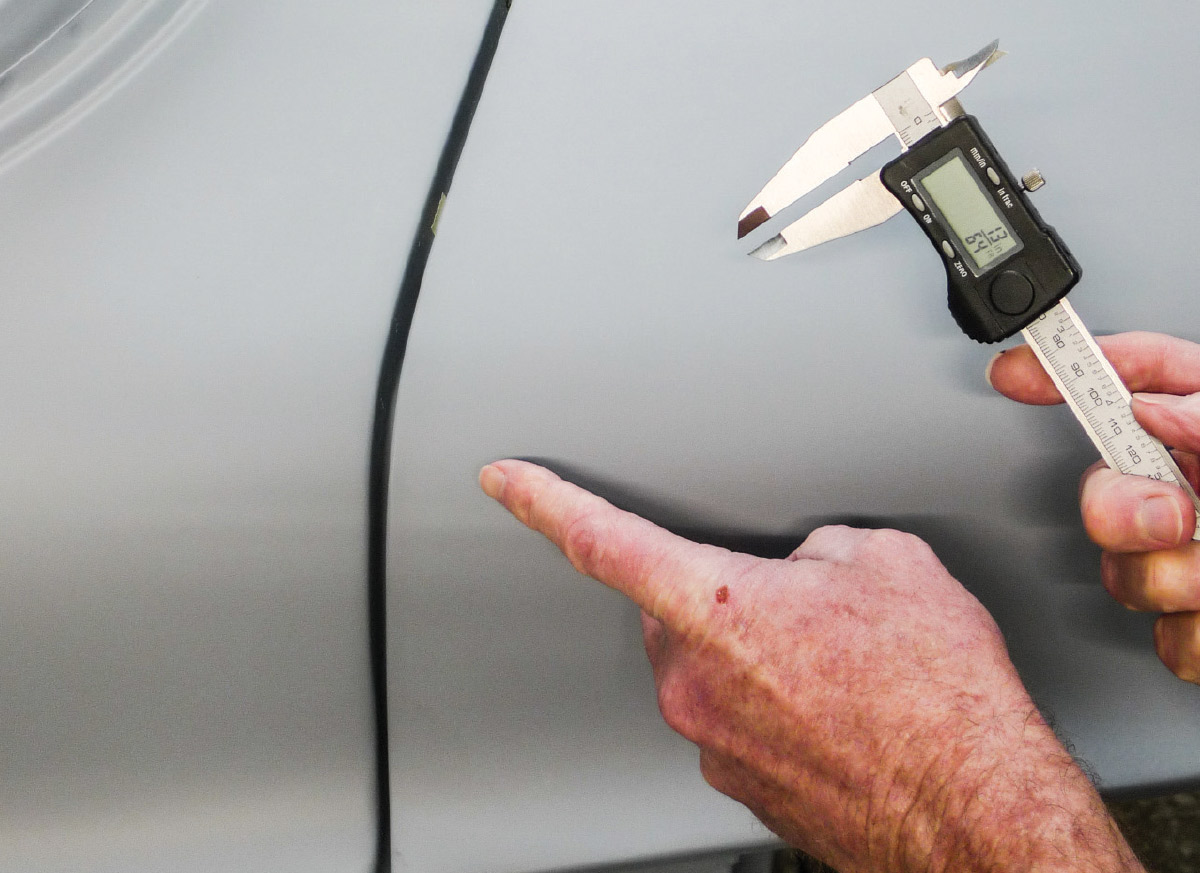
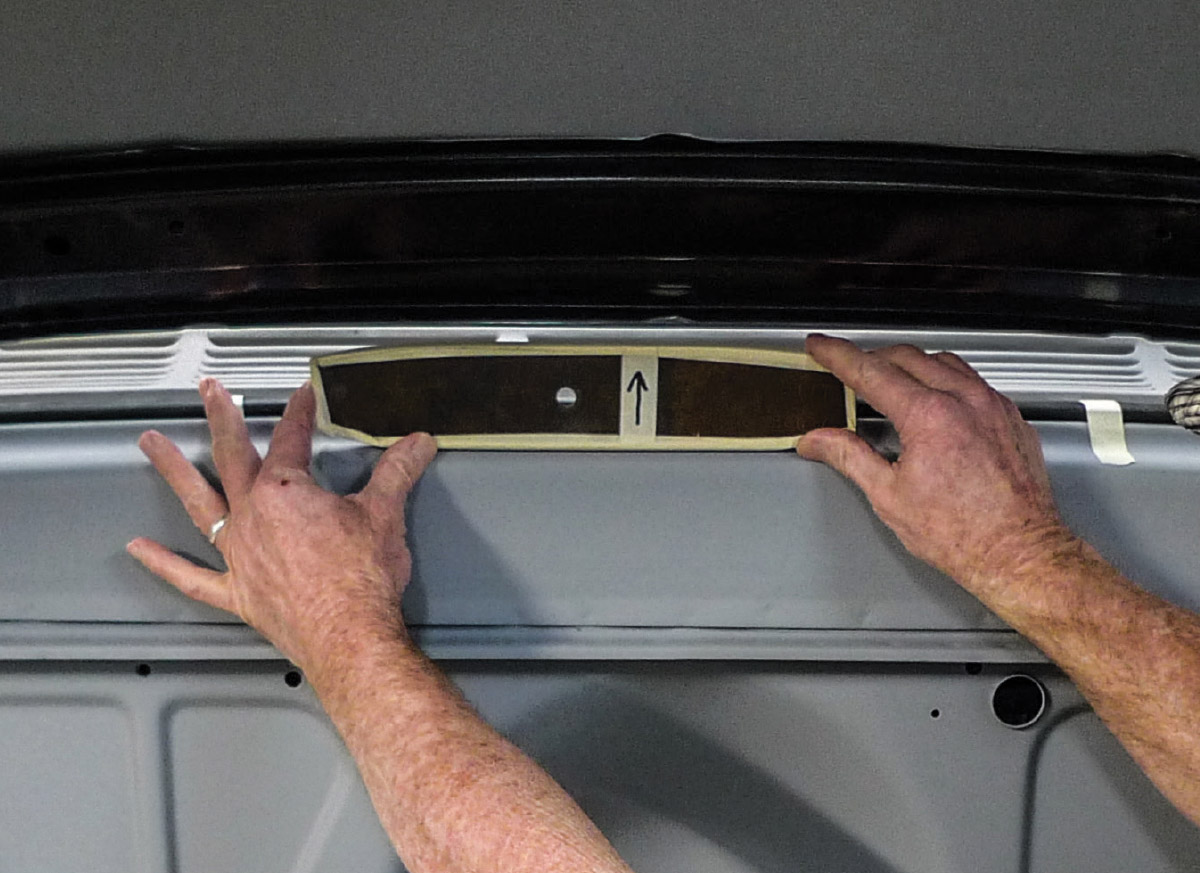
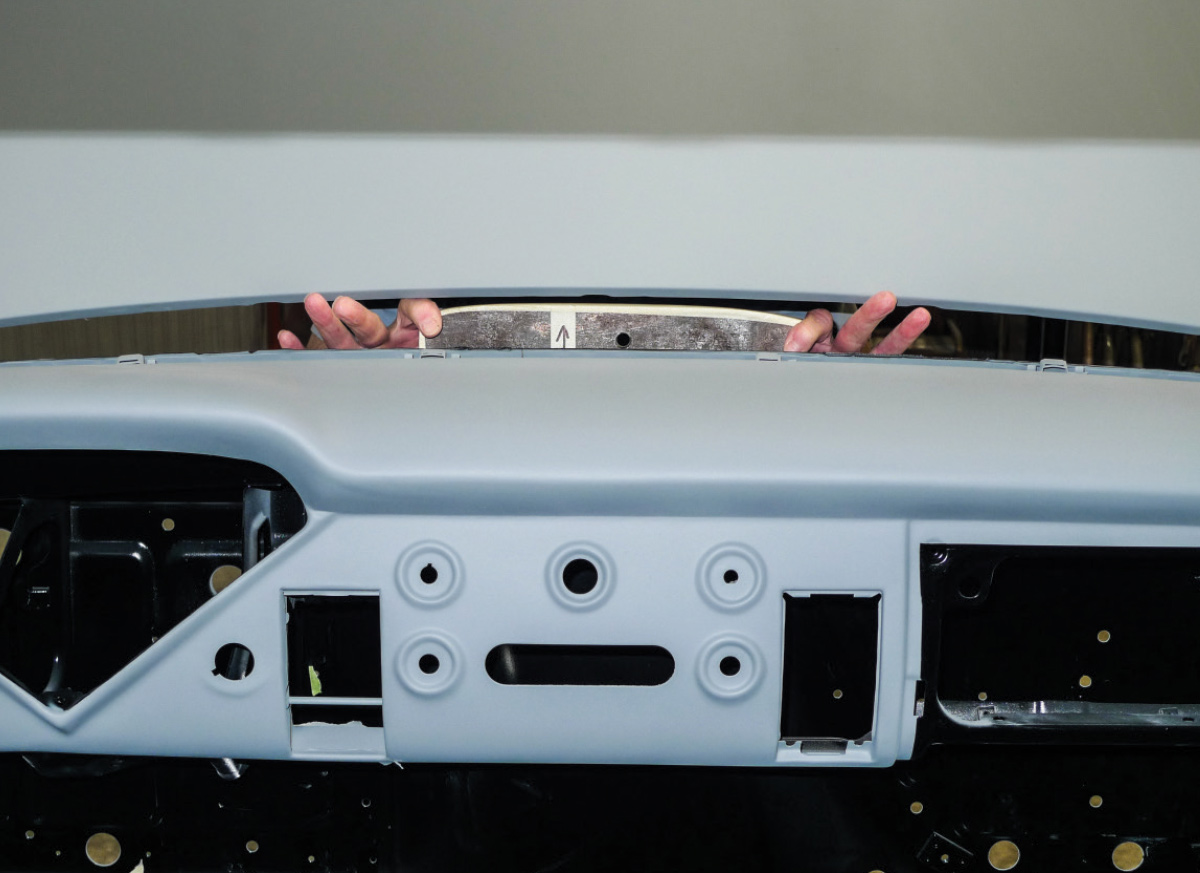
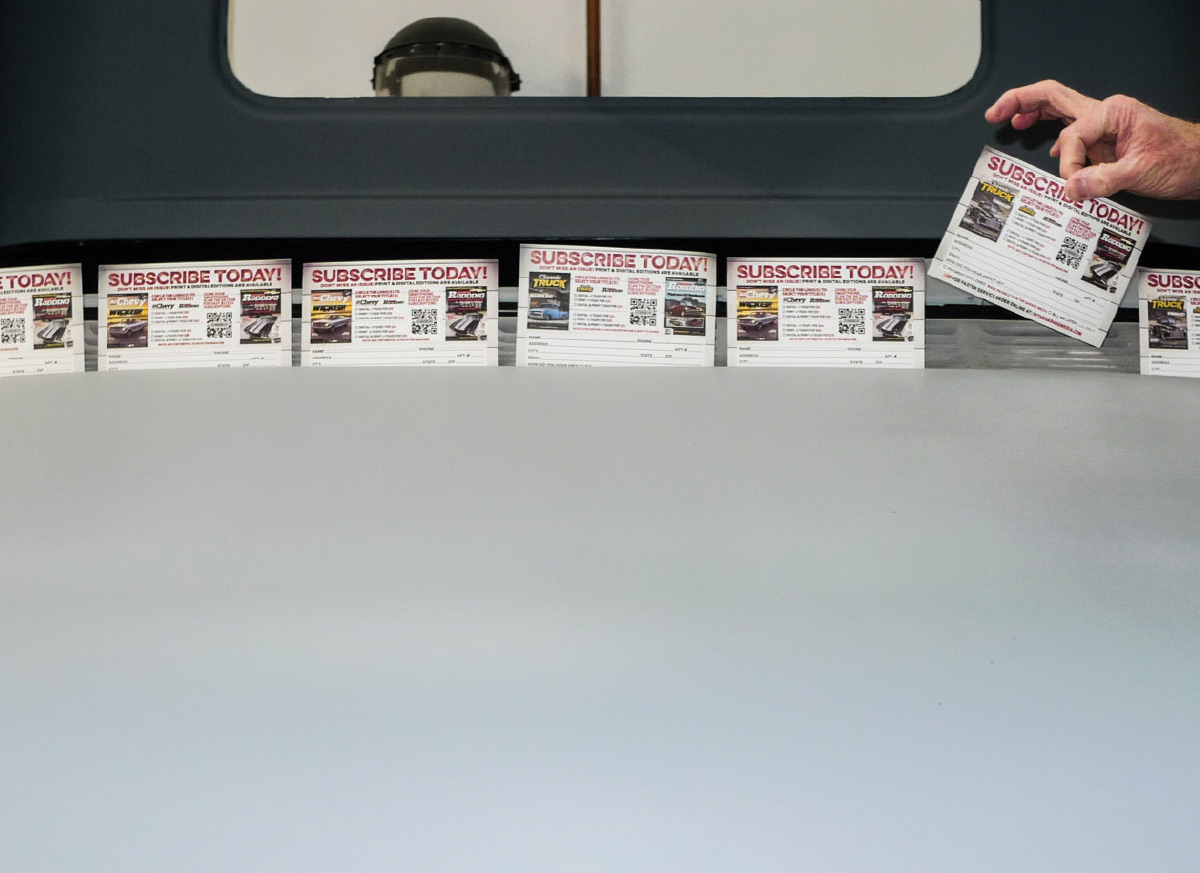
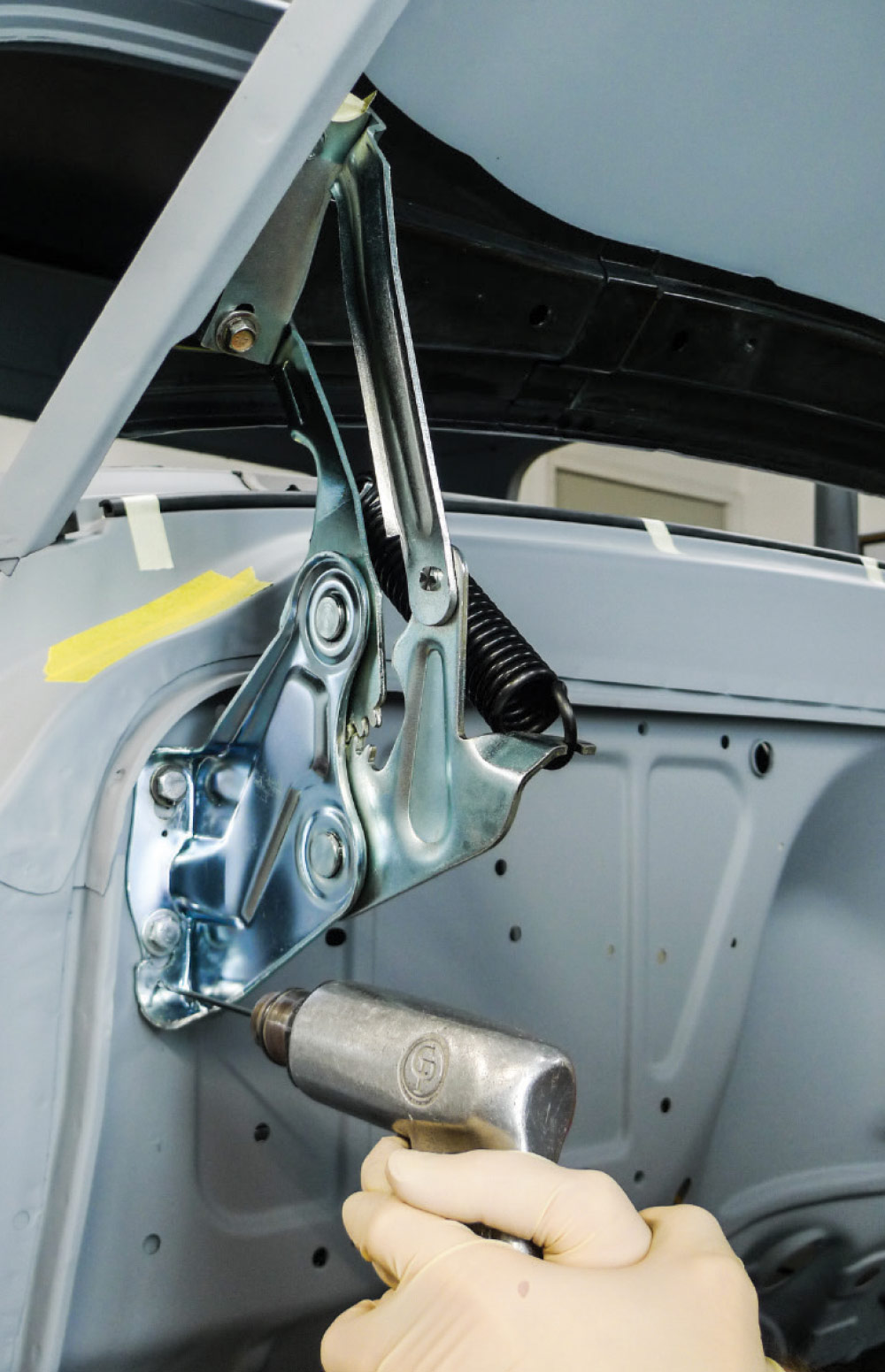
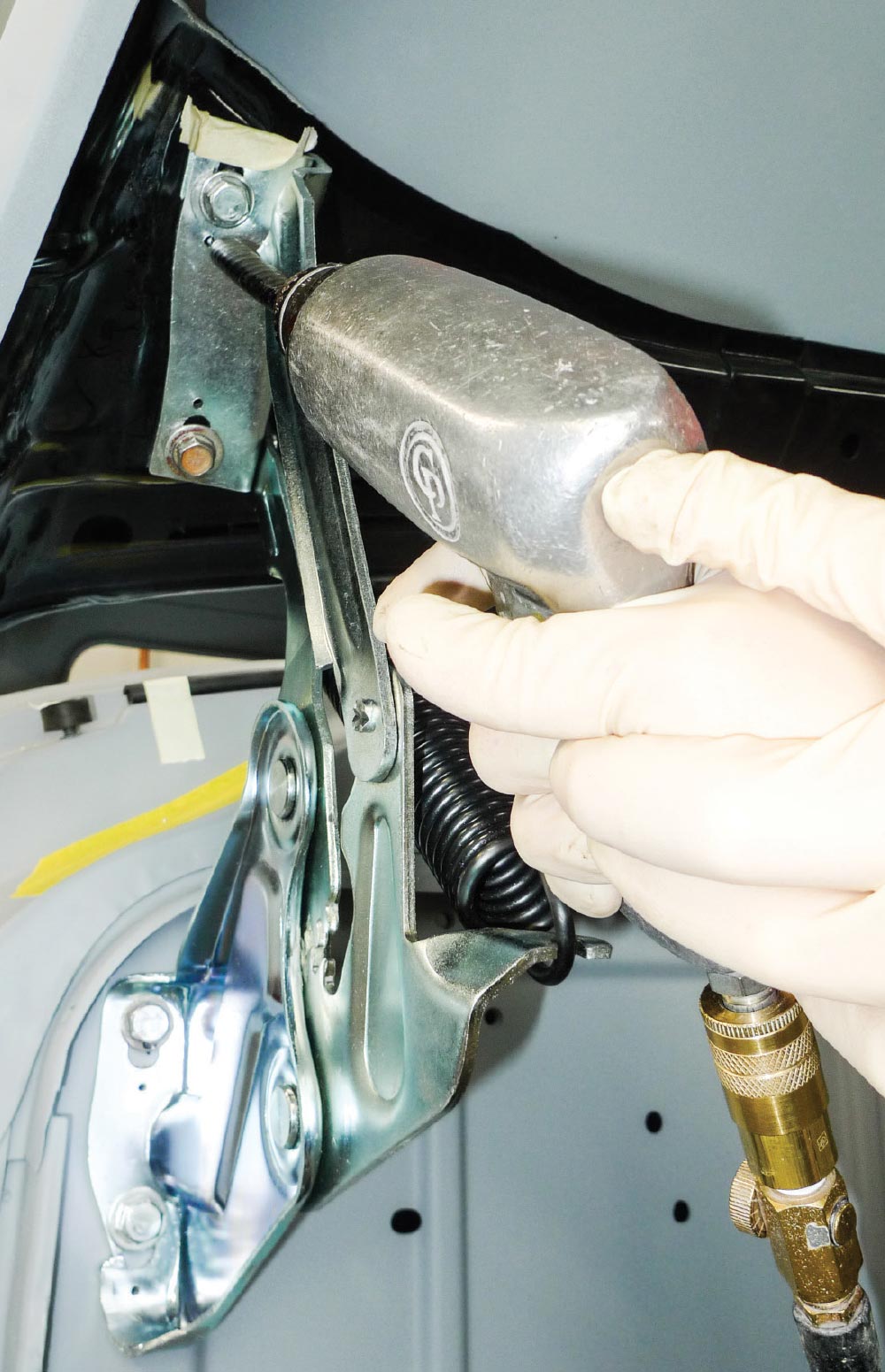
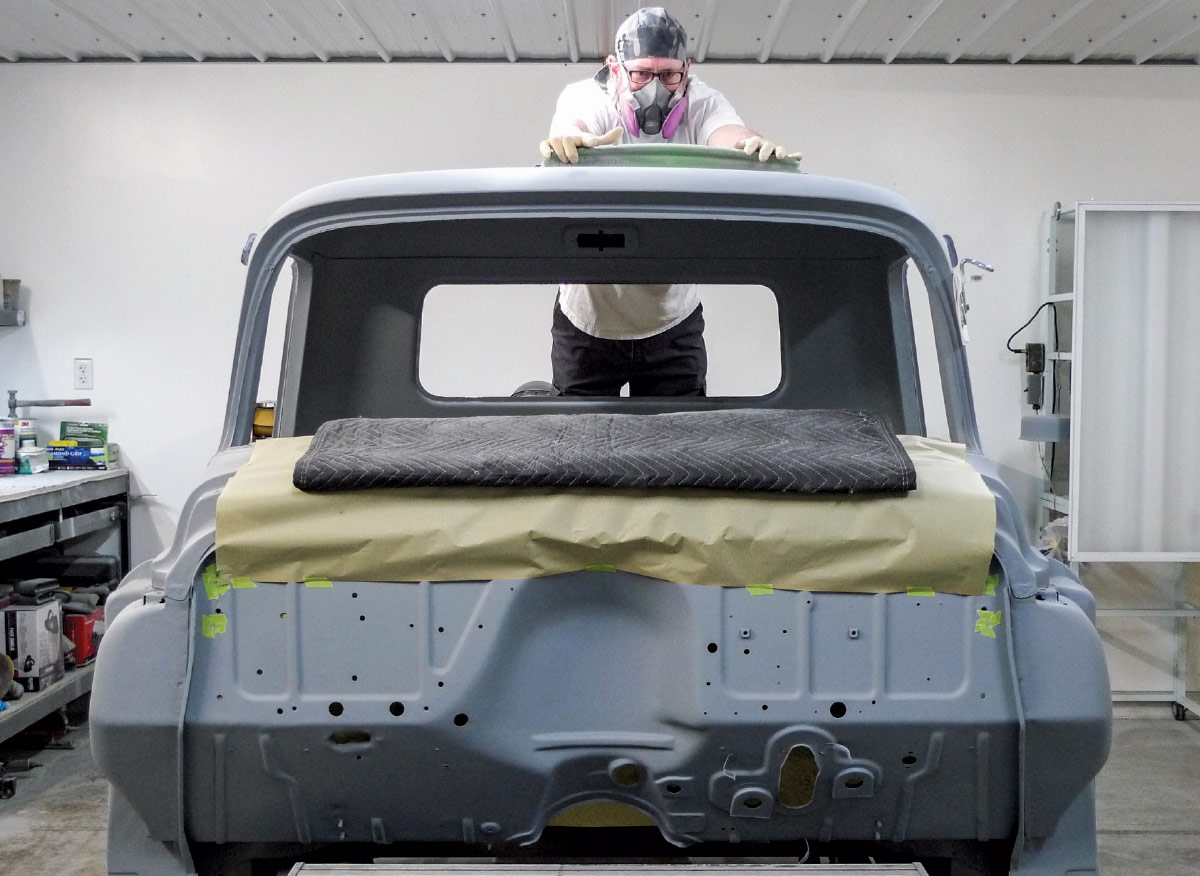
