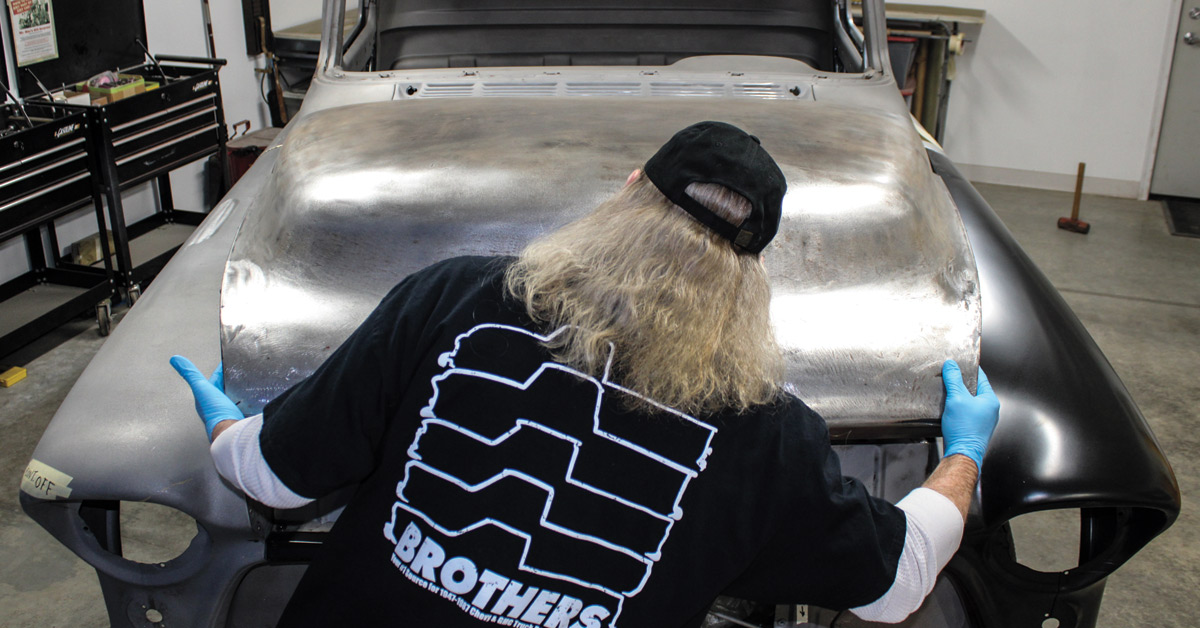
With 3/16-inch average gaps, the previously crash-damaged hood was fitting in with adjacent panels, except toward the front corners. The driver side was the worst. In that short stretch the hood appeared to sit a bit too high, as it also protruded a bit too far forward—at least by most of our standards today.
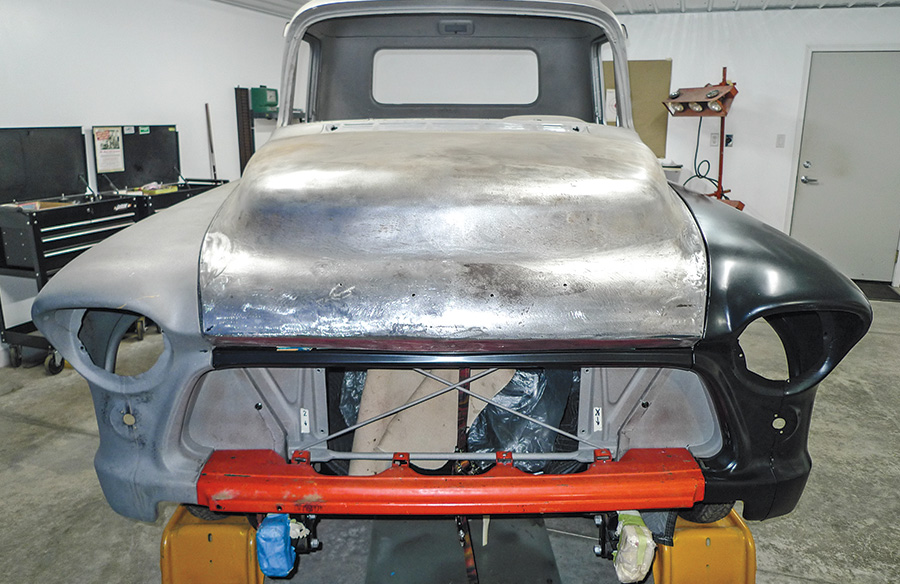
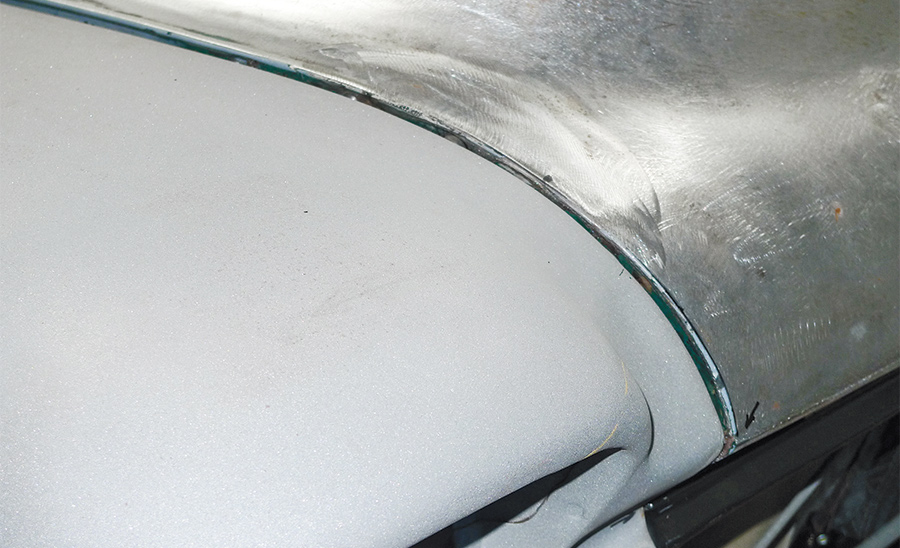
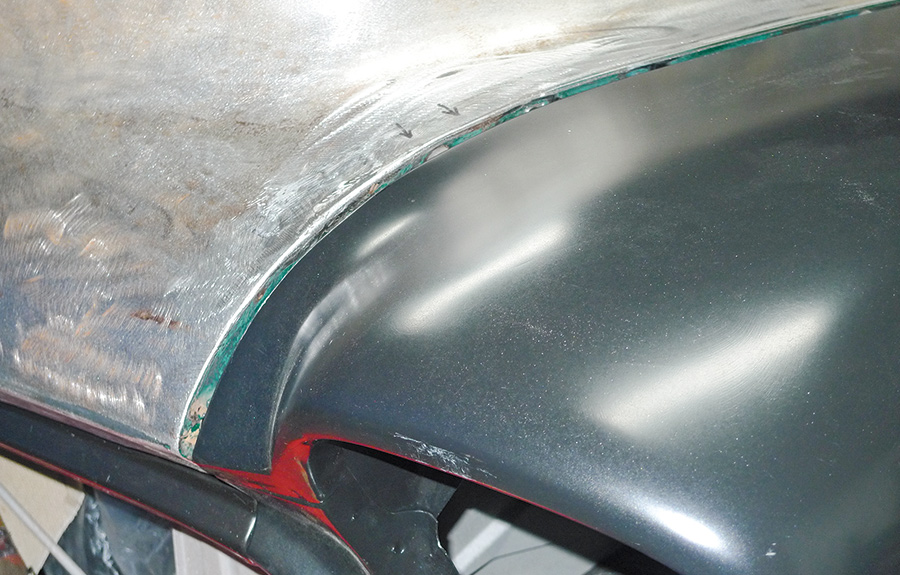
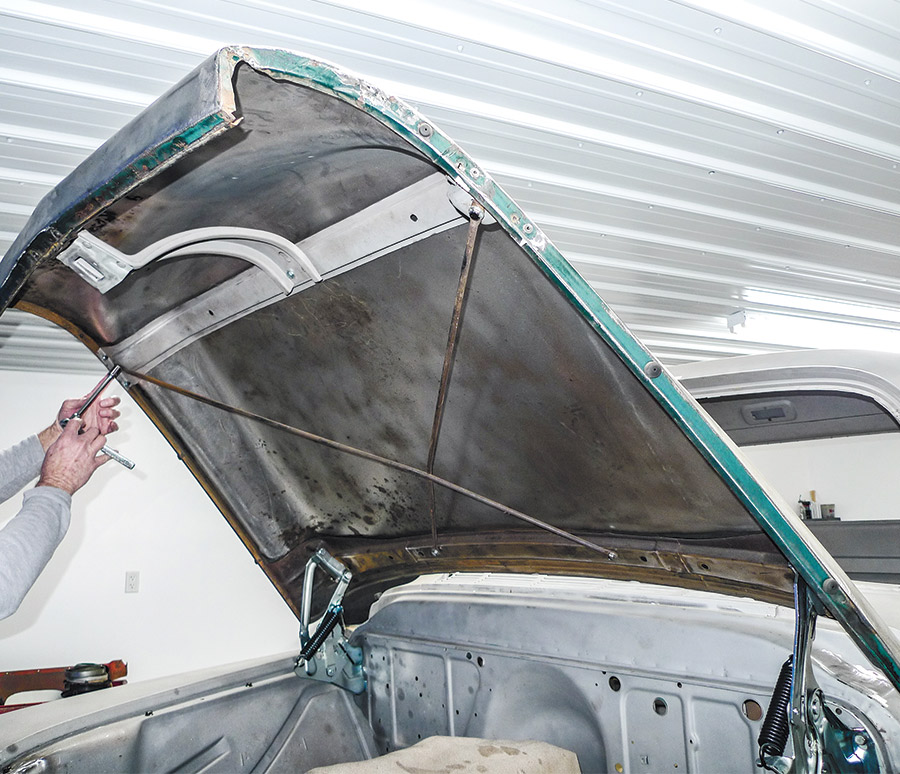
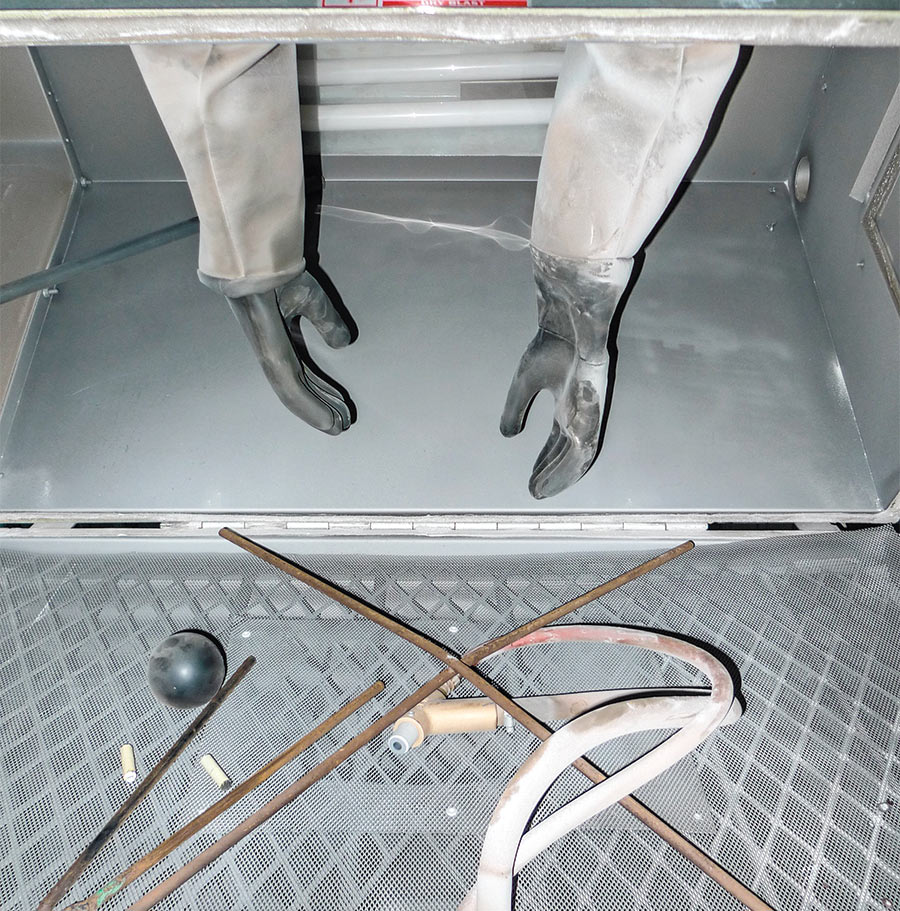
When it reassumed its position atop the new hinges that we’d previously purchased from Brothers, we were satisfied that the hood was square. Right about that time, our friend Dave Symcox of Restorations Limited stopped by. “I’m not sure square is what you want,” he says. Symcox knows this type of truck quite well. He’s been our go-to guru, and, as it turned out, he was right—again. The core support had already been shimmed to raise the left side as necessary. Even so, the left-front horizontal gap was wider where the hood’s lower edge met the new Brothers upper valance.

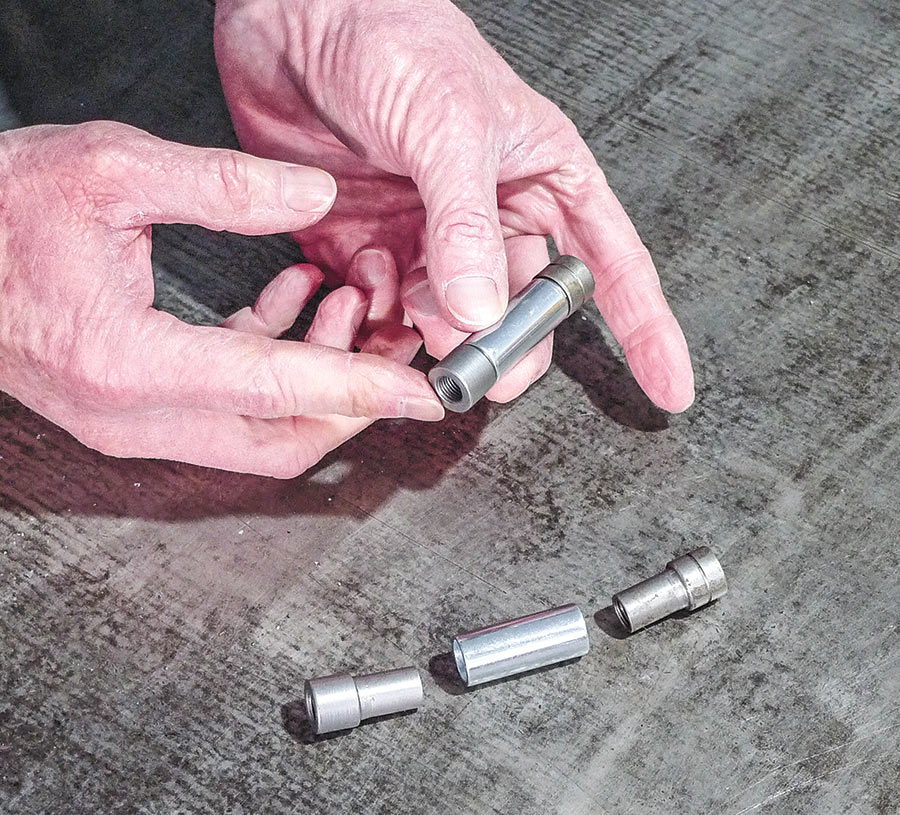
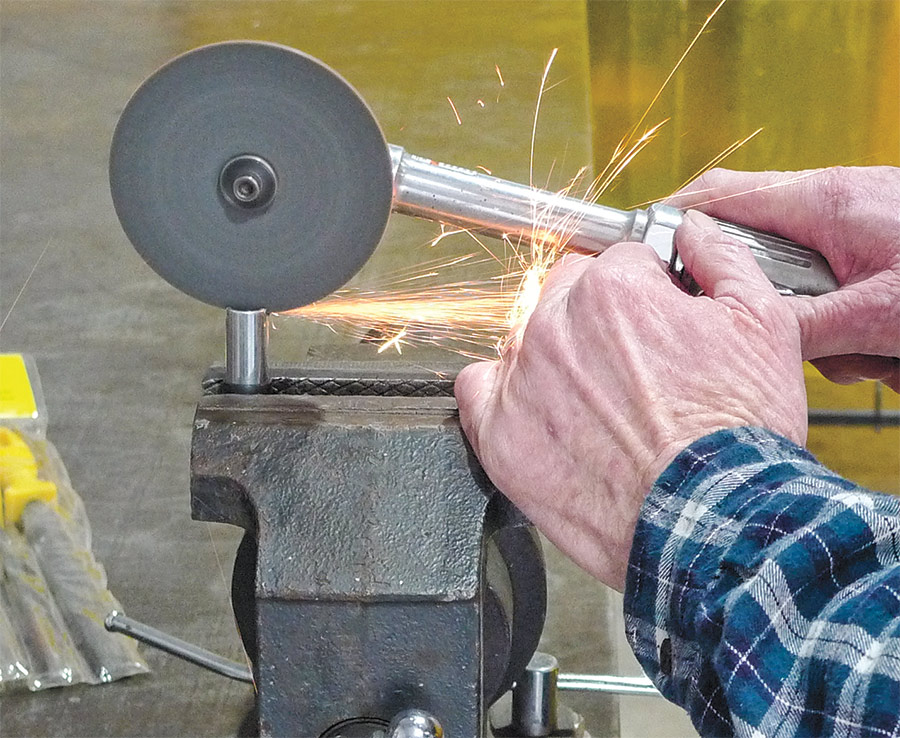
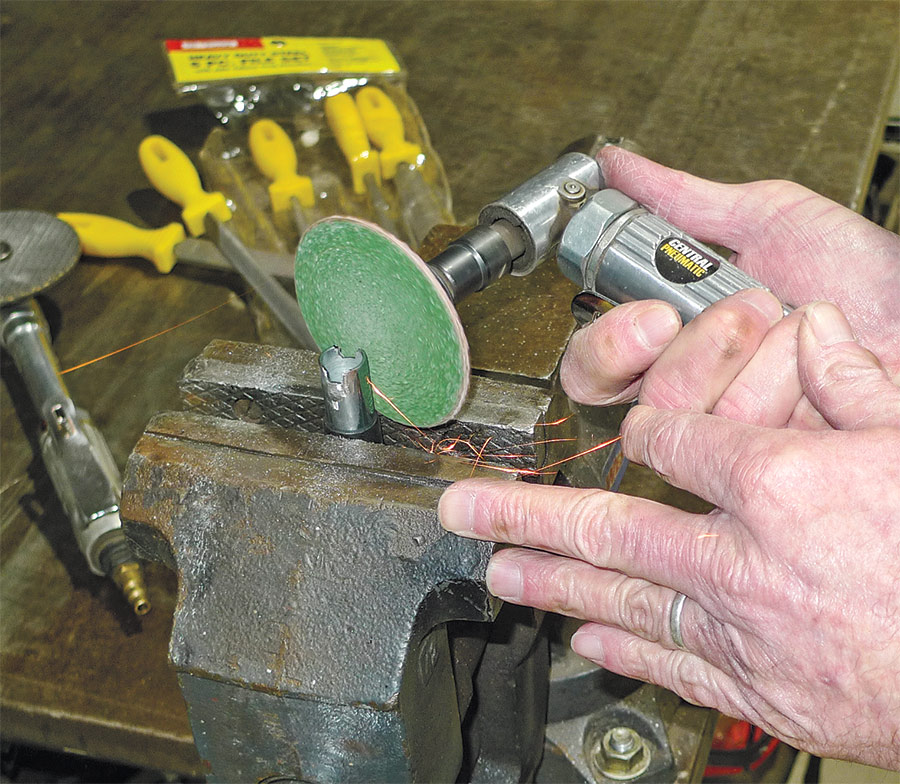
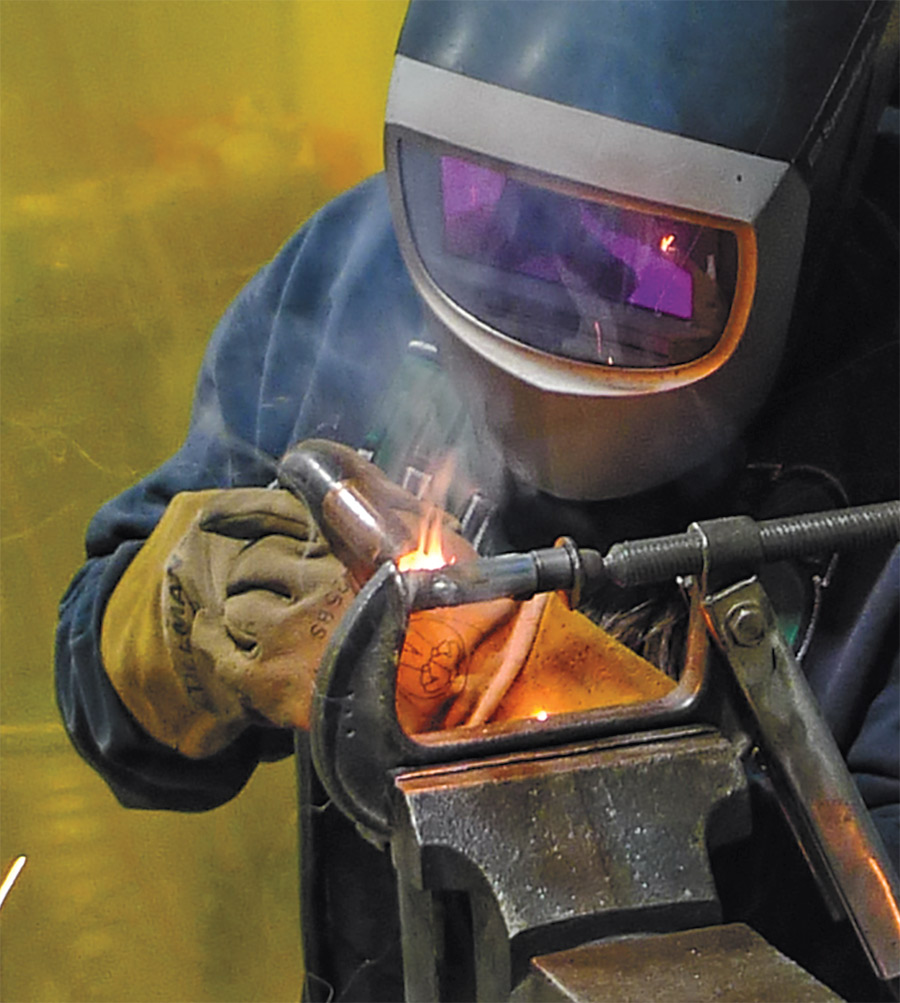
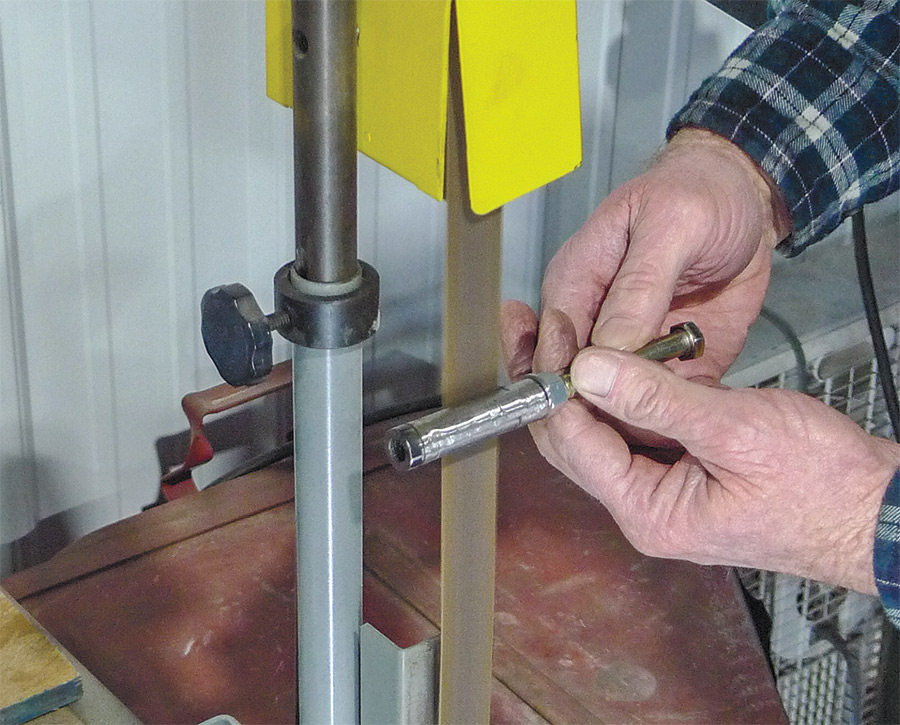
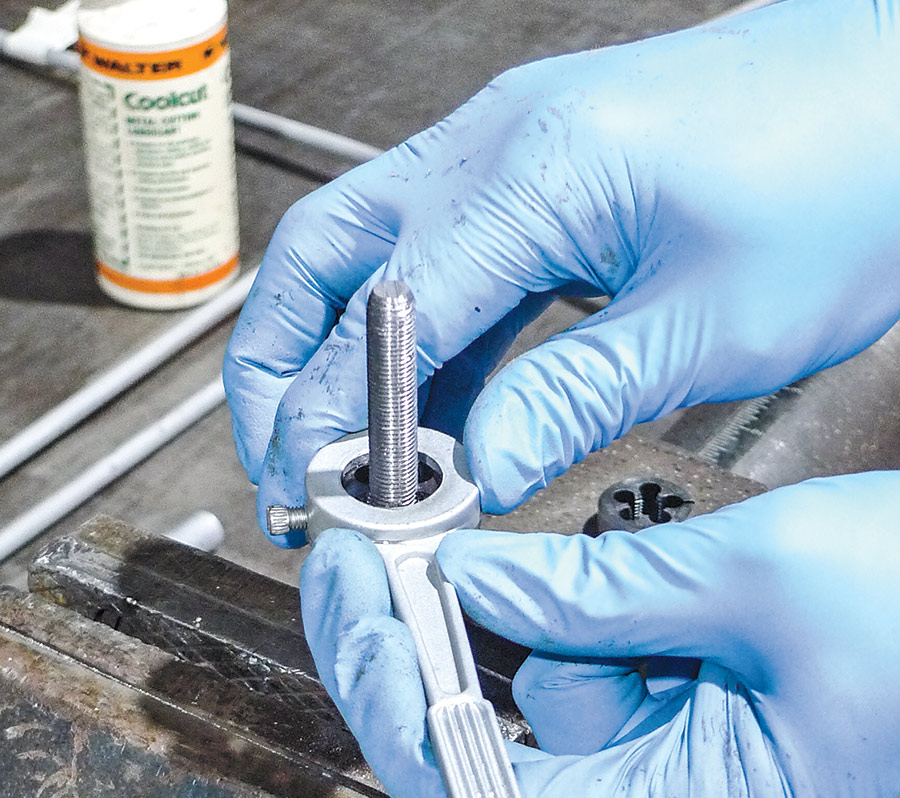
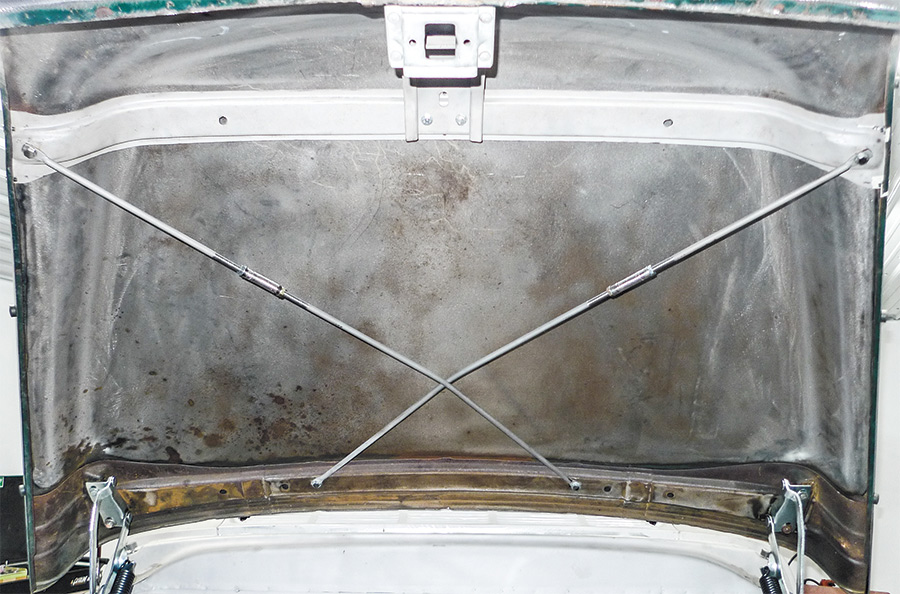
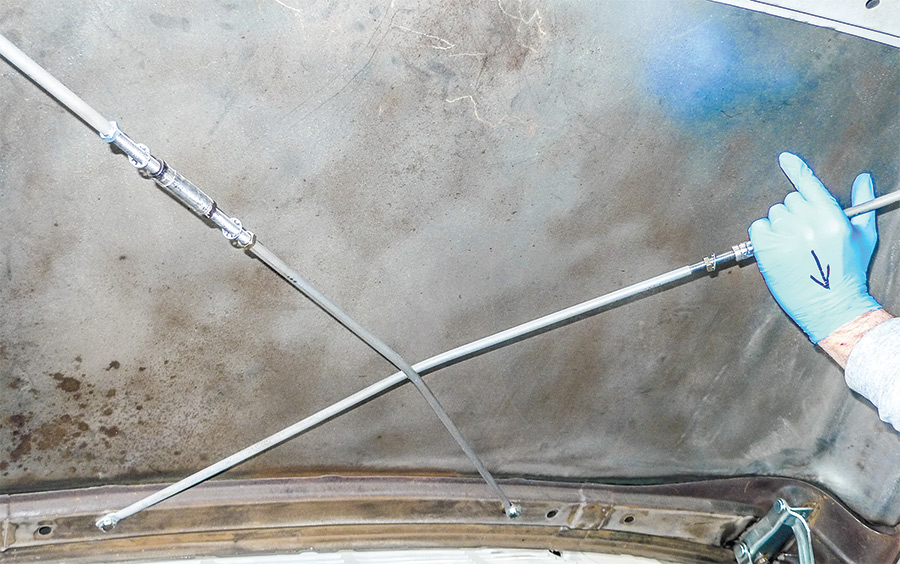
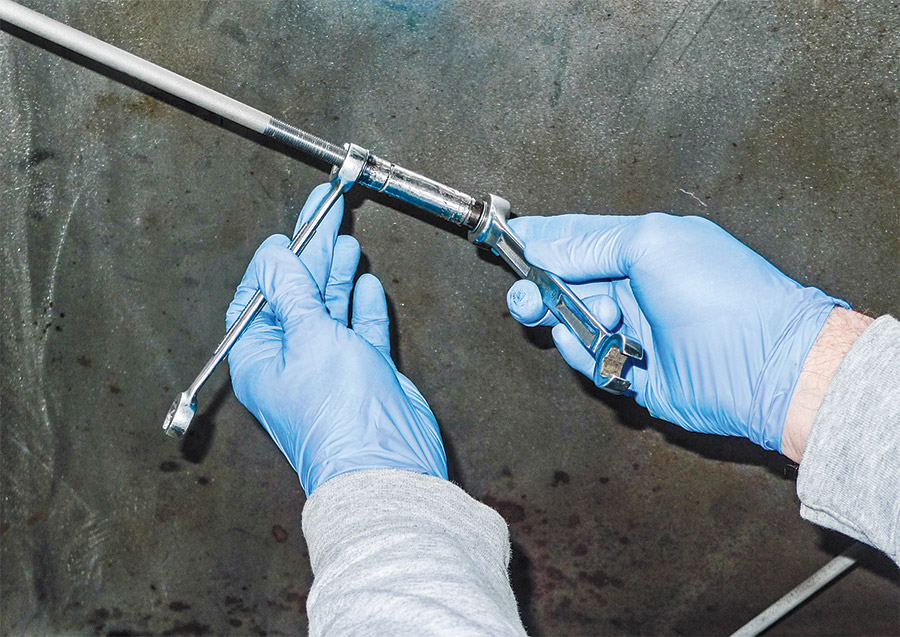
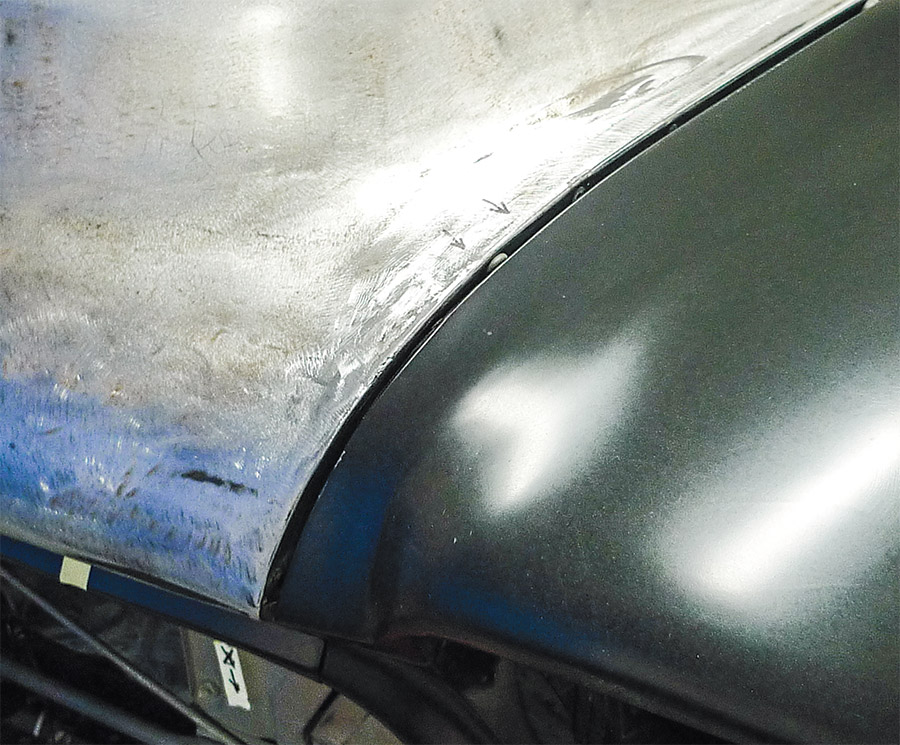
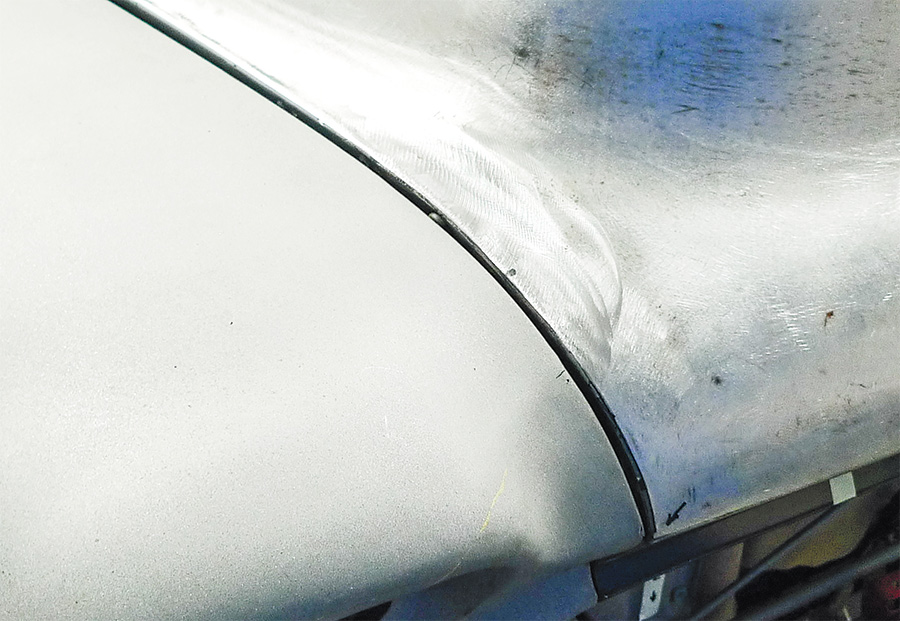
Granted, what we’re about to try isn’t absolutely necessary. It certainly won’t be easier than filing the ends of two slotted holes, but who knows? If this works, we might gain a little fine-tuning advantage. On that note, let’s see!
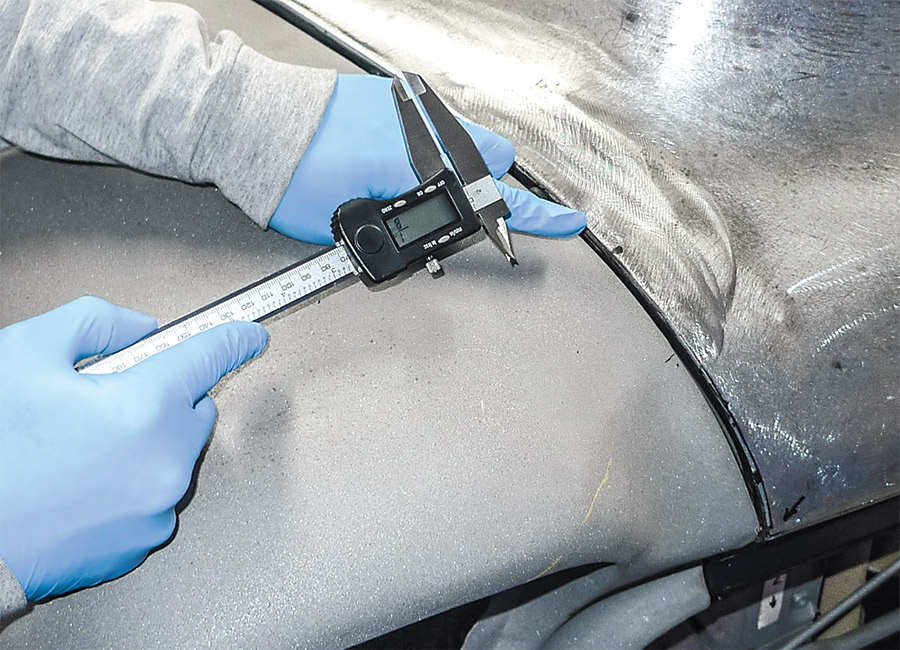
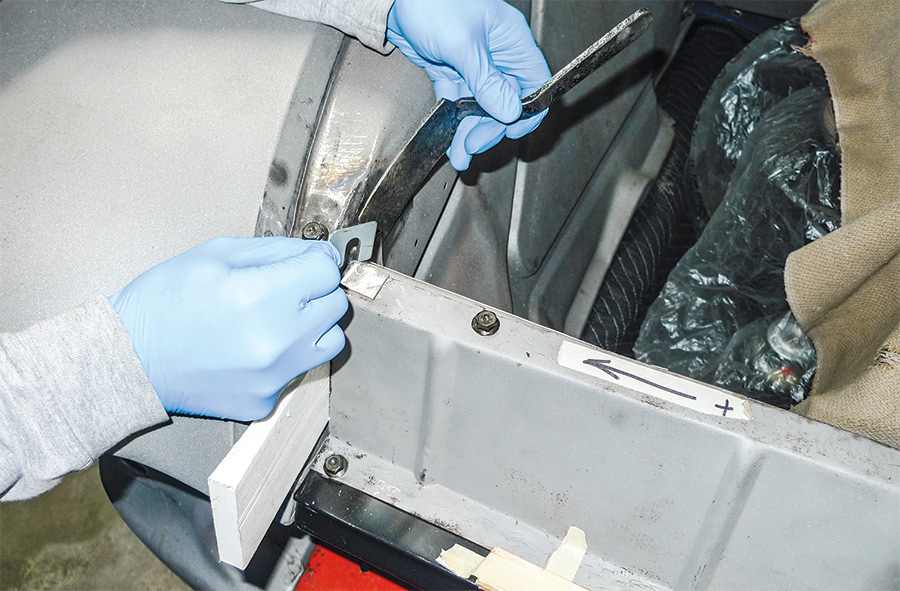
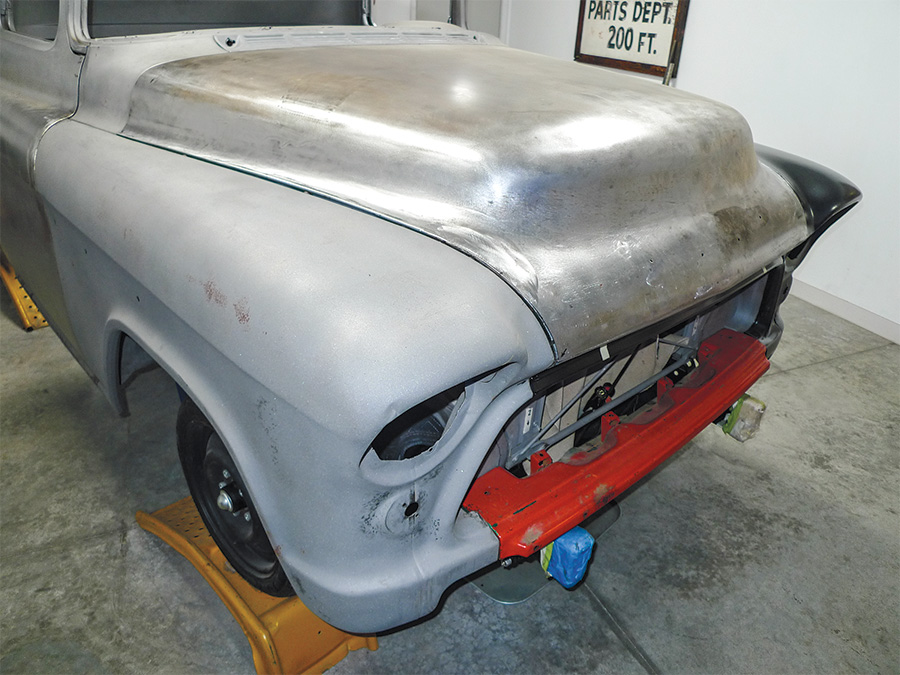
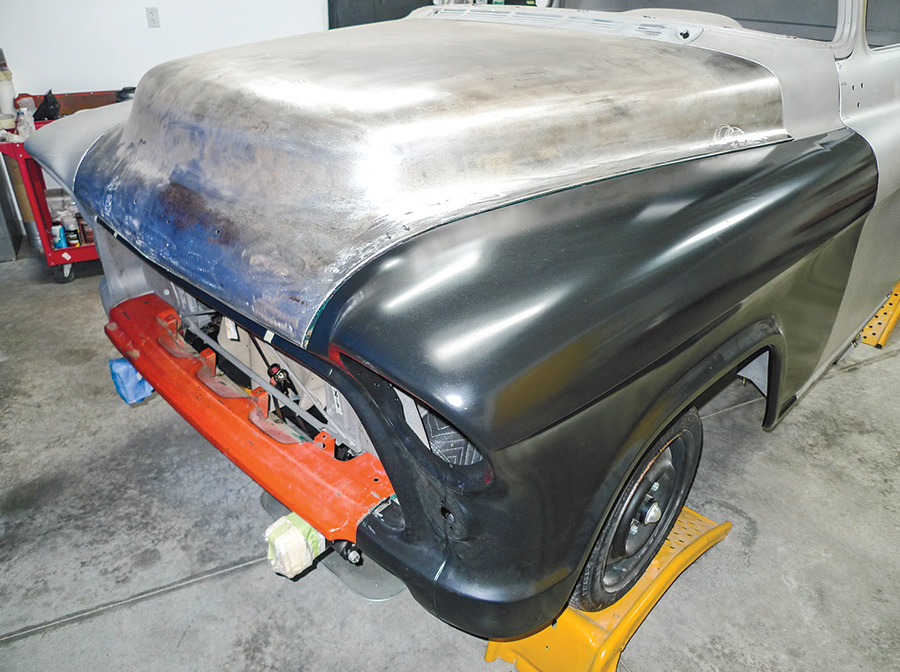
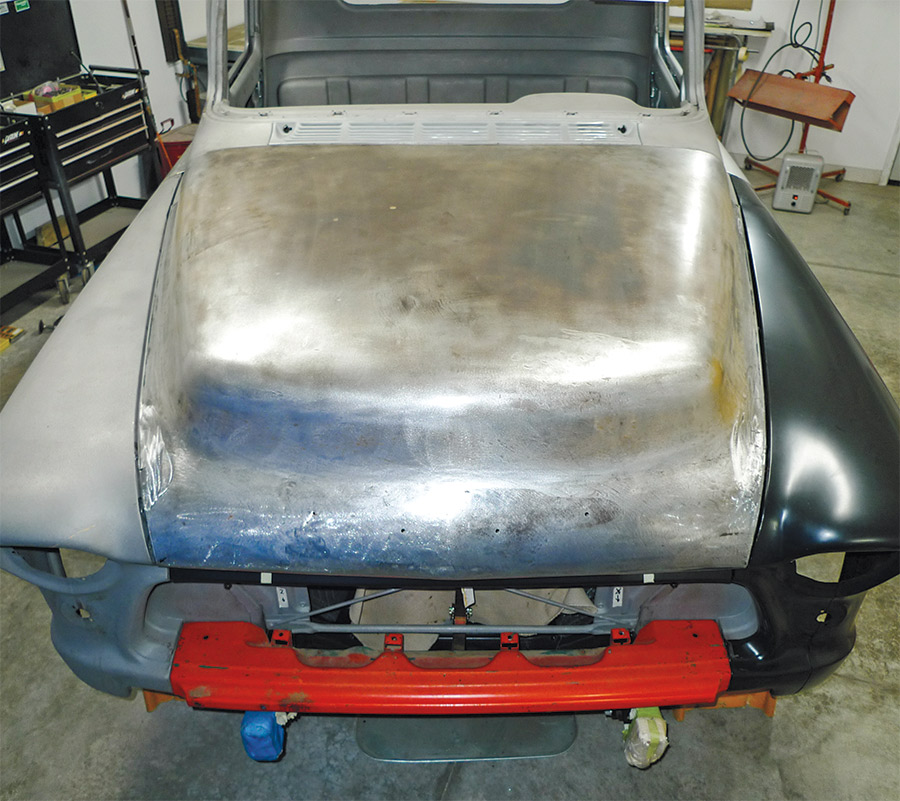
(800) 977-2767
www.brotherstrucks.com
(800) 979-0122
www.speedwaymotors.com
(406) 892-7897
www.restorationsltd.com